Get a Free WorkTrek Demo
Let's show you how WorkTrek can help you optimize your maintenance operation.
Try for freeScheduling maintenance activities is a complex task, no doubt about it.
There are many factors to consider, from technician skills and availability to production schedules and the impact of downtime on your facility’s operations.
That is precisely why, in this article, we’re sharing our best tips to help you efficiently schedule maintenance tasks and keep your operations running smoothly.
Let’s get started.
Leverage Maintenance Management Software
The first thing you can do to schedule maintenance tasks more efficiently is to stop doing that manually.
Sure, using pen and paper—or perhaps Excel spreadsheets—for maintenance scheduling is inexpensive and straightforward since everyone is already familiar with these methods.
But is this truly the most efficient way to go about it?
Robert Burgh, President at Nexcor Food Safety Technologies, doesn’t think so.
He explains that using CMMS is the best way to schedule maintenance tasks.
Such software solutions, he says, make scheduling more efficient, as all the necessary data is aggregated and easily accessible in one place.
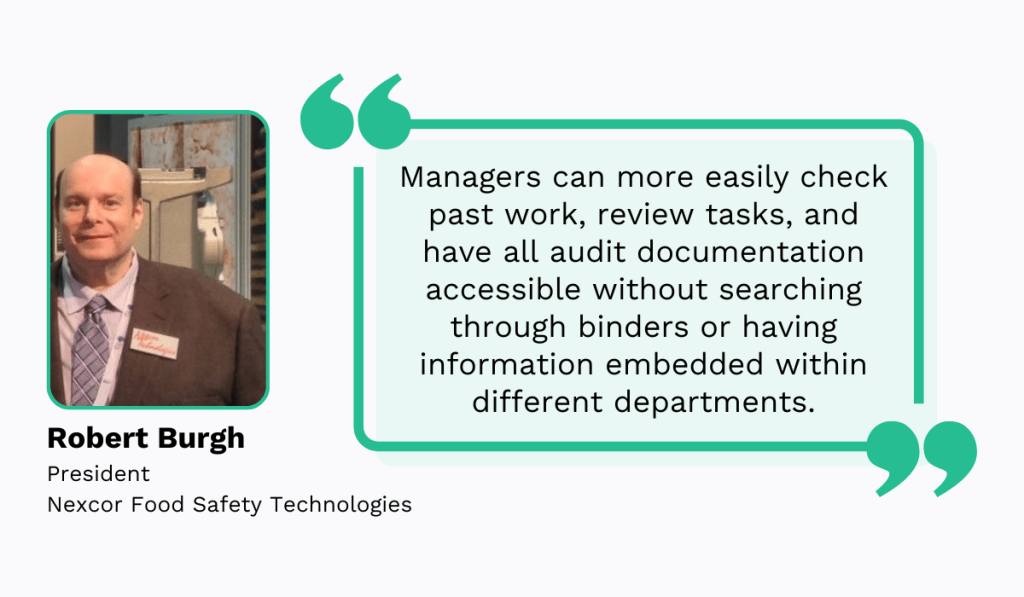
Using a CMMS means no more digging through paperwork to figure out when specific technicians are available or shuffling the entire schedule because you accidentally double-booked someone.
With all the relevant data in one central location, maintenance management becomes a breeze.
To illustrate our point, we’ll use our maintenance management software, WorkTrek, as an example.
Our Work Order Scheduler provides a holistic view of all things maintenance.
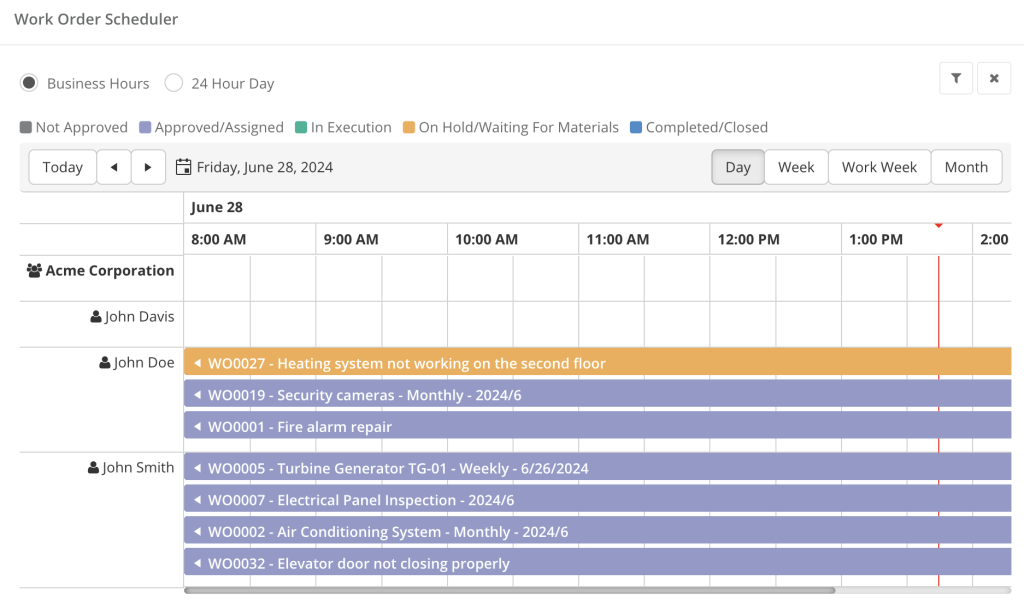
You can see which technicians are available, what maintenance tasks are assigned, and their status.
This makes it easier to create and assign new work orders.
What makes this system even better is that its benefits extend to your maintenance technicians.
Once assigned a work order, they’ll receive a notification via our mobile app.
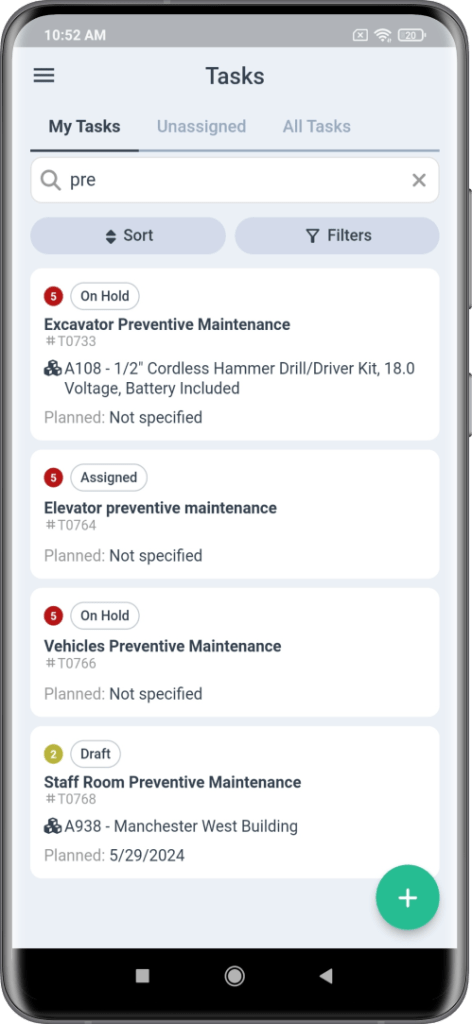
That way, they don’t have to constantly check in with their supervisor to see whether there are any new tasks they’re in charge of.
They can access the app anywhere, anytime, and find out exactly what they need to do.
In addition, WorkTrek allows users to enrich work orders with details such as the start and end date, the description of the problem at hand, and instructions on how to fix it.
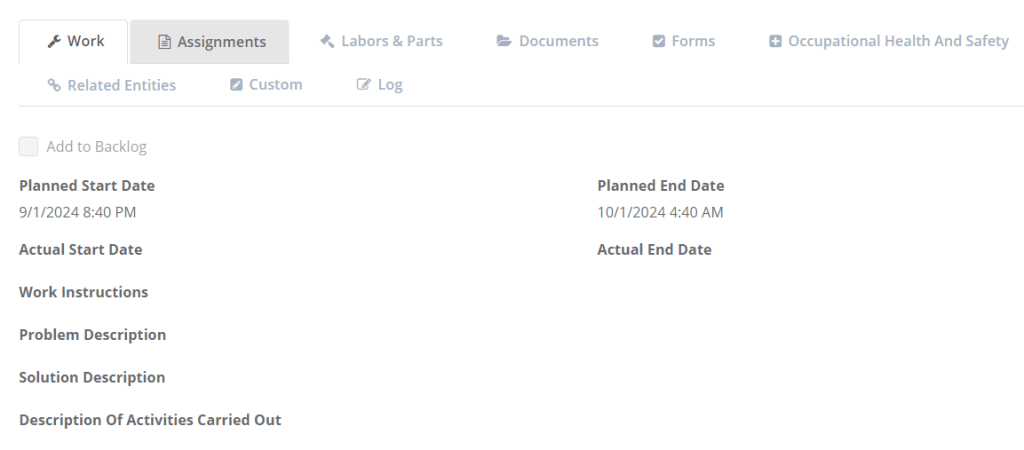
This minimizes the back-and-forth communication between technicians and supervisors as the software answers many potential questions.
In short, relying on CMMS streamlines a plethora of maintenance scheduling processes that are time-consuming and error-prone.
Does it require an initial investment and getting used to it? Yes.
But leveraging maintenance management software for this purpose will save you and your team so much time, energy, and money in the long run, so it pays off.
Match Technician’s Skills to Tasks
An important part of scheduling maintenance is ensuring that the technicians you choose to assign specific tasks have the necessary skill set to complete them.
That’s because accounting for skill levels when assigning tasks ensures each task is carried out correctly, efficiently, and safely.
If tasks are assigned to technicians who are not skilled enough to handle them, the consequences can be detrimental.
Take the 2020 Evergreen Packaging Paper Mill incident for example.
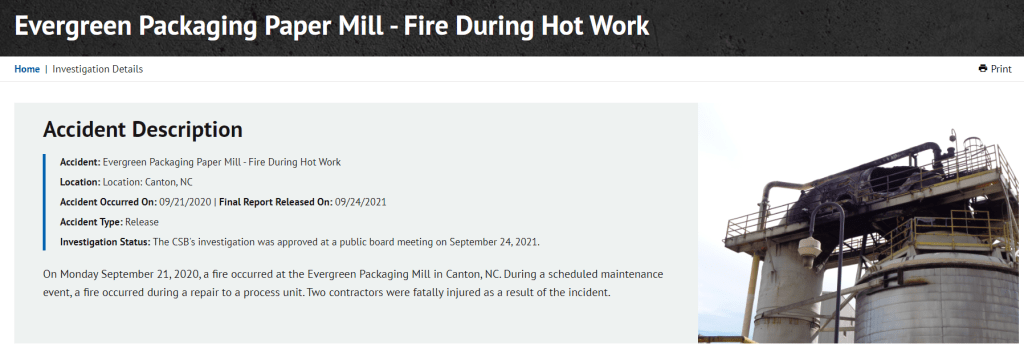
In this tragic case, two Blastco workers were tasked with repairing the inside surface of the upflow tower using epoxy vinyl ester resin and fiberglass matting.
Since the night was colder, the resin—which hardens faster at higher temperatures—and fiberglass matting were not hardening at the expected rate.
After they couldn’t stop the material from sliding down the tower’s walls, the workers used an electric heat gun to get the resin to harden.
The heat gun ended up falling into the bucket of flammable resin, causing a fire that traveled through the connecting pipe, ultimately killing the workers maintaining the downflow tower.
After the incident, the U.S. Chemical Safety Board (CSB) Lead Investigator Drew Sahli said:
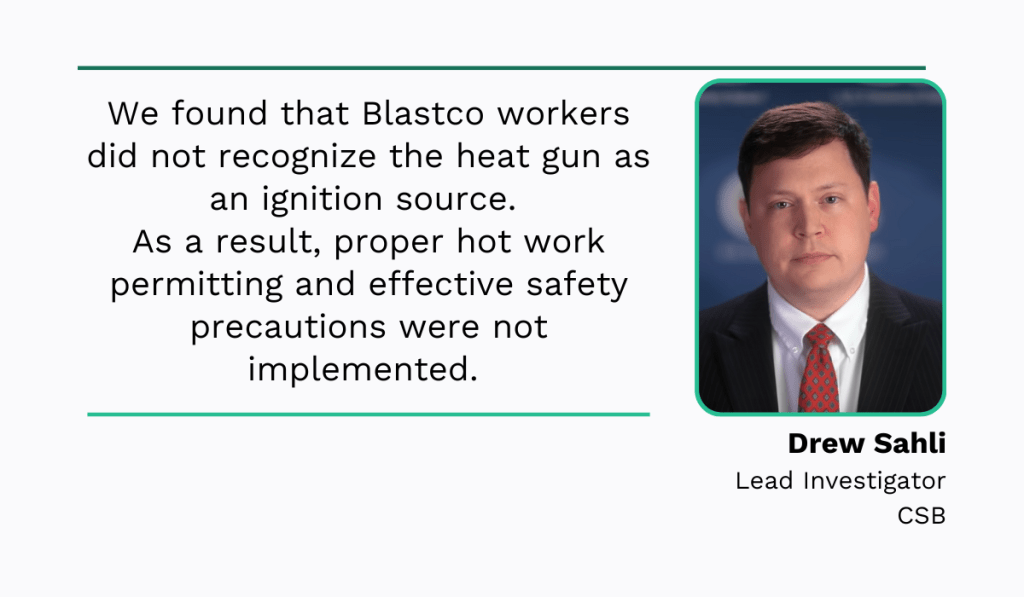
Had the task been given to workers experienced with resin application in cold weather, this tragedy could have been prevented.
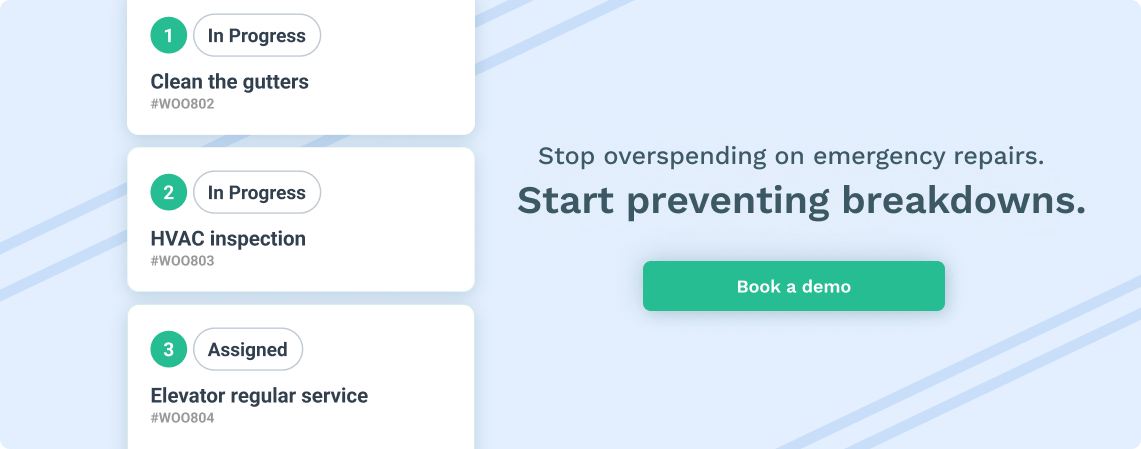
So, what can we learn from this?
For starters, this tragic incident underscores the importance of thoroughly evaluating the skills and experience of each technician before assigning them a maintenance task.
The research conducted by Plant Engineering has shown that over 70% of maintenance personnel in the facilities are trained in basic mechanical and electrical skills.
However, significantly fewer technicians have the skills necessary for maintaining fluid power systems, for instance.
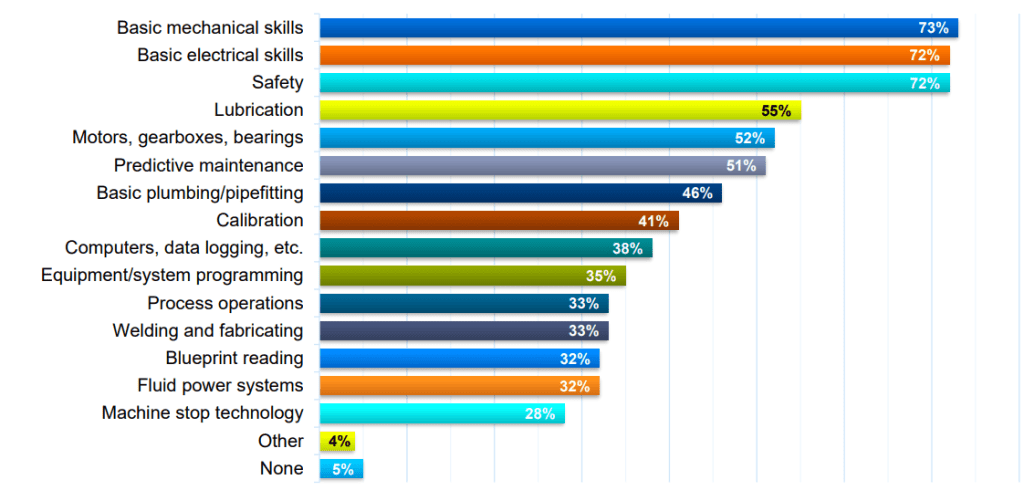
So, before you schedule any of your technicians for a task, try to determine whether they have the experience and certifications needed to perform it.
This is, again, where having a CMMS comes in handy.
As you can see in the screenshot below, you can use your CMMS to store information about any training courses your workers have completed and see what maintenance tasks they’ve handled in the past.
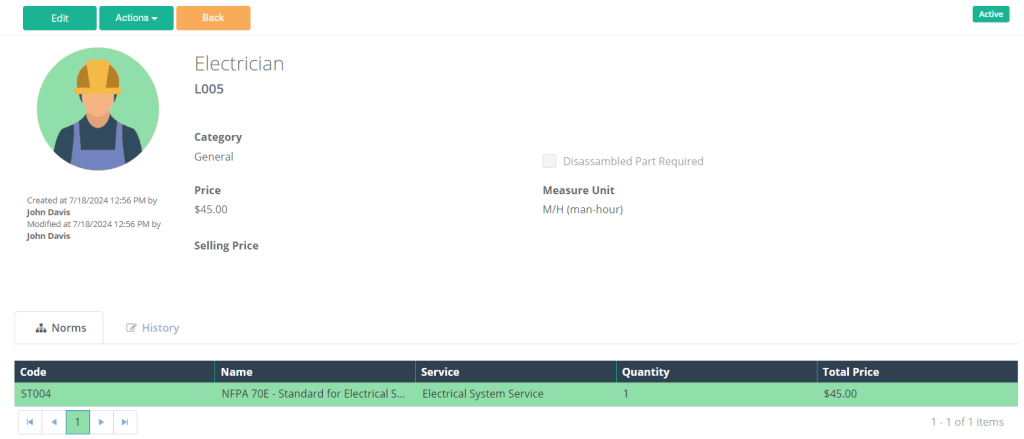
With this information at your fingertips, you can always be confident that the technicians you’re assigning tasks to can complete them.
Coordinate Maintenance Schedules with Operations
Yes, figuring out who you should assign to which maintenance task is essential.
However, another big question needs to be answered correctly to maintain the efficiency of your facility’s operations.
And that question is: “When is the best time to schedule specific maintenance tasks?”
As it turns out, answering it is not as easy as it may seem.
If it were, the results of the 2022 Maintenance Manager Report wouldn’t show that planning and scheduling maintenance are the biggest challenges for most maintenance teams.
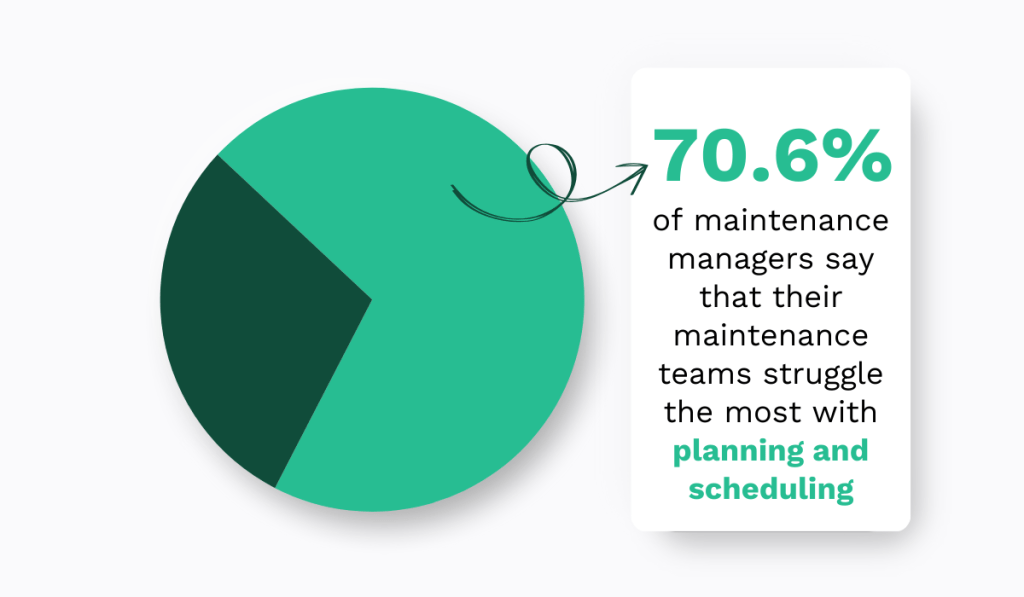
What makes scheduling maintenance so complex is that it involves more than simply matching tasks to the workers who can perform them.
For starters, if not properly scheduled, maintenance can throw off operations at your facility, causing disruptions and delays.
So, don’t schedule maintenance in a vacuum.
Instead, regularly meet and discuss maintenance with others, as this will give you a complete picture of your facility’s activities.
For instance, an operations manager might inform you that some production activities need to be completed by a specific date, so scheduling maintenance before then would throw a wrench in the works.
Or, a procurement officer could tell you that the spare parts your technicians will need for a specific maintenance task won’t be delivered as planned.
This kind of information can be a lifesaver when trying to create a solid schedule.
Aside from consulting with the stakeholders within your facility, you may also want to consider implementing predictive maintenance.
This approach to maintenance scheduling is all about using historical and real-time data and ML algorithms to predict future maintenance needs.
Hans Van der Aa, Senior VP of Lifecycle Services at the engineering and manufacturing company Duravant, finds that it can bring significant benefits to facilities trying to minimize unnecessary downtime caused by poor maintenance scheduling.
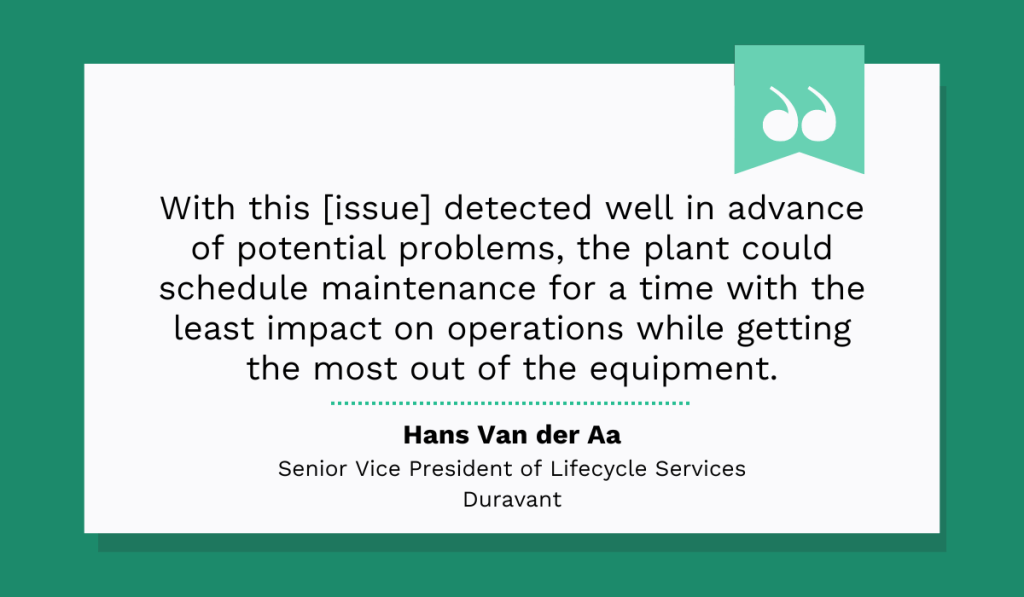
As you can see, multiple factors need to fall into place to develop the perfect maintenance schedule.
So, before you hastily assign work orders for the first available time slot, consider how your scheduling decisions will affect operations overall.
Whether this is through regular consultation with the key stakeholders, staying one step ahead by implementing predictive maintenance, or a combination of both, one thing is for sure.
Looking at the bigger picture will help you create a schedule supporting your facility’s overall goals.
Define How You Will Prioritize Maintenance Tasks
Not all maintenance tasks are equal.
You’ll probably agree that replacing a flickering lightbulb in the breakroom doesn’t carry the same weight as fixing a broken conveyor belt that has brought your production to a halt.
So, when scheduling maintenance activities, you need a clear idea of what constitutes an urgent task versus a non-critical one for your facility.
Ahmed Awad Ramadan, Maintenance Planning and Scheduling Department Manager at MIDOR Refinery explains how to do just that:
When it comes to work prioritization, we should consider two main criteria. First, the criticality of equipment, which reflects the effect of the asset’s failure on the whole organization. Second, the nature of work. While equipment criticality is a fixed number and has to be aligned with the organization’s strategy; the nature of work is variable and relies on the workers’ perspective.
He explains that to assess the criticality of specific maintenance tasks, the Ranking Index for Maintenance Expenditures (RIME) is his tool of choice.
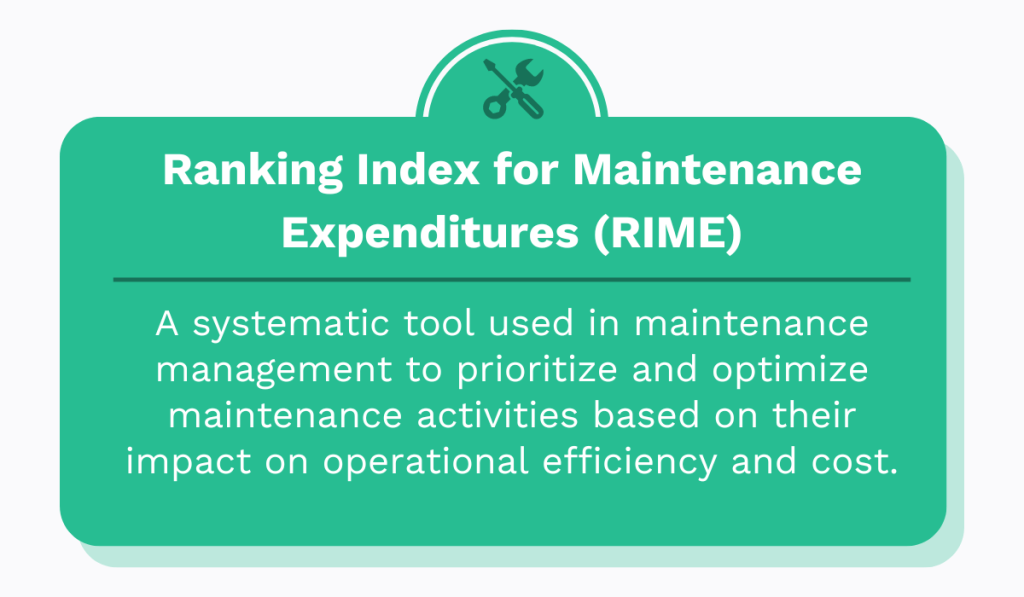
Observing the key components of RIME—criticality, cost impact, frequency of failure, and downtime—can help you gain clarity and decide which tasks should be tackled first.
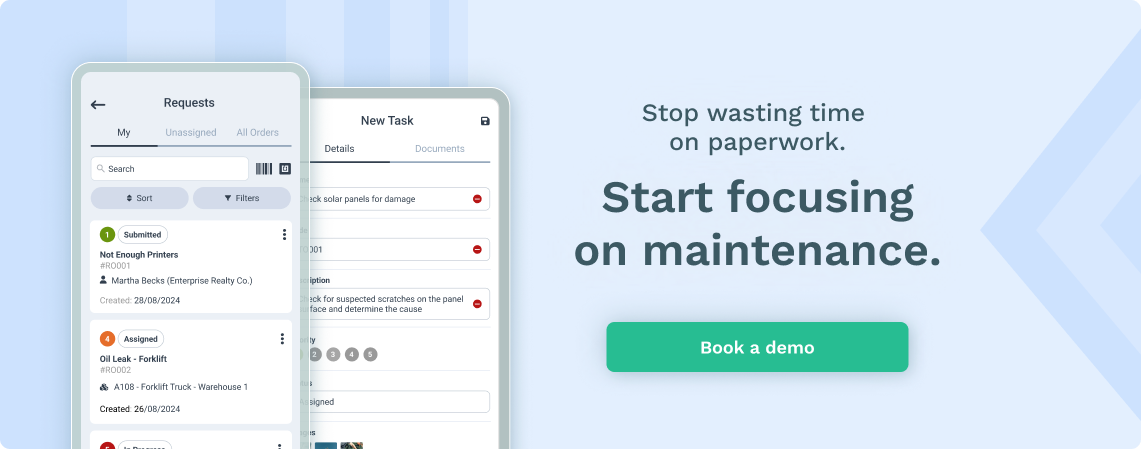
For instance, repairing a machine that is critical to the operations, but has recently experienced more frequent issues is bound to take priority over a costly repair with barely any impact on the production.
Many maintenance professionals also like to use a scale from 1 to 5 to denote the criticality of maintenance tasks, where 1 is a low-priority task, and 5 is urgent work.
John Q. Todd, a senior business consultant and product researcher at Total Resource Management and a leading asset management solutions provider, shares an important insight regarding the use of this approach.
He says he had clients who’d gone as far as to use a scale from 1-10 for task prioritization, which ultimately rendered them unable to determine the actual difference between priority levels 4 and 5, for example.
Therefore, he explains, that keeping your priority scale small can significantly simplify the decision-making process.
Many maintenance management systems have this priority scale feature, which makes assigning priority levels easier, as you can see in the example below.
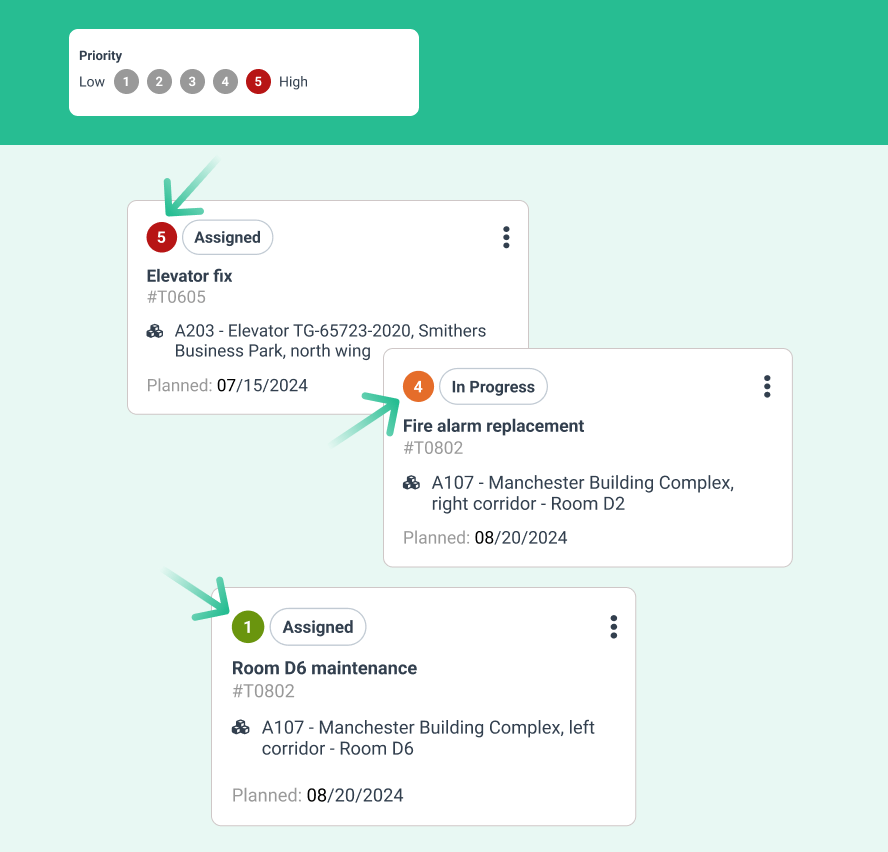
This feature makes it easier for you to assign tasks and allocate resources for maximum operational efficiency.
It also helps your maintenance technicians understand the importance and urgency of each task they’ve been assigned.
On a particularly busy day, for instance, knowing how high of a priority each task on their list is can help them make sure that they tackle those critical ones first.
So, before you put any maintenance tasks into the schedule, determine exactly how you will prioritize them.
Use Past Job Data to Estimate Maintenance Task Duration
When creating a new maintenance schedule, one of the more challenging yet essential tasks is determining how long a specific task should take to complete.
Why is that the case?
Because your estimate for the duration of maintenance tasks can make the difference between smooth running operations and those disrupted by costly downtime.
Now, trying to determine how long each task should take, but having data makes this task possible.
It’s almost like reading the third book in a trilogy without reading the first two parts.
You’ll have no idea what is going on and probably make all the wrong conclusions due to a lack of context.
That is why Daniel McGowan, Offshore Projects Director at Longitude Engineering, highlights the importance of making data-based assumptions when planning and scheduling maintenance.
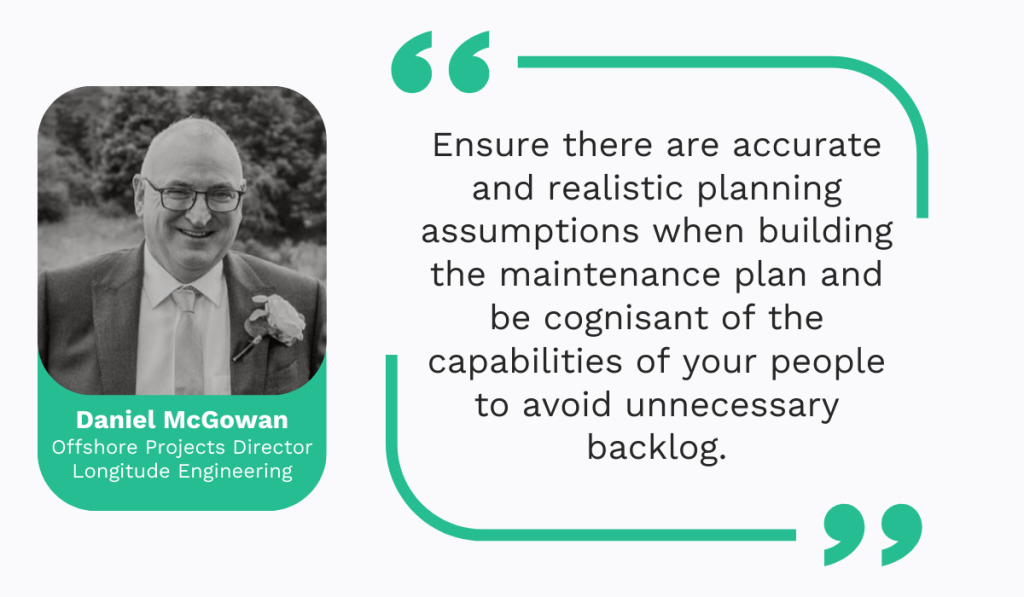
This brings us to the key question: how exactly do you do that?
Start by reviewing the data from previously completed maintenance jobs and use it to identify patterns and anomalies.
- How long did the same or similar tasks take to complete?
- Are the workers who completed them truly the most efficient, or do you have other technicians who could complete them faster next time around?
- Did your technicians encounter any unexpected obstacles that prolonged the task duration?
Asking questions like these will help you create better time estimates going forward, and your CMMS can be a great source of answers.
In the example below, you can see the task being finished sooner than expected, giving you an idea of how much time you should reserve for it next time.
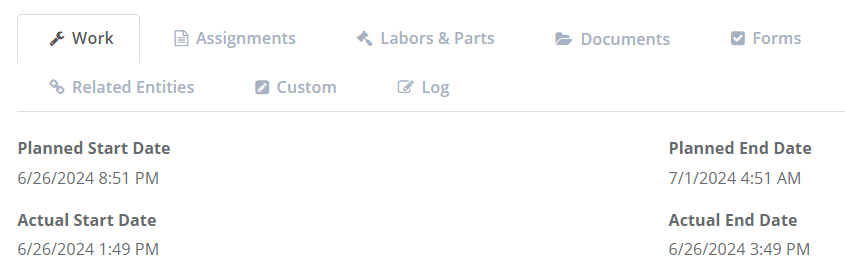
On top of that, it is wise to observe some key KPIs, such as your MTTR, or mean time to repair.
This important KPI measures the average time needed to complete a repair, providing you with a baseline for future upkeep scheduling.
You can calculate it using the following formula:
MTTR = Total Repair Time ÷ Total Number of Repairs.
Alternatively, you can use our handy maintenance calculator to quickly calculate both your MTTR and a variety of other key maintenance metrics.
Of course, the goal is to keep your MTTR as low as possible, as this indicates that both your scheduling and maintenance practices are effective.
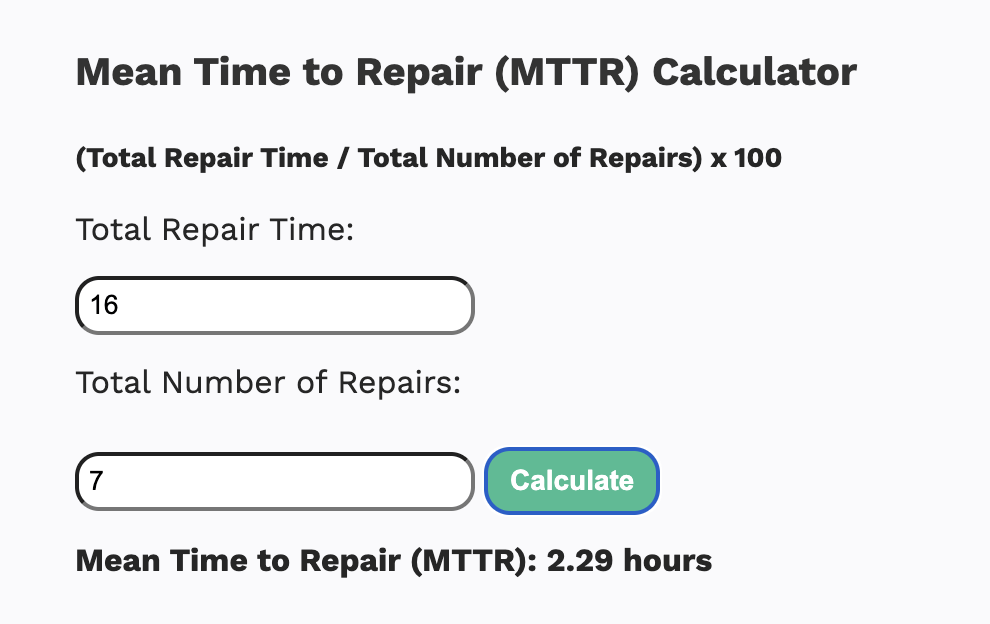
The bottom line is that one of the best ways to estimate the duration of future maintenance activities is to look at the past.
Do your best to identify patterns and pay attention to cold, hard data, and you’ll excel at making this important estimation.
Conclusion
While scheduling maintenance tasks is no easy feat, we believe that following the tips we shared throughout this article can certainly make it more manageable.
With the right blend of technology, historical and real-time data, and collaboration with key stakeholders at your facility, you can make sure that everything keeps running smoothly—both your machinery and your operations.
And if you’re still worried about how you’re going to juggle everything that goes into good maintenance scheduling, we suggest you start with tip #1: make the most of your CMMS.
Just that one piece of technology can make a world of difference and help you implement the rest of the advice we shared.