Get a Free WorkTrek Demo
Let's show you how WorkTrek can help you optimize your maintenance operation.
Try for freeWhat exactly is machine maintenance, and has it changed? Modern machine maintenance has evolved beyond the simple “fix it when it breaks” approach.
Today’s maintenance strategies combine sophisticated monitoring techniques with preventive measures to ensure equipment reliability while optimizing costs.
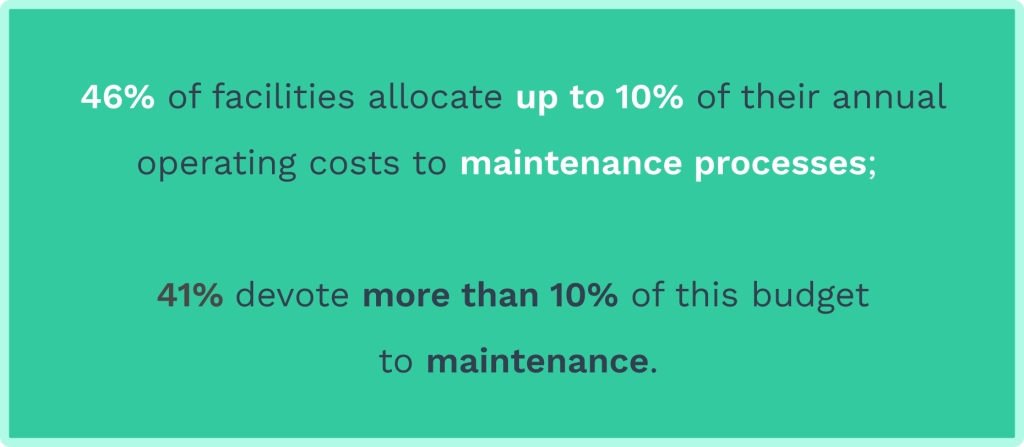
Illustration: WorkTrek / Data: Plant Engineering
Understanding the main types of machine maintenance helps organizations make informed decisions about their maintenance programs. This article is a complete guide to machine maintenance.
The Evolution of Machine Maintenance
Maintenance strategies have transformed alongside technological advancement. What began as simple reactive repairs has developed into a complex field incorporating predictive analytics and proactive measures.
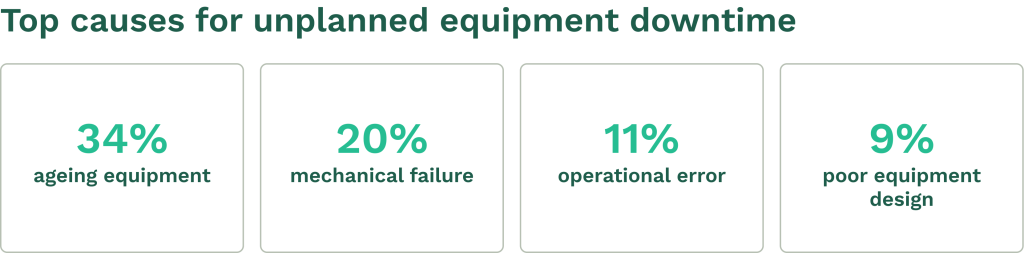
Illustration: WorkTrek / Data: Infraspeak
This evolution reflects our growing understanding of how equipment fails, how to prevent these failures efficiently, and how to incorporate them into the right types of maintenance.
Preventive Maintenance: The Scheduled Solution
Preventive maintenance introduces regularity to equipment care through scheduled inspections and services.
This is the holy grail of all maintenance approaches, but it can be more costly to execute.
This approach mirrors regular vehicle maintenance, where services occur at specific intervals regardless of condition.
This strategy effectively reduces unexpected failures and extends equipment life, though it may sometimes result in unnecessary maintenance.

Illustration: WorkTrek / Data: MaintainX
Preventive maintenance benefits organizations with critical equipment with clear wear patterns. Manufacturing facilities often implement this approach for production-critical machinery where consistent operation is essential.
For maintenance managers, the key is balancing maintenance frequency with operational needs—too frequent maintenance wastes resources, while insufficient maintenance risks failure.
Reactive Maintenance: The Basic Approach
Unlike preventive maintenance, reactive maintenance, sometimes called corrective maintenance, represents the most straightforward maintenance strategy.
Equipment runs until complete failure occurs, at which point repairs are made.
So what’s the catch?
This approach requires minimal initial planning and lower upfront costs, but it often results in longer downtimes and higher repair expenses.
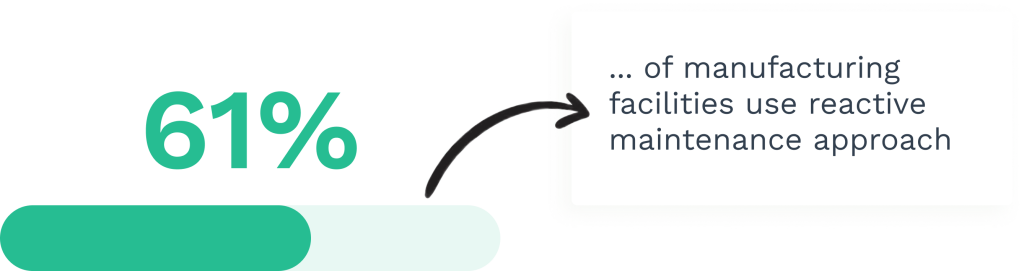
Illustration: WorkTrek / Data: Technomax
This strategy works well for non-critical equipment where replacement costs less than prevention. Use reactive maintenance for backup systems or quickly replaceable components where failure won’t significantly impact operations.
The simplicity of reactive maintenance comes at a cost. Unexpected breakdowns can halt production, create safety hazards, and lead to cascade failures in connected systems.
Are there times you can use reactive? This approach is viable if for your simple and non-critical equipment.
Predictive Maintenance: The Data-Driven Future
Predictive maintenance represents the intersection of traditional maintenance practices and modern technology.
By utilizing condition-monitoring equipment and data analysis, organizations can anticipate failures before they occur. This approach optimizes maintenance timing and reduces unnecessary interventions.

Illustration: WorkTrek / Data: Reliable Plant
Implementing predictive maintenance requires significant initial investment in monitoring equipment and personnel training.
However, organizations operating expensive machinery or those where downtime carries substantial costs often find this investment worthwhile.
Proactive Maintenance: The Root Cause Solution
Proactive maintenance focuses on identifying and eliminating the sources of equipment failure. Rather than simply preventing failures, this approach aims to fundamentally improve system design and operation.
This strategy requires deep analysis of failure patterns and a commitment to continuous improvement.
Organizations implementing proactive maintenance often see long-term benefits through reduced maintenance requirements and improved equipment reliability.
This approach is valuable in facilities with recurring equipment problems or those seeking to optimize their maintenance programs comprehensively.
Usage-Based Maintenance: Just-in-time maintenance
Usage-based maintenance is a strategic approach that schedules maintenance activities based on actual equipment utilization rather than calendar time.
This method recognizes that wear and deterioration primarily occur during operation. This makes, metrics like operating hours, cycles completed, or production volume more relevant than fixed time intervals.
Think of it like maintaining a car based on miles driven rather than months owned. A vehicle driven 50,000 miles in one year needs maintenance sooner than one driven 5,000 miles in the same period.
Similarly, two identical machines might require different maintenance schedules based on their workload in industrial settings.
Condition-Based Maintenance: The X-Ray method
Condition-based maintenance is a sophisticated approach that relies on real-time equipment health monitoring to determine when maintenance is necessary.

Source: WorkTrek
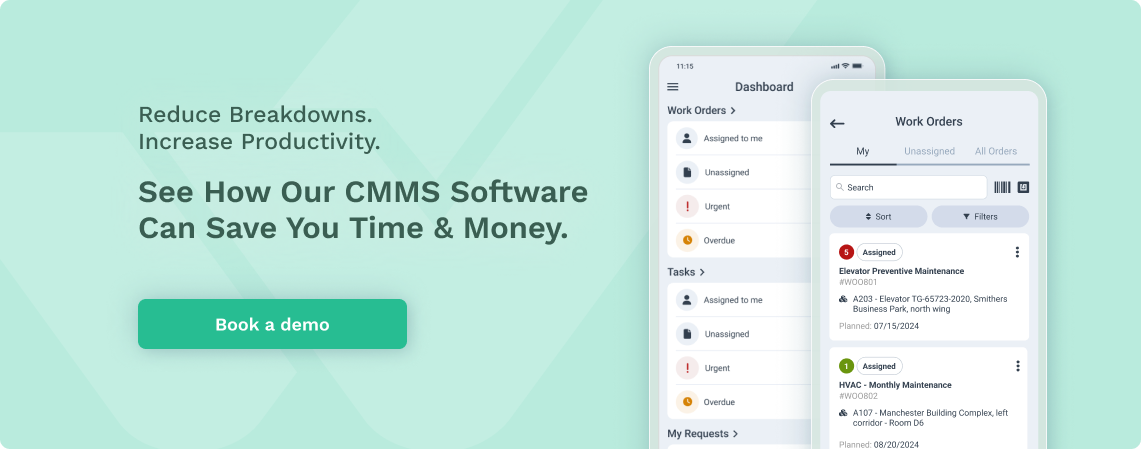
Rather than following fixed schedules or usage metrics, this method uses various smart sensors and monitoring tools to track key performance indicators. The signals from the sensors can then provide insight into potential problems.
Think of it like modern health monitoring – just as a smartwatch tracks vital signs to detect health issues early, condition-based maintenance uses sensors to monitor equipment vital signs such as vibration, temperature, oil condition, or noise levels.
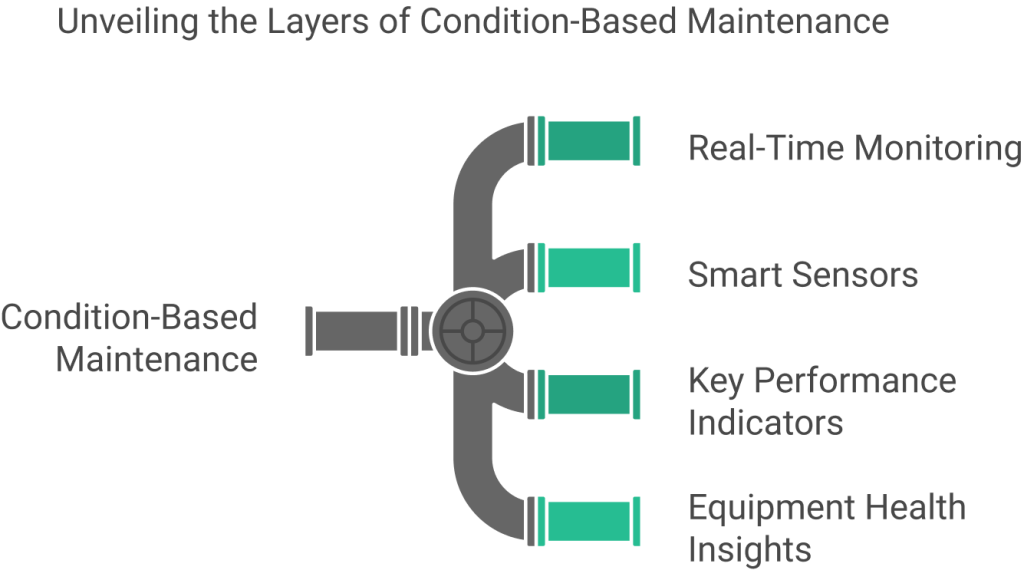
Source: WorkTrek
When these indicators deviate from normal ranges, they trigger maintenance actions.
For example, a manufacturing facility might use vibration sensors on rotating equipment to detect subtle changes that indicate bearing wear.
Similarly, thermal imaging can identify unusual heat patterns suggesting electrical or mechanical problems.
This real-time monitoring allows maintenance teams to address issues at the optimal time – not too early, which wastes resources, and not too late, which risks equipment failure.
Software Tools for Machine Maintenance
Trying to run any of the above maintenance approaches manually will be painful. Managing work orders and parts using a paper-based approach will be slow and error-prone.
This is where implementing a CMMS system like WorkTrek comes in.
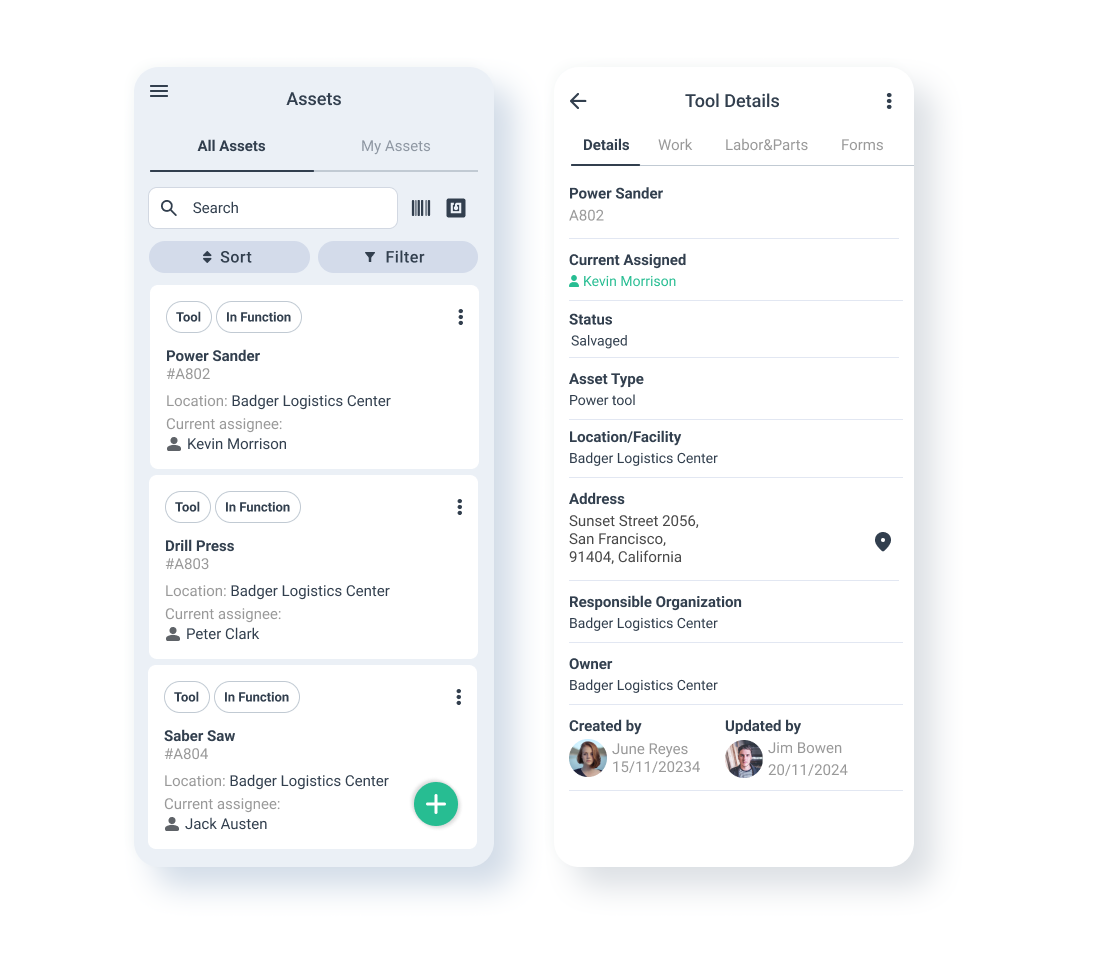
Source: WorkTrek
There are several benefits to implementing a CMMS system to manage your machine maintenance needs. They include:
- Work Order Management
- Preventive Maintenance Automation and Scheduling
- Asset Management
- Inventory Control
- Resource Planning
- Reports and Analytics
How to Create an Effective Maintenance Strategy
There is not a single maintenance program that can fit all scenarios.
Instead, they combine elements from each strategy based on equipment criticality, resource availability, and operational requirements. The key lies in understanding each equipment’s role in operations and failure patterns.
Consider a manufacturing facility as an example. Critical production equipment might warrant predictive maintenance with sophisticated monitoring systems.
Support equipment could operate under a preventive maintenance schedule.
Less critical components might follow a reactive maintenance approach. Meanwhile, persistent problem areas become targets for proactive improvement efforts.
Making the Right Choice
Sometimes, selecting the correct maintenance strategy is not easy. Before making your decision, you need to evaluate several factors.
Equipment criticality plays an important role – more important machinery justifies more sophisticated maintenance approaches. Cost considerations must balance immediate expenses against long-term savings. Resource availability, including skilled personnel and monitoring technology, often constrains strategy selection.
The most effective maintenance programs evolve continuously. Regular assessment of maintenance outcomes helps organizations refine their approaches. This might mean shifting some equipment to different maintenance strategies or adjusting maintenance intervals based on observed performance.
Looking Forward: The AI-Driven Evolution of Machine Maintenance
The future of machine maintenance is poised for a technological revolution. Artificial Intelligence and Machine Learning are transforming traditional maintenance approaches into sophisticated, predictive systems that can fundamentally change how we care for equipment.
The Rise of Intelligent Maintenance Systems
Modern AI systems can process vast amounts of sensor data to detect impossible patterns for human operators to identify.
These systems learn from historical maintenance records, real-time operational data, and equipment specifications to create increasingly accurate failure predictions.
For example, an AI system might notice that a particular motor’s power consumption pattern, combined with subtle vibration changes, indicates an impending bearing failure weeks before traditional monitoring methods detect any issues.
Machine Learning algorithms continuously improve their predictive capabilities through exposure to new data. As these systems observe more equipment failures and maintenance interventions, they refine their understanding of failure mechanisms and early warning signs.
This learning process creates a virtuous cycle where prediction accuracy increases over time, leading to more precise maintenance scheduling and fewer unexpected failures.
Digital Twins and Simulation-Based Maintenance
Digital twin technology represents another frontier in maintenance evolution. These virtual replicas of physical equipment can simulate operating conditions and predict wear patterns with unprecedented accuracy.
By running thousands of simulations under various conditions, maintenance teams can better understand how different operating parameters affect equipment life and optimize maintenance schedules accordingly.
These digital models become increasingly sophisticated as they incorporate more real-world data. They can simulate entire production systems, helping maintenance teams understand how equipment interactions might lead to cascading failures or unexpected stress points.
This system-level view enables more strategic maintenance planning that considers the entire operation rather than just individual pieces of equipment.
The Integration of IoT and Edge Computing
The proliferation of Internet of Things (IoT) sensors provides the foundation for AI-driven maintenance systems.
These sensors can monitor everything from temperature and vibration to acoustic signatures and power consumption patterns. Edge computing capabilities allow for real-time processing of this data directly at the equipment location, enabling immediate response to developing issues.
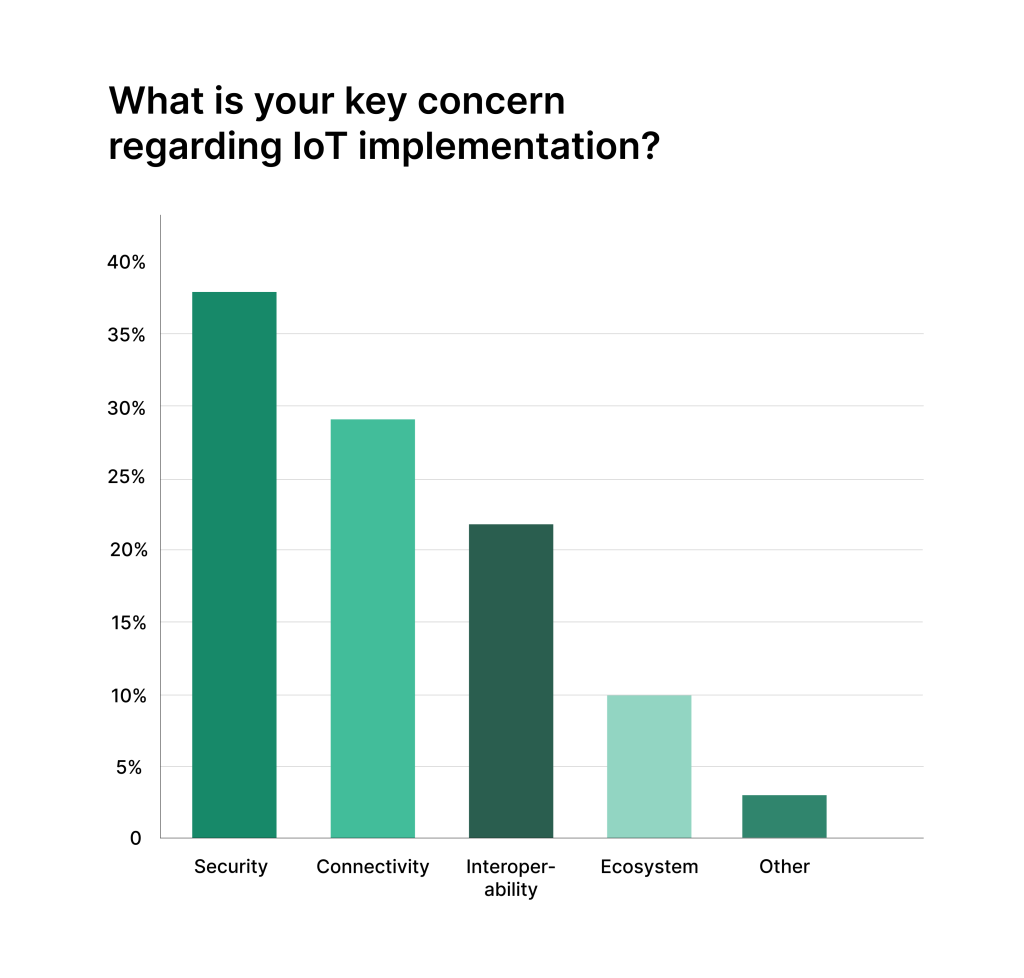
Illustration: WorkTrek / Data: Newark
This distributed intelligence creates new possibilities for maintenance automation. When they detect potential problems, smart sensors can automatically adjust operating parameters to reduce stress on equipment.
They can also trigger maintenance requests automatically when they identify specific condition patterns, reducing the delay between problem detection and corrective action.
Augmented Reality in Maintenance Operations
Augmented Reality (AR) technology revolutionizes how maintenance personnel interact with equipment. AR systems can overlay real-time sensor data, maintenance history, and repair instructions directly onto equipment as technicians view it through smart glasses or mobile devices.
This technology reduces repair times and improves accuracy by providing contextual information exactly when and where it’s needed.
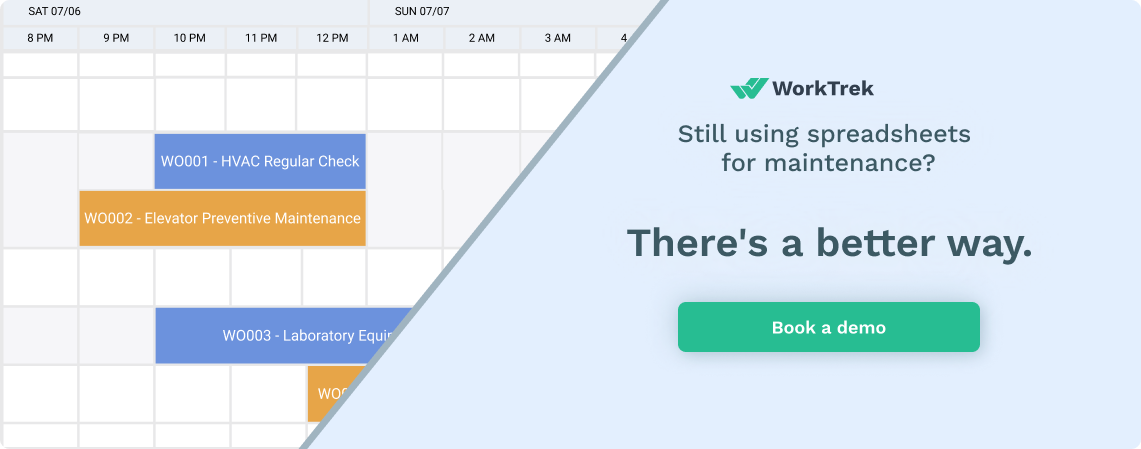

Illustration: WorkTrek / Data: FieldCricle
Future AR systems will likely incorporate AI-powered assistance that can guide technicians through complex repairs, automatically identify parts, and provide real-time feedback on repair quality.
These systems might even predict what tools and parts will be needed for specific repairs, streamlining maintenance operations and reducing downtime.
Predictive Analytics and Resource Optimization
Advanced analytics platforms are beginning to optimize maintenance timing and resource allocation across entire facilities. These systems can more effectively predict parts requirements, optimize inventory levels, and schedule maintenance personnel.
To create optimal maintenance schedules, they consider equipment criticality, maintenance history, current operating conditions, and even weather forecasts.
Incorporating machine learning into these systems enables them to adapt to changing conditions automatically. They can adjust maintenance schedules based on production demands, personnel availability, and economic factors like energy costs or raw material prices.
Challenges and Considerations
While AI and machine learning offer tremendous potential for improving maintenance operations, their implementation presents several challenges.
Organizations must consider data quality and quantity requirements, integration with existing systems, personnel training needs, and cybersecurity implications.
Success requires a strategic approach that balances technological capabilities with practical implementation considerations.
Data privacy and security concerns also need careful attention as maintenance systems become more connected and data-driven. Organizations must implement robust security measures to protect their equipment data and maintenance management systems from cyber threats.
The Human Factor in Future Maintenance
Despite increasing automation, human expertise remains crucial in maintenance operations. Maintenance personnel’s role will evolve from reactive repair work to more strategic activities such as system optimization, data analysis, and predictive planning.
This evolution requires new skills and training approaches to prepare maintenance teams for changing responsibilities.
The most successful maintenance programs of the future will likely combine AI capabilities with human insight and experience.
While AI systems can process vast amounts of data and identify patterns, human judgment remains essential for understanding context, making strategic decisions, and handling unique situations that AI hasn’t encountered before.
Industries that Depend on Machine Maintenance
Several industries depend on machine maintenance to keep their operations running smoothly. Below are a few examples:
Manufacturing
Manufacturing is perhaps the most obvious example, where production lines depend on properly functioning equipment. Consider an automotive assembly plant: Every robot, conveyor belt, and welding machine needs regular maintenance to ensure cars can be produced without interruption. A single hour of downtime could mean hundreds of vehicles not being completed on schedule.
Transportation
The transportation sector relies heavily on maintenance, particularly in aviation. Aircraft maintenance isn’t just about efficiency—it’s a matter of safety. Airlines follow strict maintenance schedules for every component, from engines to landing gear. Similarly, railroad companies must maintain their locomotives and tracks to prevent accidents and ensure on-time performance.
Energy
Energy production presents another fascinating case. Power plants, whether nuclear, coal, or renewable, require constant maintenance to generate electricity reliably. For instance, wind farms need regular inspection and maintenance of turbine bearings, gears, and blades to maximize power generation and prevent failures during high winds.
Food Services
The food and beverage industry depends on maintenance tasks to meet strict hygiene standards and maintain production quality. Think about a large brewery: The brewing equipment, bottling lines, and refrigeration systems need precise maintenance to ensure consistent product quality and prevent contamination.
Healthcare
Healthcare facilities represent a critical application of maintenance. Medical equipment like MRI machines, ventilators, and surgical tools must be maintained meticulously to ensure patient safety and accurate diagnoses. A malfunctioning piece of equipment could be a matter of life and death.
Mining

Illustration: WorkTrek / Data: Innovapptiove
Mining operations showcase how maintenance can impact both safety and productivity. Underground mining equipment operates in harsh conditions, dealing with dust, moisture, and extreme temperatures. Regular maintenance of drilling machines, ventilation systems, and transport equipment is essential to prevent accidents and maintain production targets.
Telecommunications
Even the telecommunications industry, which might not immediately come to mind, relies heavily on maintenance. Cell towers, data centers, and network infrastructure require constant upkeep to maintain the connectivity we take for granted. A single failed cooling system in a data center could disrupt services for millions of users.
Summary
The future of machine maintenance lies in the intelligent integration of AI, machine learning, and human expertise. These technologies promise to make maintenance more predictive, precise, and cost-effective than ever before.
Choosing the right maintenance strategy depends on your organizational goals and budget.
Organizations that embrace these advances while thoughtfully addressing implementation challenges will gain significant competitive advantages through improved equipment reliability and reduced maintenance costs.
As these technologies evolve, the key to success will be maintaining flexibility in maintenance strategies and being ready to adopt new approaches as they prove their value.
The future of maintenance is not just about fixing machines – it’s about creating intelligent, adaptive systems that keep equipment running at peak efficiency while minimizing costs and downtime.