What is Maintenance Repair and Operations?
Maintenance, Repair, and Operations (MRO) refers to the activities, supplies, equipment, and processes needed to keep an organization’s facilities and equipment functioning properly. MRO practices include all actions required for preserving and restoring industrial equipment and systems to their optimal working condition while ensuring workplace safety and regulatory compliance.
Definition and Overview
MRO stands for Maintenance, Repair, and Operations. It encompasses all the activities, processes, and tasks associated with maintaining a plant, facility, or equipment. MRO is essential for ensuring the smooth operation of a business, as it involves the maintenance of physical infrastructure, equipment, and materials and supplies used to maintain infrastructure and equipment. Effective MRO management is critical for reducing downtime, improving operational efficiency, and increasing cost savings.
In short, MRO is the backbone of any organization’s operational framework. Without proper MRO management, businesses can face frequent equipment failures, production halts, and increased operational costs.
By investing in MRO practices, companies can ensure that their production processes run smoothly, leading to enhanced productivity and significant cost savings.
MRO Methods
Below is a list of MRO Methods:
Preventive Maintenance
This proactive approach involves regular maintenance activities to prevent equipment failure and reduce emergency maintenance. For example, a manufacturing plant might schedule monthly bearing lubrication and belt tension checks on production machinery. This reduces unexpected breakdowns but requires a consistent investment of time and resources.
Predictive Maintenance
Advanced analytics and sensors monitor equipment performance and predict potential failures before they occur, reducing equipment downtime. Consider a power plant that uses vibration analysis sensors on turbines to detect subtle changes indicating upcoming maintenance needs. This approach optimizes maintenance timing but requires sophisticated technology and expertise.
Corrective Maintenance
Repairs are performed after equipment failure occurs. While this reactive approach might seem cost-effective initially, it often leads to more extended downtime and higher emergency repair costs. Think of it like waiting for your car to break down entirely before servicing it.
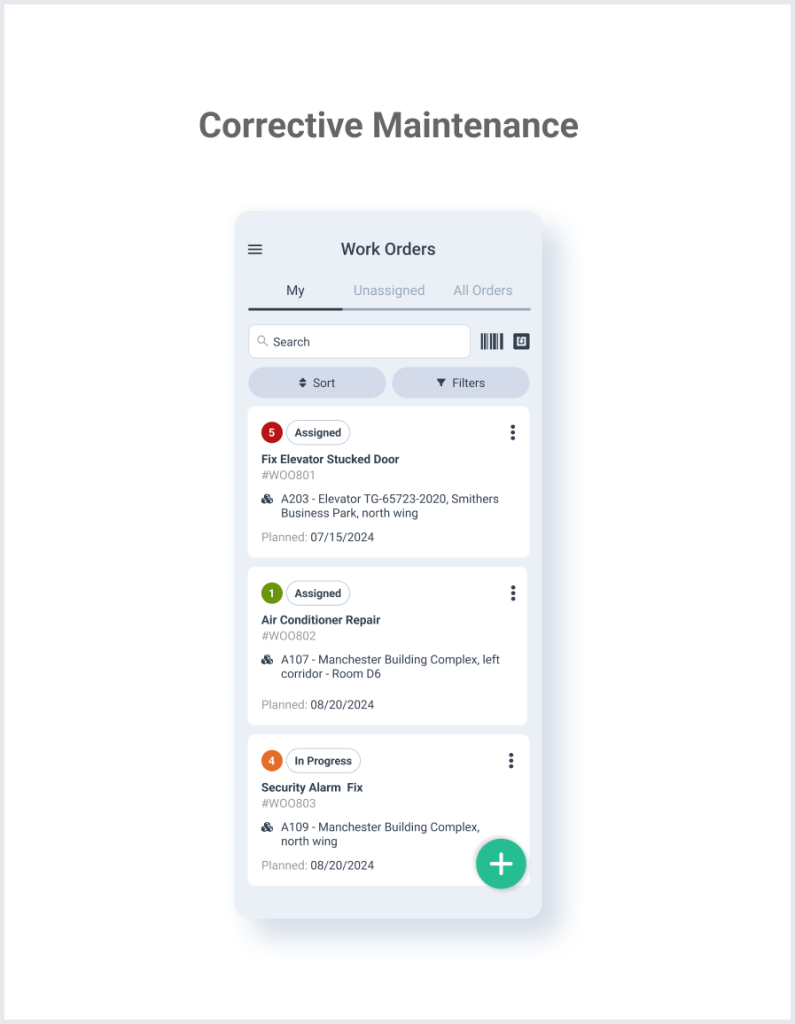
Pros of MRO
- Reduced downtime through regular maintenance
- Cost savings by preventing major repairs
- Improved workplace safety through the use of personal protective equipment
- Enhanced equipment lifespan through proper care
Pros of MRO:
- Extended equipment lifespan through proper care and maintenance
- Reduced frequency of catastrophic failures
- Improved workplace safety through well-maintained equipment
- Better compliance with regulatory requirements
- Enhanced operational efficiency and productivity
- Lower long-term operational costs
Cons of MRO:
- Requires significant upfront investment in tools, parts, and training
- Can involve substantial labor costs for maintenance personnel
- May cause temporary production interruptions during maintenance
- Needs careful inventory management of spare parts
- Requires ongoing staff training to keep up with new technologies
Types of MRO
Raw Material
MRO encompasses materials used in manufacturing processes that don’t become part of the final product. These include lubricants, cleaning supplies, and coolants to keep production equipment running smoothly.
Managing raw material MRO requires careful inventory control to prevent production disruptions while avoiding excess stock.
Tools and Supplies
Maintenance MRO consists of the tools and supplies needed for equipment upkeep and repair. This category includes everything from basic hand and power tools to sophisticated diagnostic equipment. It also covers spare parts for machinery, equipment, and consumable items such as filters, belts, and bearings. The effective management of maintenance MRO is crucial for minimizing equipment downtime.
Operating Supply
Operating Supplies form another essential category, covering the daily consumables needed to keep operations running. This includes office supplies like paper and ink, safety equipment such as gloves and goggles, janitorial supplies, and packaging materials. While these items seem minor individually, they’re crucial for smooth daily operations.
Production Support
Production Support Equipment represents non-production machinery and tools that support manufacturing processes. This includes material handling equipment like forklifts and pallet jacks, storage systems, quality control equipment, and computer systems. These items typically require substantial investment and careful maintenance planning. Regular maintenance ensures operational efficiency and prevents idle time and disruptions.
Infrastructure MRO inventory
Infrastructure MRO focuses on facility maintenance supplies and components, including HVAC system parts, electrical supplies, plumbing materials, and building repair supplies, all essential for infrastructure repair in maintaining commercial facilities and associated systems. It requires long-term planning and consideration of facility lifecycle costs.
Testing and Lab MRO
Laboratory and Testing MRO includes calibration equipment, testing materials, laboratory instruments, and measurement devices. This category is significant for quality control and regulatory compliance. Managing these items often requires special attention to accuracy and certification requirements. The term ‘MRO stand’ refers to the various tasks and actions that ensure the upkeep of facilities and essential equipment, highlighting the importance of maintenance, repair, and operations in maintaining operational efficiency.
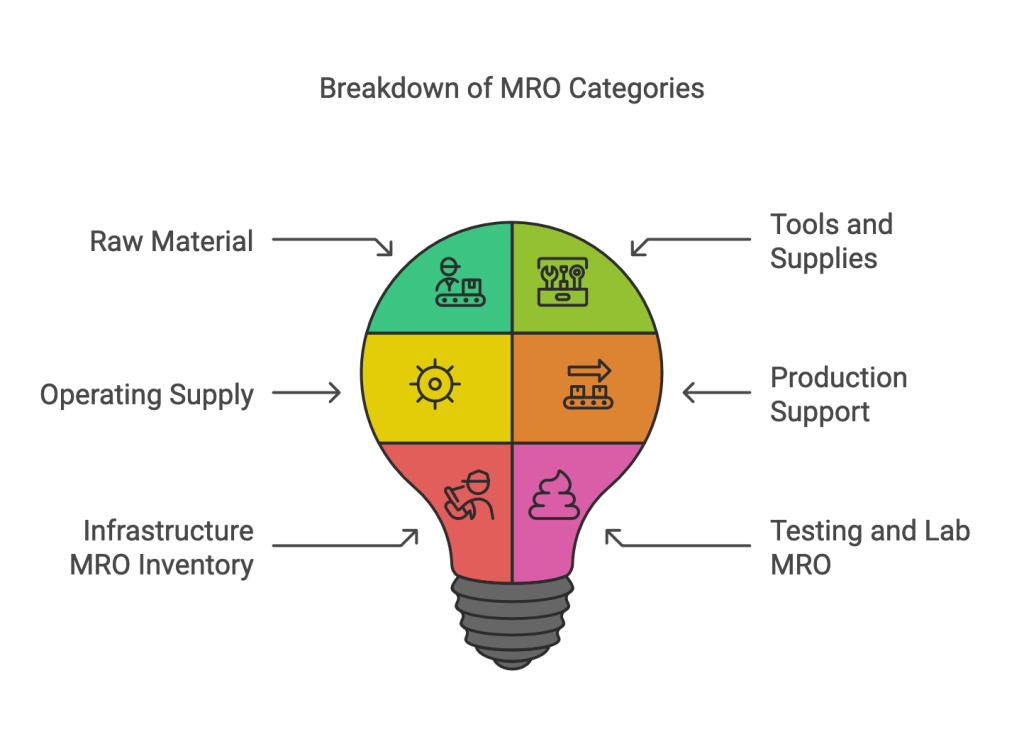
MRO Inventory Management
MRO inventory management manages and controls the stock of maintenance, repair, and operations materials and supplies. It involves tracking inventory levels, monitoring usage, and optimizing stock levels to ensure that the right materials are available when needed. Proper MRO inventory management is essential for reducing downtime, improving maintenance efficiency, and minimizing MRO costs.
Effective inventory management ensures that maintenance tasks are completed on time and that production processes are not disrupted. For instance, having a well-organized MRO inventory means that spare parts for critical machinery are readily available, preventing costly production delays. Additionally, by optimizing stock levels, businesses can avoid the pitfalls of overstocking or stockouts, leading to better cost control and operational efficiency.
Safety and Compliance MRO
Safety and Compliance MRO covers emergency response equipment, first aid supplies, environmental control equipment, and regulatory compliance materials. This category directly impacts workplace safety and legal compliance, making it particularly critical for risk management.
Information Technology MRO
Technology and IT MRO encompasses computer hardware, network equipment, software licenses, and communication systems. This category has grown in importance and complexity as businesses become increasingly digitized.
Each MRO type requires different management approaches based on criticality, procurement strategy, and usage patterns. Critical items that immediately impact operations need different handling than general supplies with minimal operational impact. Similarly, high-volume consumables require different inventory strategies than specialized, low-frequency items.
MRO Roles and Responsibilities
MRO involves various roles and responsibilities, including procurement officers, supplier relationship managers, inventory managers, and maintenance technicians. Each plays a critical part in ensuring the smooth operation of MRO activities.
Procurement Officers
Procurement officers are responsible for purchasing MRO materials and supplies. They assess suppliers, products, and services to negotiate contracts and ensure that high-quality, cost-effective MRO products are purchased. Procurement officers also ensure that MRO purchases are aligned with the organization’s overall procurement strategy and goals.
Procurement officers help reduce MRO costs and ensure a steady supply of necessary materials by carefully selecting suppliers and negotiating favorable terms. Their role is crucial in maintaining the balance between cost-effectiveness and quality, directly impacting the efficiency of maintenance repair and operations.
Supplier Relationship Managers
Supplier relationship managers are responsible for maintaining relationships with MRO suppliers. They research, prioritize, and purchase order arrangements to ensure the organization has the required MRO materials and supplies. Supplier relationship managers also work closely with procurement officers to negotiate contracts and ensure that suppliers meet the organization’s quality and delivery standards.
Effective supplier relationship management ensures that the organization receives reliable and timely deliveries of MRO supplies, which is vital for uninterrupted production processes. By fostering strong relationships with suppliers, these managers can negotiate better terms and ensure that the quality of materials meets the organization’s standards, contributing to overall operational efficiency.
Benefits of Implementing MRO
The benefits of implementing a robust MRO strategy extend beyond just keeping equipment running. Organizations experience:
Improved Asset Performance
Regular maintenance ensures equipment operates at peak efficiency, reducing energy consumption and improving output quality. For instance, a well-maintained HVAC system can reduce energy costs by 15-20% compared to a poorly maintained one.
Enhanced Safety and Compliance
Properly maintained equipment reduces workplace accidents and helps meet regulatory requirements. This not only protects workers but also prevents costly fines and legal issues.
Better Cost Control
While MRO requires investment, effective production equipment repair prevents more expensive emergency repairs and replacement costs. Consider how regular oil changes in a vehicle cost far less than replacing a seized engine.
Streamline MRO with CMMS
Computerized Maintenance Management Systems (CMMS) are crucial in modern MRO management.
Here’s how organizations can effectively use CMMS:
Asset Tracking
CMMS maintains detailed records of all equipment, including maintenance history, technical specifications, and location. This creates a comprehensive equipment lifecycle database that helps make informed maintenance decisions, ensuring a smooth and efficient production process.
Work Order Management
The system automatically generates and tracks maintenance work orders based on predetermined schedules or condition monitoring alerts. This ensures that no maintenance tasks are overlooked and provides accountability for completion.
Inventory Control
CMMS helps optimize spare parts inventory by tracking usage patterns, automating reordering, and preventing stockouts. For example, if a critical machine component typically needs replacement every six months, the system can ensure parts are ordered in advance.
Data Analysis and Reporting
Modern CMMS platforms provide powerful analytics capabilities to identify trends, optimize maintenance schedules, and demonstrate ROI. This data-driven approach helps maintenance teams move from reactive to predictive maintenance strategies.
Documentation Management
All maintenance procedures, safety protocols, and equipment manuals can be stored digitally and easily accessed by maintenance staff. This ensures consistency in maintenance procedures and helps with training new personnel.
Implement CMMS to Optimize MRO
Think of CMMS as the central nervous system of your maintenance operations, coordinating all aspects of MRO management.
Manage Inventory Levels
At its core, CMMS helps track and manage inventory levels of MRO supplies. The system continuously monitors stock levels for parts and supplies, automatically generating purchase orders when inventory reaches predetermined minimum levels.
For example, when the stock of air filters drops below 20 units, the system can automatically trigger a reorder process, ensuring you never run out of critical supplies.
Work Order Management
CMMS also revolutionizes work order management by creating a systematic approach to maintenance tasks. When a machine requires scheduled maintenance, the system automatically generates a work order, assigns it to qualified technicians, and lists all the necessary parts and tools. This prevents the common problem of forgotten maintenance tasks or miscommunication about resource requirements.
Track Assets
Asset tracking becomes significantly more efficient with CMMS. Each piece of equipment gets a unique identifier, allowing you to track its complete maintenance history, parts usage, and performance metrics. Imagine instantly pulling up the entire service history of a production line, including every repair, part replacement, and maintenance check ever performed.
Predictive Maintenance
The predictive maintenance capabilities of modern CMMS systems are particularly powerful. By analyzing historical data and equipment performance metrics, these systems can predict when failures might occur. For instance, if a particular bearing typically fails after 5,000 hours of operation, the system can schedule replacement at 4,800 hours, preventing unexpected breakdowns.
Manage Costs
CMMS makes cost tracking and analysis much more sophisticated. The system records all MRO-related expenses, from parts and supplies to labor hours and contractor costs. This detailed financial tracking helps organizations identify areas where they’re spending too much and opportunities for cost reduction. For example, you might discover that one brand of bearings lasts twice as long as another while only costing 20% more.
Improved Compliance
CMMS also enhances regulatory compliance by maintaining detailed records of all maintenance activities. When an auditor asks for maintenance records from the past three years, you can generate comprehensive reports with a few clicks instead of digging through paper files. This documentation includes who performed the work, what procedures they followed, and what parts they used.
3rd Party Integrations
The system can integrate with other business systems, such as ERP (Enterprise Resource Planning) or procurement. This integration ensures that MRO management aligns with broader business operations. For example, when an extensive maintenance project is scheduled, the system can automatically check if required parts are in stock and, if not, initiate the procurement process while considering lead times and budget constraints.
Mobile Apps
Mobile capabilities in modern CMMS allow technicians to access and update information anywhere in the facility. Using tablets or smartphones, they can view work orders, access equipment manuals, update maintenance records, and even order parts while standing beside the equipment they’re servicing. This real-time information flow significantly improves efficiency and accuracy.
Reporting and Analytics
Perhaps most importantly, CMMS provides powerful analytics and reporting capabilities. The system can analyze trends in equipment performance, maintenance costs, and parts usage to help make better decisions. For instance, you might discover that specific preventive maintenance tasks could be performed less frequently without increasing failure rates, leading to significant cost savings.
Steps to Implement CMMS
To implement CMMS effectively, organizations should:
- Start with clear objectives and KPIs
- Ensure proper staff training on the system
- Regularly update asset information and maintenance procedures
- Use mobile capabilities for real-time updates
- Review and analyze data regularly to improve processes
Get a Free WorkTrek Demo
Let's show you how WorkTrek can help you optimize your maintenance operation.
Try for free