What are Maintenance Triggers?
A maintenance trigger is a specific condition, event, or measurement that signals when maintenance work should be performed on equipment or assets. Think of these triggers as warning signs or indicators that tell us when a piece of equipment needs attention—similar to how your car’s dashboard lights illuminate to indicate various issues or required service.

Maintenance triggers are foundational to effective asset management because these triggers determine the timing and nature of maintenance interventions. Understanding triggers helps organizations move from reactive to more predictive and proactive maintenance approaches.
Maintenance Triggers Categories
Maintenance triggers generally fall into several key categories:
Time-Based Triggers
These are perhaps the most straightforward types of maintenance triggers based purely on the passage of time or calendar dates. Imagine how you might change your home’s air filters every three months—that’s a time-based trigger. In industrial settings, these triggers might initiate daily inspections, weekly cleanings, monthly calibrations, or annual overhauls. The timing is typically based on manufacturer recommendations, historical data, or regulatory requirements.
Usage-Based Triggers
These triggers activate after a certain amount of use or wear, measured in operating hours, cycles, miles, or production counts. Consider how a car needs an oil change after a certain number of miles—that’s a usage-based trigger. In manufacturing, this might mean maintaining a machine after it produces a specific number of parts or operates for a set number of hours.
Condition-Based Triggers
These more sophisticated triggers respond to equipment conditions measured through various monitoring techniques.
They might include:
- Temperature readings exceeding normal ranges
- Unusual vibration patterns
- Changes in oil composition
- Electrical current fluctuations
- Pressure variations
- Noise level changes
Think of these like your body’s vital signs – just as elevated blood pressure might trigger a visit to the doctor, abnormal equipment readings trigger maintenance responses.
Performance-Based Triggers
These triggers activate when equipment performance falls below acceptable levels. For example:
- Decreased production speed
- Lower quality output
- Reduced efficiency
- Increased energy consumption
- Higher scrap rates
Imagine how you might take your car to a mechanic when you notice it’s using more fuel than usual – that’s a performance-based trigger.
Event-Based Triggers
These triggers respond to specific events or incidents, such as:
- Equipment failures
- Safety incidents
- Environmental conditions
- Operator observations
- Quality issues
- Regulatory inspections
The effectiveness of maintenance triggers depends on several factors:
Threshold Setting
Organizations must carefully determine the right trigger points – set them too sensitively, and you’ll waste resources on unnecessary maintenance; set them too loosely and risk equipment failure.
This process often requires balancing multiple considerations:
- Equipment criticality
- Safety requirements
- Cost implications
- Production demands
- Resource availability
Monitoring Systems
Different triggers require different monitoring approaches:
- Simple visual inspections
- Manual measurements
- Automated sensor systems
- Computerized monitoring
- Regular testing procedures
The selection of appropriate monitoring methods depends on factors like equipment value, failure consequences, and monitoring costs.
Response Planning
Once a trigger activates, organizations need clear procedures for:
- Evaluating the trigger’s significance
- Determining the appropriate response
- Allocating necessary resources
- Scheduling maintenance activities
- Documenting actions taken
Modern Developments
Contemporary maintenance triggers are becoming increasingly sophisticated with the advent of:
- Internet of Things (IoT) sensors
- Artificial Intelligence analysis
- Machine learning algorithms
- Real-time monitoring systems
- Predictive analytics
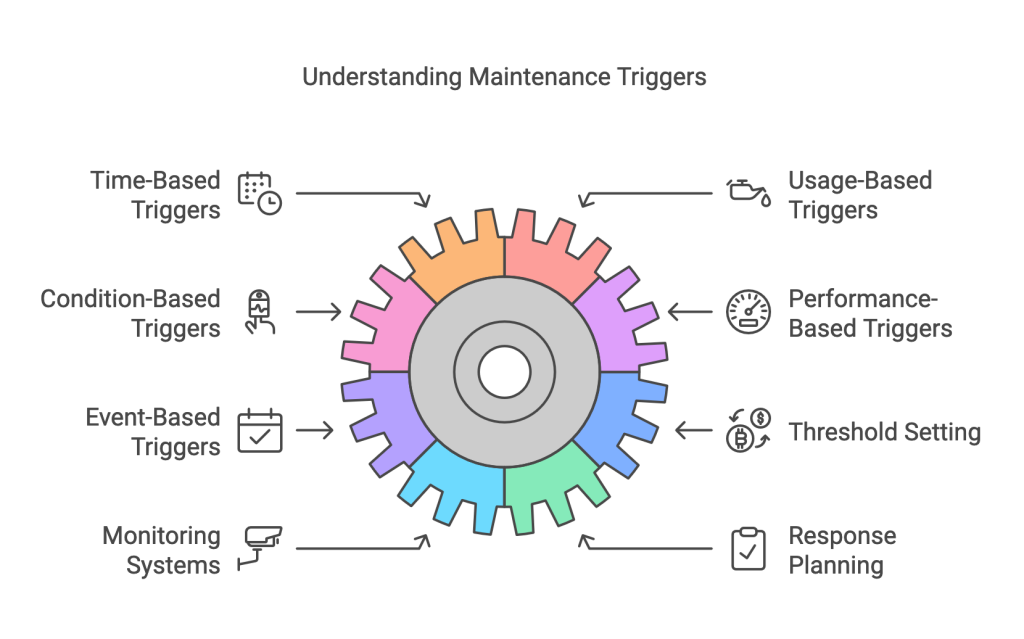
These technologies enable more precise and predictive triggering of maintenance activities, similar to how modern medical devices can continuously monitor patients and alert healthcare providers before serious problems develop.
Get a Free WorkTrek Demo
Let's show you how WorkTrek can help you optimize your maintenance operation.
Try for free