Get a Free WorkTrek Demo
Let's show you how WorkTrek can help you optimize your maintenance operation.
Try for freeThere is no denying that regular maintenance of your assets is important.
After all, it prevents breakdowns and keeps productivity high, contributing to the overall success of your facility.
But we’re here to argue that the way you approach the task of scheduling maintenance is what can truly make or break your operations.
In this article, we’re exploring six different approaches to this important process, comparing them, and sharing some actionable tips on how to make the most of each.
Let’s get right into it.
Time-Based Scheduling
One of the most straightforward approaches to maintenance is scheduling it at regular, predetermined time intervals, regardless of the asset’s condition or usage.
Time-based maintenance (TBM), also known as periodic maintenance, can seem appealing because it is predictable and easy to plan and schedule.
All you have to do is check manufacturer recommendations, put maintenance tasks into the schedule every X days, weeks, or months, and you’re done.
And even if the equipment is in good mechanical health and doesn’t need any maintenance, it’s better to be safe than sorry, right?
Well, not exactly.
Despite the convenient nature of TBM scheduling, this rigid approach isn’t always the best choice.
For starters, it can lead to over-maintenance of assets, which can cause more harm than good.
Charles Rogers, a Senior Software Implementation Consultant at Fiix, agrees.
Performing maintenance on your assets for no reason other than “it says so in the schedule” can lead to a range of consequences, including:
- increased maintenance costs,
- unnecessary downtime,
- faster asset depreciation, and
- waste of your technicians’ time.
And you certainly don’t want any of that.
However, just as it can push you to conduct maintenance more often than necessary, time-based maintenance scheduling can result in maintenance activities that need to be more frequent.
For example, let’s say you schedule centrifugal pumps for inspection and maintenance every six months because they’re new, and you feel more frequent checks are unnecessary.
Since your technicians are sticking to this time-based schedule and looking at the pumps less frequently than recommended, missing the warning signs that something’s wrong with them becomes all too easy.
At this point, you might be thinking that TBM scheduling is no good and that you might be better off opting for a different approach altogether.
But Erik Hupjé, Founder and Managing Director of Reliability Academy, believes you can make it work.
This maintenance and reliability expert with over 20 years of experience says that time-based maintenance is best used for equipment whose failure is age-related.
In other words, TBM is a solid choice for equipment whose failure patterns are predictable.
For instance, Hupjé explains, it’s only natural for equipment nearing the end of its useful life to experience a higher likelihood of failure.
Therefore, scheduling maintenance at regular intervals for such equipment might be just what you need.
But you don’t have to stop there.
TBM scheduling also works for equipment with predictable usage patterns.
Think about the equipment running for the same number of hours daily or at the same speed and frequency.
Such assets will experience more predictable wear and tear thanks to this consistency.
So if you opt for the time-based approach to maintenance scheduling for some of your equipment, don’t just blindly follow manufacturer recommendations or your discernment.
Make sure to combine both, and you’re bound to make the most of it.
Meter-Based Scheduling
If you feel like the time-based approach is too limiting and somewhat risky, a good alternative to consider is meter-based maintenance scheduling.
Rather than basing the frequency of maintenance tasks on strict time intervals, this approach requires you to track your equipment usage and schedule maintenance accordingly.
As such, it is more flexible than TBM but also more complex to set up and schedule.
Meter-based scheduling is based on defining usage metrics, such as the number of operating hours or cycle counts, and scheduling maintenance once that predefined usage threshold has been met.
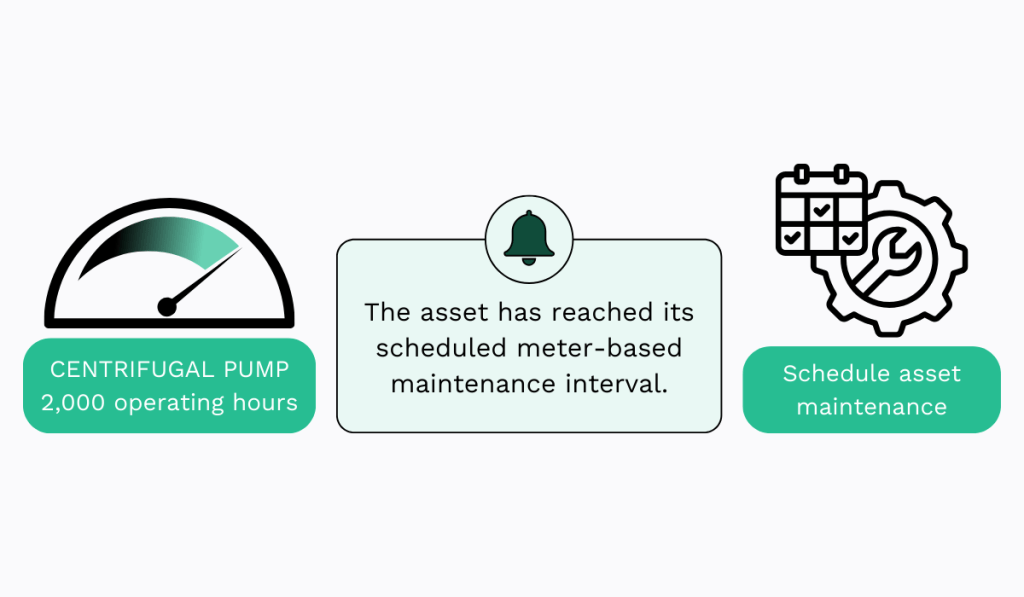
However, just like time-based scheduling, this usage-based approach doesn’t consider the asset’s condition at the time of scheduled maintenance.
So how is meter-based scheduling any different, then?
Well, it requires you to look at your own usage data to set and adjust a metric threshold that accurately reflects when maintenance is truly needed.
Simply put, while it doesn’t directly account for the asset’s condition, meter-based scheduling lets you observe metrics that correlate with the asset’s wear and tear.
Sticking with our centrifugal pump example, let’s say you’ve noticed that its bearings require lubrication about every 2,000 operating hours.
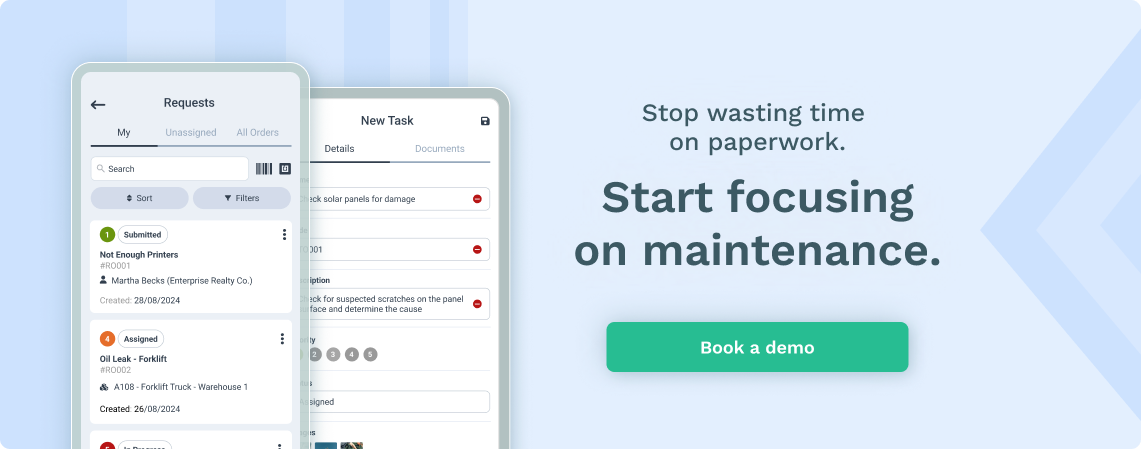
If the pump runs 24/7, it will take almost three months to reach that number of operating hours, but if you use it occasionally, it might take six months or more.
Time-based scheduling doesn’t account for this, so it would likely have you over-maintaining the pump and wasting resources.
Therefore, meter-based scheduling allows you to respond to the changing needs of your assets more accurately.
However, it also requires you to monitor the usage metrics of your assets actively.
And you’ll agree doing this manually can be pretty time-consuming and resource-intensive.
Luckily, with a maintenance management solution such as our WorkTrek, you can automate at least a part of this process.
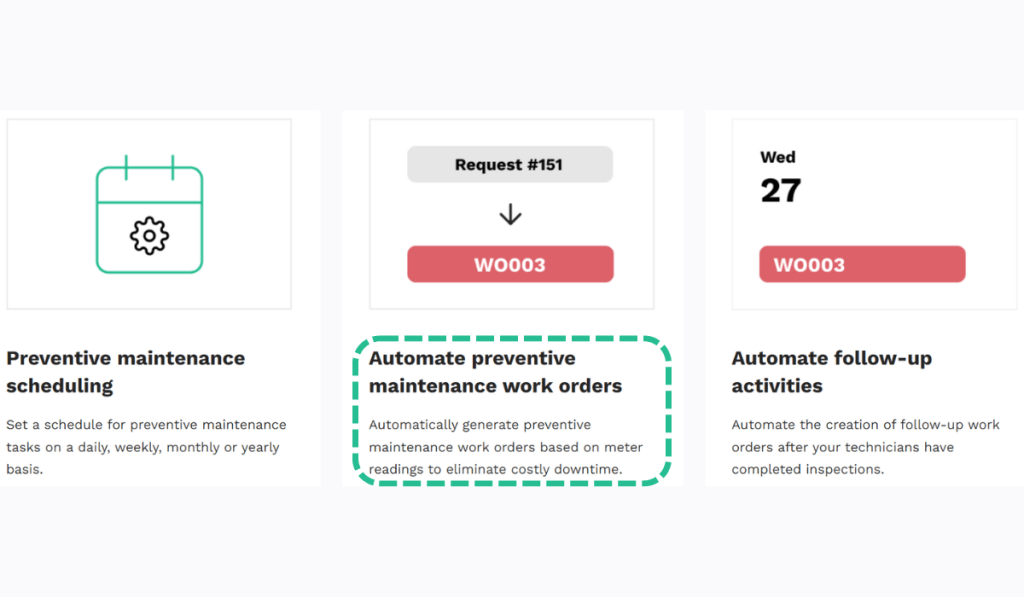
All you need to do is enter your assets into the system and determine the thresholds at which maintenance should be initiated.
Setting this up in WorkTrek is incredibly easy—you simply need to fill out the required fields, as shown below.
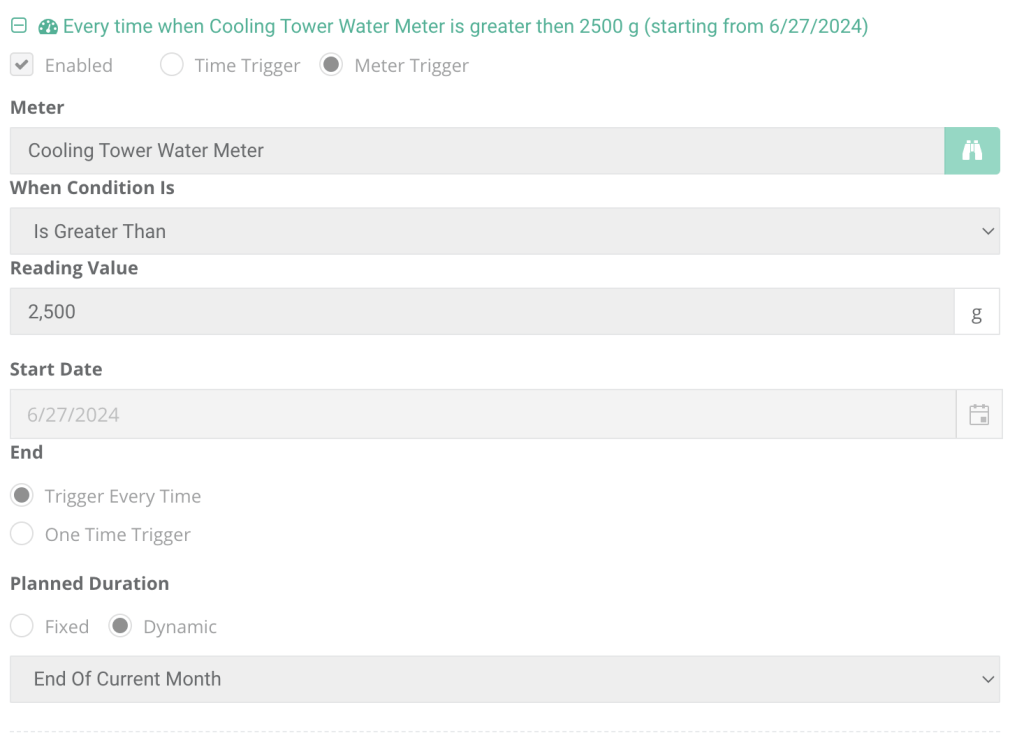
Then, once the threshold you have set has been reached, you update this information in the system, and WorkTrek will automatically generate a work order, setting the maintenance process in motion.
Overall, if you’re working with equipment whose wear patterns can be determined based on meter readings, this type of scheduling could be a good approach for you to follow.
Condition-Based Scheduling
Another approach to maintenance scheduling that you might want to consider is condition-based maintenance scheduling, also known as CBM scheduling.
As its name suggests, this proactive approach is based on real-time monitoring of your equipment’s condition and performance.
We could say that CBM is an upgraded version of meter-based maintenance because it tracks health indicators in real time, triggering maintenance as soon as deterioration begins, regardless of usage or time.
This makes CBM a good choice if you’re looking to maximize your machines’ uptime and prevent unnecessary maintenance costs at your facility.
Yet, it’s a much less popular approach to maintenance scheduling than preventive and reactive maintenance, according to the MaintainX 2024 State of Industrial Maintenance Report.
Why is this the case?
It could be that condition-based maintenance is less predictable than time- and meter-based options that follow a strict schedule.
On top of that, it is more complex to implement and manage, as it requires you to continuously collect real-time data using different types of analyses, such as:
Vibration Analysis | Analyzes the vibration patterns of equipment to detect issues like imbalances, misalignment, and bearing failures. |
Infrared Analysis (Thermography) | Uses thermal imagers to identify abnormal heat patterns that can indicate electrical faults, misaligned components, or friction in mechanical systems. |
Oil Analysis | Monitors the properties of oil fluid, like viscosity and acid levels, and detects the presence of contaminants, wear particles, and chemical degradation. |
Ultrasonic Analysis | Detects high-frequency sounds and converts them into digital and audio data to identify issues that emit high-frequency noise, like leaks, electrical discharges, and mechanical anomalies. |
Electrical Analysis | Measures the current in the circuit using clamp-on ammeters and detects whether a piece of equipment is receiving a normal amount of electricity. |
Pressure Analysis | Monitors pressure levels to check for leaks, blockages, and structural integrity in pressurized systems. |
As you can see, there are quite a few things to track if you want to properly monitor the mechanical health of your assets and schedule maintenance accordingly.
However, we’d say it’s worth the effort.
This certainly was the case for Končar, an industrial and electrical engineering company that decided to implement condition-based monitoring to protect its critical production motors.
They gained insight into all the critical parameters, from vibrations and speed of rotation to temperature levels.
This approach made it possible for them to schedule maintenance based on the actual condition of the equipment rather than on the assumption that wear and tear would occur after a specific amount of time or usage.
And the good news is that it can do the same for you, too.
Scheduling by Data-Based Predictions
The following method on our list relies on data-based prediction to schedule equipment maintenance.
In other words, predictive maintenance.
With data gradually becoming the backbone of successful plants and facilities, this maintenance management approach is gaining traction.
In fact, according to the MaintainX report we mentioned earlier, it’s the third most commonly used maintenance program, with 30% of facilities utilizing it.
Why?
Well, the Maintenance Supervisor at Cintas, a company that provides uniforms, facility services, and safety products, believes scheduling maintenance using data-based predictions helps facilities stay ahead of equipment issues.
In a way, predictive maintenance goes a step further than condition-based maintenance.
Aside from using condition-based diagnostics, the predictive maintenance approach relies on historical and real-time data and machine learning algorithms to predict potential failures.
So, while CBM tells you that maintenance is needed, predictive maintenance predicts when it may be needed.
Freddie Coertze, National IoT Business Manager for ifm Australia, explains why he advocates for predictive maintenance over CBM:
Condition monitoring with vibration analysis is simply not enough – by the time vibration has started, it’s often already too late to intervene and save the machine. To protect your assets, you need to predict.
But predictive maintenance doesn’t just protect your assets and prevent minor hiccups from turning into serious issues.
It also increases productivity and reduces breakdowns, maintenance planning time, and maintenance costs, reports Deloitte.
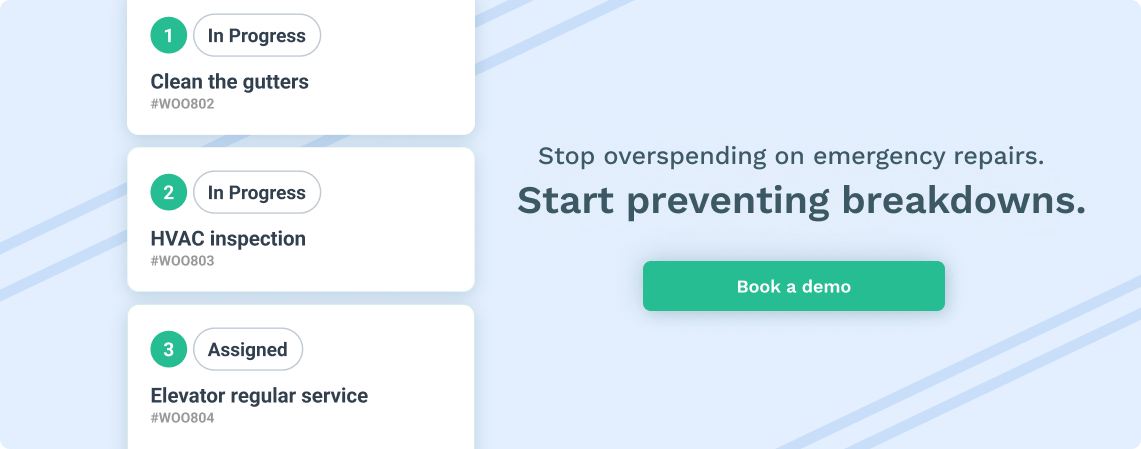
These numbers show that predictive maintenance carries a lot of potential advantages for industrial facilities.
While its implementation can be more demanding due to the sheer amount of components it requires—from IoT devices and sensors to CMMS and data collection systems—the long-term benefits you can reap make predictive maintenance scheduling an approach worth considering.
Criticality-Based Scheduling
The criticality-based approach to maintenance scheduling prioritizes maintenance tasks in a way where the most critical equipment is taken care of first.
But how do you determine which equipment needs to receive maintenance first?
And how do you decide which assets’ failure poses a greater risk to your operations?
Well, that is where criticality analysis comes in.
This analysis will help you assess how significant each piece of equipment is for your organizational objectives and how big of an impact its failure would have on your operations.
To successfully conduct it, you first need to assemble a cross-functional team to help you develop an equipment criticality assessment matrix.
Its purpose is to help you visualize and rank your equipment’s criticality, making prioritizing its maintenance easier.
- For starters, you want input from those within the organization affected by equipment failures—from maintenance engineers and operations managers to maintenance technicians.
- From there, you’ll need to compile a list of all the equipment that needs to be assessed and then agree on criticality ranking criteria. These can include factors like the age and condition of the asset, its impact on the operations, the safety risks it carries, and the impact made by its downtime.
- You then need to define how severe the consequence of failure is for each asset.
- Lastly, you need to agree on how likely each piece of equipment will fail within a specified timeframe.
When you put all of these elements together, you’ll end up with a criticality assessment matrix such as the one you can see below.
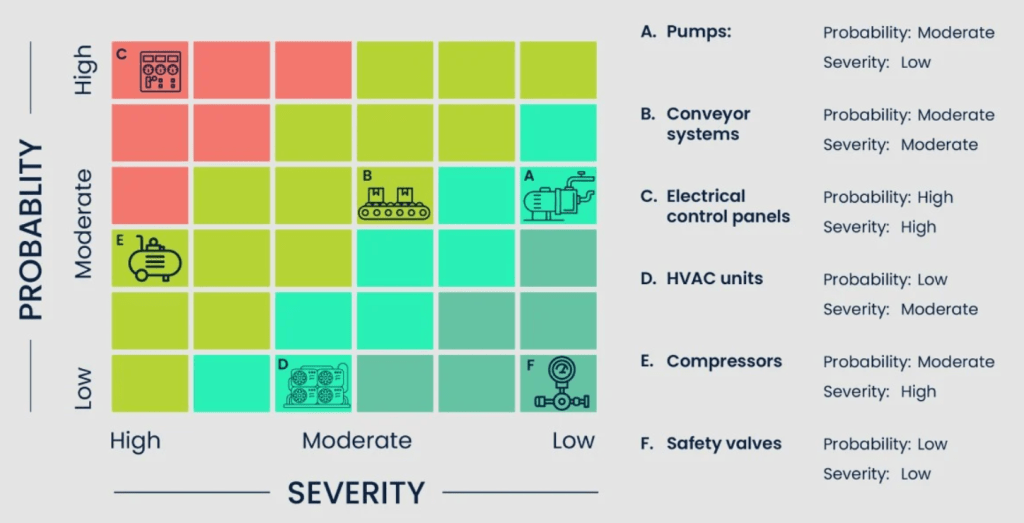
Using this systematic approach, you can confidently create a maintenance schedule that addresses the most urgent equipment inspections and fixes first.
This, in turn, keeps your operations running smoothly and helps you mitigate the safety risks of faulty equipment.
Scheduling Around Seasonality
The final approach we’re going to cover today focuses on scheduling maintenance activities around seasons.
The idea behind it is to schedule maintenance tasks in alignment with the seasonal variations in equipment use.
Why?
Because, by scheduling maintenance of specific assets during lower activity seasons, you can ensure that there are minimal to no disruptions to your operations during peak seasons.
Let’s take HVAC maintenance, for example.
Given that the usage of HVAC systems is increased during the summer and winter months, it comes as no surprise that many choose to schedule their maintenance during spring and fall.
Marcin Bizewski, Operations Director at Sescom Facility Management, explains why this is the case.
Because scheduling around seasonality proactively addresses potential issues before they get the opportunity to happen, the risk of failures during peak usage season is decreased significantly.
Can you imagine working in 100°F heat just because you didn’t schedule a technician to look at the HVAC system in the springtime?
And we don’t even have to mention the fact that, if the unit breaks down, repairing or completely replacing it will cost you much more than a slot in the schedule for its maintenance would have.
So, don’t underestimate the power of scheduling maintenance of some of your assets based on seasonal changes.
For that, use your CMMS to plan and schedule them for a checkup ahead of time.
You can even create a checklist for seasonal maintenance tasks so that the technician performing them knows precisely which steps they need to follow, season after season.
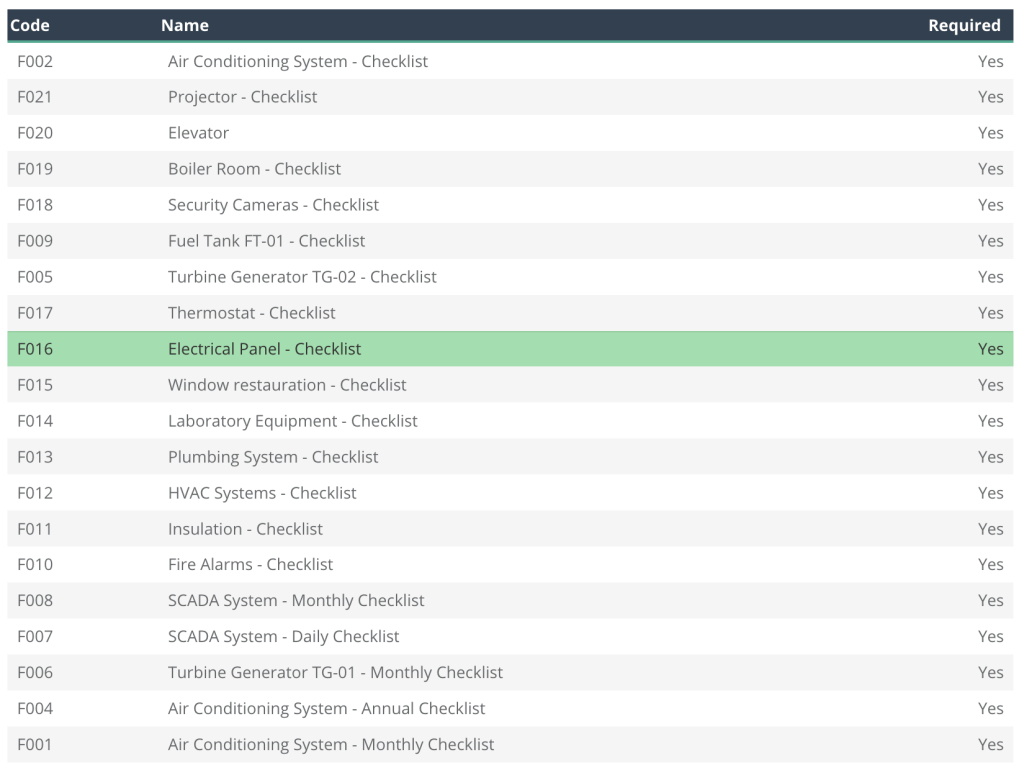
Overall, scheduling particular maintenance activities based on seasonality is a great way to complement the other approaches to maintenance scheduling used at your facility.
Conclusion
And there you have it – six approaches you can choose from when deciding how and when you should schedule maintenance tasks for your equipment!
While having this many options might seem overwhelming at first glance, this variety can help you improve your maintenance planning and scheduling.
You don’t have to opt for just one of these approaches.
Instead, you can weigh the pros and cons of each and assess which equipment would benefit the most from each method.
Don’t forget to optimize the whole process using a CMMS, as this kind of solution will be your biggest ally in keeping your maintenance activities on track.