What is Meter-Based Maintenance?
Meter-based maintenance (MBM) is a strategy that schedules equipment maintenance based on actual usage metrics (like operating hours, cycles, or distance) rather than fixed calendar intervals.
This approach ensures maintenance is performed when necessary, optimizing equipment reliability and minimizing unnecessary servicing by utilizing equipment usage metrics.
How Does it Work?
Meter-based maintenance is a type of preventive maintenance that uses meter readings to determine when maintenance is required. Unlike traditional time-based maintenance, which relies on fixed calendar intervals, meter-based maintenance is a data-driven approach that adapts to the actual usage of equipment.
This means maintenance tasks are performed only when necessary, based on metrics such as operational hours, cycle counts, miles driven, and more.
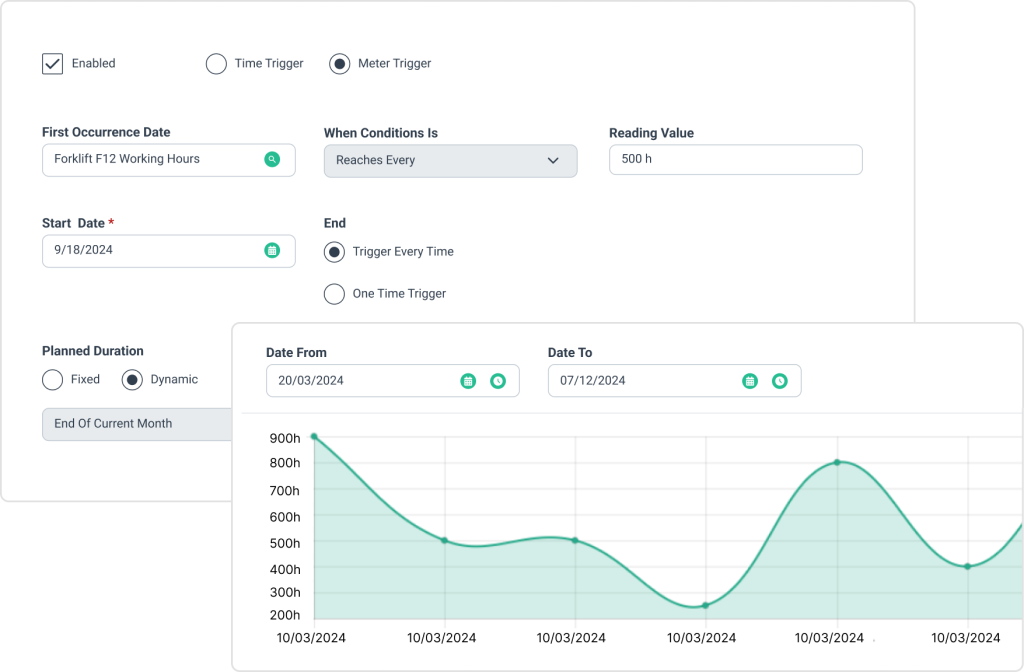
Aligning maintenance schedules with actual equipment usage can help organizations reduce high maintenance costs, increase equipment reliability, and optimize overall operational efficiency.
This approach ensures that resources are used effectively, preventing both premature maintenance and the risk of equipment failure due to delayed servicing.
Benefits of Meter-Based Maintenance
Meter-based maintenance offers several advantages over traditional time-based approaches.
First, it aligns maintenance directly with actual equipment wear and tear, preventing premature maintenance that wastes resources and delayed maintenance that risks equipment failure.
For example, maintaining a forklift after 500 operating hours rather than every three months ensures service is performed when genuinely needed, regardless of how intensively the equipment is used.
Furthermore, MBM typically reduces maintenance costs by eliminating unnecessary service intervals while extending equipment life through more precise maintenance timing.
Organizations often report 15-30% reductions in maintenance costs after effectively implementing MBM programs. This approach also lowers maintenance costs by identifying potential issues before they escalate.
The approach improves equipment reliability since maintenance is based on actual usage patterns rather than arbitrary calendar dates.
How Does Meter-Based Maintenance Works
The process begins with establishing usage metrics for each piece of equipment. These meters track actual equipment utilization, such as operating hours, miles driven, or production cycles completed.
When equipment reaches predetermined threshold values, the system triggers maintenance tasks.
For instance, an industrial printer might receive maintenance every 10,000 prints, while a delivery truck might be serviced every 5,000 miles.
The system continuously monitors these usage metrics and automatically generates work orders as equipment approaches its maintenance thresholds.
This creates a dynamic maintenance schedule that adapts to varying equipment usage patterns.
Key Metrics for Tracking Preventive Maintenance Tasks
Several essential metrics help organizations monitor and optimize their meter-based maintenance programs. The primary usage metrics typically include:
- Operating hours
- Tracking actual running time of equipment Cycle counts
- Measuring the number of operations performed Distance traveled
- For mobile equipment Production volume
- Units produced or processed Energy consumption
- Power usage as a proxy for wear
Additionally, organizations should track performance metrics such as:
- Mean Time Between Failures (MTBF) –
- Validate maintenance intervals Maintenance costs per operating hour –
- Assess program efficiency Equipment downtime
- Measure maintenance effectiveness Compliance rate –
- Percentage of maintenance performed within specified meter readings
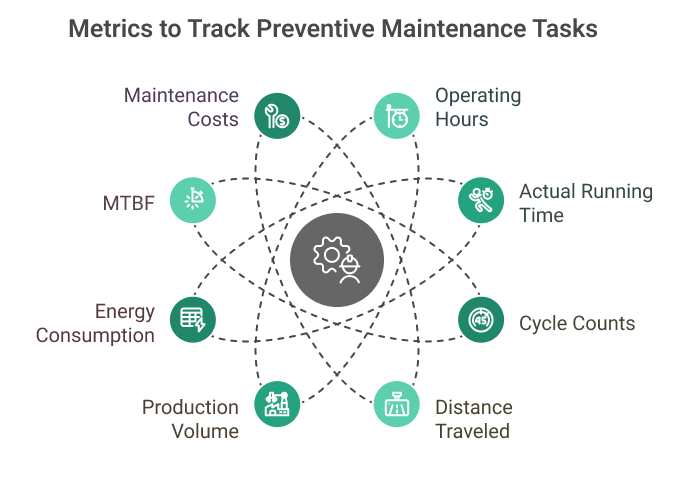
Implementing a Meter-Based Maintenance Program
Successful implementation requires a systematic approach. First, an equipment audit must identify assets suitable for meter-based maintenance. Not all equipment benefits equally from this approach – critical equipment with clear usage patterns is typically the best candidate.
Next, establish appropriate meter thresholds for each maintenance task. This often involves analyzing manufacturer recommendations, historical maintenance data, and equipment failure patterns. Start conservative with thresholds and adjust based on performance data.
The implementation also requires proper technology infrastructure. An essential component is a computerized maintenance management system (CMMS) that tracks meter readings and automatically generates work orders.
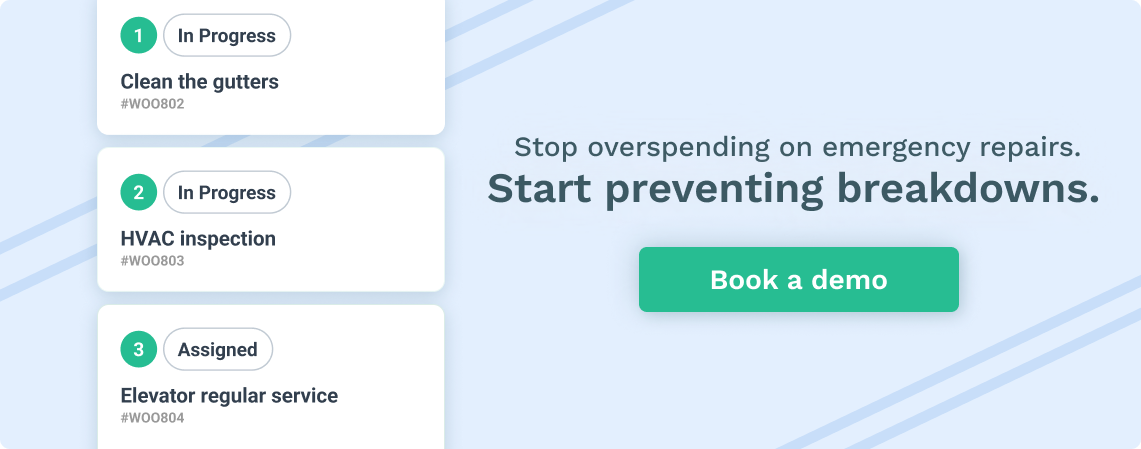
Predictive maintenance (PdM) can further enhance this approach by utilizing data analytics and sensor technologies to foresee equipment failures, enabling proactive maintenance strategies and reducing unplanned downtime.
Many modern equipment have built-in sensors and monitoring capabilities that can automatically update meter readings in the CMMS.
Train maintenance staff on the new system and establish clear procedures for recording meter readings and responding to maintenance triggers.
Regularly reviewing and adjusting thresholds based on equipment performance data helps optimize the program.
Meter-Based Maintenance Implementation Challenges and Maintenance Costs
To deepen your understanding, let me provide some concrete examples of meter-based maintenance across different industries and equipment types.
Meter-based PMs offer a significant advantage over time-based approaches. They use actual usage metrics to schedule maintenance tasks, allowing organizations to tailor maintenance strategies based on real-time operational data and enhance overall efficiency.
Manufacturing Equipment Example: Consider an industrial injection molding machine that produces plastic components. Rather than servicing it every month, the maintenance schedule might be based on:
- Main hydraulic system maintenance every 2,500 operating hours
- Die cleaning and inspection every 10,000 injection cycles
- Complete overhaul every 50,000 cycles
This approach accounts for varying production demands. When the machine runs 24/7 during peak seasons, it receives more frequent maintenance than during slower periods when it only operates one shift daily.
Vehicle Fleet Example:
A delivery company operating a fleet of trucks might implement meter-based maintenance like this: Engine oil changes every 7,500 miles instead of every three months, Transmission fluid replacement every 50,000 miles, Brake inspections every 15,000 miles, Tire rotation every 6,000 miles
The system automatically flags vehicles approaching these thresholds, allowing fleet managers to schedule maintenance during non-peak delivery times. This prevents unnecessary early maintenance on rarely used vehicles and overdue maintenance on heavily used ones.
Meter-Based Preventive Maintenance Tasks
Meter-based preventive maintenance tasks are designed to prevent equipment failures and reduce downtime by addressing potential issues before they become serious problems.
These tasks can include routine inspections, cleaning, lubrication, and adjustments tailored to the equipment’s specific needs and usage patterns.
For instance, a continuously operating machine might require more frequent lubrication and inspection than one used sporadically.
By performing these preventive maintenance tasks regularly, maintenance teams can help extend the equipment’s life, reduce maintenance costs, and ensure that the equipment operates reliably.
This proactive maintenance approach helps minimize unexpected breakdowns and keeps the equipment running smoothly, contributing to overall operational efficiency.
Using CMMS for Meter-Based Maintenance
A Computerized Maintenance Management System (CMMS) like WorkTrek can be a powerful tool for supporting meter-based maintenance. A CMMS helps track equipment usage, schedule maintenance tasks, and manage maintenance records in one centralized system.
Using a CMMS, maintenance teams can streamline their maintenance processes and make data-driven decisions. The system can automatically generate work orders based on meter readings, ensuring that maintenance tasks are scheduled correctly.
This improves overall operational efficiency and helps reduce maintenance costs by preventing unnecessary maintenance and minimizing equipment downtime.
Additionally, a CMMS provides valuable insights into equipment performance and maintenance history, enabling maintenance managers to optimize their maintenance strategy and improve asset management.
Healthcare Equipment Example
An MRI machine in a hospital might have maintenance scheduled based on scan counts:
- Helium level checks every 500 scans
- Gradient coil inspection every 2,000 scans
- Full calibration every 5,000 scans Major preventive maintenance every 10,000 scans
This ensures that high-volume facilities maintain their equipment more frequently than facilities with lower patient volumes, optimizing safety and equipment longevity.
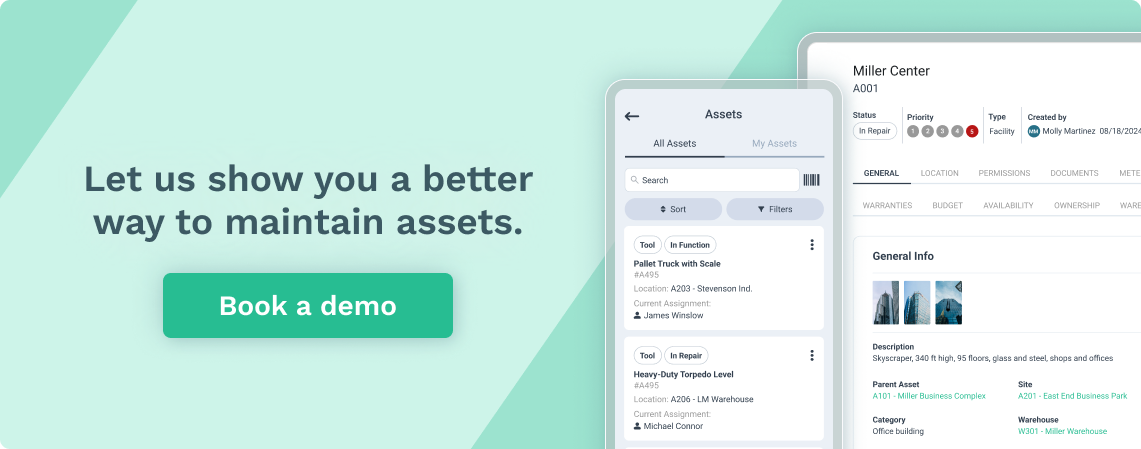
Construction Equipment Example
For a hydraulic excavator, maintenance might be structured as:
- Daily fluid level checks (calendar-based)
- Hydraulic oil filter replacement every 500 operating hours
- Track tension adjustment every 100 operating hours
- Complete undercarriage inspection every 2,000 operating hours
The combination of both meter-based and some calendar-based maintenance ensures comprehensive equipment care while accounting for varying usage intensities across different construction projects.
Building Systems Example
Consider an HVAC system in a commercial building:
- Filter replacement every 2,000 running hours
- Belt inspection every 1,500 running hours
- Coil cleaning every 3,000 running hours
- Compressor maintenance every 5,000 running hours
This approach accounts for seasonal variations in HVAC usage, ensuring more frequent maintenance during peak cooling or heating seasons.
Production Line Example
A high-speed bottling line might implement meter-based maintenance like this:
- Conveyor belt inspection every 100,000 bottles
- Filling head maintenance every 500,000 cycles
- Labeler calibration every 50,000 labels
- Complete line maintenance every 1,000,000 bottles
This ensures maintenance aligns with actual production volumes rather than calendar time, which is especially important for facilities with varying production schedules.
Industries Benefiting from Meter-Based Maintenance
Maintenance based on meter readings is exceptionally useful for sectors that employ machinery 24/7. Industries such as fleet management depend on maintenance strategies informed by meter data to guarantee their vehicles’ optimal performance and extend their service life.
A preventive maintenance strategy is crucial for optimizing asset and equipment management. It reduces costs and downtime by preventing issues before they arise.
In healthcare, this maintenance method ensures that the medical apparatus remains in constant working order while meeting safety standards.
Likewise, industries like facility management, energy and utilities, and food and beverage utilize maintenance structured around meter measurements. They do so to maintain the trustworthiness of essential infrastructure, adhere to prescribed safety protocols, and prevent expensive equipment failures.
Best Practices for Preventive Maintenance
Implementing a successful preventive maintenance program involves following best practices to ensure efficiency and effectiveness. Key practices include:
- Reviewing Inventory: Regularly assess which assets require meter-based maintenance to cover all critical equipment.
- Setting Maintenance Triggers: Establish maintenance triggers based on specific usage metrics, such as operating hours or cycle counts, to ensure timely maintenance.
- Staff Training: Provide regular training for maintenance staff to ensure accurate tracking of usage metrics and efficient completion of preventive maintenance tasks.
- Leveraging Technology: Use advanced technology to track usage metrics and set condition-based maintenance triggers based on meter readings.
- Automating Processes: Utilize a CMMS to automate scheduling and work order creation, ensuring maintenance tasks are timely.
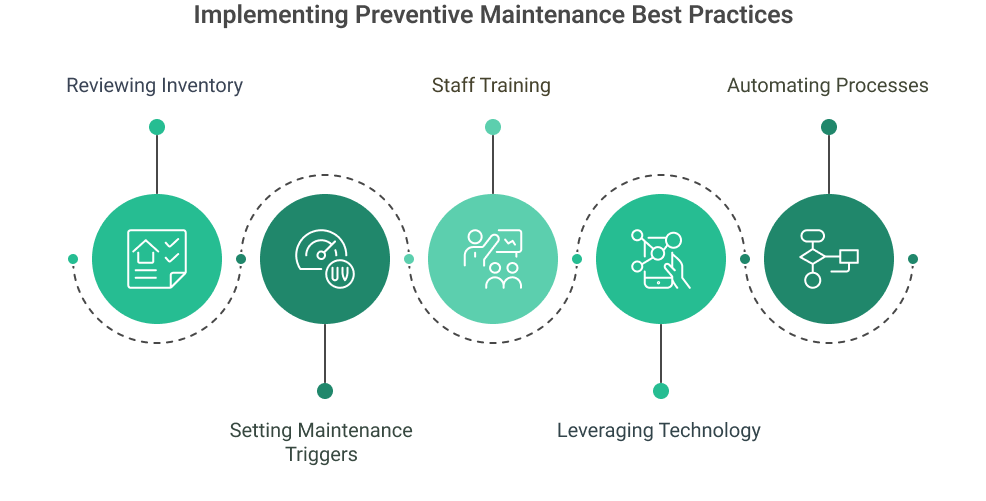
By following these best practices, maintenance teams can ensure that their preventive maintenance program is effective and efficient. This approach helps reduce maintenance costs, increase equipment reliability, and optimize overall operational efficiency, ultimately contributing to the organization’s long-term success.
Get a Free WorkTrek Demo
Let's show you how WorkTrek can help you optimize your maintenance operation.
Try for free