Get a Free WorkTrek Demo
Let's show you how WorkTrek can help you optimize your maintenance operation.
Try for freeWant to take your maintenance regime to the next level?
You’ve come to the right place.
In this article, we dive into the fundamentals of successful maintenance management, outlining seven key steps of effective maintenance planning.
We bring you tips, tricks, and insights from industry experts, all to help you better understand this vital process that can truly transform your maintenance process, no matter your company or asset portfolio size.
Let’s dive right in.
1. Define Maintenance Goals
First, it’s indispensable to clearly define and articulate the specific objectives your maintenance program aims to achieve.
Why?
Because doing so will provide the whole team with a sense of direction and give them shared targets to aim for, making the execution of the entire maintenance plan much easier.
But don’t just take our word for it.
Ricky Smith, the Vice President of World Class Maintenance, a company providing maintenance training and consulting, supports this notion.
As he rightly puts it, getting everyone on the same page across the organization is a must.
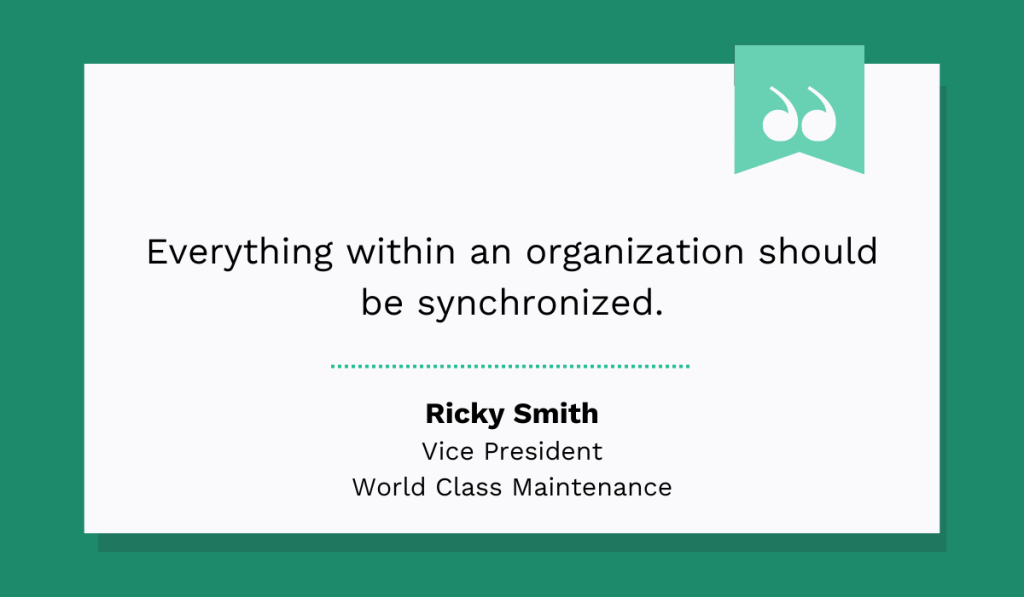
And guess what?
Defining your goals is the key to unlocking that type of synchronization as it spells out precisely what needs to be done, by when, and how.
Skip this step, and you’re setting yourself up for confusion, finger-pointing, and unfinished tasks.
But with well-defined objectives, all that chaos fades away, leaving room only for efficient and purposeful work.
Establishing clear targets, however, doesn’t just keep your workflows smooth but can also help drive the company towards its broader objectives.
For instance, if the organization wants to improve its eco-efficiency, maintenance goals could reflect that by focusing on reducing downtime to aid in resource conservation.
Pieter du Plessis, the Group Product Engineer at Welding Alloys Group, a company specializing in welding consumables, goes deeper into the link between a well-thought-out maintenance program and improved sustainability performance at the company level.
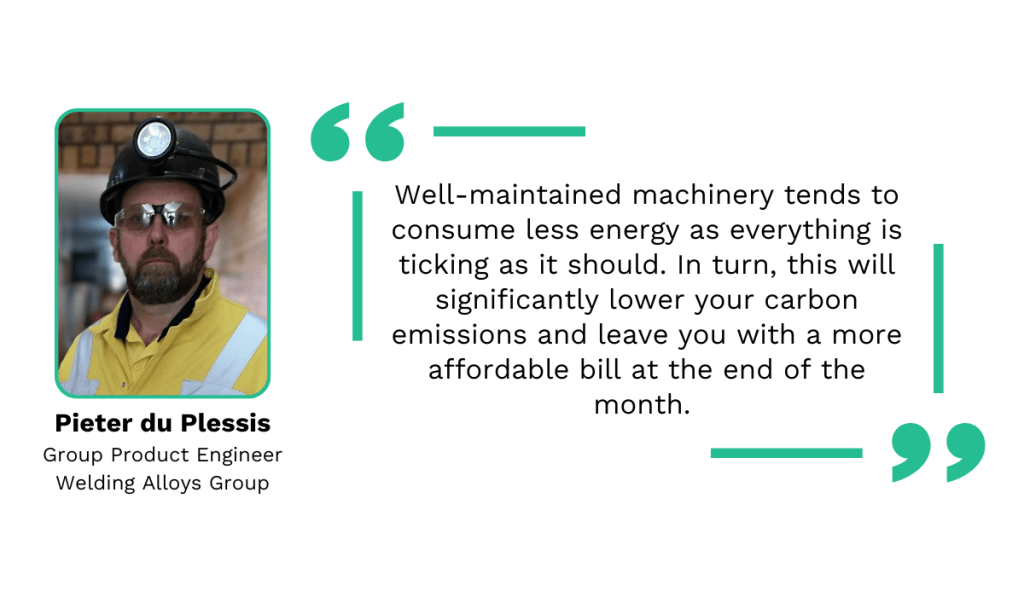
But remember: this is only possible if you do this first step right. So, establish precise, measurable, and easy-to-follow goals.
And how do you do that, you ask?
You can follow the SMART framework outlined below.
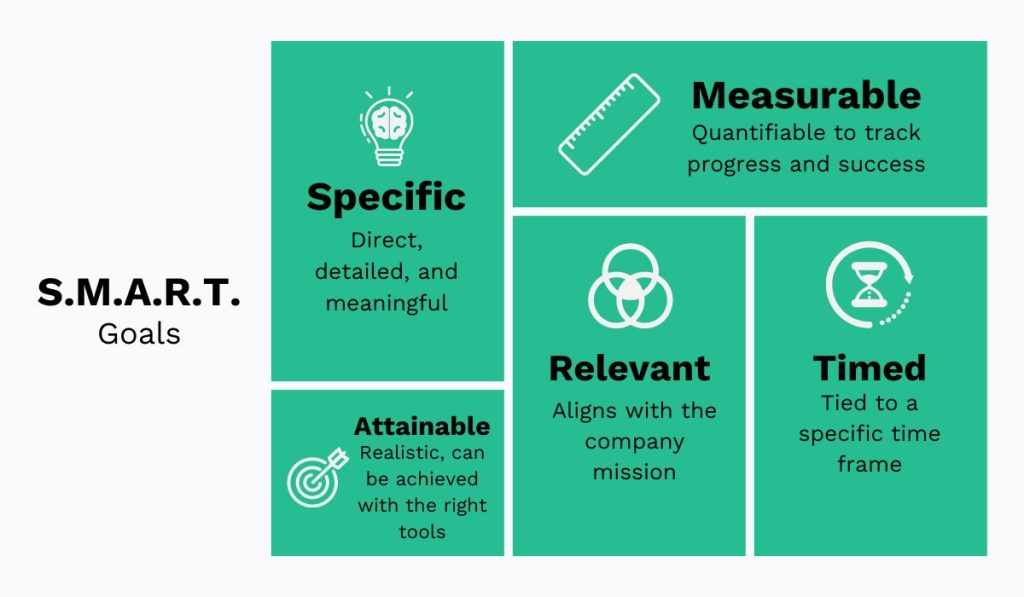
This popular goal-setting method ensures your objectives are specific enough and eliminates any ambiguity, making your targets achievable.
For example, the following goal is not SMART:
Reduce maintenance costs
It just doesn’t specify how much the expenses need to be reduced, which specific costs are targeted, or the timeframe for achieving these savings. Is 1$ saved an accomplished goal? Or is it $1,000?
Without specifics, you cannot measure progress on this target, leading to potential delays or even abandonment of the task.
A far better way to phrase the goal would be:
Reduce spare parts costs by 10% over the next 12 months by implementing a preventive maintenance program.
Now, it’s much clearer what needs to be achieved, when, and through which method.
At the end of the day, a maintenance plan without clearly defined goals is just an abstract idea or a wish.
So be sure to dedicate enough time to this critical phase, and establish targets to keep your team accountable and focused on the right activities.
2. Create an Inventory of Assets
Creating an asset inventory involves systematically documenting and cataloging every piece of equipment, machine, infrastructure, and other physical asset that requires regular upkeep.
Whether you prefer to do this the old-school way via spreadsheets or using a dedicated software solution (check out the example below), the goal of this step stays the same: gaining complete visibility into your assets and their status.
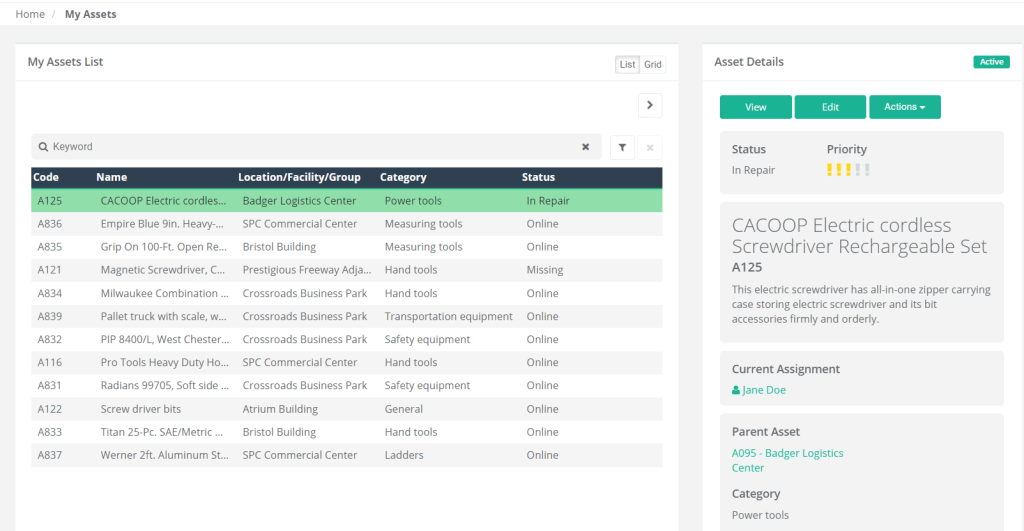
This enables a deeper understanding of maintenance needs, preventing the duplication of service tasks and neglect of certain equipment.
In other words, an accurate inventory empowers you to allocate resources more strategically, prioritize machinery needing immediate attention, and, ultimately, keep each asset operating at peak performance.
Now, as we mentioned, you have two options when it comes to creating these lists: manual methods like spreadsheets or pen and paper and digital tools.
However, in this context, software wins hands down.
It automates data entry, slashing the risk of human error and ensuring your equipment information is always reliable, up-to-date, detailed, and deduplicated.
Matjaž Valenčič, O&M Manager at InterEnergo, a leading renewable energy provider in central Europe, experienced the difference automation can make firsthand by using our solution for maintenance management—WorkTrek.
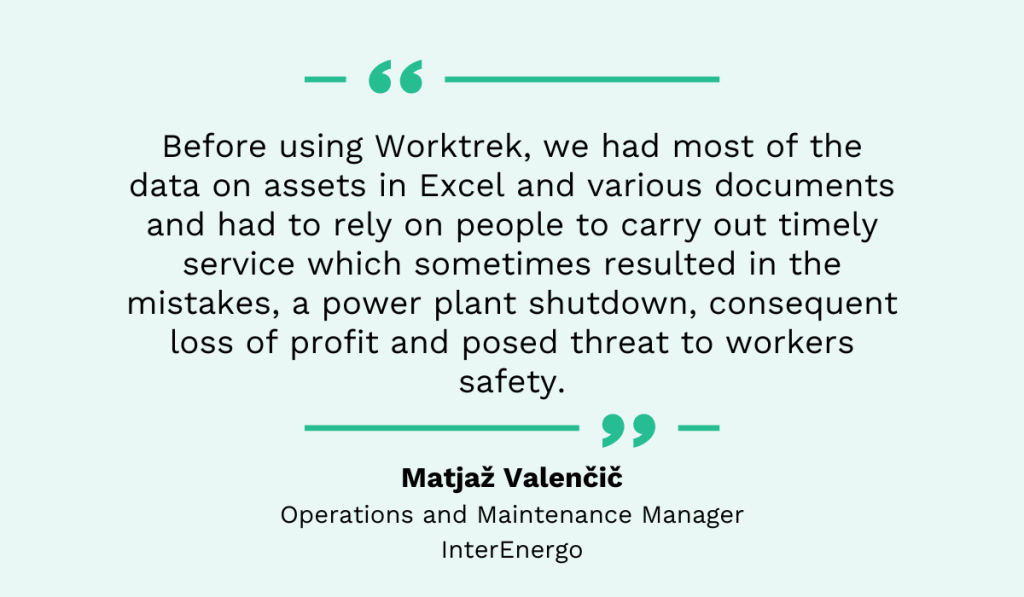
Switching to WorkTrek helped them cut down on asset data mistakes significantly, in turn reducing delays, improving machine reliability, and boosting overall operational efficiency.
The bottom line?
Don’t underestimate the power of a precise asset inventory.
It’s the key to transparency needed to create the most efficient and cost-effective maintenance plan and keep all your valuable assets maintained adequately throughout their whole life cycles.
3. Conduct a Risk Assessment
Now it’s time to identify, evaluate, and analyze the likelihood and consequences of potential maintenance-related hazards such as equipment failures, safety issues, and operational disruptions.
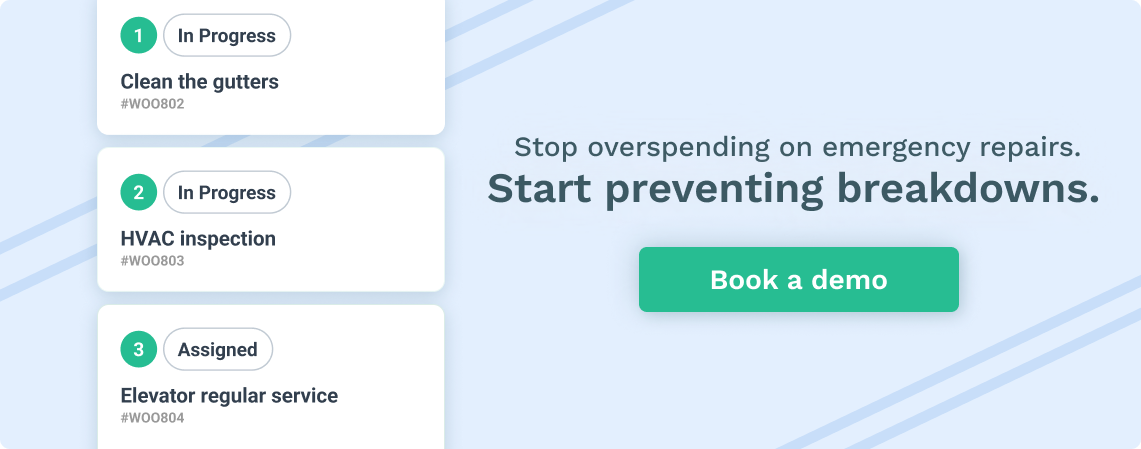
This step is of grave importance because it allows you to properly prioritize maintenance activities and address problems proactively, reducing their impact or eliminating them altogether.
This way, you can significantly reduce that expensive unplanned downtime, keeping your operations intact and costs under control.
But how much money do you exactly save by minimizing unscheduled downtime?
According to a “Value of Reliability” survey from ABB Motion Services in 2023, unplanned downtime is one of the most costly events any industrial or manufacturing facility can experience, costing them an average of $124,669 per hour.
Yes, you read that right—more than $100,000 every hour. That’s a financial risk no organization can afford to ignore.
But it’s not just about the money. Conducting a thorough risk evaluation also safeguards against noncompliance, legal issues, and shutdowns.
And here’s a real-world example.
Bluestone Coke, an Alabama coking plant, faced a $925,000 fine in 2021 and was closed due to leaking toxic chemicals and environmental pollution.
The cause of this incident?
Poor upkeep and neglect of aging equipment, as reported by Manufacturing.net:
The plant, which is more than a century old, has been shut down since October 2021. At that time, the health department declined to renew its operating permit after finding that the oven doors were leaking toxic chemicals, as well as citing other maintenance failures. The agency sued for damages, calling the plant “a menace to public health.
Had more attention been given to these assets and had proper risk assessment been conducted, these problems would have been identified earlier, preventing harm to owners, workers, the plant, and the local community.
Sadly, this isn’t the worst-case scenario, either. In extreme cases, failure to identify risks and perform timely maintenance can result in severe injury or even death.
However, it’s important to remember that you can’t conduct a successful risk analysis without detailed asset information.
Insights, such as the machine’s location, status, condition, specifications, or repair history, can help you understand your equipment better, pinpoint its vulnerabilities, and develop the most effective risk mitigation strategies.
When it comes to gathering and analyzing such information, maintenance management solutions like our very own WorkTrek work like a charm.
WorkTrek’s data-driven Asset Management module tracks all your assets along with their costs, spare parts, downtime, work processes, service histories, and more.
Plus, the system lets you add images and documents to enrich the depth of information about each asset.
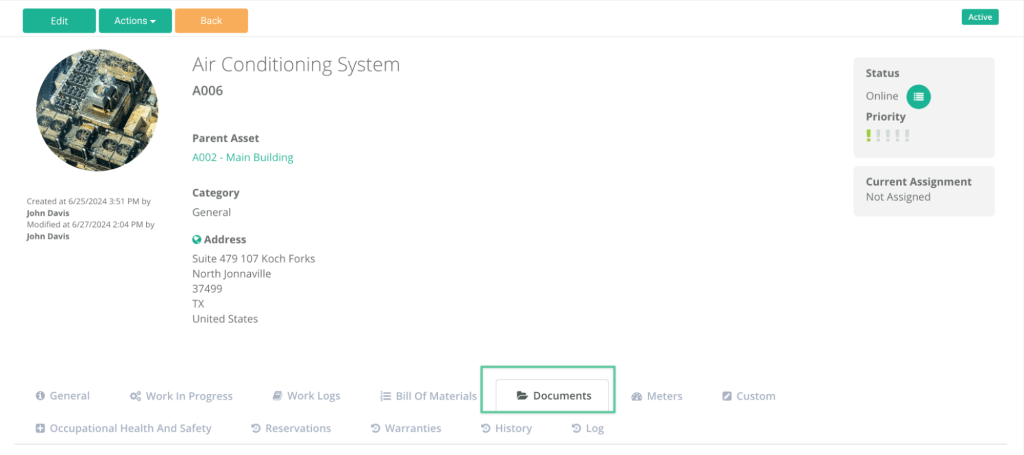
The best part?
All this data is available in real-time through a single platform, whether a desktop, tablet, or mobile device, allowing you to conduct risk assessment essentially from anywhere, at any time.
Who says that risk evaluation has to be complex or time-consuming?
With the right tools, you can easily perform this critical step in maintenance planning, obtaining accurate and actionable insights that shield your organization from all sorts of legal, operational, and equipment-related challenges.
4. Plan the Type of Maintenance Needed
Based on risk assessment, you’ll be able to come up with specific maintenance strategies and actions required to keep each of your assets functioning optimally.
This is precisely what this next step is all about. It includes determining:
- The type of maintenance required (such as inspection, lubrication, cleaning, parts replacement, etc.)
- The order in which maintenance tasks will be performed
- The frequency of maintenance (based on time intervals or other metrics)
- The duration of downtime required for maintenance
Planning this out in advance helps define the scope of your upkeep needs, which is necessary to identify the resources—such as labor, materials, and budget—needed to get the job done right.
It’s best to adhere to the guidelines provided by the Original Equipment Manufacturers (OEMs) to adapt the maintenance strategy to each machine’s specific requirements.
They offer detailed maintenance schedules, procedures, and recommendations tailored to each asset, leveraging the manufacturer’s deep understanding of their products, including operational limits and optimal upkeep practices.
As such, they are a complete must-have for any maintenance team and program.
If somebody knows what works for a particular piece of equipment and what doesn’t, it’s the manufacturers. After all, it’s their product.
Tyler Smith, a Product Manager at Volvo Construction Equipment, agrees with this approach.
Once you’ve figured out the ideal path to fulfilling each asset’s maintenance requirements, it’s time to determine which resources you need to execute your strategy effectively.
Let’s elaborate.
5. Plan the Needed Resources
In this context, resources entail labor, tools, equipment, spare parts, components, and information like technical documentation and work instructions, all essential for effective maintenance execution.
Strategic planning during this step ensures that all necessary resources are readily available at all times, reducing the time an asset is out of operation and boosting operational efficiency.
Jeff Shiver, the President and CEO of People and Processes Inc., a consulting and education services company, knows this all too well:
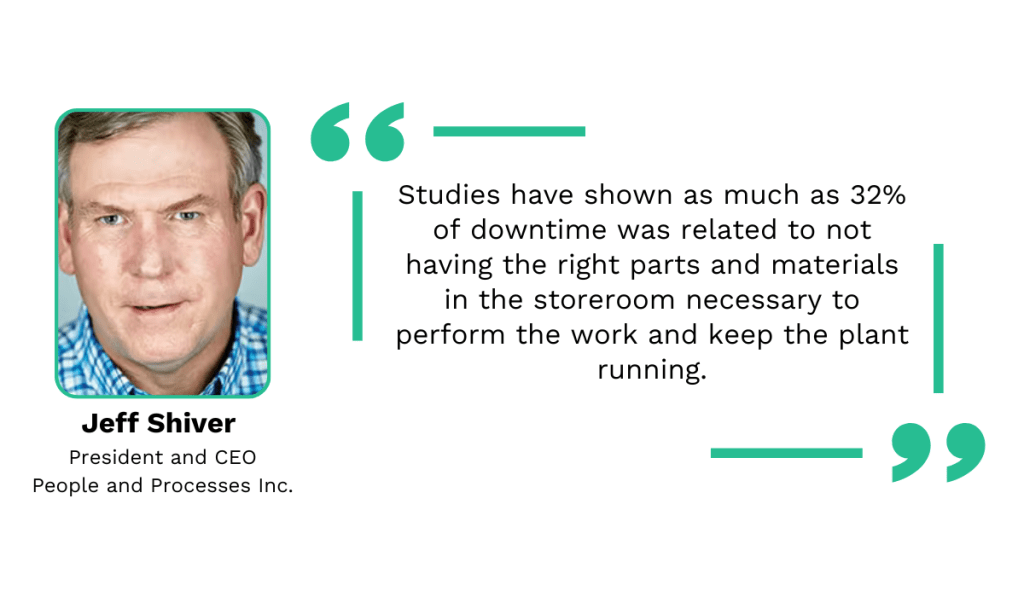
Once he started working as a maintenance manager, he says, he realized how important it is to have the right spare parts at the ready.
Just imagine the scenario where resource needs are not carefully planned: wasting time searching through the warehouse for that vital component, only to discover you no longer have it.
Then you’d have to take the time to order the materials you need, possibly paying extra for expedited shipping, and wait for the order to arrive.
Alternatively, you could risk using an incorrect part you do have at hand, potentially causing even more damage to the asset.
The Pepsi Bottling Group encountered firsthand the pitfalls of poorly managed resources, although, interestingly, their challenge wasn’t having too few spare parts, but having too many.
Tony Yanora, their former maintenance manager, explains what exactly the problem was:
Because of the extensive number of sensors we had in inventory, including multiple styles and brands, simply finding the right replacement could result in an hour of downtime. We had a lot of specialized sensors that we didn’t really need which increased our inventory costs and made it a nightmare for our technicians to make repairs—if we even had the right parts in stock.
Luckily, Pepsi was able to get the issue under control by using inventory management software that helped them identify products they needed and eliminate the rest, ultimately increasing their productivity by 8%.
This example only shows how crucial precise resource planning is when it comes to maintenance.
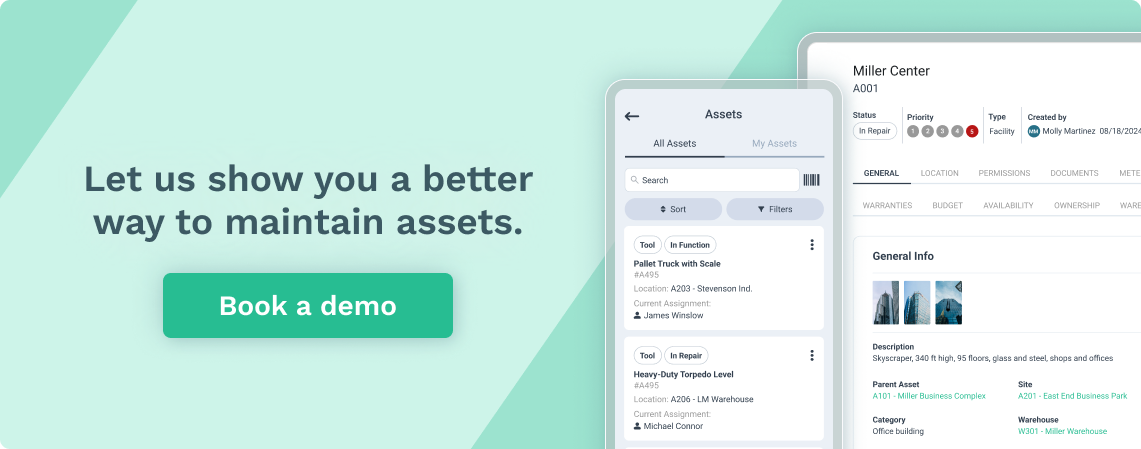
Sure, you don’t want to run out of key materials, but simply stockpiling as much as possible in hopes you might one day need them doesn’t work either.
That’s why you should always thoroughly consider all the assets the company owns, potential risks you identified, and maintenance activities you planned out in the previous steps.
6. Calculate the Budget for Maintenance Tasks
Don’t forget that maintenance costs money.
That’s why it’s crucial to budget wisely for it, taking into consideration all relevant costs such as:
- Labor costs
- Consumables costs
- Tools and equipment costs
- Maintenance software license fees
- Costs associated with unforeseen maintenance
- Consulting fees for external maintenance experts
Creating a detailed budget will help you allocate resources more strategically, ensuring enough money to cover all regular upkeep activities, unexpected repairs, and upgrades effectively without compromising any of your asset’s health.
It will provide a clear framework for expenditure, essentially protecting you from situations where you overspend on specific areas or equipment and then have no money left to cover the rest of the assets.
In WorkTrek, users can easily input parts and labor costs and then compare their planned and realized maintenance expenses.
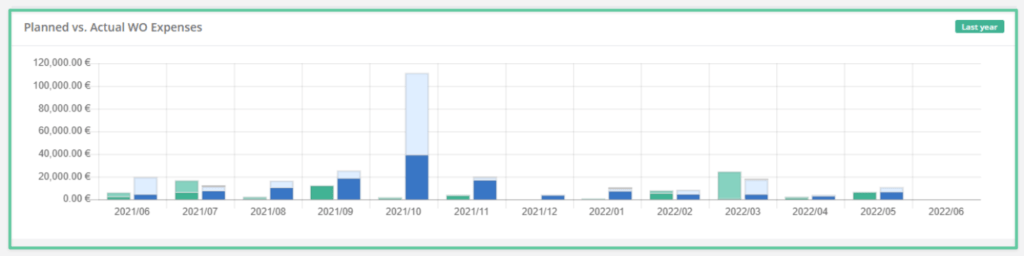
Joe Anderson, Chief Operating Officer at ReliabilityX, a consulting company dealing with maintenance and asset management, points out that budgeting is something maintenance managers often struggle with.
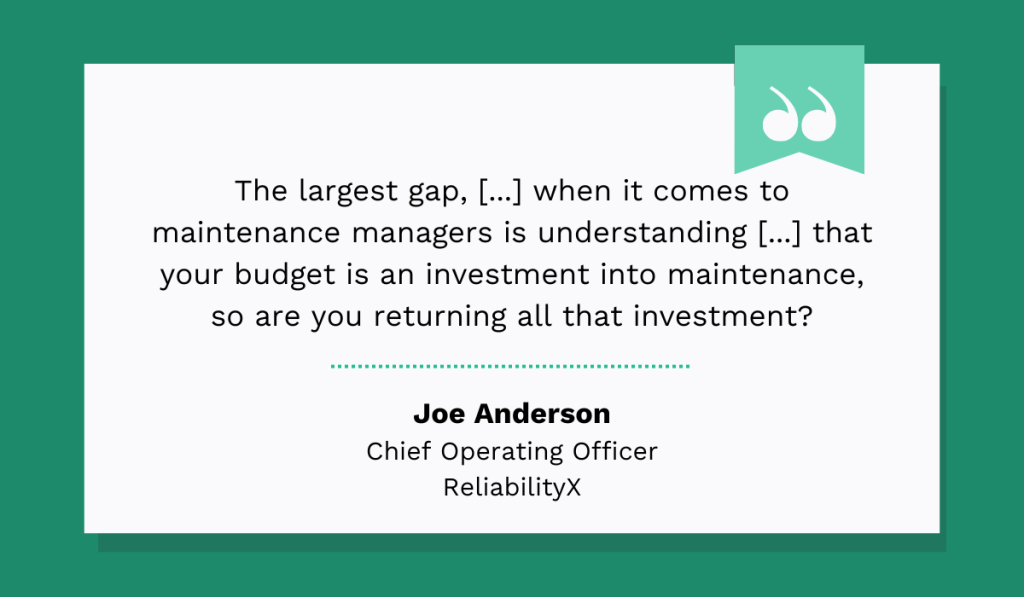
They need to understand, he explains, that this step must be approached strategically to deliver tangible ROI for the business rather than merely spending money reactively and without any plan.
That’s why many organizations aim for the 80-20 principle regarding maintenance budgets.
This means they try to dedicate 80% of their financial resources to preventive upkeep, which offers far more benefits while keeping the remaining 20% for reactive repairs and unforeseen circumstances.
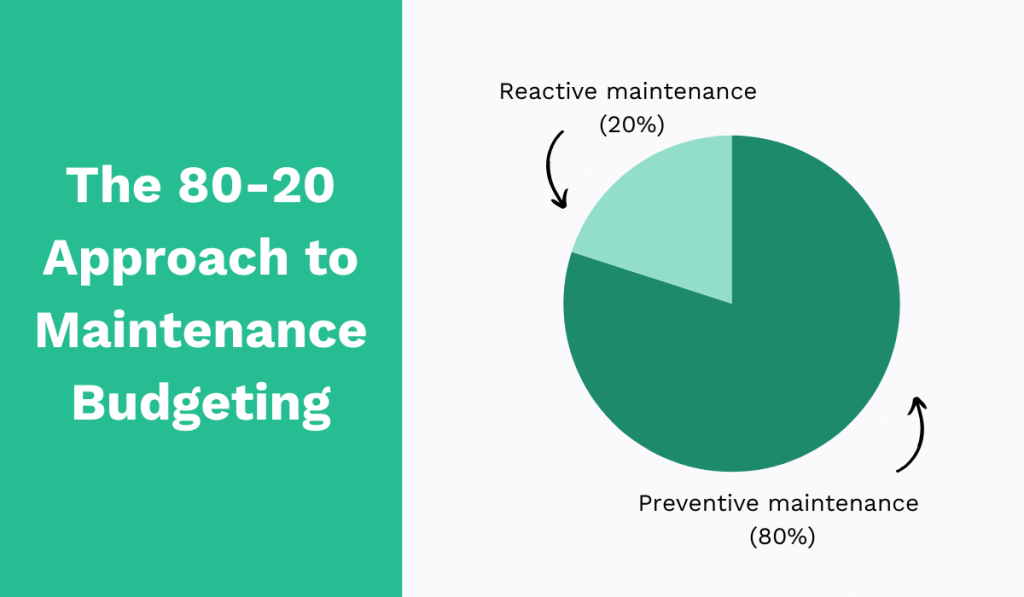
The logic is simple: by investing in proactive maintenance, you save more money on keeping your machines reliable, preventing unexpected failures or disruptions, and prolonging their useful life.
This not only boosts the maintenance ROI Anderson talks about but also keeps your assets in prime condition and even ensures you have a safety net for unplanned expenses.
That’s precisely the trifecta of benefits a maintenance budget should strive to unlock.
7. Develop Standard Operating Procedures
If you’re not sure, a standard operating procedure (SOP) is a detailed, written set of step-by-step instructions on completing maintenance tasks and procedures safely, efficiently, and consistently.
This is crucial for maintaining the efficiency of your operations, as SOPs make sure all processes are carried out the same way, regardless of who performs them.
It eliminates a lot of guesswork, confusion, and time spent figuring out everybody’s responsibilities, thereby increasing productivity and reducing unnecessary downtime.
More importantly, SOPs can also boost safety.
Maintenance work often involves hazardous equipment or environments, so having clear safety guidelines is non-negotiable. SOPs are just that.
With a good CMMS, you can remind technicians of the SOPs they should follow and the PPE they should wear when you assign them work orders.
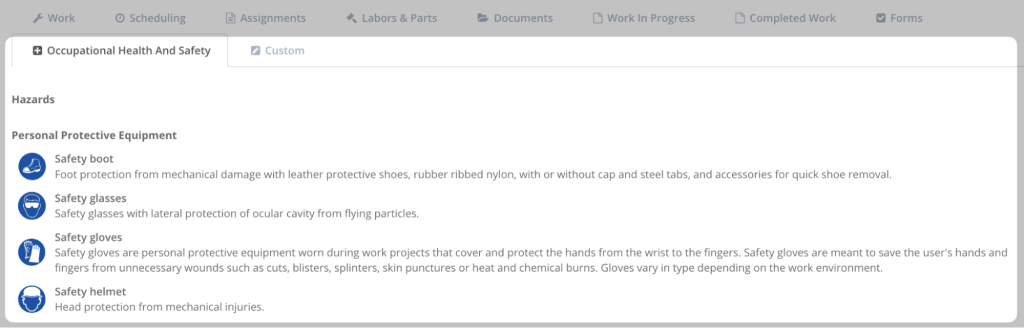
Kristen Panella, founder of 2SAFE Consulting, explains how she has seen many safety issues during her career tied precisely to the lack of SOPs:
I find a lot of companies don’t have SOPs. Let’s say an electrician is working at a facility, and he does the same routine maintenance activity on the electrical panel. There’s often no set SOP for that individual to follow that would give him the knowledge: “I’m supposed to do this. I’m supposed to shut it off and lock it out and then work in there. I’m not supposed to work on live electricity.”
She says that, although often overlooked, these documents are key to educating employees about potential dangers and safety protocols that help them avoid injury.
For complex processes like equipment upkeep, hierarchical SOPs are most commonly used.
They use a top-down approach to break down activities and tasks into four levels: policies, procedures, guidelines, and documentation.
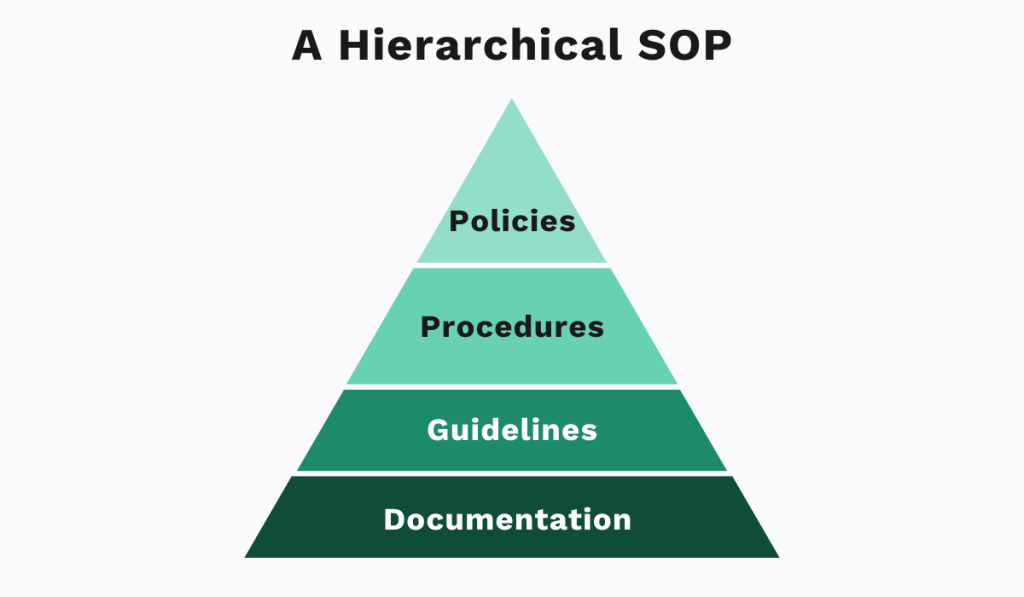
You can think of policies as the “why“. They establish the scope of the SOP.
Procedures are, then, the “what” and “who,” detailing the specific steps and roles involved, while guidelines represent the “how,” providing extra tips to meet quality standards.
Finally, documentation details how to document all the activities thoroughly to ensure compliance with internal processes and industry regulations.
Ultimately, this final step is the backbone of your entire maintenance plan.
It ensures all assets are properly cared for, resources are used effectively, maintenance needs are addressed promptly, and risks are mitigated proactively every single time.
Conclusion
So, there you have it: these are the steps to create an efficient maintenance plan that ensures smooth workflows, minimizes downtime, and keeps your equipment performing at its peak for years.
Sure, it all might seem like a lot of work right now, but with the right digital tools and patience, thorough maintenance planning will become second nature to you in no time.
And the perks are well worth the effort.
Once you’ve mastered this critical task, you’ll be all set for the next phase of maintenance management: scheduling and assigning upkeep tasks.