What is OEE?
Imagine you’re baking cookies in your kitchen. You plan to bake for 4 hours but spend 1 hour looking for ingredients and fixing your mixer (availability loss). When you start baking, your oven can only fit half as many cookies as it should (performance loss).
At the end of the day, some cookies are burnt and must be thrown away (quality loss). This everyday scenario illustrates the core concept of Overall Equipment Effectiveness (OEE) – a powerful metric that helps manufacturers understand how effectively they use their equipment and reduce downtime.
To fully grasp OEE, it’s essential to understand how to calculate OEE using specific formulas that account for availability, performance, and quality losses.
How does OEE work?
Overall Equipment Effectiveness is like a report card for manufacturing equipment that measures how well a machine performs compared to its full potential. Think of OEE as answering three fundamental questions:
- Is the equipment available when we need it?
- Is it running as fast as it should?
- Are we producing good-quality units?
Let’s break this down further with a simple example: Imagine a machine that should produce 100 widgets per hour for an 8-hour shift.
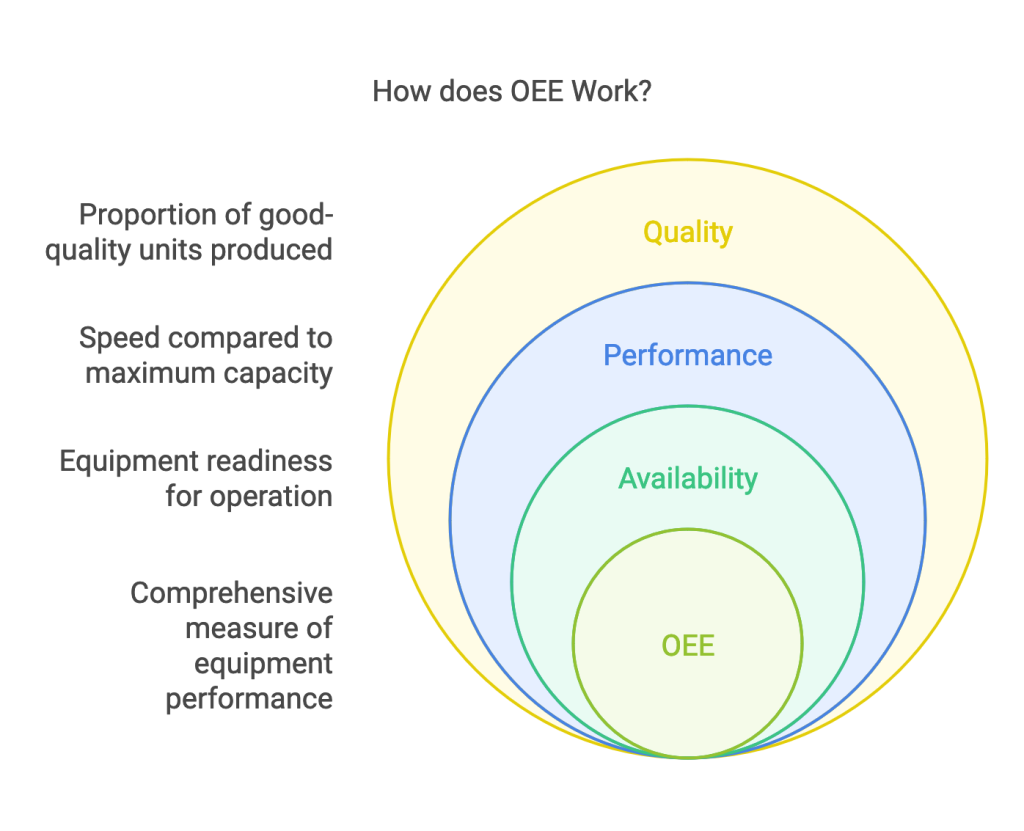
The Three Pillars of OEE
Availability: Is Your Equipment Ready When You Need It?
Availability measures how much of your planned production time is spent producing. It’s like showing up to work on time and staying until the end of your shift.
When we say a machine has 80% availability, it means that for every 10 hours we plan to run it, it will run for 8 hours.
This metric helps us understand truly productive manufacturing time, the actual time spent producing quality products during planned production time.
Common availability losses include:
- Equipment failures (like when your car won’t start)
- Setup and adjustment time (like preparing your workspace before starting a project)
- Material shortages (like running out of ingredients while cooking)
Performance: Is Your Equipment Running at Full Speed?
Performance compares how fast your equipment runs versus how fast it should run.
Imagine driving a car that can go 60 mph, but you can only drive at 45 mph due to traffic—that’s a 25% performance loss.
Performance losses often occur due to:
- Minor stops (like briefly pausing to adjust something)
- Reduced speed (like running a machine slower to prevent overheating)
- Start-up losses (like warming up an engine)
Quality: Are You Making Good Products?
Quality measures the number of good pieces you produce compared to the total number of pieces started. If you make 100 products but five are defective, your quality rate is 95%.
Think about:
- Defects during startup (like the first pancake that never turns out quite right)
- Production defects (like a misaligned part)
- Reduced yield (like fabric waste when cutting patterns)
Putting It All Together: The OEE Calculation
Let’s walk through a real-world example:
Suppose you have a machine that:
- Should run for 8 hours (480 minutes) but is only available for 6 hours due to various stops
- Should produce 100 pieces per hour but only produces 75
- Makes 50 good pieces out of every 75 produced
Your OEE would be:
- Availability: 6/8 = 75%
- Performance: 75/100 = 75%
- Quality: 50/75 = 67%
OEE = 75% × 75% × 67% = 38%
This seemingly low number is quite common in manufacturing. Even world-class manufacturers typically achieve an OEE of around 85%, demonstrating that there’s always room for improvement.
While OEE focuses on productivity during planned production times, total effective equipment performance (TEEP) measures the maximum potential output if the plant operates continuously.
OEE Calculator
Below is a OEE calculator that you can use:
OEE Calculator
Common Losses in OEE
Overall Equipment Effectiveness (OEE) is a powerful tool for measuring manufacturing productivity and identifying areas for improvement. However, several common losses can negatively impact OEE scores. These losses can be categorized into six main areas:
- Availability Losses: These occur when equipment is unavailable for production due to unplanned downtime, such as breakdowns or maintenance. Imagine planning to bake cookies but spending an hour fixing your mixer – that’s an availability loss.
- Performance Losses: These happen when equipment runs slower than its maximum speed. For example, if your oven can bake 20 cookies in an hour but only manages 15 due to slow cycles, you’re experiencing a performance loss.
- Quality Losses: These result from producing defective products that do not meet quality standards. Think of burnt cookies that need to be discarded – a quality loss.
- Setup and Adjustment Losses: Time spent preparing equipment for production, such as setting up or adjusting machines, falls into this category. It’s like spending time preheating your oven before you can start baking.
- Idling and Minor Stops: These are brief interruptions in production, such as minor adjustments or cleaning. Imagine pausing to scrape off burnt bits from your baking tray – that’s an idling loss.
- Reduced Speed: When equipment operates below its optimal speed to prevent overheating issues, it reduces speed losses. This is similar to baking at a lower temperature to avoid burning cookies.
By understanding and addressing these common losses, manufacturers can significantly improve the effectiveness of their overall equipment and boost productivity.
Why OEE Matters: The Practical Impact
Understanding OEE helps manufacturers in several practical ways:
- Identifying Problems Early Think of OEE like a doctor’s regular check-up for your equipment. It helps spot issues before they become serious problems. For instance, if performance starts dropping, it might indicate that maintenance is needed soon. This can improve actual production count efficiency.
- Making Better DecisionsWhen you know your true production capacity, you can make more accurate promises to customers and better plans for your production schedule. It’s like knowing exactly how long your commute takes so you can plan when to leave for work.
- Saving Money By identifying losses, OEE helps focus improvement efforts where they’ll have the biggest impact. It’s similar to finding out where you spend too much money in your monthly budget.
How to Use OEE Effectively
The key to using OEE effectively is to consider it a journey rather than a destination. Here’s how to approach it:
- Start Small: Measure OEE on one critical machine or process. This will help you learn the measurement process without becoming overwhelmed.
- Collect Good Data: Accurate measurements are crucial. Modern manufacturers often use automated systems, but even a simple spreadsheet can work when starting out.
- Focus on Trends: Don’t get too hung up on the absolute number. What’s more important is whether your OEE is improving over time and understanding what causes changes.
- Involve Everyone: Operators, maintenance staff, and managers all contribute to improving OEE. When everyone understands how their work affects overall efficiency, improvements happen naturally.
Implementing OEE in Your Manufacturing Process
Implementing Overall Equipment Effectiveness (OEE) in your manufacturing process can be a powerful way to improve productivity, reduce waste, and increase efficiency. Here are some steps to follow:
- Identify Key Equipment: Start by selecting the most critical machines or processes in your production line. These are the areas where improvements will have the most significant impact and improve machine uptime.
- Collect Accurate Data: Gather data on availability, performance, and quality. This can be done manually or through automated systems. Accurate data is essential for reliable OEE calculation.
- Analyze Losses: Identify the main sources of losses in availability, performance, and quality. Understanding where and why these losses occur will help you effectively target your improvement efforts.
- Set Realistic Goals: Establish achievable targets for improving OEE and a real-time production target. Focus on incremental improvements rather than trying to achieve perfection overnight.
- Involve the Team: Engage operators, maintenance staff, and managers in the OEE process. When everyone understands their role in improving equipment effectiveness, it fosters a culture of continuous improvement.
- Monitor and Adjust: Review OEE data regularly and make adjustments as needed. Use the insights gained to refine your processes and address new challenges as they arise.
Following these steps, you can effectively implement OEE in your manufacturing process, leading to better equipment effectiveness, reduced waste, and higher productivity.
Improving Manufacturing Productivity with OEE
A leading automotive parts manufacturer implemented Overall Equipment Effectiveness (OEE) to improve manufacturing productivity and reduce waste. The company had experienced significant downtime and quality issues, resulting in reduced production efficiency and increased costs.
To address these challenges, the company took the following steps:
- Data Collection: They began by collecting accurate data on their production processes, focusing on availability, performance, and quality metrics.
- Identifying Losses: The data revealed several key areas of loss, including frequent equipment breakdowns, slow cycles, and a high rate of defective parts.
- Targeted Improvements: The company implemented improvements, such as preventive maintenance schedules to reduce unplanned downtime and process optimizations to increase production speed.
- Team Involvement: Operators and maintenance staff were trained on the importance of OEE and how their actions could impact overall equipment effectiveness. This fostered a collaborative approach to problem-solving.
- Continuous Monitoring: The company continuously monitored OEE metrics and adjusted as needed. This allowed them to quickly address new issues and maintain high levels of production efficiency.
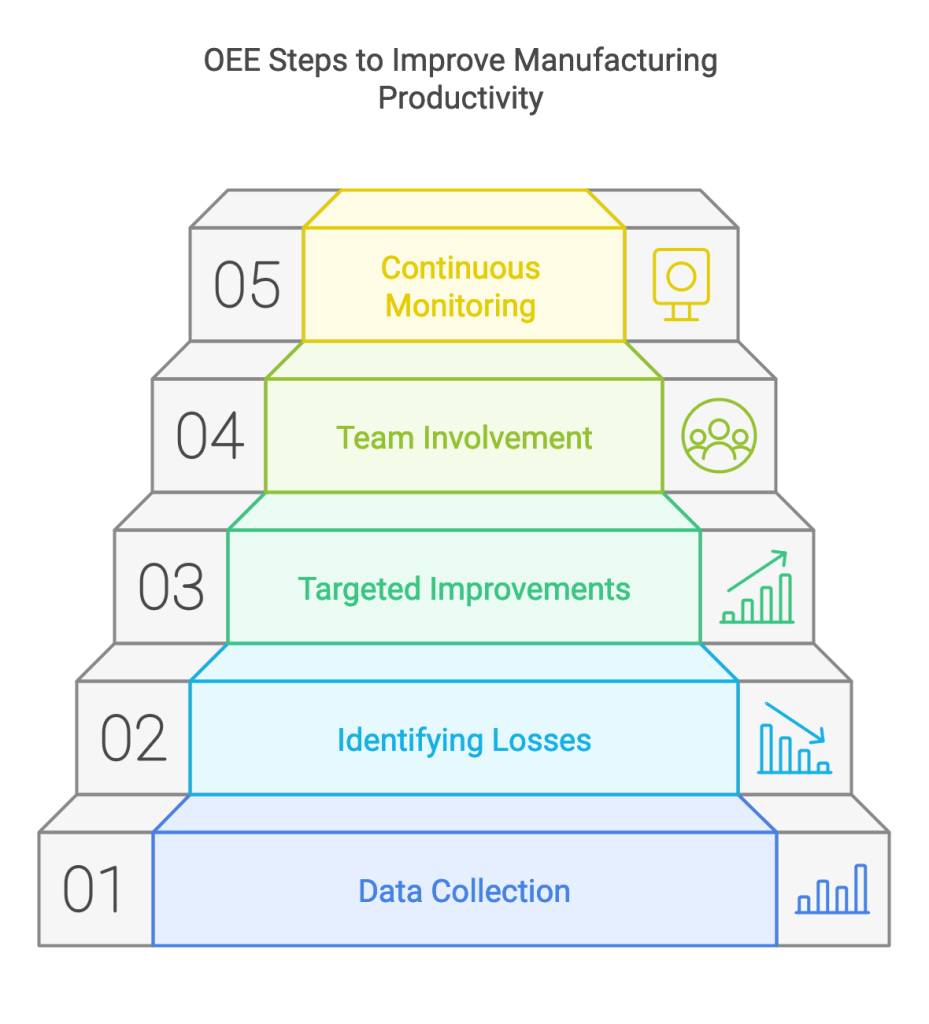
As a result of these efforts, the company saw a significant improvement in its OEE score, which led to increased production efficiency, reduced waste, and lower operational costs.
This case study demonstrates the practical benefits of implementing OEE in manufacturing and highlights the importance of continuous improvement in achieving long-term success.
Common Challenges and Solutions
Understanding OEE isn’t always straightforward. Here are some common challenges and how to address them:
Challenge 1
Challenge: “Our OEE seems too low compared to industry standards.”
Solution: Remember that OEE is a journey. Focus first on improvement rather than achieving a specific number. Many successful manufacturers started with OEE below 40%.
Challenge 2
Challenge: “We don’t have automated data collection systems.”
Solution: Start by collecting manual data for your most critical processes. Even basic measurements can provide valuable insights for improvement.
Challenge 3
Challenge: “Different shifts report different numbers.”
Solution: Create clear standards for what counts as downtime, what qualifies as a quality defect, and how to measure performance. Document these standards and consistently train all staff.
The Real-World Benefits of OEE: Why It Matters for Your Business
Understanding the benefits of OEE is like understanding why regular health check-ups are important. Just as health checks help us identify and prevent problems before they become serious, OEE helps manufacturing operations stay healthy and improve over time. Let’s explore how OEE creates value across different aspects of your business.
Financial Benefits
Think of OEE as a financial advisor for your manufacturing operation. When you improve your OEE, you get more value from every dollar invested in your equipment and operations. Here’s how this works:
First, consider your fixed costs—building rent, equipment payments, and salaried staff. These expenses don’t affect whether your machines are running efficiently.
When you improve your OEE, you spread these fixed costs across more suitable products, reducing the cost per unit. It’s similar to how a full airplane is more profitable than one-half empty, even though the fuel and crew costs remain roughly the same.
For example, if your OEE improves from 65% to 75%, you might be able to produce an additional 1,000 units per shift without increasing fixed costs. If each unit provides $10 in contribution margin, that’s an extra $10,000 per shift in potential profit.
Operational Excellence
OEE acts like a GPS for operational improvement. Just as a GPS helps you navigate by showing your current location and suggesting better routes, OEE helps you understand where your operation stands and how to improve it.
Consider a packaging line that’s running at 60% OEE. By tracking the components of OEE, you might discover that:
- Frequent material jams cause 15% of your availability losses
- Operator breaks aren’t well-coordinated, causing another 10% loss
- Minor stops eat away 8% of your performance time
- Quality issues consume 7% of your production
This detailed breakdown helps you prioritize improvements with the biggest impact. It’s like knowing whether you’re losing more money on groceries or entertainment when trying to manage your budget.
Quality Improvements
OEE’s quality component has a ripple effect throughout your organization. When you measure and improve quality as part of OEE, you’re not just reducing scrap – you’re also:
- Building Customer Trust: When your OEE quality metrics are high, customers receive consistently good products, leading to fewer returns and complaints. It’s like a restaurant that serves consistently delicious meals – customers know they can count on a good experience.
- Reducing Hidden Costs: Poor quality creates many hidden costs beyond just scrapped products. Think about all the time spent:
- Investigating quality problems
- Handling customer complaints
- Rerunning production to replace bad products
- Managing excess inventory kept as a buffer against quality issues
By improving the quality component of OEE, you eliminate hidden costs, like maintaining your car properly and preventing costly repairs later. All this can lead to higher actual output at the maximum possible speed.
Employee Engagement
One often-overlooked benefit of OEE is its positive impact on employee engagement. When implemented thoughtfully, OEE becomes a powerful tool for involving everyone in the improvement process:
Operators gain a clearer understanding of how their actions affect the overall process. It’s like giving a soccer player real-time statistics about their performance – they can see immediately how their efforts contribute to the team’s success.
Maintenance teams can use OEE data from reactive repairs to preventive maintenance. Instead of waiting for breakdowns, they can spot trends and address issues before they cause problems, similar to how regular car maintenance prevents roadside breakdowns.
Management gets objective data for decision-making. Rather than relying on gut feel or incomplete information, they can make choices based on clear metrics, much like how a doctor uses test results to recommend treatments.
Competitive Advantage
In today’s competitive manufacturing environment, OEE can provide a significant edge. It’s like having a more efficient engine in a race car – you can go faster or farther with the same amount of fuel.
For example, if your OEE is 85% while competitors are at 60%, you can:
- Offer shorter lead times because you can produce more efficiently
- Maintain lower prices while preserving margins due to better efficiency
- Respond more quickly to demand changes because you have better control over your processes
- Invest in new opportunities using the money saved through better efficiency
Environmental Impact
An often-overlooked benefit of OEE is its positive environmental impact. Higher OEE means:
- Less waste of raw materials due to better quality
- Lower energy consumption per unit produced
- Reduced environmental impact from transportation and handling of rejected products
- More efficient use of resources overall
It’s similar to how a well-tuned car engine saves money on fuel and produces fewer emissions.
Future-Proofing Your Operation
Finally, OEE helps prepare your operation for the future. By establishing strong measurement and improvement processes, you create a foundation for:
- Implementing new technologies like Industrial IoT
- Adapting to changing customer demands
- Scaling production up or down efficiently
- Training and developing staff effectively
Think of it as building a solid foundation for a house – it makes any future additions or modifications much easier and more stable.
Conclusion: The Path Forward
Think of OEE as a flashlight that helps illuminate opportunities for improvement in your manufacturing process. While the concept might seem complex initially, breaking it down into its components—availability, Performance, and Quality—makes it more manageable and actionable.
The most important thing to remember is that OEE is not just about measuring numbers—it’s about understanding your process better and improving continuously. Every small improvement in OEE represents real-time, money, and resource savings, ultimately leading to a more efficient and profitable operation.
Get a Free WorkTrek Demo
Let's show you how WorkTrek can help you optimize your maintenance operation.
Try for free