Get a Free WorkTrek Demo
Let's show you how WorkTrek can help you optimize your maintenance operation.
Try for freeAre you constantly battling unexpected equipment breakdowns that disrupt your operations?
Are your maintenance costs through the roof?
If yes, you will benefit from better maintenance planning.
This article will act as a crash course in this vital aspect of maintenance management.
We’ll explain why it’s so important to plan it, which industries benefit the most from it, which tools you could use, and more.
So, consider stumbling upon this article as a sign that your maintenance regime is ready to be improved.
Let’s get started.
Benefits of Maintenance Planning
Would you believe us if we told you that maintenance planning is the key to skyrocketing your productivity and profitability?
Let’s see why.
Maintenance planning involves outlining all the necessary upkeep activities, targets, risks, resources, and procedures, all with the goal of making sure your assets are properly taken care of.
The result?
Far fewer equipment failures, inefficiencies, and operational disruptions.
Simply put, with maintenance plans, you’re in control. Without them, things happen to you.
Did you know that in 2022, according to the Advanced Technology Services Industry Maintenance Survey, unscheduled downtime was cited as the number one cause of lost plant productivity?
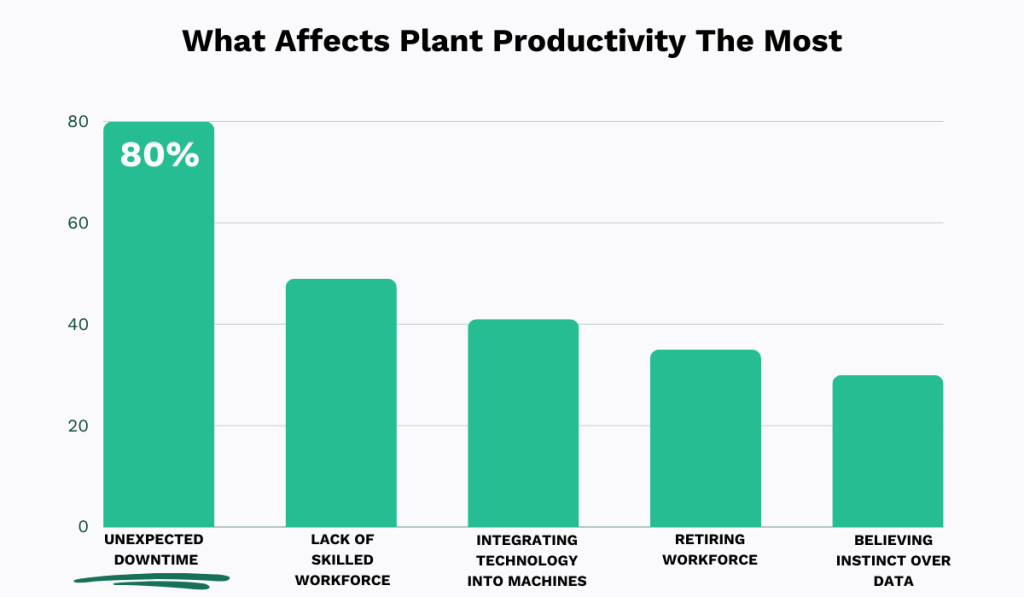
And it’s easy to see why.
When a machine unexpectedly breaks down, other work usually needs to be stopped until the problem is investigated and resolved, which can take a lot of time.
Well, guess what?
Maintenance planning addresses this issue head-on by laying out all upkeep tasks in advance, ensuring assets are regularly serviced and protected against unexpected failure.
But unplanned downtime doesn’t just waste time; it can also drain money.
Siemens has the numbers to back this up.
They did a survey in 2022 and found that automotive plants lose a whopping two million dollars per hour due to downtime.
The oil and gas industry isn’t far behind, losing $500,000 per hour.
This further demonstrates how important it is to plan your upkeep activities proactively.
It isn’t only about making sure everyone knows what they need to do, but about actually protecting the entire organization from unnecessary disruptions and expenses.
Terri Ghio, former President of FactoryEye, a global software provider, agrees that proper and regular asset care is far more cost-effective in the long run.
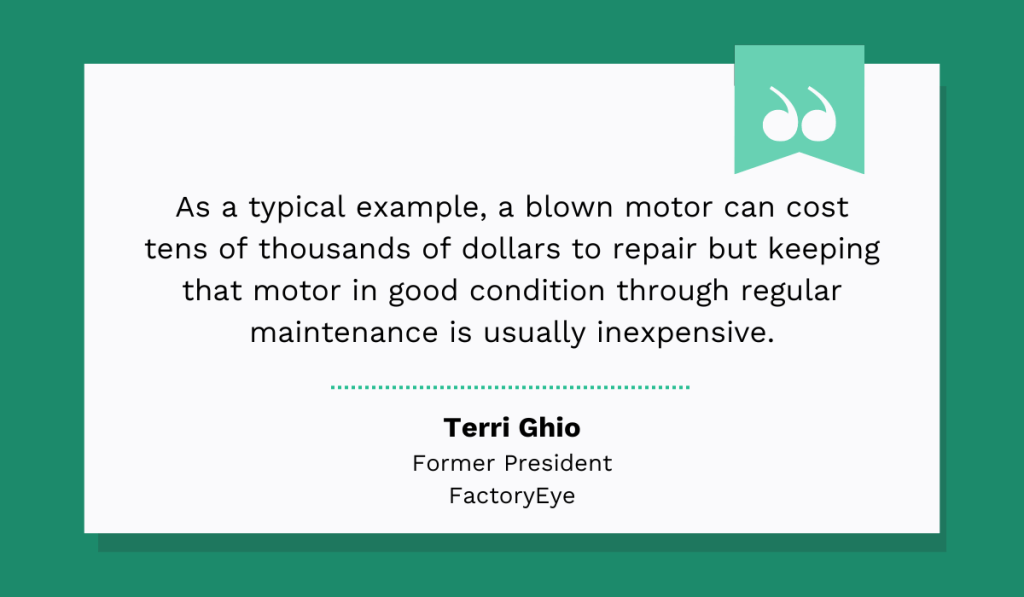
But proper and regular asset care requires an efficient maintenance plan.
Without it, there would be no clearly defined roles or procedures, and the team would struggle to execute tasks efficiently, leaving your valuable machinery neglected and poorly maintained.
And if you need more proof of the benefits of a good plan, just ask Tim Newman, Maintenance Manager at Simmons Feed Ingredients, a poultry, pet, and ingredient products supplier.
He experienced firsthand how much of a game-changer strategic planning can be.
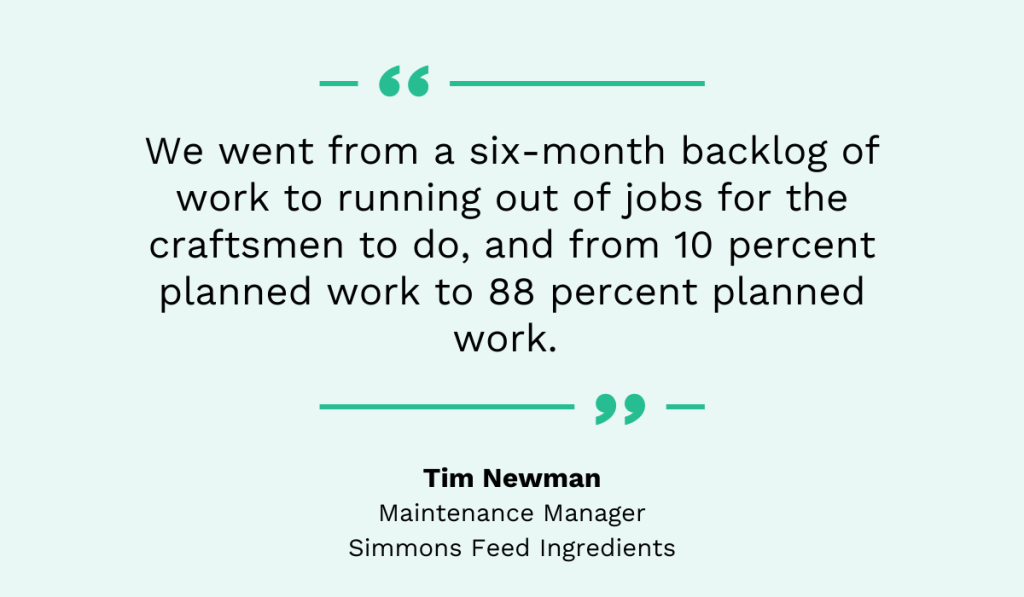
See?
It all starts with a well-thought-out maintenance plan, from reducing downtime and prolonging equipment’s lifespan to ultimately increasing overall productivity and profits.
Maintenance Planning vs Maintenance Scheduling
Although they are both vital components of maintenance management, planning and scheduling are two completely different processes.
Planning focuses on the what, why, and how of the entire upkeep process and typically happens before scheduling.
It defines the goals for maintenance efforts and lays out resources, budgets, activities, and standard operating procedures (SOPs), establishing the foundation for an efficient and cost-effective maintenance strategy.
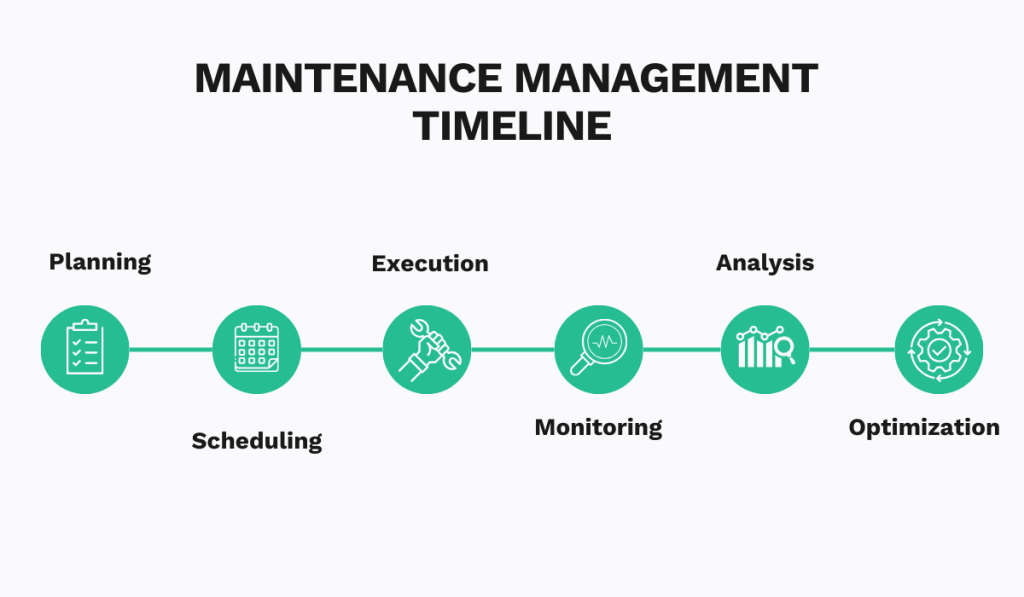
Following planning, scheduling addresses the when and who, specifying timelines as well as assigning personnel to perform the tasks that you have outlined in the plan.
The main scheduling objective is to minimize operational disruptions by ensuring maintenance is performed during scheduled downtime, preventing any dips in productivity.

So, why does planning go before scheduling?
Imagine you schedule service for a piece of equipment, and when the day comes, you realize you don’t have the necessary spare parts to perform the task.
Planning ensures everything is in place beforehand, so there are no delays when it’s time to do the work.
Ultimately, planning and scheduling are equally essential and require dedicated time and attention.
Do them right, and your workflows will be smoother, procedures more efficient, and your equipment’s reliability much higher.
Doc Palmer, an expert in scheduling and planning, points out another interesting perk of these two processes.
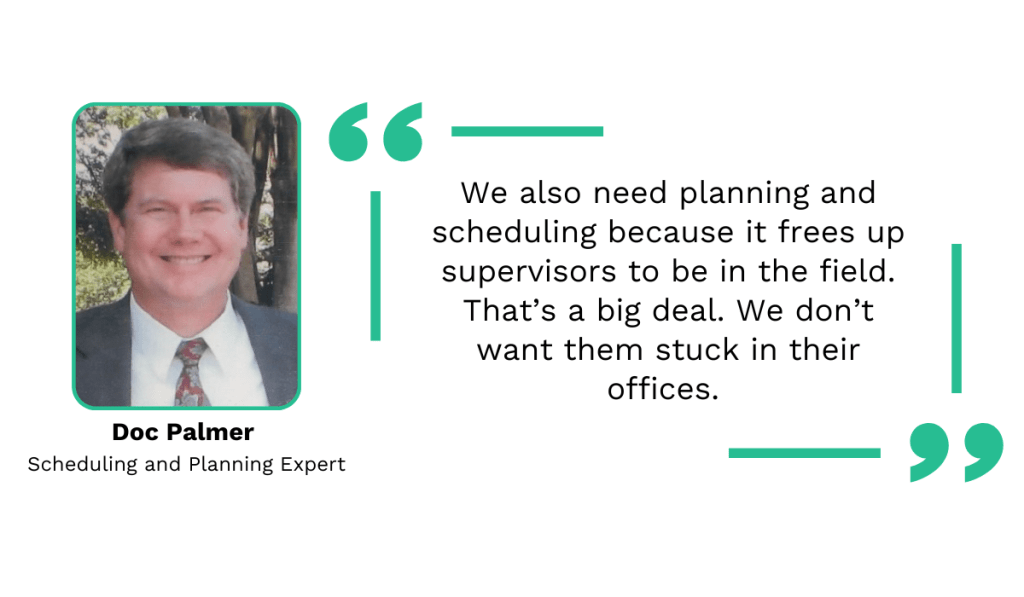
That’s right, viewing these as separate functions and appointing dedicated experts to each can free supervisors to focus on more critical tasks.
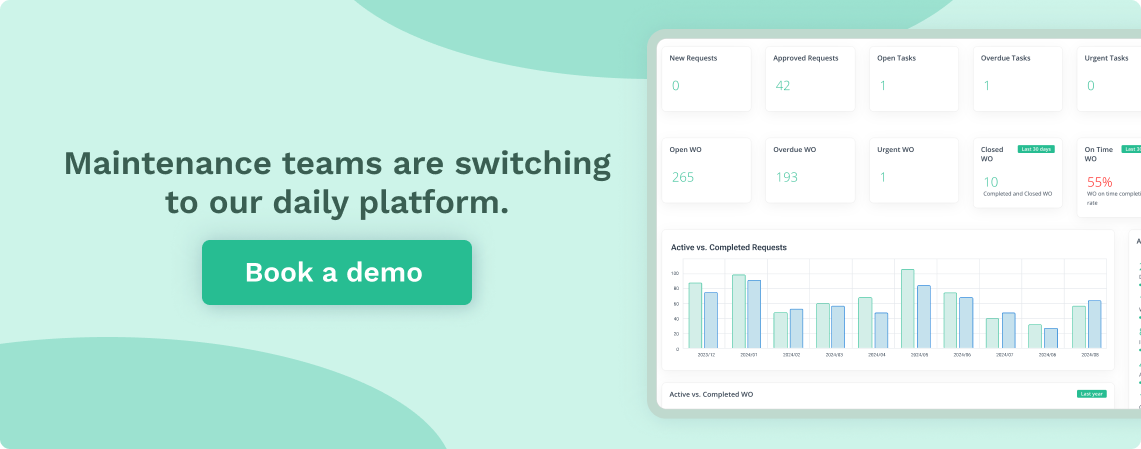
It’s, in a way, a win-win scenario. Planning and scheduling get the focus they need, and the rest of the team can concentrate on their core responsibilities.
So, remember: while planning and scheduling are two different processes with their objectives, they must work hand-in-hand to deliver the best results.
Understand and respect their unique roles, and you’ll establish the basis for a well-coordinated, successful maintenance strategy.
Different Strategies Used in Maintenance Planning
There are four different maintenance strategies you can include in your plan: reactive, preventive, condition-based, and predictive.
Let’s briefly go over each of them.
Reactive maintenance, also known as run-to-failure, breakdown, or corrective maintenance, focuses on repairs only when an asset has failed. It doesn’t prepare for asset damage but, as the name suggests, only reacts to it.
As such, it requires little to no planning or upfront expenses.
While this might seem positive due to lower initial costs, many experts argue otherwise.
Gerard Wood, Managing Director at Wood and Media Pty Ltd, a consulting company focusing on asset management, says the following:
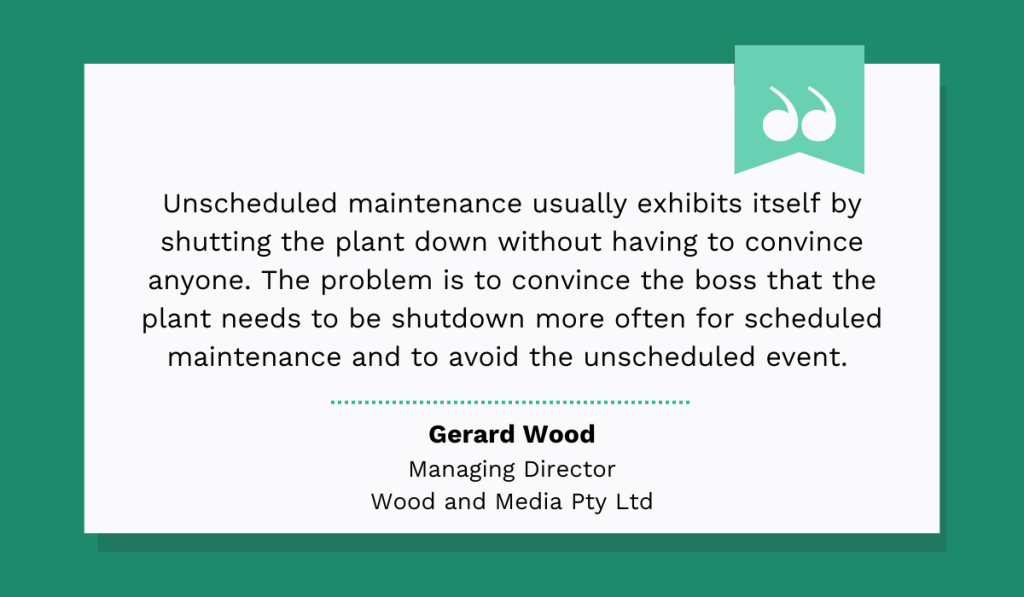
A much better approach, he says, is to regularly perform more minor repairs and inspections to keep your equipment fully operable and avoid any unpleasant surprises.
This brings us to preventive maintenance.
This strategy is much more proactive, prioritizing frequent and regular upkeep, including daily checkups, cleaning, lubrication, and parts replacements.
That way, any potential issues get nipped in the bud well before they start wreaking havoc on your operational efficiency.
According to the 2023 ABB survey, this is the most preferred form of maintenance, with 45% of businesses implementing it at the moment.
In contrast, the reactive approach is being phased out because, as the survey reports, it “leads to unplanned downtime, disrupted operations, and can halt procedures entirely.”
So, it’s good to see more and more companies working to avoid that.
Next, condition-based maintenance tracks assets’ conditions in real time to determine the necessary service tasks and activities.
It relies on various sensors to collect asset data minute-by-minute and schedule upkeep as soon as any irregularities are detected.
This could, in a way, be considered a step up from preventive maintenance, but it does come with a higher price tag due to the technology involved.
Similarly, predictive maintenance also uses tech-like sensors and machine learning to identify, detect, analyze, and address equipment problems as they arise.
But what separates this strategy from all the rest is its ability to predict future issues by analyzing asset usage patterns and history, providing insights into the actual future conditions of your machinery rather than relying solely on guesswork.
Now, you’re probably wondering: which one of these methods is the best?
Well, according to NCBI research, companies that use preventive and predictive maintenance see about 52% less unscheduled downtime and 78% fewer defects.
That’s certainly not something to glance over. But truth be told, there’s no one-size-fits-all answer.
Each of these strategies has its place in an effective maintenance plan, depending on your budget, asset’s criticality, labor availability, and other factors.
So carefully study each of them and assess your needs thoroughly, and you’ll be much better equipped to find the right path to fulfilling all your maintenance objectives.
Industries that Need Maintenance Planning
Essentially, any industry that relies on heavy machinery, different kinds of equipment, and other physical assets to conduct its operations can benefit from maintenance planning.
After all, this process is the key to long-lasting, reliable equipment, safe and efficient workflows, and effective cost control.
For example, in manufacturing, a good maintenance plan can significantly reduce unexpected equipment failures that halt production lines.
In an industry where every hour counts, such unscheduled downtime is simply unacceptable, explains Vivre Viitanen, Head of Global Service Line at ABB Motion Services, a technology leader in electrification and automation:
[…], in the food and beverage sector for example, downtime can cost from between US$4,000 and US$30,000 per hour […] Paper producers, meanwhile, lose up to US$25,000 every hour when a key asset breaks down, with the steel industry averaging around US$300,000 in losses per critical machine failure. On top of the obvious direct financial costs, downtime also presents businesses with several indirect costs, like reputational damage, health and safety risks, loss of team morale and insurance premium rises.
Therefore, for those in manufacturing, a maintenance plan is like a shield for their operational efficiency, bottom line, and overall company success.
The oil and gas industry isn’t immune to the benefits of maintenance planning, either.
In this highly complex sector, adequate maintenance of refineries, pipelines, or drilling rigs can prevent oil leaks, explosions, and prevent significant environmental damage.
According to Bruno Vidal, Business Applications Manager at Petrobras, a state-owned Brazilian oil company, a solid maintenance regime has had a huge influence on their business, preventing oil losses and boosting their bottom line.
In a way, it transformed maintenance from a cost center into a strategic partner with a considerable return on investment.
Industries operating in harsh and demanding environments, like mining, should prioritize proper asset care, too.
After all, when you work in such rough conditions, you want to be able to spot any irregularities immediately, not only because it helps you repair your equipment on time and keep it operable but also because it protects your workers from dangerous situations.
In this context, having a maintenance plan in place increases the likelihood of identifying and eliminating any possible risks before they cause substantial damage.
And, as Eugenio Gomez, Regional Manager at MineSense Technologies Ltd., a company providing mining technology, says, all of this ultimately has an impact on productivity and financial performance as well.
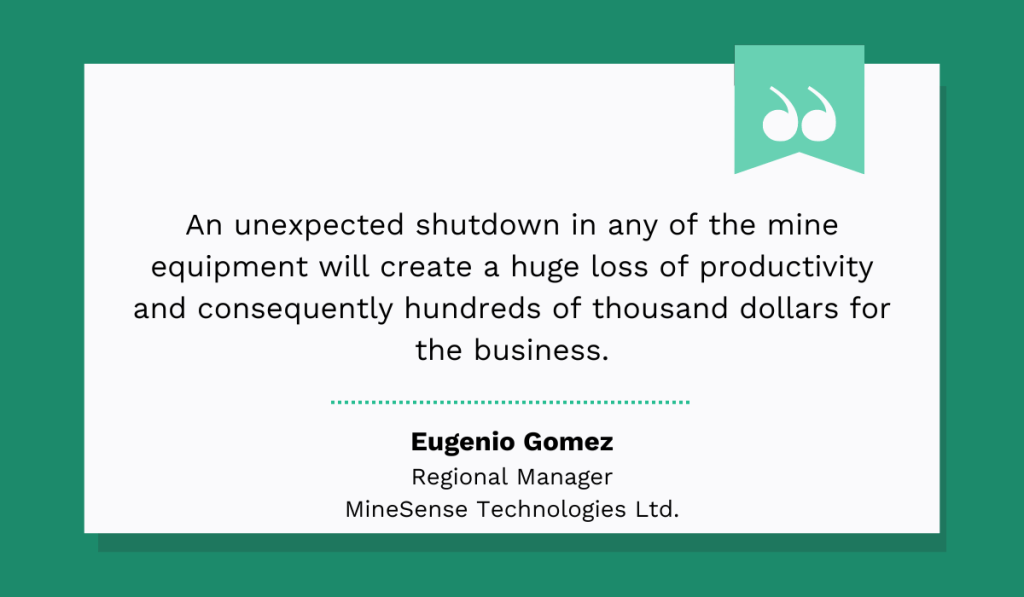
Virtually, a win-win situation.
And let’s not forget about aerospace.
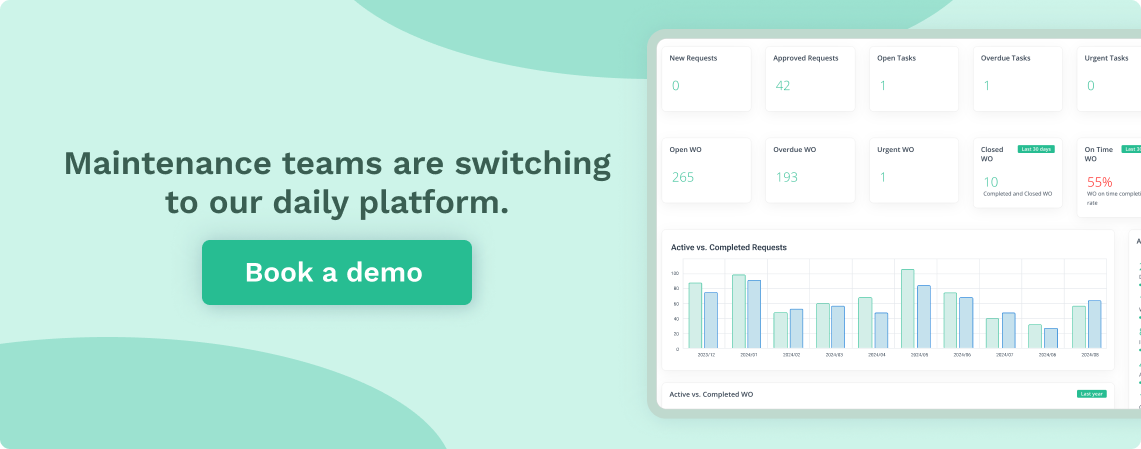
Here, upkeep planning is not just about productivity or profits but also about adhering to stringent safety standards.
Tatiana Aloia, Co-founder, CEO, and CFO of Aloia Aerospace Inc., a company selling replacement aeronautical parts, knows this all too well.
According to her, in this industry, thorough maintenance programs are an absolute must-have.
Plus, they must be constantly reevaluated and updated to accommodate the ever-changing and demanding safety rules and regulations.
At the end of the day, whether your equipment is in the air, on the ground, or deep beneath it, it requires frequent, regular, and strategic care to keep your operations running smoothly and help generate revenue.
That’s why maintenance plans are so crucial.
They prevent your equipment from turning into an operational hindrance or a financial burden and ensure they stay a valuable asset for years to come.
Tools for More Streamlined Maintenance Planning
Now, if you think that maintenance planning seems like one of those tasks that take too much effort and time, worry not.
You can use so many amazing software solutions to make the planning process quicker, easier, and more streamlined.
For instance, you could use inventory management software.
These systems automate many activities related to inventory management, from stock-level monitoring and order management to warehouse organization, significantly reducing human error and boosting overall efficiency.
Some also come with maintenance planning and scheduling features and send alerts when equipment is due for service, such as EZOfficeInventory.
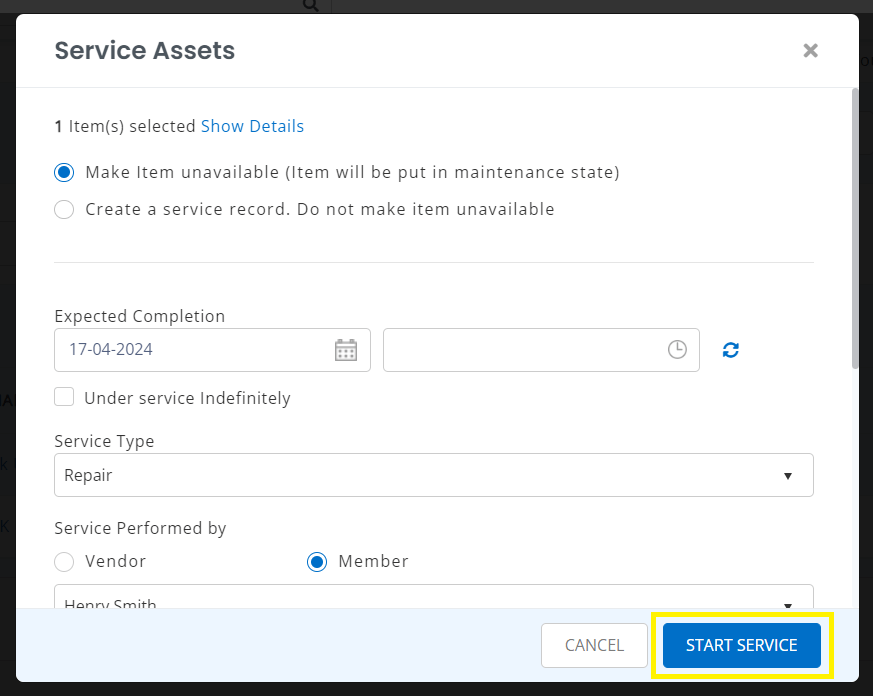
Plus, they keep track of all the spare parts, tools, and materials you need for regular upkeep, which can be a massive help during the resource planning phase.
Or, what about a work order management system—a tool designed to create, manage, and monitor work orders?
Such solutions can be a godsend for maintenance planners because they allow them to clearly define tasks that need to be carried out and assign them to employees without having to deal with endless piles of paperwork.
Besides, they keep all maintenance activities well-documented so that you can use that data as a reference for plans.
However, if you’re in need of a more well-rounded solution that encompasses all these capabilities and more, consider looking into CMMS.
According to a 2024 survey by UpKeep, these systems are the current go-to choice for a large number (65%) of organizations.
And when it comes to the benefits of the software, they often cite increased visibility into completed work, reduced unplanned downtime, and improved team communication.
Not bad for a single software solution, right?
But how do these systems exactly do it?
Let’s demonstrate using our very own maintenance management solution, WorkTrek.
WorkTrek offers a variety of features that make planning a breeze.
For starters, its asset management feature centralizes and updates all relevant asset data in real time, such as locations, costs, conditions, downtime, history, and more.
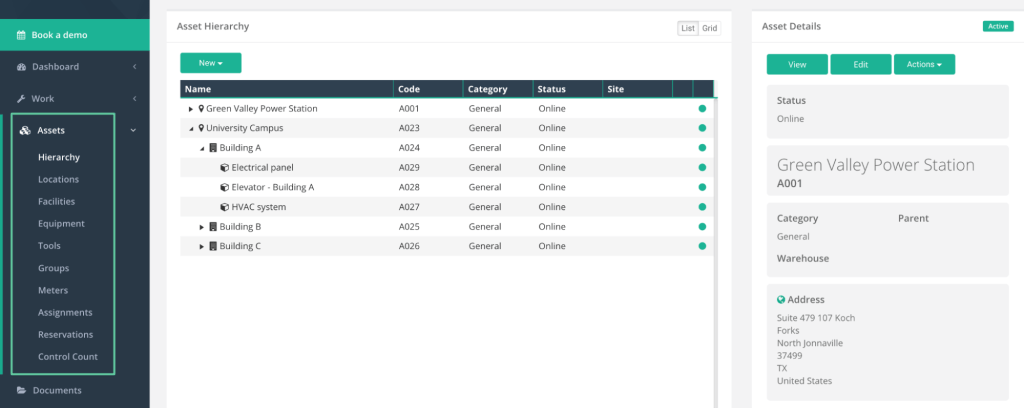
This can be your starting point during planning as it tells you all you need to know about your assets’ current state and needs.
But that’s not all.
Using WorkTrek’s preventive maintenance feature, you can automatically generate preventive work orders based on meter readings.
When sensors detect a certain value, you input that value into the system, and the system automatically creates a new work order for you.
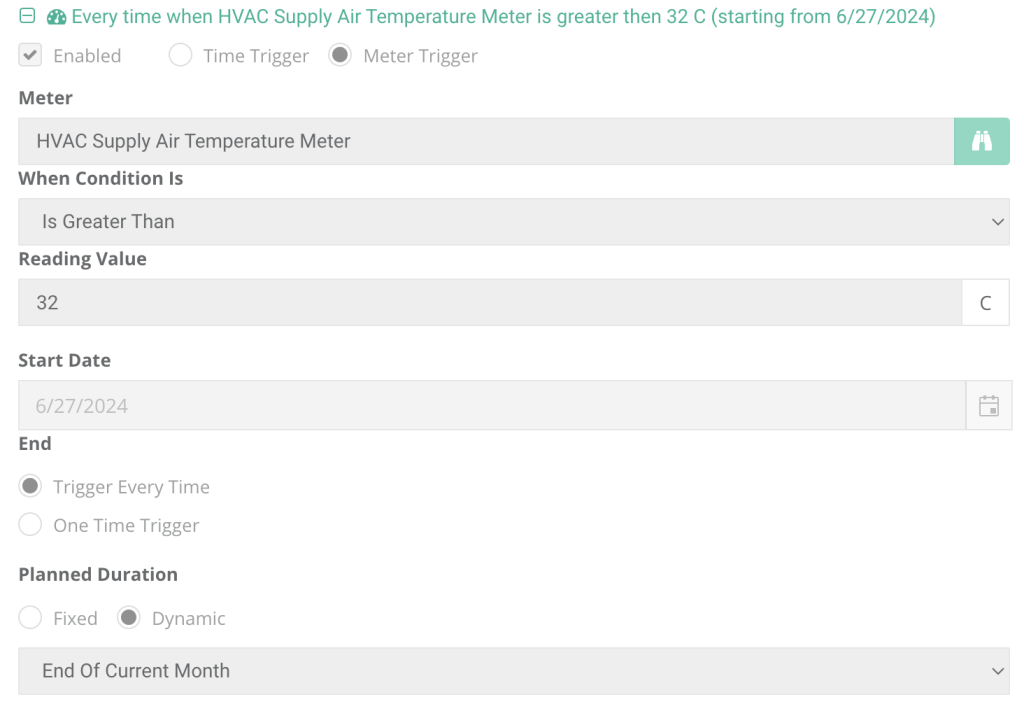
You can even create follow-up work orders after your technicians have finished their inspections.
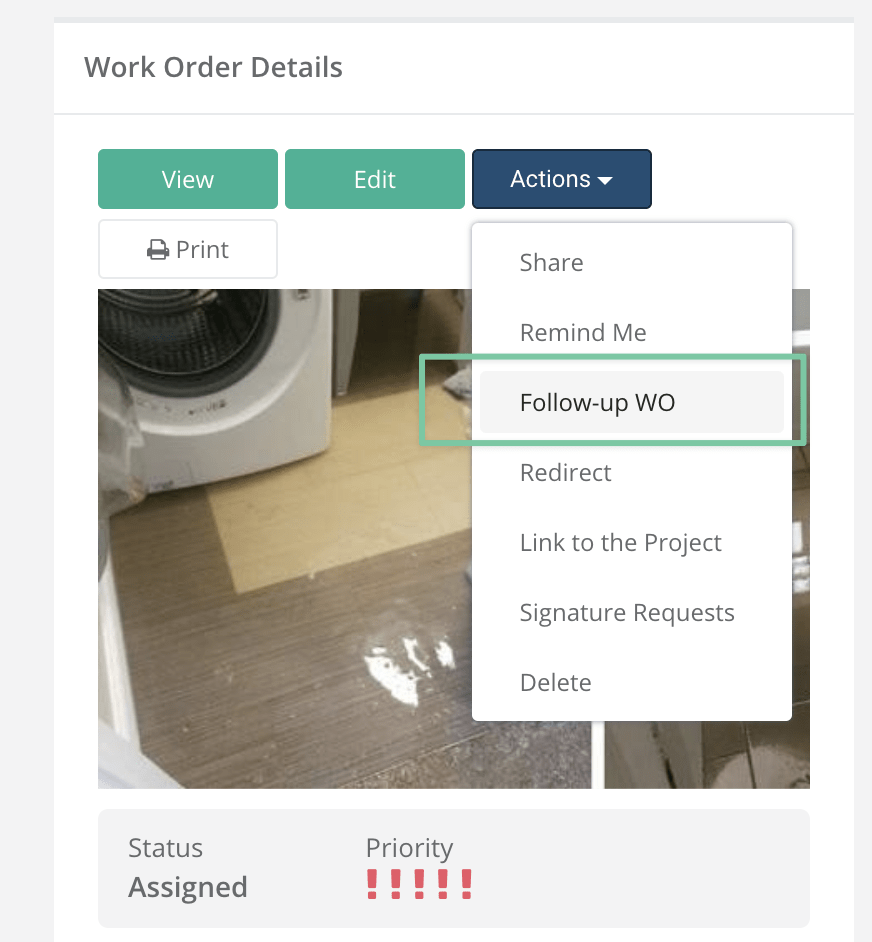
With this neat little function, organizing upkeep activities is all but a hassle.
Lastly, with our task management feature, you can assign and then track the completion of tasks, ensuring everyone is aware of their responsibilities and meets deadlines.
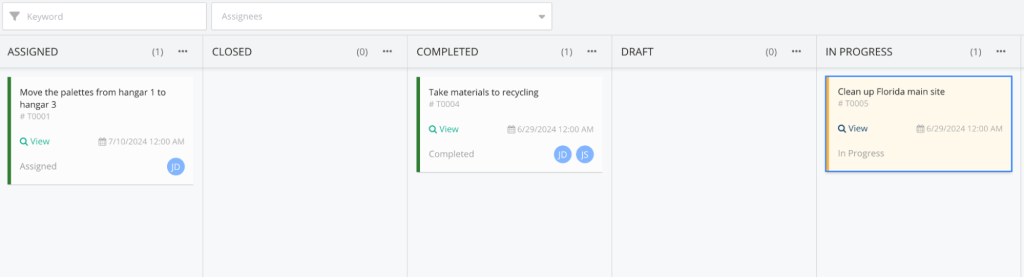
Essentially, wherever you are in your maintenance planning process, WorkTrek has your back.
No matter what tool you choose to use, make sure first to do thorough research, explore all the features, read reviews, and take full advantage of free trials, if offered.
This will help you find the perfect solution for your own unique needs.
Conclusion
Congratulations!
You’re one step closer to a super-efficient maintenance program that ensures your assets stay reliable, your operations run smoothly, and your maintenance costs stay low.
Who knew a maintenance plan could make such a difference?
So get your hands on good maintenance software and start planning today.
You’ll see a huge improvement across your entire operation in no time!