Lean Manufacturing is a systematic approach to production that focuses on maximizing customer value while minimizing waste. This methodology originated from Toyota’s Production System (TPS) in the mid-20th century, which Taiichi Ohno and Eiji Toyoda developed. The fundamental idea is to create more value for customers using fewer resources by optimizing the entire value stream, from raw materials to final product delivery.
Think of Lean Manufacturing as similar to preparing a complex meal in a professional kitchen. Just as a chef ensures ingredients arrive fresh when needed, tools are perfectly organized, and cooking processes are standardized to create high-quality dishes without waste consistently, lean manufacturing applies these same principles to production environments.
How is it used?
Organizations implement Lean Manufacturing through several core principles and practices:
Value identification comes first. Companies must understand exactly what customers value and are willing to pay for. For example, an automotive manufacturer might learn that customers value fuel efficiency and safety features more than high-speed performance, directing production focus accordingly.
Value stream mapping examines the entire production process to identify steps that add value and eliminate those that don’t. Consider a furniture manufacturer tracking a piece of wood from raw lumber to a finished cabinet, analyzing each step for waste reduction opportunities.
Flow optimization ensures products move smoothly through production without interruption. Instead of producing large batches that create inventory and waiting time, an electronics manufacturer might set up assembly lines that complete one product at a time, passing it immediately to the next station.
Pull systems allow customer demand to drive production rather than pushing products based on forecasts. A clothing manufacturer might only begin producing new items when inventory reaches certain threshold levels, triggered by actual sales rather than predictions.
Continuous improvement, or Kaizen, becomes part of the organizational culture. Teams regularly analyze processes and implement small improvements. For instance, workers might suggest and implement better ways to organize tools or modify workstation layouts to reduce motion waste.
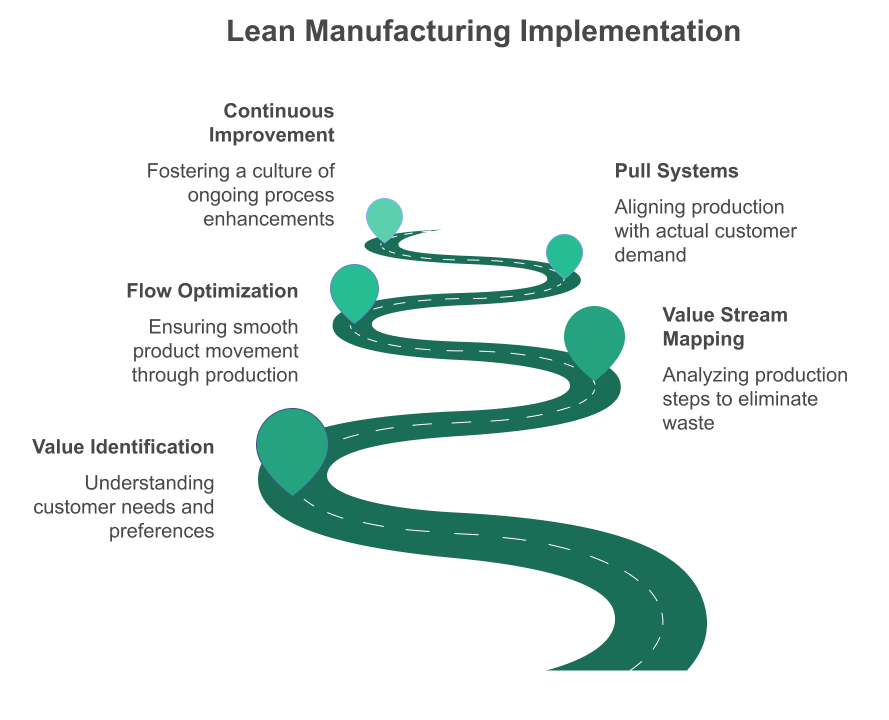
When to use Lean Manufacturing?
Lean principles work particularly well in:
Repetitive manufacturing environments where processes can be standardized and refined over time. Automotive assembly plants exemplify this with highly optimized, repeatable processes.
Operations with relatively stable demand patterns that allow for reliable pull systems. Consumer electronics manufacturing often benefits from this predictability.
Industries where quality consistency is crucial. Medical device manufacturing, for example, requires the strict process control that lean principles provide.
Environments where waste reduction directly impacts profitability. Industries with thin margins, like food processing, particularly benefit from lean efficiency improvements.
Implementation Strategies
Successful implementation typically involves several key elements:
The 5S system (Sort, Set in order, Shine, Standardize, Sustain) provides a foundation for workplace organization. A manufacturing facility might start by thoroughly organizing workstations, marking tool locations, and establishing cleaning routines.
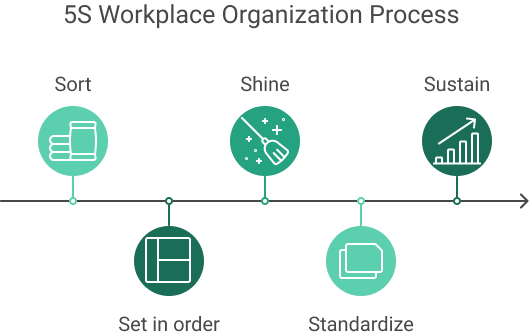
Visual management makes process status immediately apparent to all workers. Production boards might use visual indicators to show real-time production rates, quality metrics, and maintenance status.
Standard work procedures ensure consistency and efficiency. Detailed work instructions might specify each operation’s exact steps, timing, and quality checks.
Quick changeover techniques (SMED—Single Minute Exchange of Dies) reduce production line downtime between products. For example, a bottling plant might optimize its process to switch between different drink types in minutes rather than hours.
Total Productive Maintenance (TPM) involves operators in basic equipment maintenance, reducing downtime and extending equipment life. Operators might perform daily equipment checks and basic maintenance tasks rather than waiting for maintenance staff.
Common Challenges and Solutions
Implementation often faces several obstacles:
Cultural resistance to change requires patient leadership and clear communication about benefits. Successful organizations often start with pilot areas to demonstrate success before broader implementation.
Initial efficiency drops during implementation and needs management support to persist through the learning curve. Teams might need time to adjust to new procedures before seeing improvement.
Investment in training and possible equipment modifications requires careful ROI justification. Companies often begin with low-cost improvements to build momentum and justify larger investments.
What are the Benefits of Implementation
- Reduced manufacturing costs through the elimination of waste
- Improved product quality through standardized processes
- Shorter lead times and faster customer response
- Reduced inventory carrying costs
- Improved employee engagement and job satisfaction
- Enhanced competitive position through operational excellence
Get a Free WorkTrek Demo
Let's show you how WorkTrek can help you optimize your maintenance operation.
Try for free