Get a Free WorkTrek Demo
Let's show you how WorkTrek can help you optimize your maintenance operation.
Try for freeEvery facility manager has encountered the challenge of deferred maintenance at some point. It’s the maintenance equivalent of pushing off today’s problems until tomorrow – except tomorrow inevitably arrives, often with compounded issues and costs.
This comprehensive guide will explore practical strategies for reducing deferred maintenance and creating a more sustainable maintenance program to protect your facility’s assets for years.
Understanding Deferred Maintenance: More Than Just Delayed Repairs
Deferred maintenance isn’t simply about postponed repairs – it represents a complex challenge that can significantly impact an organization’s bottom line and operational efficiency.
When we defer maintenance, we take out a high-interest loan against our facility’s future. The interest comes from accelerated deterioration, increased repair costs, and potential safety risks.
Deferring maintenance due to budget constraints can lead to a growing backlog of unaddressed issues, escalating minor problems into major failures and reducing equipment lifespan.
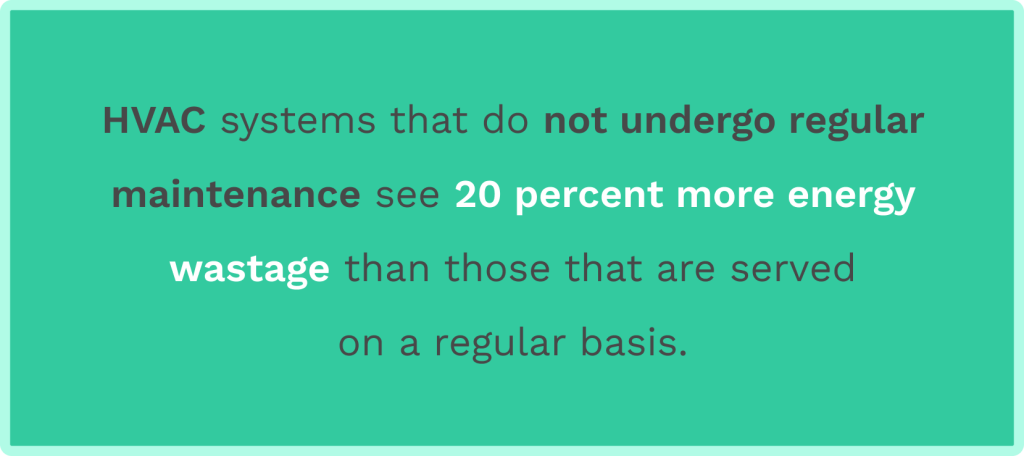
Consider a small roof leak as an example. While it might seem minor initially, postponing its repair can lead to water damage, mold growth, structural issues, and a much more expensive roof replacement.
What might have been a $500 repair can escalate into a $50,000 problem. Delaying maintenance in such scenarios can result in increased costs and safety hazards.
This pattern illustrates why any facility manager must understand and address deferred maintenance.
The ripple effects of deferred maintenance extend beyond the immediate asset. A malfunctioning HVAC system, for instance, doesn’t just affect comfort – it can impact productivity, increase energy costs, and even lead to compliance issues.
Understanding these interconnections is crucial for developing an effective maintenance strategy.
Assessing Your Current Maintenance Backlog
Before effectively reducing deferred maintenance, you must understand its full scope within your facility. This process begins with a comprehensive maintenance audit – think of it as taking inventory of your maintenance debt. This audit should be systematic and thorough, leaving no stone unturned. An insufficient maintenance budget can lead to deferred repairs, causing unexpected costs and financial strain.
Start by documenting all delayed maintenance tasks, from minor repairs to major system overhauls. For each item, record:
- The asset or system affected
- The nature of the required maintenance
- How long the maintenance has been deferred
- Potential consequences of further delay
- Estimated cost of repair or replacement
- Impact on facility operations and safety
- Dependencies with other systems or equipment
- Required resources and expertise
- Regulatory or compliance implications
This detailed assessment provides the foundation for developing an effective reduction strategy. It’s like creating a financial budget—you need to know where you stand before planning your moves.
The assessment should also include a condition rating for each asset, typically on a scale of 1-5, where 1 represents critical failure and 5 represents excellent condition.
Prioritizing Maintenance Tasks: The Art of Strategic Decision-Making
Once you clearly understand your maintenance backlog, the next crucial step is prioritization. Not all deferred maintenance tasks carry the same weight or urgency.
Developing a systematic approach to prioritization helps ensure that your limited resources are allocated to the most critical needs first.
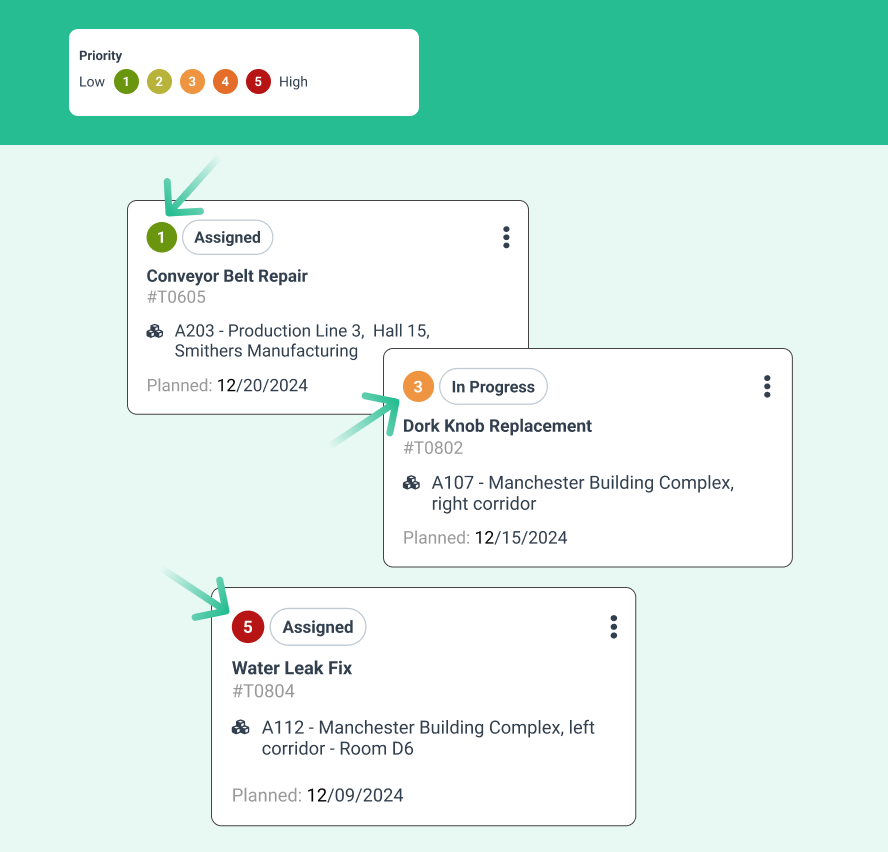
A dedicated maintenance team is vital in this process. They assess and prioritize tasks to prevent minor issues from escalating into major problems.
Consider creating a priority matrix based on these factors:
- Safety Impact: Issues that could affect occupant safety should always take top priority
- Operational Impact: How significantly does the issue affect daily operations?
- Cost Escalation: How quickly will repair costs increase if further maintenance is delayed?
- Regulatory Compliance: Are there any legal or regulatory requirements at stake?
- Asset Life Cycle: How critical is the maintenance to the asset’s expected lifespan?
- Energy Efficiency: Will addressing the issue improve energy performance?
- Occupant Comfort: How does the issue affect building occupants?
- Public Image: Does the maintenance issue affect the facility’s appearance or reputation?
Let’s examine a real-world scenario to make this prioritization process more concrete. Imagine you’re managing a commercial office building with the following deferred maintenance issues:
- A lobby elevator showing signs of wear
- Several roof leaks
- An aging boiler system
- Cracked parking lot pavement
- Outdated lighting systems
In this case, you might prioritize the roof leaks and boiler system first, as they have the highest potential for causing cascading problems and safety issues. The elevator would come next due to its impact on accessibility and tenant satisfaction.
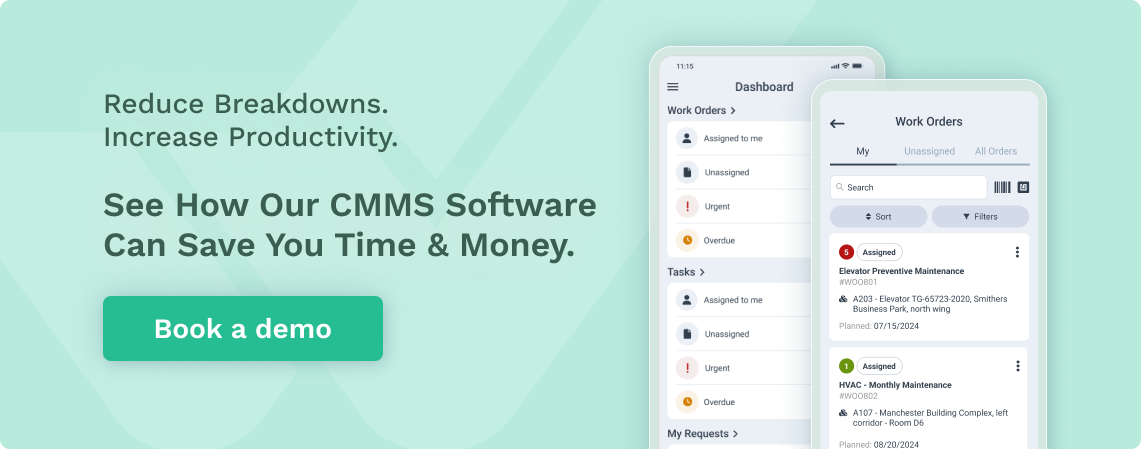
While important, the parking lot and lighting systems would be addressed later unless they pose immediate safety concerns.
Maintenance teams manage these deferred maintenance tasks and ensure effective repairs. Due to a backlog of necessary repairs, they often respond reactively to system failures.
Leveraging technology and cross-departmental collaboration can empower maintenance teams to secure budgets and improve preventive maintenance strategies.
Implementing Preventive Maintenance: The Key to Breaking the Cycle
One of the most effective ways to reduce deferred maintenance is to prevent it from occurring. This is where a robust preventive maintenance (PM) program becomes invaluable.
Implementing preventive maintenance tasks is crucial in preventing emergency maintenance and deferred maintenance.
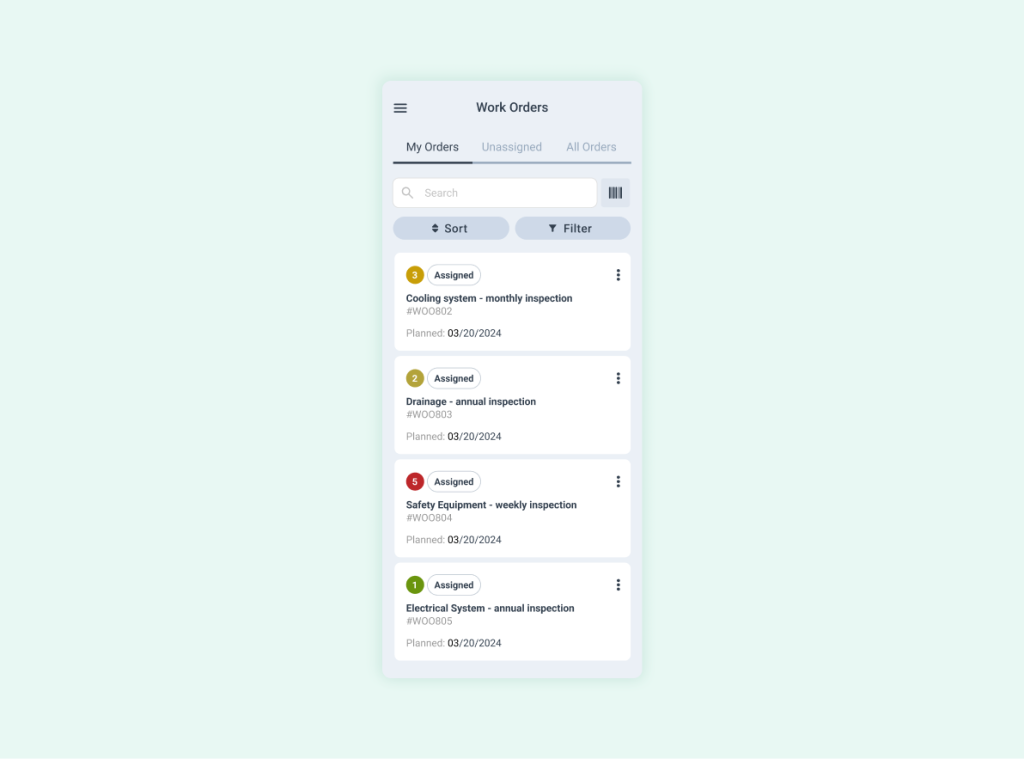
Think of preventive maintenance as regular health checkups for your facility—it’s always better to prevent problems than treat them after they develop.
A well-designed PM program should include:
Regular Inspections
Establish routine inspection schedules for all critical systems and equipment. These inspections should be thorough and documented, with clear criteria for acceptable performance.
Create detailed checklists for each type of inspection to ensure consistency and completeness.
Scheduled Maintenance Tasks
Create a calendar of regular maintenance tasks based on manufacturer recommendations and historical performance data. This might include tasks like:
Routine maintenance tasks are key to deferred maintenance, as insufficient resources or poor planning can lead to delays in addressing necessary upkeep.
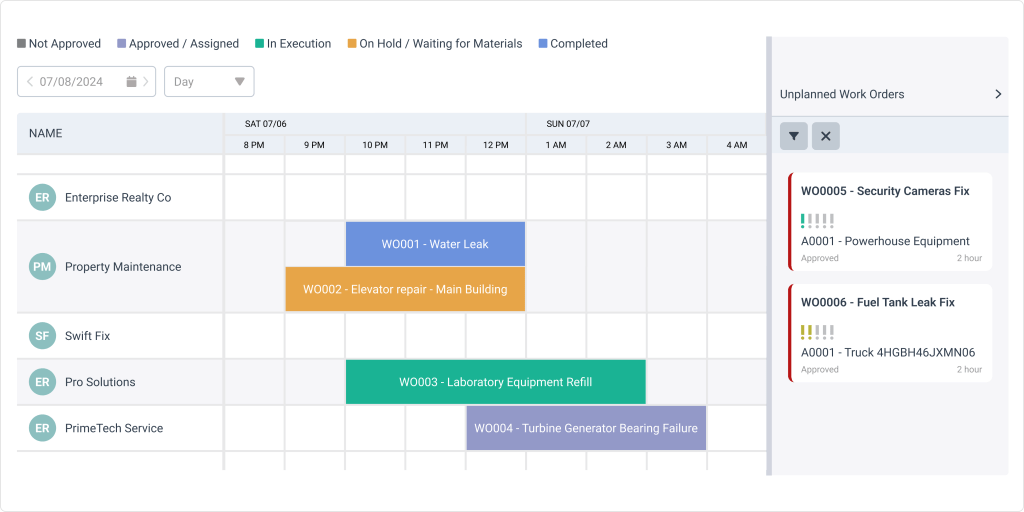
Unexpected events can further divert attention from these essential high-priority tasks, exacerbating maintenance backlogs and complicating corrective measures.
- Quarterly HVAC filter changes and system cleaning
- Annual roof inspections and minor repairs
- Monthly elevator maintenance and safety checks
- Weekly safety system checks
- Daily equipment monitoring and lubrication
- Seasonal preparations for weather-related stress
Performance Monitoring
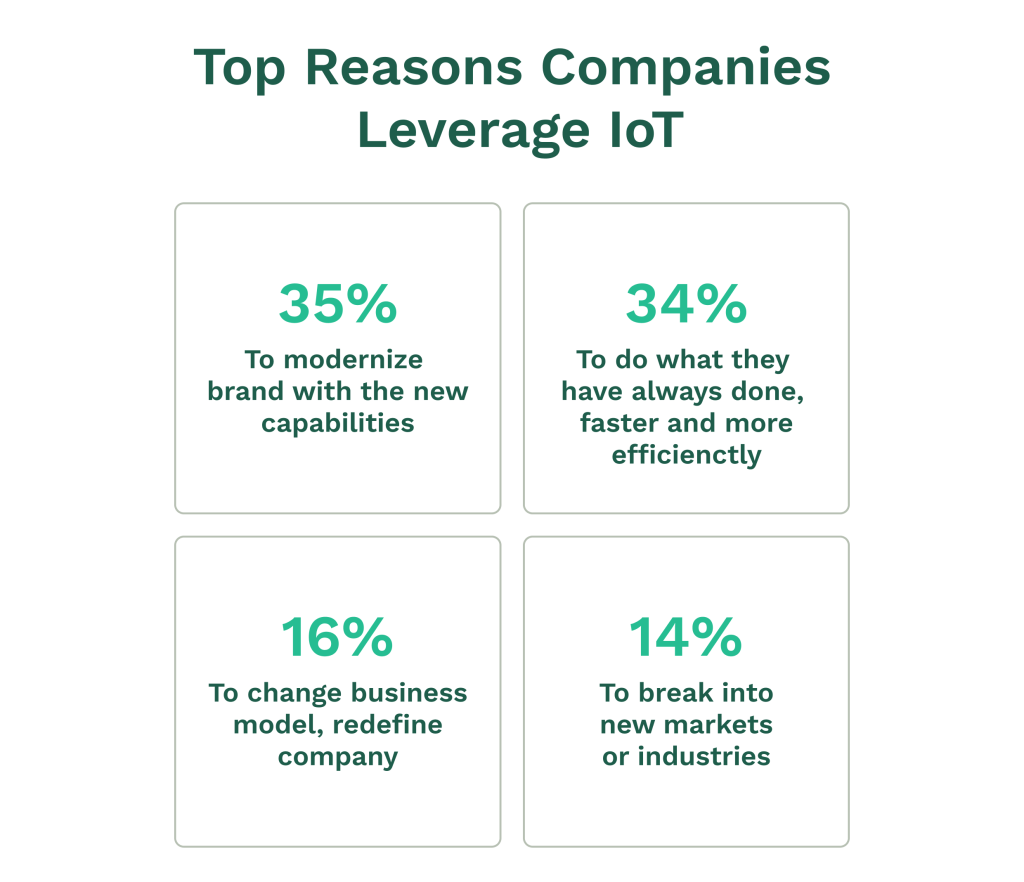
Implement systems to monitor equipment performance in real time. Modern building automation systems and IoT sensors can provide valuable data about equipment operation and help identify potential issues before they become problems. This might include:
- Energy consumption patterns
- Equipment running temperatures
- Vibration analysis
- Air quality measurements
- Water usage tracking
- Noise level monitoring
Securing Additional Budget and Resources
Securing additional budget and resources is crucial to effectively addressing deferred maintenance. Without adequate funding, even the best-laid plans can fall short.
This section will guide you in identifying funding opportunities, justifying maintenance investments, and building a business case to support your request.
Identifying Funding Opportunities
There are various funding opportunities available to support deferred maintenance initiatives. Some of these include:
- Government Grants and Funding Programs: Many governments offer grants and funding programs specifically designed to help organizations address deferred maintenance. Researching these opportunities can uncover valuable resources.
- Private Sector Partnerships and Collaborations: Partnering with private sector companies can provide additional funding and resources. These partnerships can be mutually beneficial, offering companies a chance to invest in community infrastructure.
- Energy Savings Performance Contracts: These contracts allow organizations to fund maintenance projects through the energy savings they generate. This can be a cost-effective way to address deferred maintenance without upfront capital.
- Budget Reallocation and Prioritization: Sometimes, the solution lies within your budget. Reallocating funds from less critical areas and prioritizing maintenance can provide the necessary resources.
- Capital Improvement Plans: Including deferred maintenance projects in your capital improvement plan can secure long-term funding and ensure these projects are prioritized.
Researching and exploring these funding opportunities is essential to determine which ones suit your organization’s needs.
Justifying Maintenance Investments
Justifying maintenance investments requires understanding the benefits and return on investment (ROI) of addressing deferred maintenance. Here are some key points to consider:
- Reduced Maintenance Costs: Addressing deferred maintenance can help reduce maintenance costs in the long run by preventing equipment failures and reducing the need for emergency repairs. Proactive maintenance is often less expensive than reactive maintenance.
- Improved Safety: Deferred maintenance can pose safety risks to employees, customers, and the general public. Addressing these issues can help improve safety and reduce liability, which is crucial for any organization.
- Increased Efficiency: Regular maintenance can help improve equipment efficiency, reduce energy consumption, and increase productivity. Efficient systems and equipment can lead to significant cost savings over time.
- Extended Asset Lifespan: Regular maintenance can help extend the lifespan of assets, reducing the need for costly replacements. This saves money and ensures that your facility remains operational and efficient.
By highlighting these benefits, you can make a compelling case for why investing in maintenance is a smart financial decision.
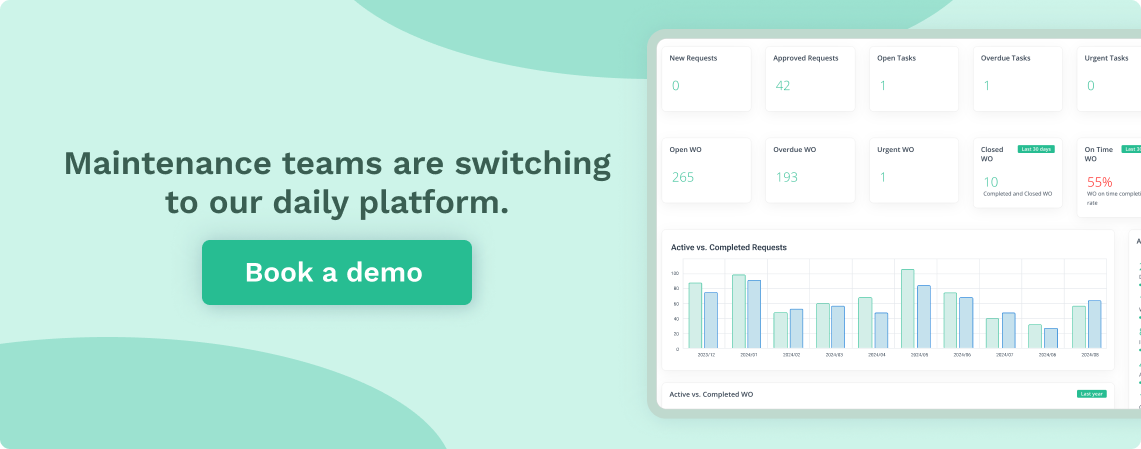
Building a Business Case
Building a business case for deferred maintenance requires clearly and concisely presenting the benefits and ROI of addressing these issues. Here are the key elements to include:
- Executive Summary: Provide a brief overview of the deferred maintenance issue and the proposed solution. This should be a high-level summary that captures the attention of decision-makers.
- Problem Statement: Clearly define the problem and its impact on the organization. Use specific examples and data to illustrate the severity of the issue.
- Solution Overview: Describe the proposed solution and its benefits. Explain how addressing deferred maintenance will improve operations, safety, and efficiency.
- ROI Analysis: Provide a detailed analysis of the ROI of addressing deferred maintenance, including cost savings, increased efficiency, and improved safety. Use data and projections to support your claims.
- Implementation Plan: Outline the steps required to implement the solution, including timelines, budgets, and resource allocation. This shows that you have a clear and actionable plan.
- Conclusion: Summarize the key points and reiterate the importance of addressing deferred maintenance. Emphasize the long-term benefits and the positive impact on the organization.
Following these steps, you can build a strong business case to support your request for additional budget and resources to address deferred maintenance.
This will help ensure your facility remains safe, efficient, and operational for years.
Leveraging Technology to Streamline Maintenance Management
In today’s digital age, technology is important in effective maintenance management. A Computerized Maintenance Management System (CMMS) like WorkTrek can be transformative in reducing deferred maintenance by providing powerful tools for tracking, scheduling, and analyzing maintenance activities.
Automating Work Orders
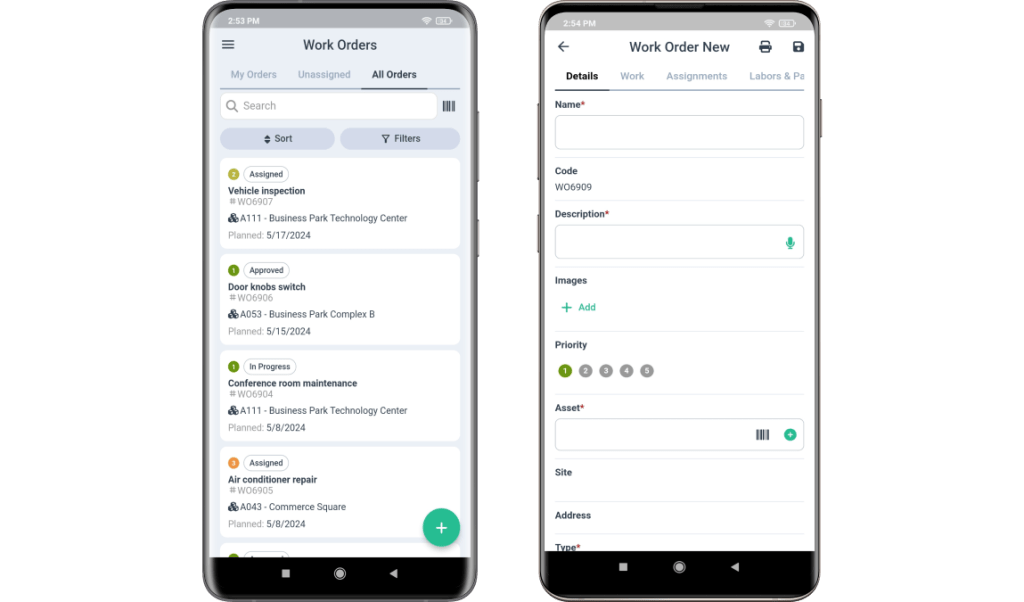
A CMMS can automatically generate work orders based on predetermined maintenance schedules, ensuring routine maintenance isn’t overlooked or delayed. This automation helps eliminate human error and provides consistent maintenance scheduling.
Tracking Asset History
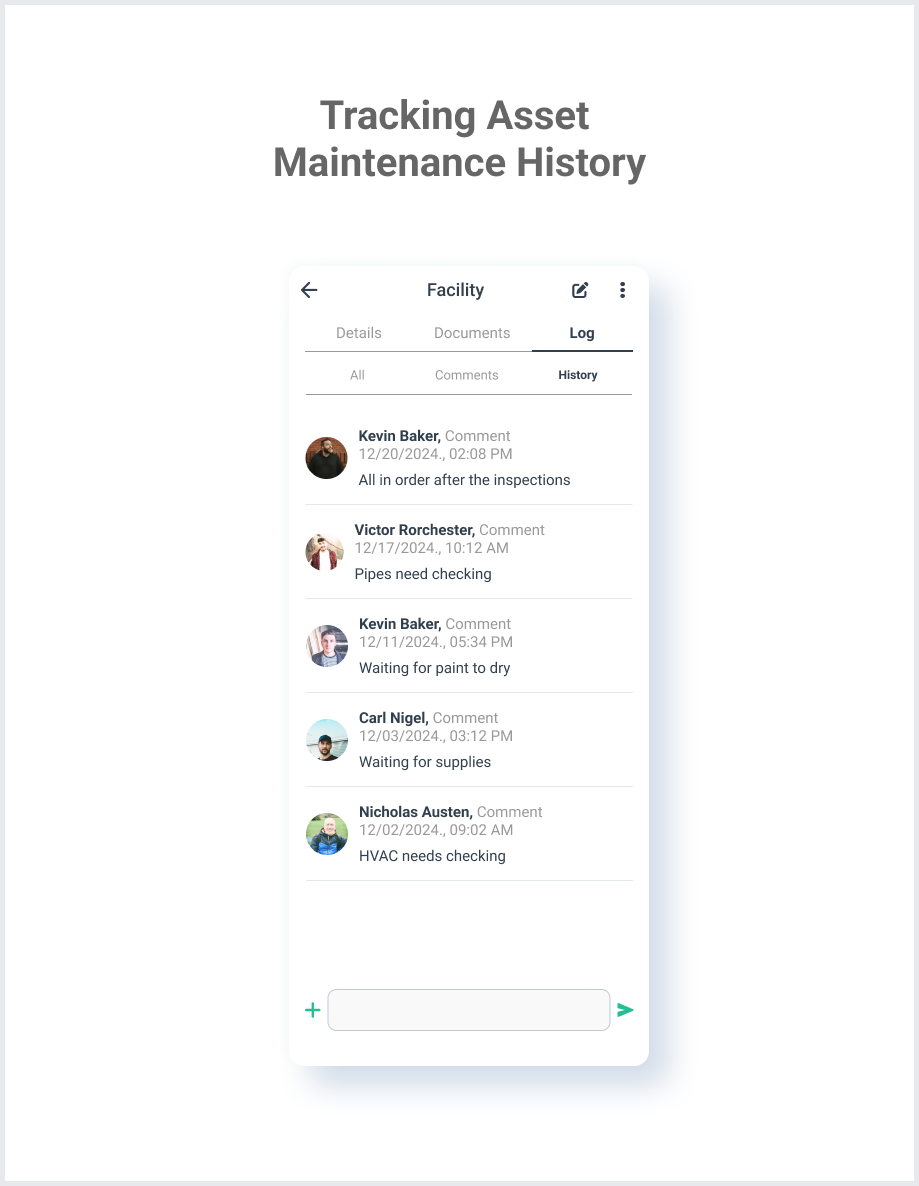
By maintaining detailed records of asset maintenance history, a CMMS helps identify patterns and predict potential failures before they occur. This historical data becomes invaluable for making informed decisions about costly repairs versus replacement and optimizing maintenance schedules.
Resource Management
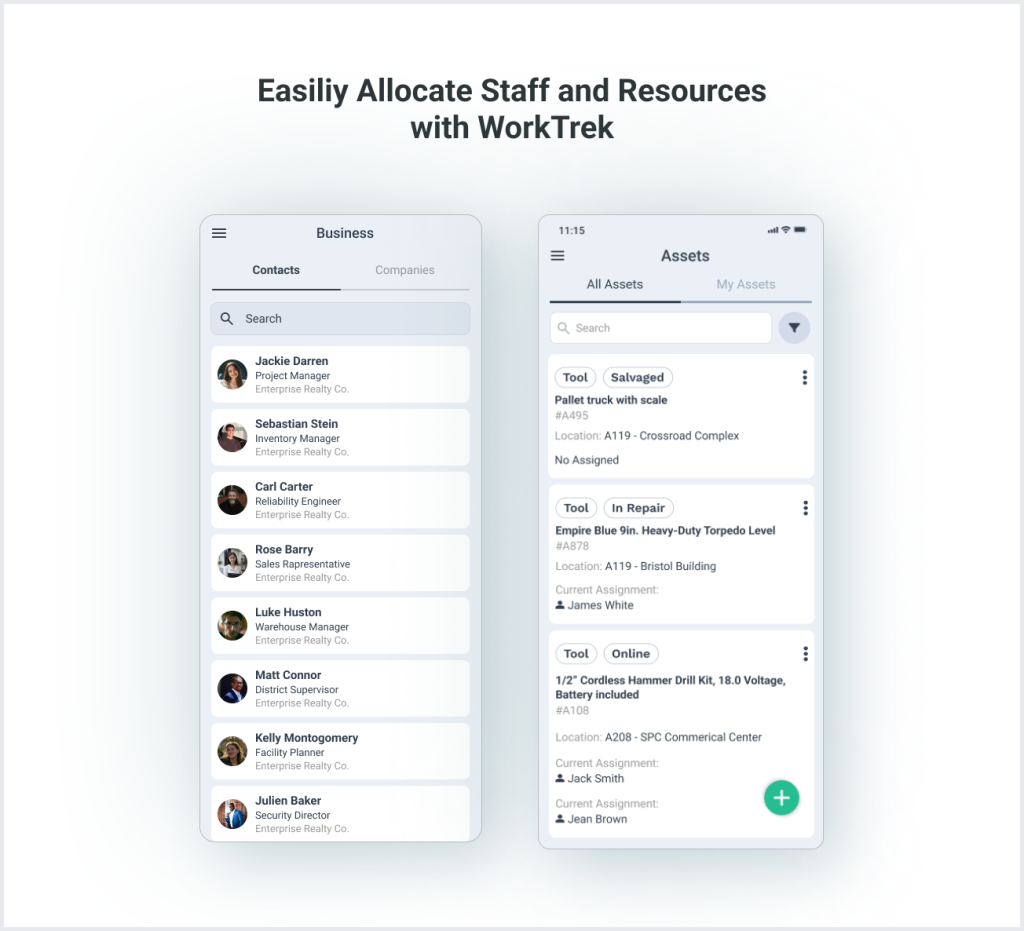
Efficient allocation of maintenance staff and resources becomes much easier with a system that tracks work orders, maintenance schedules, and resource availability in real time. This includes:
- Staff scheduling and workload balancing
- Parts inventory management
- Contractor coordination
- Budget tracking and forecasting
- Tool and equipment allocation
Creating a Sustainable Maintenance Culture
Reducing deferred maintenance isn’t just about implementing new systems and processes – it requires a cultural shift within the organization. This cultural transformation involves several key elements:
Training and Development
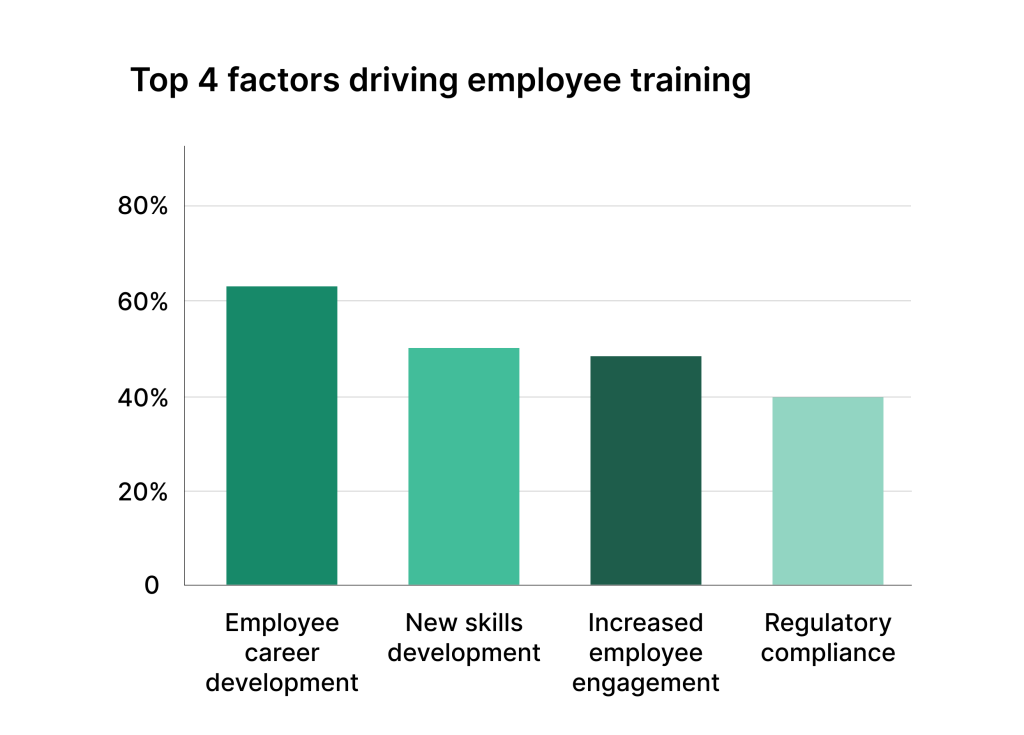
Invest in regular training for maintenance staff to ensure they have the skills to perform preventive maintenance effectively. This includes:
- Technical skills training
- Safety procedures and protocols
- New technology and equipment training
- Best practices for specific systems
- Sustainability and energy efficiency awareness
Communication and Collaboration
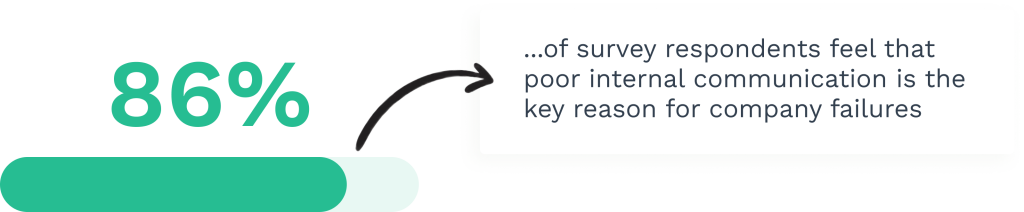
Foster open communication between maintenance staff, facility users, and management to promptly identify and address maintenance needs. This might involve:
- Regular team meetings
- Clear reporting procedures
- Feedback mechanisms
- Cross-departmental collaboration
- Stakeholder engagement
Measuring Success and Continuous Improvement
To ensure your deferred maintenance reduction efforts are effective, you need to track key performance indicators (KPIs) such as:
- Maintenance backlog reduction rate
- Percentage of preventive vs. reactive maintenance
- Asset uptime and reliability
- Maintenance costs per square foot
- Energy efficiency metrics
- Work order completion rates
- Response times to maintenance requests
- Safety incident rates
- Occupant satisfaction levels
Regularly reviewing these metrics helps identify what’s working and what needs adjustment in your maintenance strategy. Consider implementing quarterly reviews of your maintenance program to assess progress and make necessary adjustments.
Conclusion: A Journey, Not a Destination
Reducing deferred maintenance is an ongoing process that requires commitment, resources, and a strategic approach. By implementing the abovementioned strategies, facility managers can break the deferred maintenance cycle and create a more sustainable maintenance program.
Remember that success in reducing deferred maintenance doesn’t happen overnight. It requires consistent effort, regular evaluation, and strategy adjustments as needed.
The key is to start by clearly understanding your current situation, develop a comprehensive plan, and maintain a focus on long-term facility health rather than short-term cost savings.
Reducing deferred maintenance has benefits far beyond the immediate financial savings. These include improved occupant satisfaction, enhanced safety, better energy efficiency, and increased property value.
By taking these steps and remaining committed to the process, facility managers can significantly reduce their deferred maintenance backlog and create a more efficient, reliable, and cost-effective facility maintenance program.