Get a Free WorkTrek Demo
Let's show you how WorkTrek can help you optimize your maintenance operation.
Try for freeIdentifying what needs to be fixed, writing a detailed maintenance plan, and determining which tools or spare parts you need differs from putting this task into a calendar and setting a deadline.
What we just described are, in fact, two very different processes—maintenance planning and maintenance scheduling.
But both are equally important for keeping your assets healthy and your facility running.
However, many people don’t distinguish between the two, which can lead to inefficiencies. After all, when processes are not clearly defined, it becomes challenging to execute them successfully.
So, if you’re unsure about the differences between maintenance planning and scheduling, you’ve come to the right place.
This article will thoroughly explain both processes, highlight their key differences, and show why you need both for efficient maintenance.
Let’s start with the process that comes first.
What Is Maintenance Planning
Maintenance planning ensures you have everything prepared before starting a maintenance task.
This process outlines:
- What tasks must be done and why
- How to perform them
- What parts and tools are required
- Which safety measures must be taken
As well as other necessary information that maintenance technicians should know.
The next logical question is: who does all this maintenance planning?
The answer is: a designated maintenance planner.
Their main job is to create a plan that helps the scheduler prioritize tasks and guides the technician in performing maintenance.
But, for planning to be successful, maintenance planners need a specific set of skills.
First and foremost, they need to understand the details of maintenance work. Which means they should ideally have some experience as technicians.
This hands-on experience helps them know exactly what needs to be done, what tools are required, and how long each task might take so they can estimate time and resources more accurately.
But when that’s not the case, and someone without technical experience takes on the role of a maintenance planner, both maintenance planning and maintenance can quickly become inefficient.
Erik Hupje, an expert in the field, explains what happens when an inexperienced person takes over:
When someone without technical experience fills the role of a planner, they can’t plan the work effectively or eliminate waste from unplanned or poorly planned work. As a result, your team becomes inefficient in the use of resources and there will be increased downtime due to poor planning. This also results in lower team morale and increased frustration due to ineffective communication and organization.
So, the first skill a maintenance planner needs is field experience.
Planners should also communicate well and have great analytical skills to extract meaningful information from older maintenance data.
In the video below, Allan Barry, Senior Consultant at IDCON, a reliability and maintenance management consulting and training company, summarizes these and other necessary skills for maintenance planners.
Take a moment to learn more about the needed skill set:
But apart from devising a maintenance plan, the planner has one more crucial responsibility: ensuring all materials, tools, and spare parts are available when needed.
So, this role also requires specific procurement skills, like ordering parts and materials and communicating with suppliers.
Now that we have explained maintenance planning and who performs it, let’s briefly review the critical steps of the planning process.
According to Don Armstrong from Veleda Services Ltd., consulting and training services for maintenance departments in industrial plants and institutions, there are five crucial steps that every planner must go through.
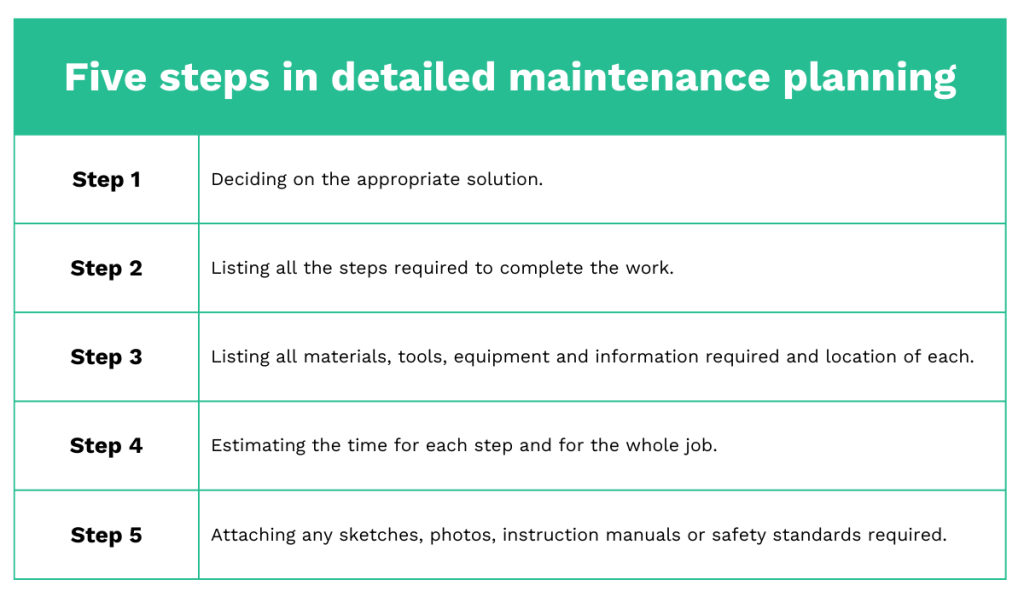
Why should you invest time and effort into such detailed maintenance planning?
Because good maintenance planning can decrease unnecessary delays during jobs.
For example, if a plan ensures a technician has all the necessary tools and materials, the likelihood of disrupted work is much lower.
This increases the technician’s wrench time and improves job performance overall.
Technicians will be grateful for well-planned work.
Tim Newman, Maintenance Manager at Simmons Feed Ingredients, explains the positive impact that implementing maintenance planning had on their technicians:
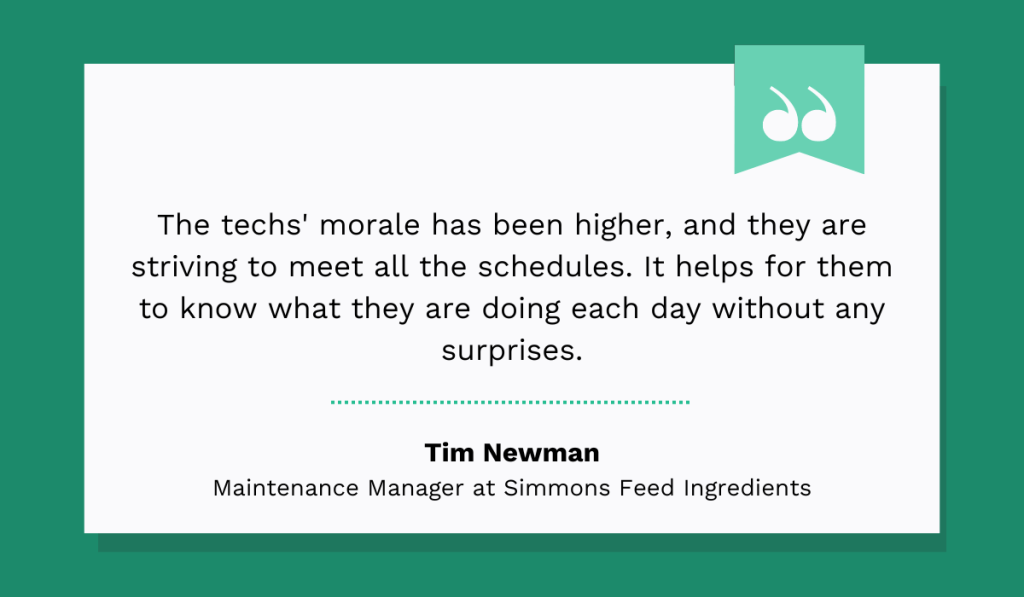
Overall, maintenance planning is all about identifying what needs to be maintained, breaking down tasks that need to be done, managing materials and tools, and ensuring their availability.
When maintenance planning ends, maintenance scheduling begins.
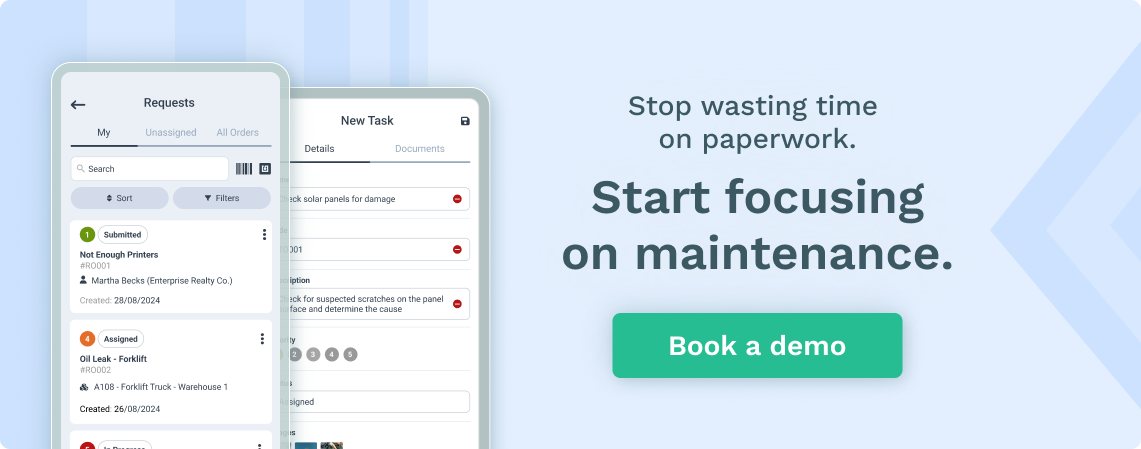
What Is Maintenance Scheduling
Essentially, scheduling means putting the planned tasks into a calendar.
And it revolves around answering two critical questions:
- Who will perform the maintenance?
- When should it be done?
Of course, it’s not that simple. This process requires a great deal of organization.
After all, schedulers have to coordinate all resources required for the job.
This person also has to:
- Prioritize maintenance tasks according to plan.
- Make sure all necessary resources (tools, workers, supplies) are available.
- Ensure the equipment is accessible and ready for maintenance.
- Assign the job to the right technician (with the right skill level).
- Keep track of the job’s progress and address any issues in time.
But who should take on the role of a maintenance scheduler?
According to IDCON, the maintenance supervisor is the most optimal person for scheduling:
This role knows their team and the skill level of each technician. However, as IDCON noted, the problem arises if the supervisor is too busy to do it.
Then, another person may need to take on the scheduler role. But remember that assigning a planner to this role is not ideal.
That’s because planners should focus on planning future tasks and not scheduling the current week’s maintenance.
The ultimate goal is to minimize reactive maintenance so that the supervisor can focus on scheduling planned work and monitoring how it goes.
In any case, the scheduler should follow specific steps when scheduling tasks.
Here they are:
- Review the work order with the maintenance planner to understand the job’s needs, including tools, safety, and expected results.
- Gather all necessary tools, workers, supplies, spare parts, and safety gear needed for the job.
- Assign the task to a qualified technician.
- Ensure the equipment is accessible, safe, and ready for maintenance.
- Monitor the task to ensure it stays on schedule, meets quality standards, and addresses any issues that arise.
Maintenance scheduling optimizes time usage and prevents delays between jobs when done efficiently.
Key Differences Between Maintenance Planning and Scheduling
By now you have learned that maintenance planning and scheduling are two crucial steps in the maintenance process, each with its distinct focus and responsibilities.
Maintenance planning centers on the “what,” “why,” and “how” of maintenance tasks.
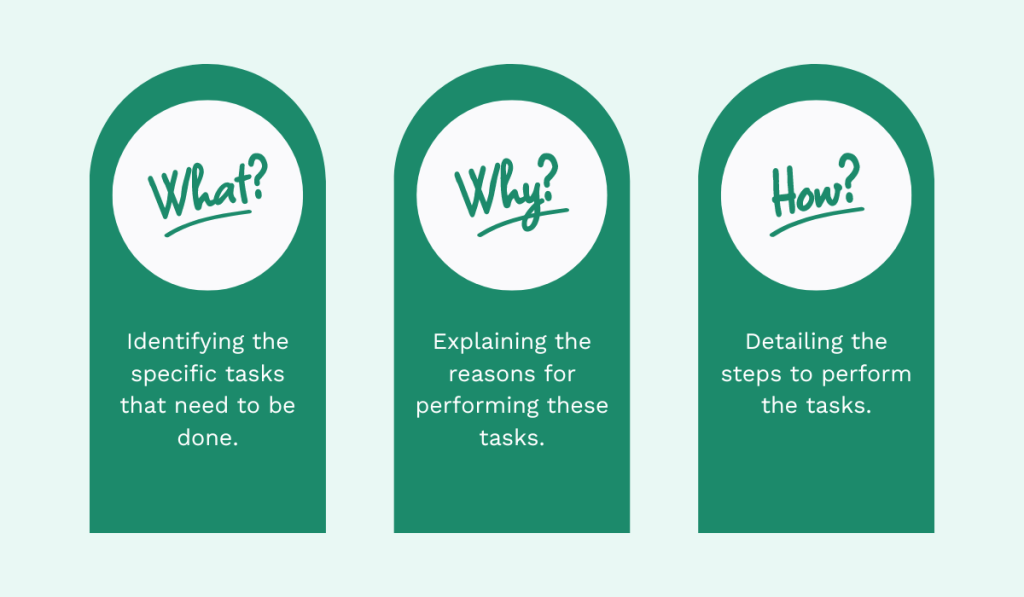
The maintenance planner’s role requires in-depth technical knowledge, experience, and strong analytical skills to estimate time and resources accurately.
On the other hand, maintenance scheduling is concerned with the “when” and the “who.”
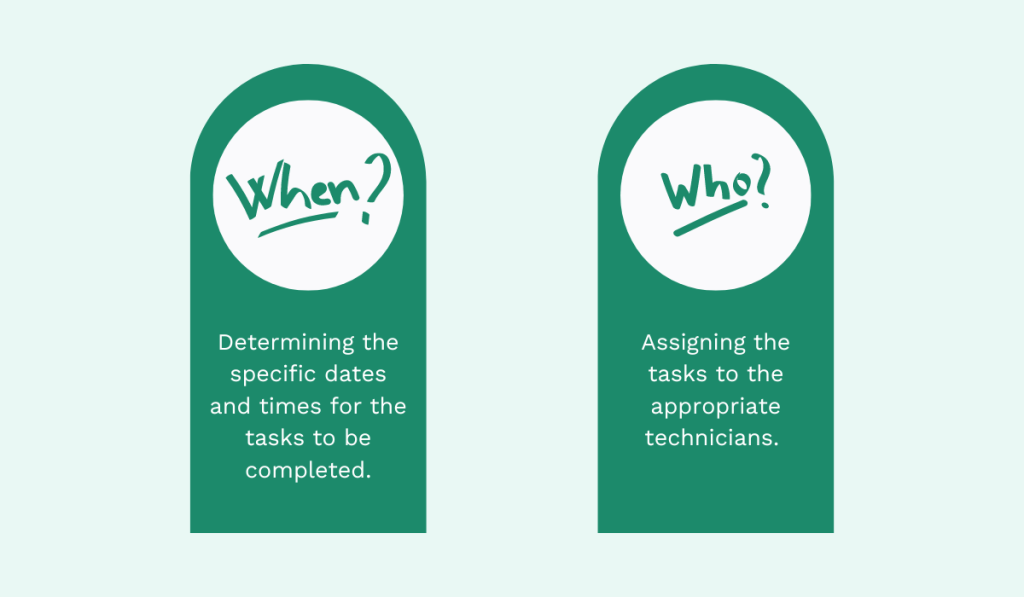
The role of maintenance scheduler requires different skills.
From excellent organizational and coordination skills, and understanding of team capabilities, to managing resources efficiently.
Planning and scheduling are two pieces of a puzzle.
Do You Need Both?
Absolutely, you do!
Maintenance planning and maintenance scheduling work hand-in-hand to transform your maintenance from reactive to proactive.
Here’s why both are essential.
Budget control | Better keeping track of maintenance costs and resources |
Less downtime | Preventing unexpected breakdowns by keeping equipment healthy |
Better productivity | Everyone knows what must be done and has the tools ready |
Better workflows | Tasks are done more efficiently without interruptions |
Both planning and scheduling are key to reducing downtime, boosting productivity, and keeping maintenance costs in check.
The best-in-class facilities, like the Facility Services organization at Raytheon Missile Systems, know this too well.
As their mechanical planner John Lowe (now retired) aptly put it for Reliable Plant:
A well-designed plan, and executing that plan to the schedule, puts us where we want to be.
He also adds that better communication with production and using the right computerized maintenance management system are two key enablers for better planning, scheduling, and, therefore, better maintenance.
And their results show it better than any words could:
- They increased planned work completed to schedule from 25% to 95.3%
- Their breakdowns reduced to 2% of unplanned work orders
However, not all companies have mastered maintenance planning and scheduling.
Many still struggle with it.
In 2019, 17% of companies reported poor scheduling as a key challenge for improving facility maintenance.
But to make matters worse, by 2021, that number jumped to 20%.
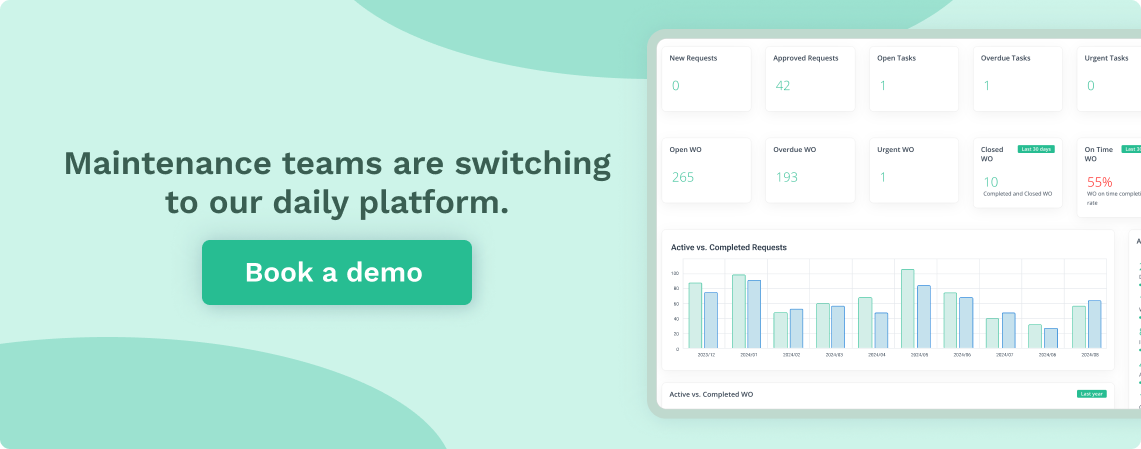
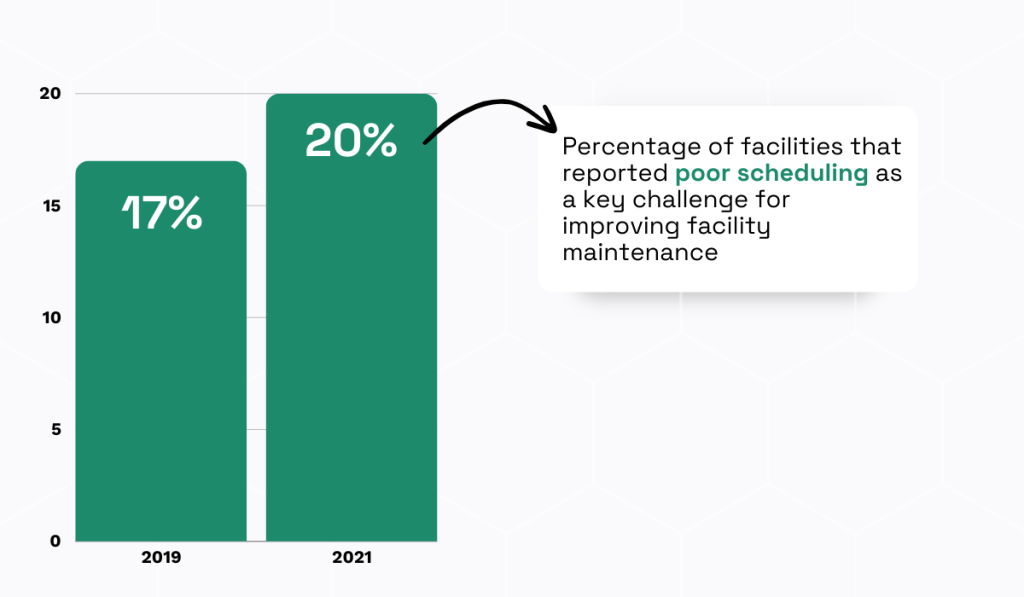
So, why does poor scheduling happen?
Often, bad planning is the culprit. Here’s what can go wrong:
- The plan isn’t detailed enough.
- Time estimates are too short.
- Planners overestimate what technicians can do, especially if they don’t have field experience.
But even with good planning, there can be some scheduling mistakes.
For example, if the scheduler assigns a difficult task to a technician with basic skills, the technician might take much longer to complete the task. This delay can cause the entire schedule to be moved.
Additionally, technicians may have too much idle time if the scheduler assigns too little work and doesn’t fill their schedule.
Such mistakes lead to wasted resources, decreased productivity, higher operational costs, and delays in maintenance.
So, what’s the solution?
To get maintenance right, your planning and scheduling processes must be in sync.
The best way to achieve this is with a computerized maintenance management system like our very own WorkTrek.
With all maintenance data stored in one place, your maintenance planner has a solid ground for planning future maintenance tasks.
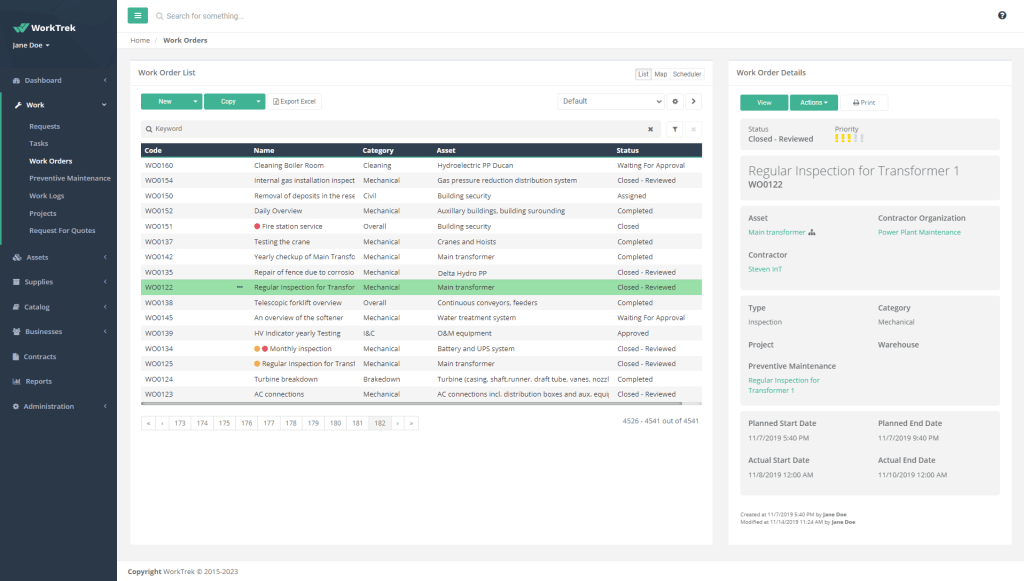
On the other hand, with WorkTrek’s work management features, your scheduler can easily assign maintenance tasks, set urgency levels, and keep track of them all in one scheduling calendar.
Check below how neat and organized such a calendar can be in WorkTrek:

What’s more, WorkTrek also lets you set preventive maintenance tasks on a daily, weekly, monthly, or yearly basis and automatically generate work orders based on meter readings to eliminate costly downtime.
For example, when your meter exceeds a condition you set in the system, WorkTrek automatically creates a work order.
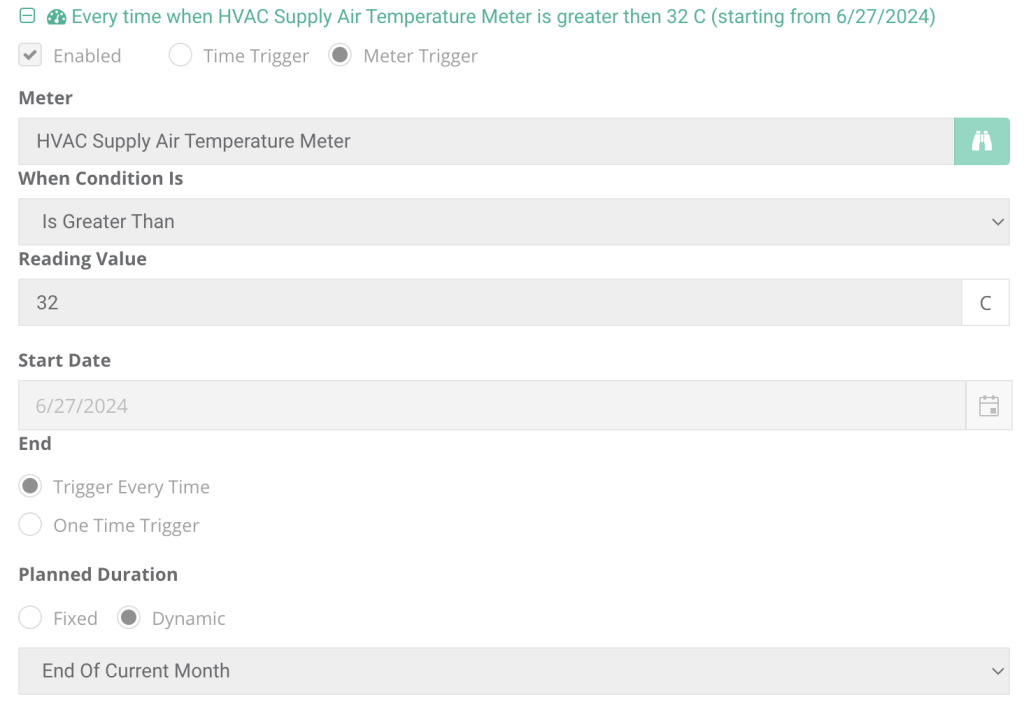
This immediate response helps prevent breakdowns and system failures.
The bottom line is this: technology is your best friend here.
With tools like WorkTrek, maintenance planning and scheduling become more accessible and faster.
And both the planner and the scheduler can perform their jobs better.
Conclusion
With this, we wrap up our exploration of maintenance planning and scheduling.
It’s more than evident that these two processes are different but, at the same time, complement each other.
Effective scheduling relies on robust planning. Without it, tasks will be poorly allocated, leaving technicians unsure of their responsibilities.
On the other hand, detailed planning can falter if scheduling lacks coordination of tools, people, and time, resulting in inefficiencies and downtime.
However, when harmonized, these two processes optimize productivity and ensure efficient maintenance.
Therefore, ensure your maintenance planners and schedulers are on top of their game and equip them with the right CMMS to make their lives easier.
You’ll soon see improvements in your maintenance regime in no time!