What is an asset?
In maintenance organizations, an asset refers to any physical item, equipment, machinery, or infrastructure that holds value and contributes to the organization’s operation or services. These assets are critical to achieving business goals, whether directly producing goods, supporting processes, or providing essential services.
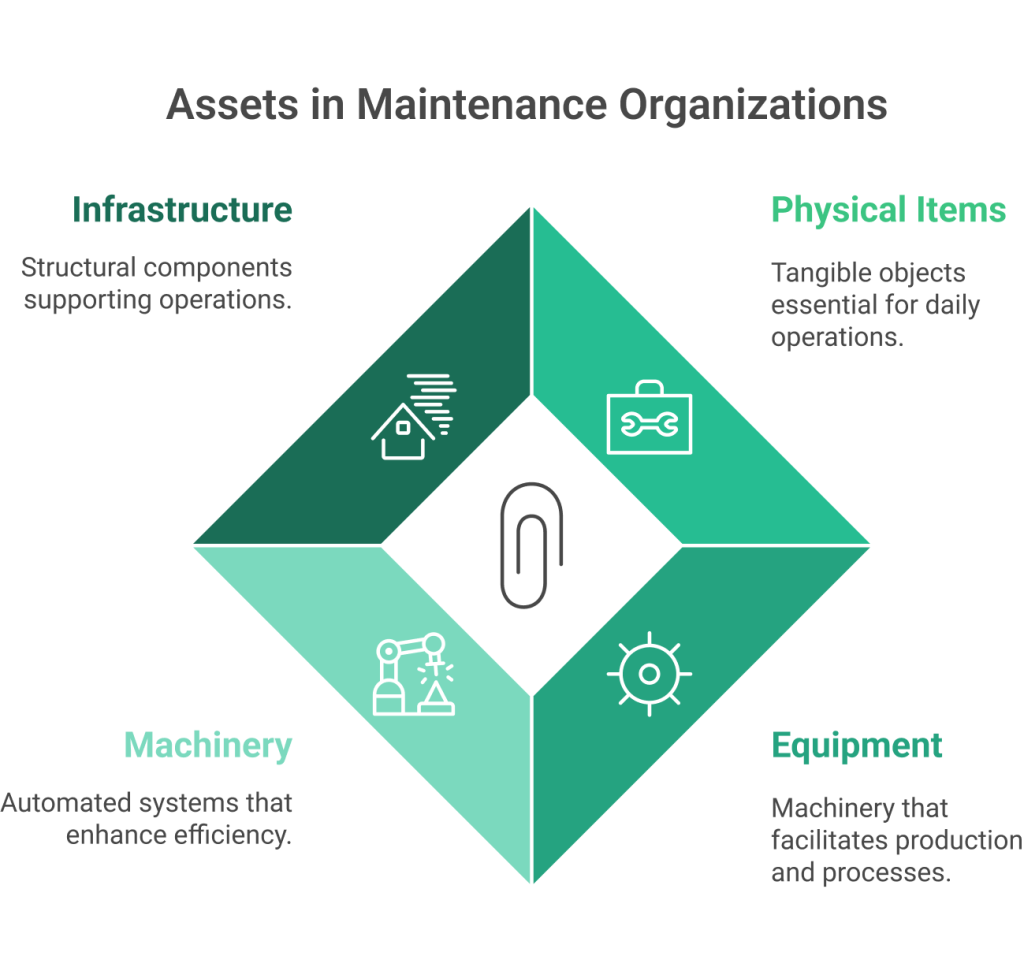
Some examples include vehicles, HVAC systems, production machinery, tools, and even buildings or IT infrastructure.
Assets are classified as fixed or movable depending on whether they remain stationary or can be relocated. They can also be categorized by type, such as critical assets, which are essential to operations and require higher maintenance priority, or non-critical assets, which have less immediate impact on business functions.
In maintenance contexts, an asset is not just an item but an entity that requires careful monitoring, repairs, and upkeep throughout its lifecycle.
Organizations utilize asset management systems to track each asset’s status, usage, and condition, ensuring they operate efficiently, safely, and reliably. Preventive, predictive, and corrective maintenance activities are scheduled to minimize downtime, extend the asset’s useful life, and optimize performance.
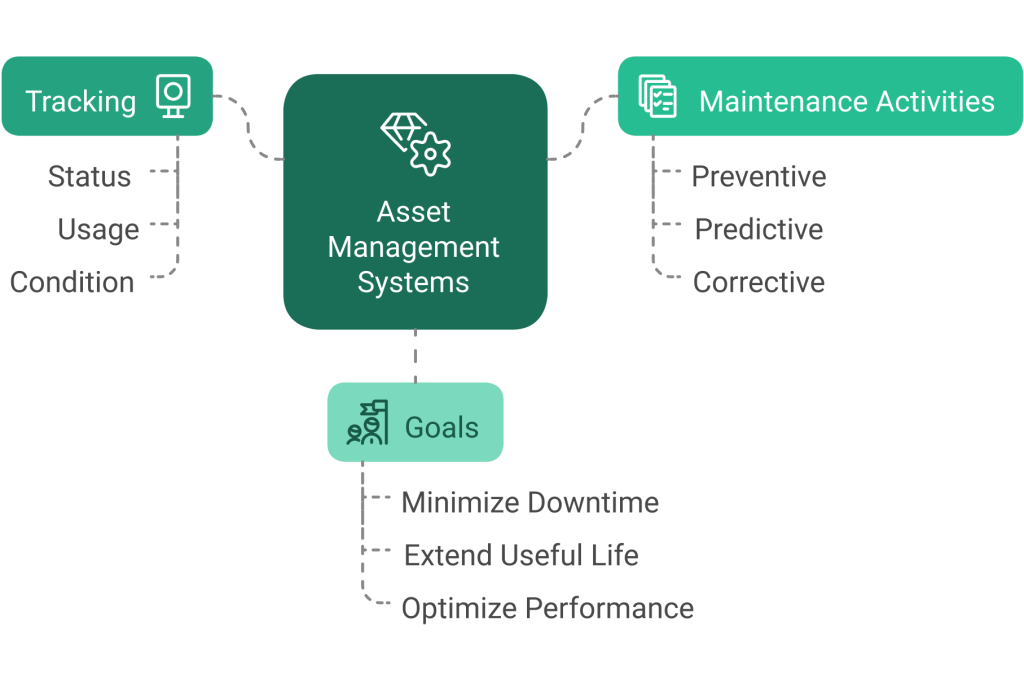
An important concept associated with assets is the asset register, which is a database that holds information like purchase dates, warranty status, maintenance history, and replacement schedules. This helps organizations decide when to repair, upgrade, or retire an asset.
By understanding and managing assets effectively, maintenance teams can improve operational efficiency, reduce unexpected failures, and ensure compliance with regulatory standards. As a result, assets become tools for production or service and key components in long-term planning and cost management.
What Tools Do Organizations Use to Manage Assets?
Here’s the breakdown of key tools:
- CMMS (Computerized Maintenance Management Systems)
- WorkTrek CMMS
- Manages work orders, schedules maintenance, tracks repairs
- Stores asset history and maintenance records
- EAM (Enterprise Asset Management)
- Broader than CMMS – includes financial planning
- Handles complete asset lifecycle management
- Integration with enterprise resource planning
- IoT Sensors & Monitoring
- Wireless sensors for temperature, vibration, pressure
- Real-time condition monitoring
- Predictive maintenance capabilities
- Integration with CMMS/EAM platforms
- Mobile Solutions
- Field service apps
- Digital inspection forms
- Barcode/QR code scanning
- Real-time data entry and access
- Building Management Systems (BMS)
- Controls HVAC, lighting, security
- Energy management
- Building automation
- Environmental monitoring
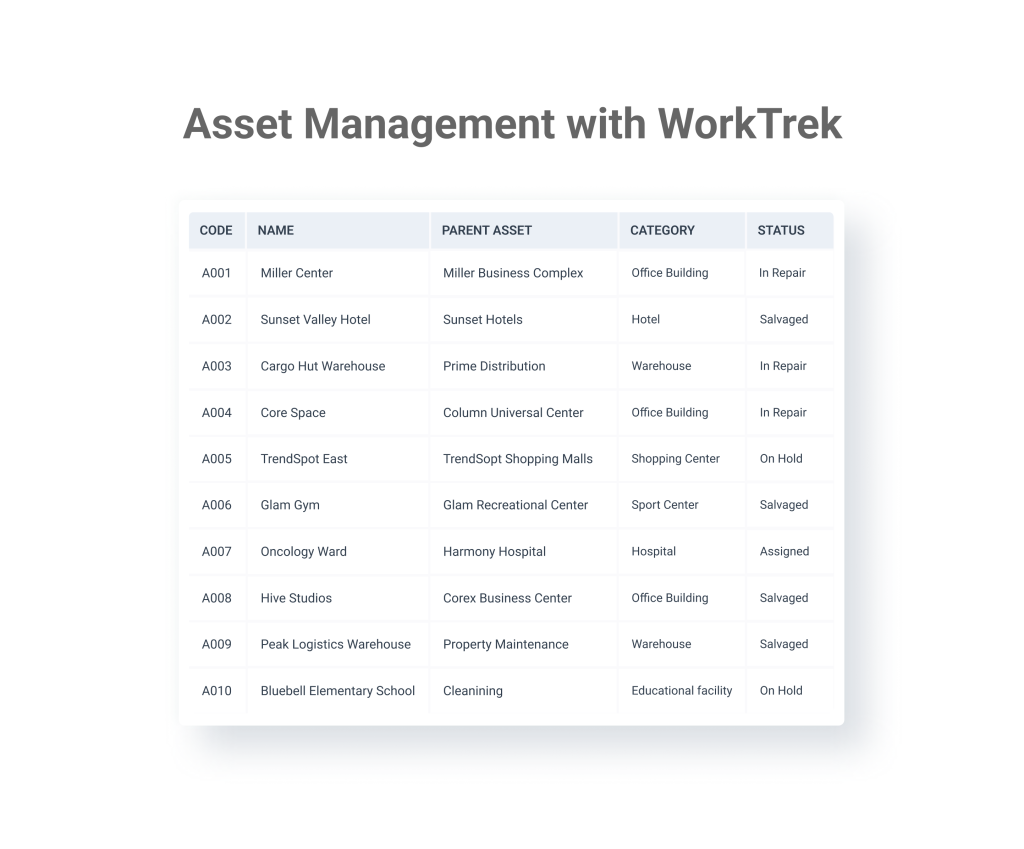
What are the best practices for managing assets?
Here are some best practices for managing assets in a maintenance organization:
- Maintain an accurate asset inventory: Keep a comprehensive and up-to-date record of all assets, including their location, condition, maintenance history, and other relevant information.
- Prioritize assets based on criticality: Identify critical assets significantly impacting operations and prioritize their maintenance accordingly.
- Implement a preventive maintenance program: Develop and execute a schedule for routine maintenance tasks to prevent breakdowns and extend asset life.
- Use a Computerized Maintenance Management System (CMMS): Leverage software to plan, track, and optimize maintenance activities, work orders, and spare parts inventory.
- Establish clear maintenance processes and procedures: Document and standardize maintenance workflows to ensure consistency and efficiency.
- Train maintenance staff: Provide regular training to ensure technicians have the necessary skills and knowledge to perform their duties effectively.
- Analyze asset performance data: Collect and analyze asset performance, maintenance costs, and downtime to identify improvement opportunities and make data-driven decisions.
- Implement condition-based monitoring: Use sensors and other technologies to monitor asset conditions in real-time, enabling proactive maintenance and reducing unplanned downtime.
- Manage spare parts inventory: Maintain an optimized inventory of critical spare parts to minimize downtime while avoiding overstocking.
- Continuously improve: Regularly review and refine maintenance strategies, processes, and technologies to continuously improve asset performance and maintenance efficiency.
- Collaborate with other departments: Work closely with operations, engineering, and other relevant departments to align maintenance activities with broader organizational goals and ensure smooth communication.
- Consider asset lifecycle costs: Make asset management decisions based on the total cost of ownership, including acquisition, operation, maintenance, and disposal costs.
Implementing these best practices allows maintenance organizations to optimize asset performance, reduce downtime, and control maintenance costs.
Get a Free WorkTrek Demo
Let's show you how WorkTrek can help you optimize your maintenance operation.
Try for free