Get a Free WorkTrek Demo
Let's show you how WorkTrek can help you optimize your maintenance operation.
Try for freeIf you’re looking for the most detailed guide on the types of maintenance used in manufacturing, you’ve come to the right place.
In this article, you’ll find plenty of information on the different maintenance strategies, including their pros, cons, and when to use them.
By the time you’re done reading, you’ll have all the knowledge needed to create an effective maintenance plan that slashes costs and boosts production uptime.
Let’s get started.
1. Reactive Maintenance
Also known as corrective or run-to-failure maintenance, this is the oldest approach to maintenance.
Let’s explore some of its subtypes.
Breakdown Maintenance
As the name implies, breakdown maintenance involves repairing equipment after it breaks down.
When people talk about reactive maintenance, this is usually what they mean—the two terms are practically synonymous.
However, contrary to popular belief, breakdown upkeep can be both planned and unplanned.
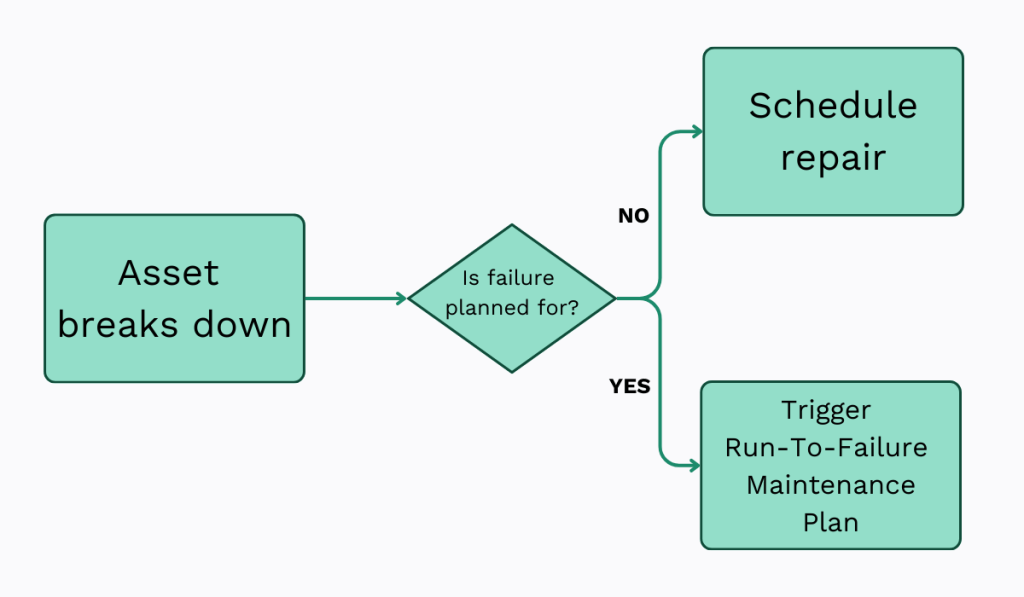
That way, if machinery unexpectedly stops working, the staff at least knows the protocol for repairing it.
Overall, it’s best to use this approach for non-critical or low-cost equipment and assets that are easy and quick to fix.
In that case, the failure doesn’t significantly threaten the operational efficiency or bottom line.
However, in manufacturing, where peak productivity really counts, this is a risky strategy.
Emergency Maintenance
Unlike breakdown maintenance, emergency maintenance is always unplanned.
It deals explicitly with urgent situations involving even critical assets where failure severely impacts safety or operational efficiency.
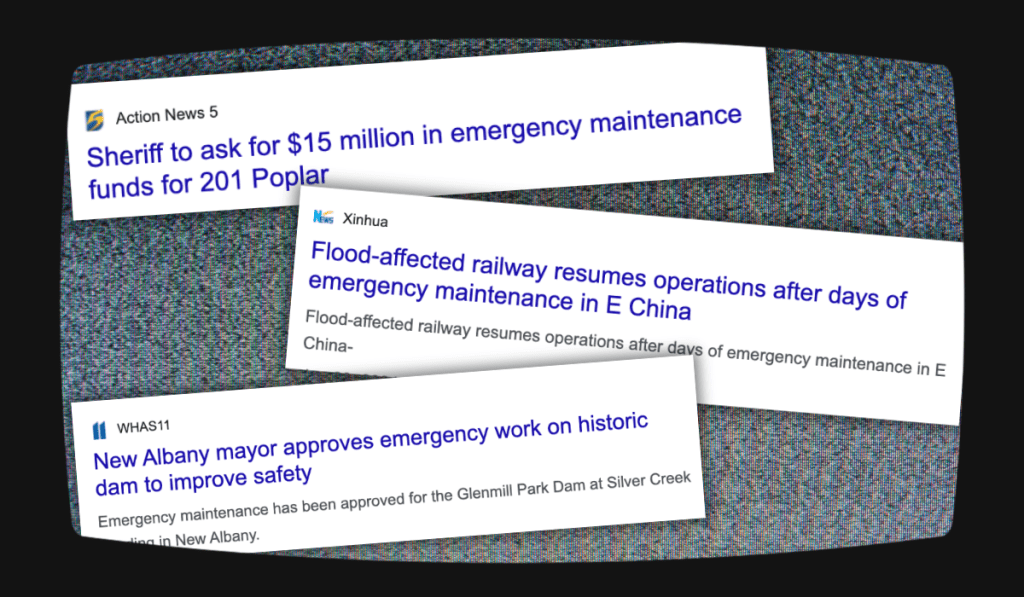
With this type of maintenance, there’s no room for waiting.
While breakdown maintenance might allow for a slower response time, these repairs require immediate action.
This is a worst-case scenario in the manufacturing industry, in which money is lost, time is wasted, and workers’ well-being is endangered.
But the reality is that this industry relies on complex systems, especially in heavy manufacturing, which inherently carry higher risks.
This means emergencies are bound to happen from time to time.
The good news is that the risk can be somewhat minimized with a more proactive approach to maintenance.
2. Proactive Maintenance
Reactive maintenance isn’t enough to keep asset health and production pace where needed.
That’s why various proactive strategies emerged as an answer to this issue.
Preventive Maintenance (PM)
Preventive maintenance schedules checkups and upkeep based on predetermined intervals, regardless of an asset’s actual condition.
It can be either:
Time-based | Scheduled at regular calendar intervals (daily, weekly, monthly, annually) |
Usage-based | Scheduled based on usage metrics (operating hours, mileage, units produced, etc.) |
This is the simplest type of proactive maintenance to plan, schedule, and implement. And in some cases, it can be highly effective.
Research shows that when you mix preventive with predictive maintenance, you can dramatically reduce defects and downtime.
However, due to its straightforward nature, this sort of upkeep is often overused or applied to activities and equipment unsuitable for it.
This can easily lead to over-maintenance.
Therefore, it’s best to use a preventive maintenance program for assets with predictable failure patterns and well-defined wear-out ages.
Or, you could apply it to equipment with low repair costs and low consequences of failure where slight over- or under-maintenance from time to time won’t hurt too much.
Condition-Based Maintenance
Condition-based maintenance monitors equipment health and schedules repairs or inspections only when problems are detected.
Condition-based maintenance is more data-driven than preventive maintenance.
It relies on real-time measurements obtained through visual inspections and other condition-tracking techniques like, for instance, data gathered through various sensors.
This type of maintenance is particularly effective in manufacturing settings, as it allows you to avoid equipment issues without the risk of over-maintenance.
This directly translates to less unnecessary repair costs, more predictable maintenance schedules, and more uptime.
And here’s another reason why condition-based maintenance is so beneficial.
Erik Hupje, Founder & Managing Director at Reliability Academy, a company providing coaching on efficient maintenance, compiled various studies on failure modes and uncovered some interesting findings.
As it turns out, 70-90% of failure modes are not age-related at all, but completely random.
Now, the studies he analyzed are a bit older, but this still is a strong enough indicator that time-based maintenance alone can’t fix everything.
Instead, it’s much smarter to blend it with strategies that focus on the actual condition of your assets.
Predictive Maintenance (PdM)
Predictive maintenance builds upon condition-based maintenance by leveraging advanced techs like AI and IoT to provide even richer information about asset health and predict future issues.
Relying on real-time and historical data from various sources, from sensors to ERP or EAM systems, it can deliver exact insights.
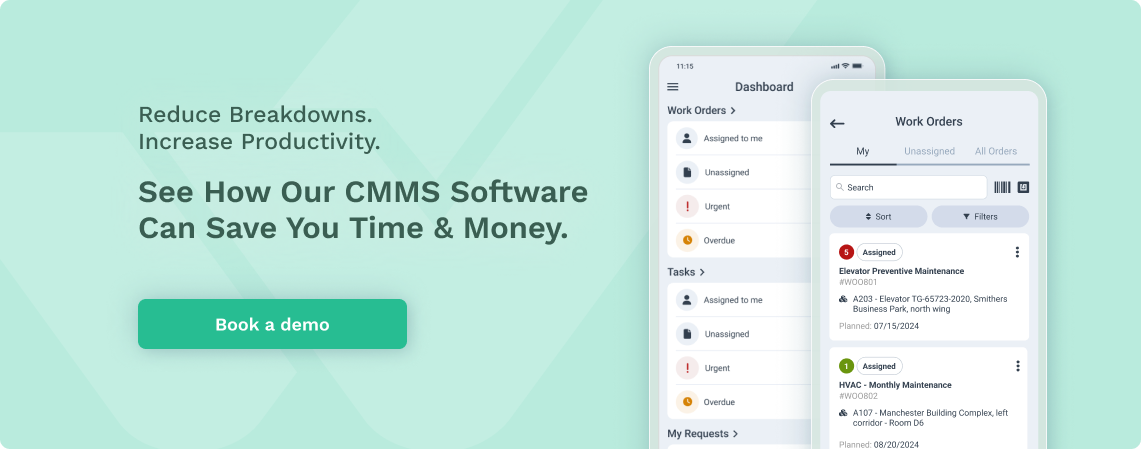
For large-scale manufacturers with rigorous production standards, this is the go-to approach.
Take Toyota, for instance.
A new car rolls off the assembly line every minute in their highly efficient factories. To maintain their production pace, downtime has to be virtually non-existent.
This is where predictive maintenance plays a large role, says their General Manager, Brandon Haight.
Now, for automotive giants like Toyota, this strategy works great.
However, for smaller plants, the upfront investment in technology and the extensive training required to master these systems can be a significant barrier.
That’s why it’s best to perform a thorough cost-effectiveness assessment before rolling out such an advanced system.
Prescriptive Maintenance (RxM)
The most advanced and automated manufacturing environments use prescriptive maintenance.
Like predictive maintenance, it forecasts when and where equipment service is needed, but it doesn’t stop there.
Instead, it suggests specific upkeep activities and operational adjustments to optimize performance.
Prescriptive maintenance represents the fifth and final stage in the maintenance maturity timeline.
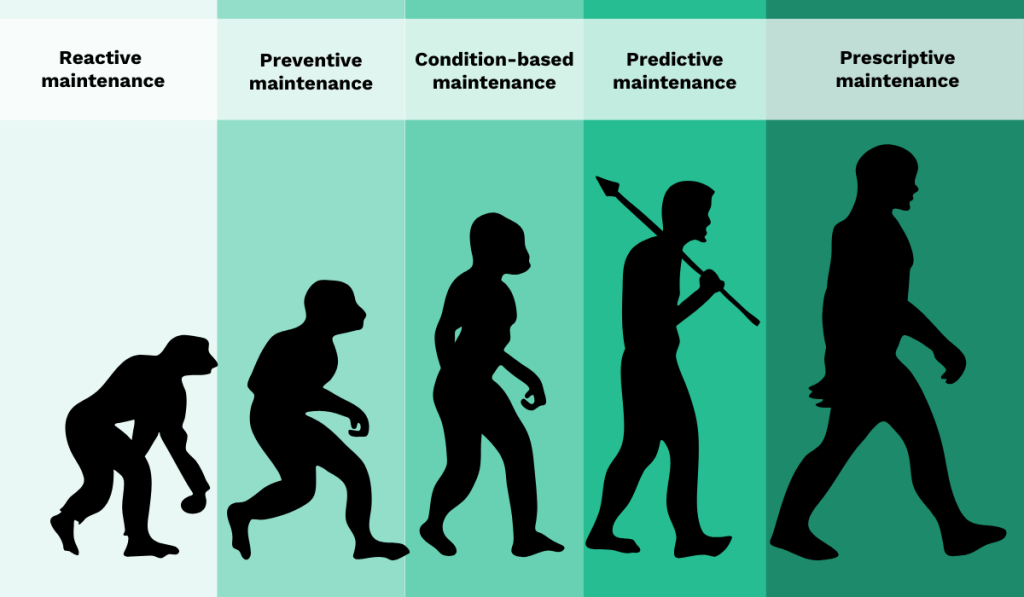
In other words, this is the most advanced approach to maintenance currently available.
As such, it’s best suited for assets with very complex failure modes and those absolutely critical for operational efficiency and safety.
While this technology is still in its infancy and slowly making its way into manufacturing, there’s no doubt it’s the next big step toward maximizing equipment reliability and effectiveness.
Right now, it may seem still a bit futuristic, but it could soon become the norm.
Reliability-Centered Maintenance (RCM)
Reliability-Centered Maintenance (RCM) focuses on critical assets and evaluates the consequences of their failure.
Based on these evaluations, it identifies potential issues that may compromise functionality and prescribes the appropriate type of upkeep for each asset to ensure reliable performance.
This could mean continuous real-time monitoring, periodic inspections, or waiting until the asset breaks down.
It all depends on how vital they are for the operations.
The assessment criteria for RCM are commonly known as the “7 Questions of RCM”:
- What are the functions and desired performance standards of each asset?
- How can each asset fail to fulfill its functions?
- What are the failure modes for each functional failure?
- What causes each failure mode?
- What are the consequences of each failure?
- What actions can be taken to predict or prevent each failure?
- What should be done if a suitable proactive task cannot be determined?
This strategy is beneficial for large-scale operations because it helps prioritize based on asset reliability and criticality.
Instead of spreading resources thin across all equipment, RCM lets you focus on the most important assets first, ensuring maximum equipment uptime and cost-effectiveness of your maintenance program.
Risk-Based Maintenance (RBM)
Risk-Based Maintenance (RBM) prioritizes assets with the highest risks if they fail.
It operates based on the following framework:
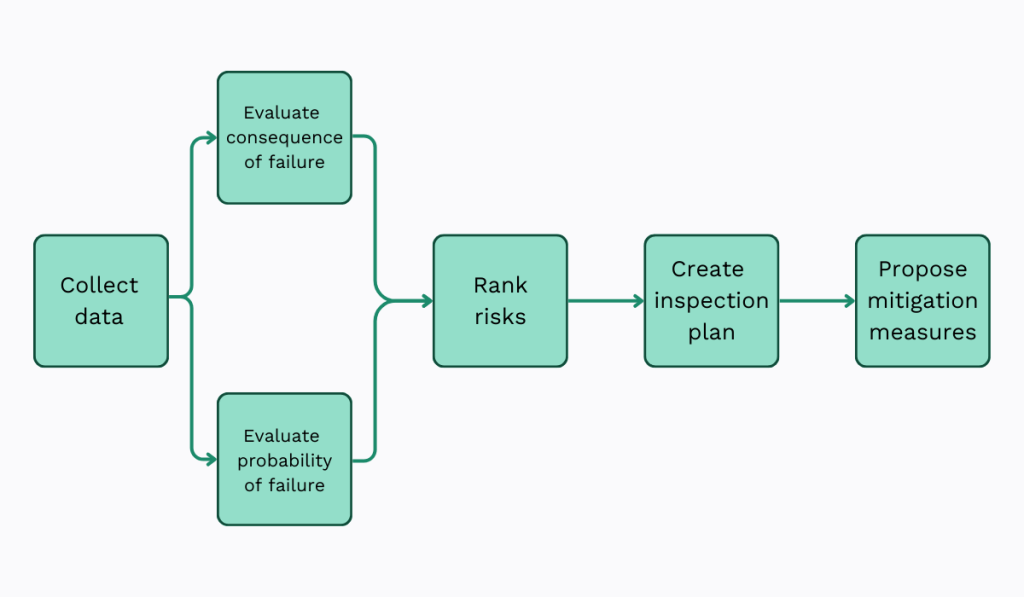
The process begins by analyzing potential risks, ranking them according to their impact and likelihood, and then developing a maintenance plan to mitigate those issues.
RBM is similar to RCM in that both approaches help prioritize and empower you to allocate resources more strategically.
However, they differ in their core focus.
While RCM zeros in on maintaining functionality, RBM minimizes risk front and center.
Sure, these two concepts might be somewhat interconnected, but they are not the same.
For example, replacing an air compressor on an asset may increase its output (an RCM concern), but the risk of a leak remains unchanged (an RBM concern).
Moreover, RCM starts by assessing only critical assets, while RBM evaluates all assets and then determines which ones should be prioritized.
Ultimately, both methods can benefit manufacturing, depending on available resources, asset portfolio, and company objectives.
Generally, RBM is more suitable for significant safety risks, whereas RCM is preferred when maximizing productivity is the primary goal.
3. Other Maintenance Types
There are several other types of maintenance that can’t be strictly categorized as either reactive or proactive. Let’s see what they are.
Autonomous Maintenance
Autonomous maintenance assigns the responsibility of performing basic service tasks, like lubrication, cleaning, and safety checks, to the primary users of equipment—the operators.
This frees up dedicated maintenance personnel to focus on more complex activities while providing operators with greater ownership and responsibility.
As a result, overall upkeep effectiveness is improved, as issues are identified more quickly and all assets receive the needed attention.
Autonomous maintenance is one of the pillars of Total Productive Maintenance (TPM), an approach developed in Japan in the 1960s.
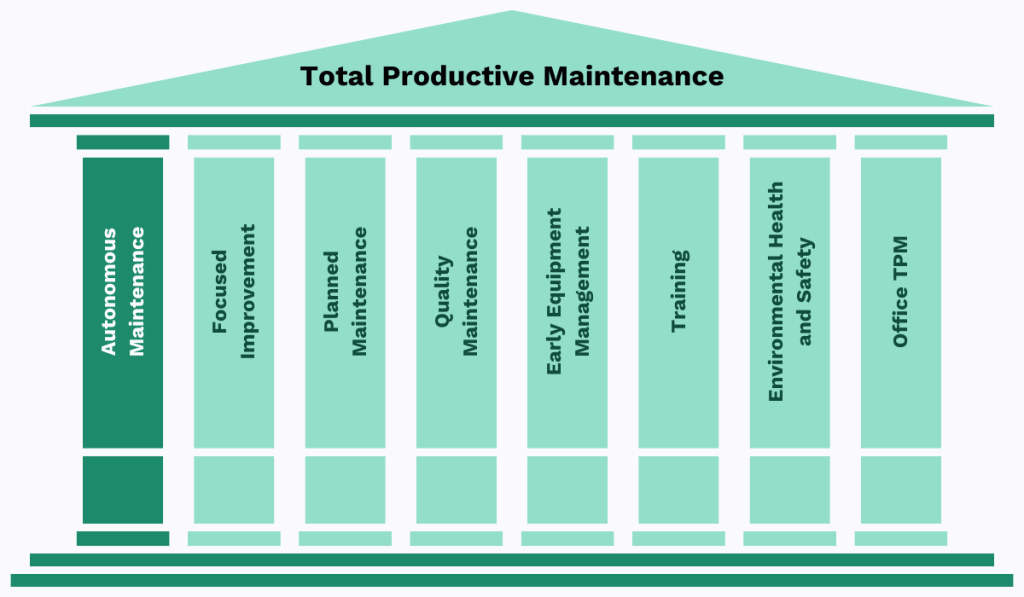
With its main goal of optimizing equipment performance as much as possible, it’s a foundational element of many lean manufacturing environments.
Although it requires an initial investment of resources and effort for training and cultural adaptation, autonomous maintenance can significantly reduce downtime and help maintain operational efficiency.
It also creates a more engaged workforce that’s invested in the factory’s success.
Deferred Maintenance
Also referred to as backlog or demand maintenance, deferred maintenance is essentially equipment service that has been postponed.
This can be either unplanned or strategic, occurring for various reasons such as:
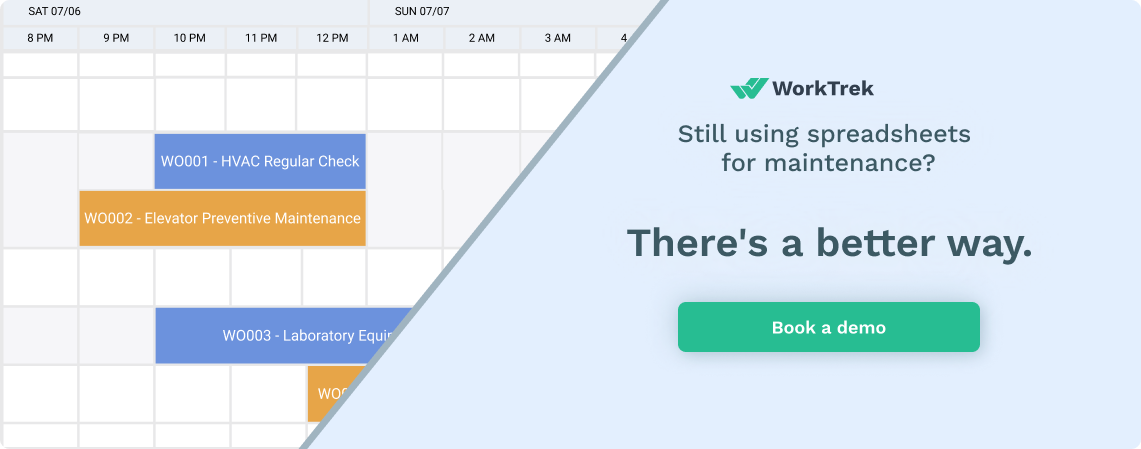
- cost control
- equipment inaccessibility
- company policies
- lack of priority
- parts unavailability
While deferring maintenance can help budget adherence and prevent staff from overworking, it often causes more harm than good in the long run.
As we’ve already explained, neglecting regular asset upkeep can lead to more unplanned downtime and higher repair costs.
Nevertheless, sometimes deferred maintenance is unavoidable.
The trick is to be smart about it.
Consider borrowing principles from RCM or RBM and perform risk analyses on your assets to determine where this kind of upkeep can be safely applied.
This task can be a breeze if you’re using a Computerized Maintenance Management System (CMMS) like WorkTrek.
WorkTrek provides instant access to all your asset data, work order histories, service requests, and other relevant documentation for minor repairs and major maintenance activities.
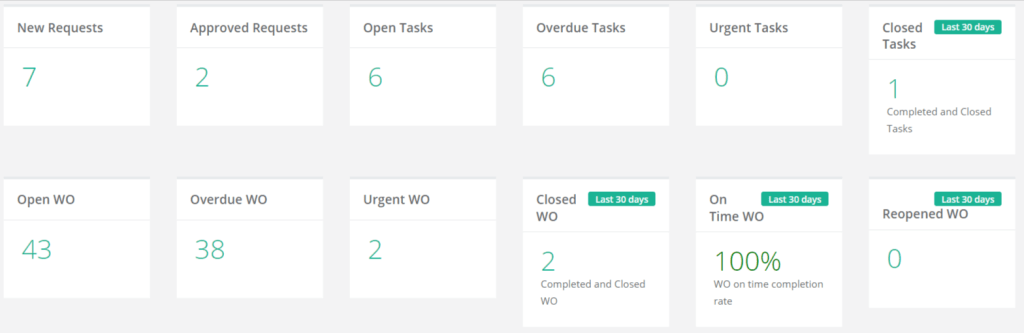
It tracks who performed what work, when, how long it took, and which resources were used.
WorkTrek also offers a wide range of reports, such as work hours summaries, rates of overdue work orders, asset warranty trackers, and more.
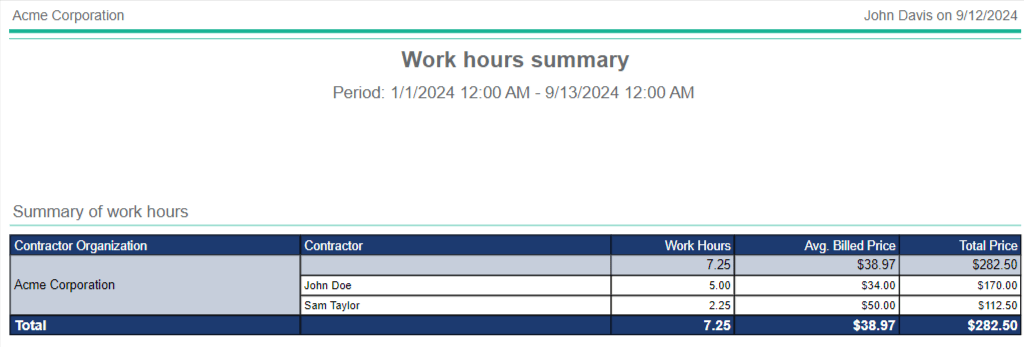
All of that empowers you to see the big picture at a glance, which can help you gauge the long-term risks of delaying certain tasks.
For instance, you might learn more about the financial implications of deferred maintenance by calculating the potential costs of breakdowns versus the cost of immediate repairs.
All in all, there is a time and place for deferred maintenance, especially when the budget is tight.
However, make sure to understand the risks before making that call.
Shutdown Maintenance
Unlike other types, shutdown maintenance involves a halt of entire, or at least a portion of, plant operations.
This is maintenance on a grand scale, encompassing multiple assets and lasting for days or even weeks.
Yes, shutting down operations can be costly and disruptive, but it’s a necessary investment in your equipment’s long-term health and reliability.
To minimize the effect of such an operational disruption, careful planning and smart scheduling are a must.
Shutdowns are usually timed to have minimal impact on key workflows, like during off-peak periods or at the end of a production cycle.
And checklists, like the one you see below, are typically used for planning.
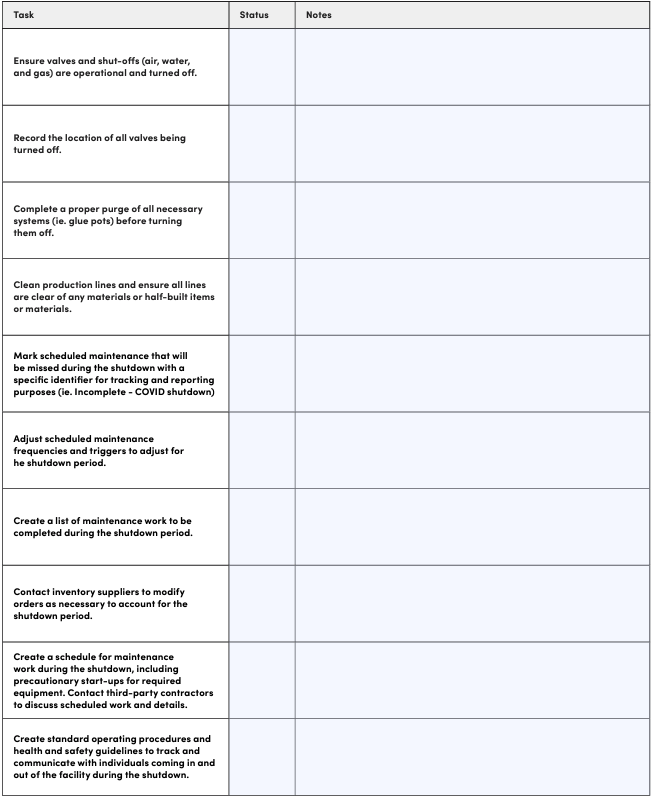
They help ensure all the steps are completed correctly and nothing slips through the cracks.
The last thing you want here is to forget to perform a key task.
Ultimately, with the right preparation and coordination, this type of maintenance, although often dreaded in manufacturing, doesn’t have to be a headache at all.
Conclusion
Each of these maintenance types has its unique benefits.
But, which one’s the best?
Unfortunately, there’s no simple answer to that question.
The most effective maintenance plans don’t rely on just one approach but often blend multiple strategies to get the best results.
For non-critical assets, reactive maintenance might do the trick.
However, you need to be more vigilant and proactive when it comes to vital equipment.
So, assess your equipment’s reliability and criticality, understand the risks involved, and prioritize accordingly.
With the right asset care, you’ll see immediate improvements in your bottom line, productivity, and safety.
If you’re ready to choose the right maintenance strategy, follow this process.