What is Lean Maintenance?
Lean Maintenance is a systematic approach to maintenance management that focuses on eliminating waste, optimizing processes, and delivering maximum value with minimum resources.
This methodology adapts core lean manufacturing principles specifically for maintenance operations. It emerged from the Toyota Production System but has evolved to address the unique challenges of maintenance work.

Think of Lean Maintenance as similar to running a highly efficient kitchen where every tool has its place, ingredients are perfectly portioned, and cooking processes are standardized – but applied to maintaining equipment and facilities.
The goal is to create smooth, efficient maintenance operations that support reliability while eliminating unnecessary steps, waiting time, and excess inventory.
How’s it Used?
Organizations implement Lean Maintenance by first identifying and then systematically eliminating eight primary types of waste in maintenance operations:
Waiting time becomes a target – for example, reducing the time technicians spend waiting for parts, approvals, or equipment access.
A maintenance team might implement a digital work order system that automatically routes approvals and coordinates access permissions.
Optimizing tool storage and workplace layout can address motion waste. Consider a maintenance shop that reorganizes to place frequently used tools within easy reach and creates mobile tool carts for common repair scenarios.
Streamlining paperwork and procedures eliminates overprocessing waste. Rather than requiring multiple signatures for routine tasks, organizations might implement tiered approval systems based on job complexity and risk.
Improving logistics and part storage locations reduces transportation waste. For example, a facility might create satellite tool cribs near major equipment clusters rather than maintaining a single central storage location.
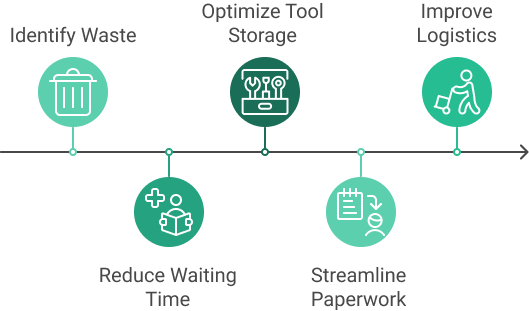
Inventory waste is managed by carefully analyzing parts usage patterns and establishing appropriate minimum/maximum levels. Instead of storing three months’ worth of air filters, a facility might maintain two weeks’ worth with reliable vendor relationships for quick replenishment.
Defect waste is attacked through root cause analysis and process standardization. When a repair fails prematurely, teams conduct detailed investigations to prevent recurrence rather than repeatedly fixing the same issue.
Skills waste is addressed through cross-training and better workforce utilization. Technicians might be trained on multiple equipment types to increase flexibility and reduce dependency on specific individuals.
Overproduction waste in maintenance appears to be an unnecessary preventive maintenance task. Teams analyze maintenance histories to optimize PM frequencies and eliminate tasks that don’t add value.
When to use Lean Maintenance?
Lean Maintenance principles work particularly well in:
Facilities with regular, predictable maintenance needs where standard processes can be established and refined. Manufacturing plants, for example, can create detailed standard work procedures for common maintenance tasks.
Organizations with stable workforces where training and continuous improvement investments can yield long-term benefits. This allows for the development of deep equipment knowledge and refined processes.
Operations where maintenance activities significantly impact overall efficiency. Consider an airline maintenance facility where aircraft turnaround time directly affects profitability.
Environments with strong management support for process improvement and cultural change. Successful implementation requires a sustained commitment to changing traditional maintenance practices.
Implementation Strategies
Successful Lean Maintenance implementation typically follows several key phases:
Value Stream mapping becomes the first step, where teams analyze current maintenance processes to identify waste and improvement opportunities. They might track a typical preventive maintenance task from start to finish, noting all delays and inefficiencies.
5S workplace organization principles are applied to maintenance shops and storage areas. Tools and parts are organized, labeled, and standardized, and organization is maintained through regular audits.
Standard work procedures are developed for common maintenance tasks, incorporating best practices and safety requirements.
These procedures are regularly reviewed and updated based on technician feedback and performance data.
Visual management systems are implemented to make process status immediately apparent. Maintenance shops might use color-coded boards showing work status, technician assignments, and parts availability.
Continuous improvement processes are established through regular team meetings and improvement events.
For example, teams might hold weekly sessions to review recent problems and suggest process improvements.
Key Success Factors
- Strong leadership support and commitment to lean principles
- Effective training programs for all maintenance staff
- Regular measurement and monitoring of key performance indicators
- Employee engagement in improvement initiatives Integration with other business systems and processes
Benefits of Successful Implementation
- Reduced maintenance costs through elimination of waste Improved equipment reliability and availability
- Faster response times to maintenance needs
- Better utilization of maintenance resources Increased job satisfaction among maintenance staff
- Enhanced safety through standardized procedures
Get a Free WorkTrek Demo
Let's show you how WorkTrek can help you optimize your maintenance operation.
Try for free