Get a Free WorkTrek Demo
Let's show you how WorkTrek can help you optimize your maintenance operation.
Try for freeWhat is Operation and maintenance?
Operation and maintenance (O&M) refers to the comprehensive set of activities, procedures, and resources required to keep a system, facility, or equipment functioning effectively and efficiently throughout its intended lifecycle.
This encompasses the day-to-day running of the asset (operation) and the systematic care and upkeep needed to prevent deterioration and ensure reliable performance (maintenance).
Effective facility management is integral to O&M. It includes routine tasks, compliance with safety standards, and the coordination of maintenance activities to optimize the management of physical assets.
The operation component involves managing and controlling the system or facility to deliver its intended function. This includes monitoring performance metrics, adjusting operational parameters, supervising automated processes, and ensuring compliance with safety and regulatory requirements.
Think of it like driving and controlling a car – you must steer, accelerate, brake, and respond to changing conditions.
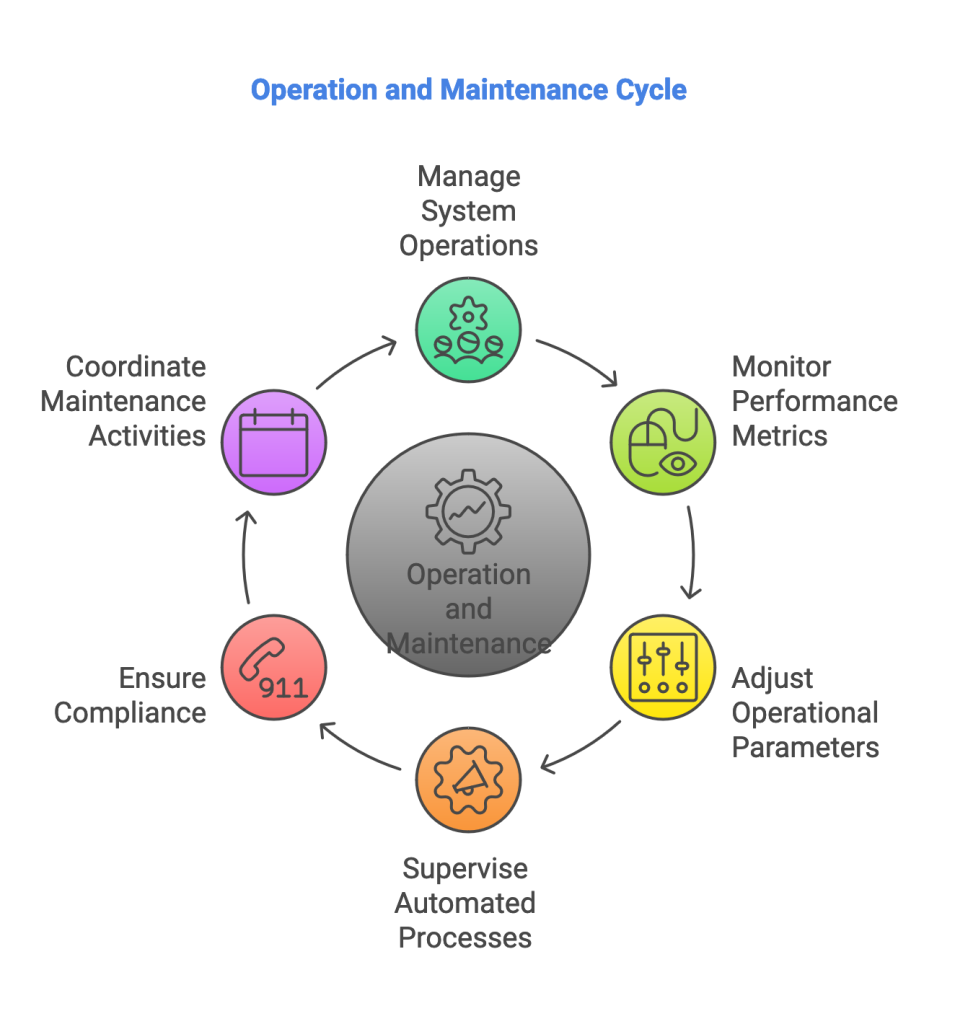
Definition and Overview
Operations and Maintenance (O&M) is a comprehensive approach to managing and maintaining physical assets, facilities, and equipment. It encompasses various activities, including routine cleaning and inspection, minor repairs, safety and compliance measures, inventory and spare parts management, and preventive maintenance.
O&M is a proactive maintenance strategy that aims to reduce unexpected equipment failure, prolong asset life, and ensure technicians, operators, and contractors can work efficiently.
Approaches to O&M
The maintenance aspect can be broken down into several key approaches within maintenance programs:
- Preventive maintenance (scheduled upkeep to prevent failures),
- Corrective maintenance (fixing problems after they occur),
- Predictive maintenance (using data to anticipate and prevent failures)
- Condition-based maintenance (performing maintenance based on the actual state of the equipment).
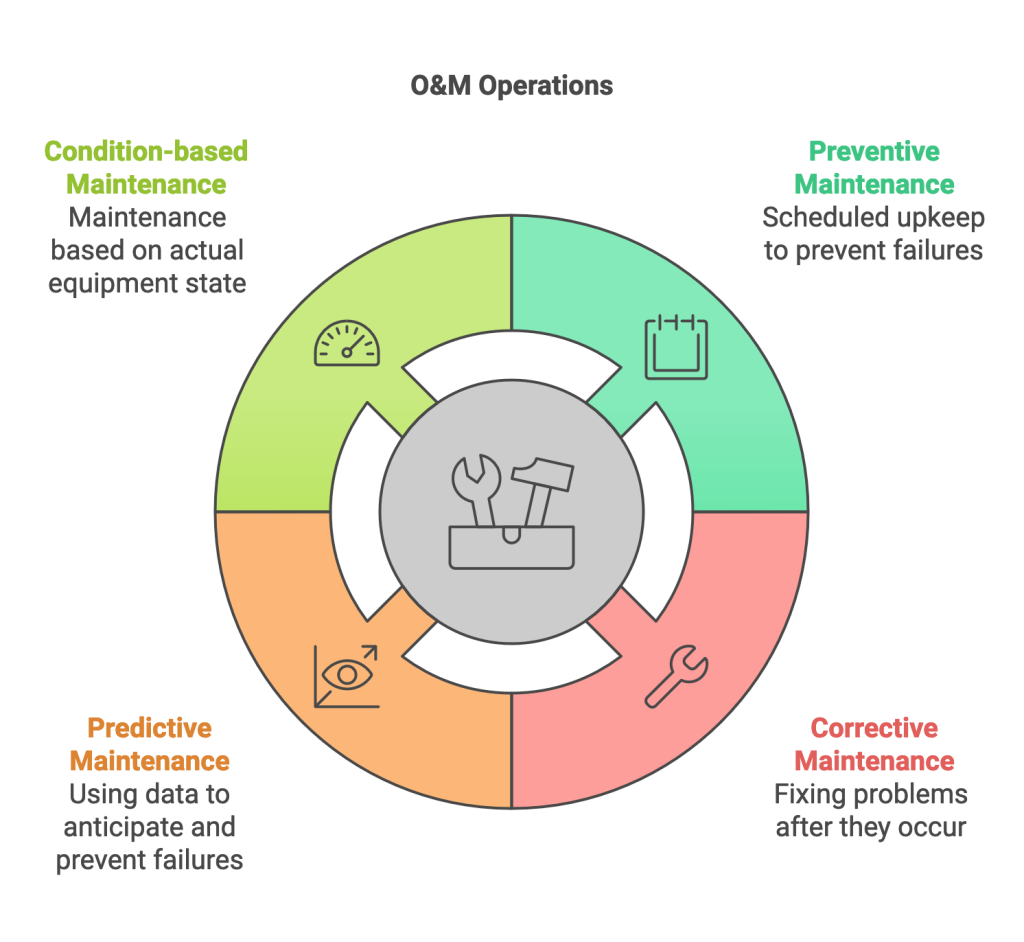
This is analogous to how we maintain our health through regular check-ups:
- Preventive – treat illnesses when they occur
- Corrective – monitor health markers to catch problems early
- Predictive – address specific issues as they arise (condition-based).
O&M requires careful planning, skilled personnel, appropriate tools and equipment, detailed documentation, and often sophisticated management systems.
For example, a modern manufacturing facility might use computerized maintenance management systems (CMMS) like WorkTrek to schedule maintenance tasks, track spare parts inventory, and document repair histories.
The scope of O&M can vary significantly depending on the context. For example, a small HVAC system might require regular filter changes and annual inspections.
For a nuclear power plant, it encompasses complex procedures, extensive safety protocols, and continuous monitoring of critical systems.
Goals of an O&M Program
The primary goals of an O&M program are to:
- Optimize asset management and performance
- Ensure operational efficiency and productivity
- Support all aspects of facility maintenance with documentation and detailed reference material
- Reduce downtime and increase productivity
- Improve quality control and safety
- Extend asset life and reduce maintenance costs
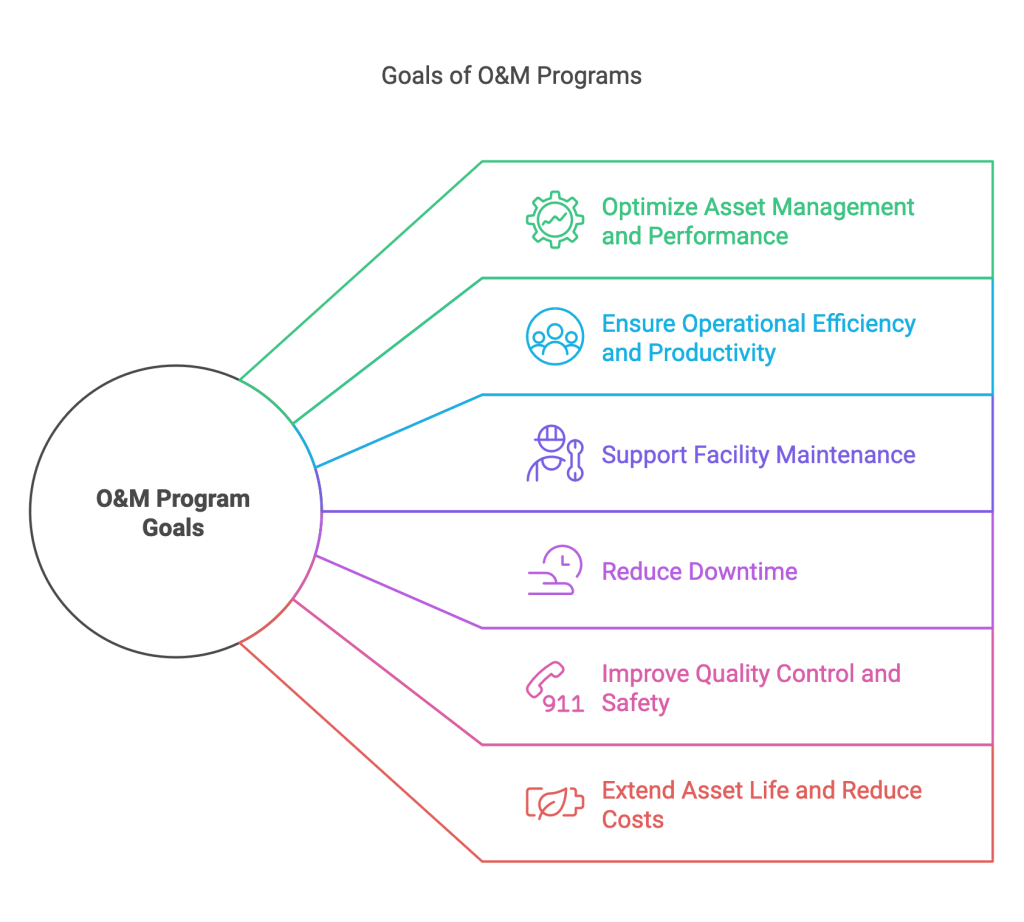
Importance of O&M
Effective operations and maintenance management (O&M) is important for several reasons:
- It maximizes asset reliability and availability,
- Extends equipment lifetime,
- Ensures safety,
- Optimizes performance,
- Reduces operating costs,
- Minimizes unexpected breakdowns.
Poor O&M practices can lead to increased downtime, higher repair costs, reduced efficiency, and potentially catastrophic failures.
Modern O&M practices increasingly incorporate digital technologies like IoT sensors, artificial intelligence, and digital twins, enabling more precise monitoring and proactive maintenance strategies.
This evolution represents a shift from traditional time-based maintenance to more sophisticated, data-driven approaches that can predict and prevent failures before they occur.
Operations and Maintenance Manual
An Operations and Maintenance (O&M) manual is a comprehensive document that contains detailed instructions and guidelines for managing and maintaining a facility, asset, or property.
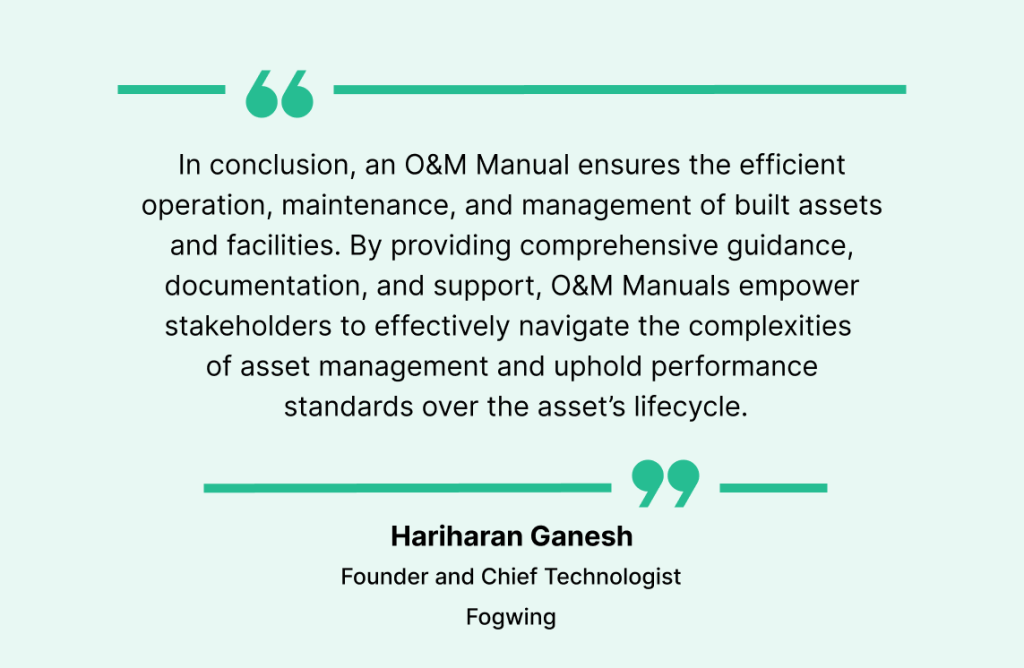
It is a centralized resource for operations and maintenance personnel, providing essential information on operating, maintaining, troubleshooting, and managing a given asset effectively and optimally.
Improve O&M Using CMMS
A Computerized Maintenance Management System (CMMS) such as WorkTrek, can transform and enhance an operations and maintenance program (O&M) in several significant ways. Let’s explore how these systems create value across different aspects of O&M management.
Work Order Management and Automation
Operations and maintenance programs (O&M) are essential for ensuring operational efficiency and asset longevity. CMMS platforms streamline the entire work order lifecycle, from creation to completion. When equipment needs maintenance, the system can automatically generate work orders based on predetermined triggers, such as runtime hours or calendar schedules.
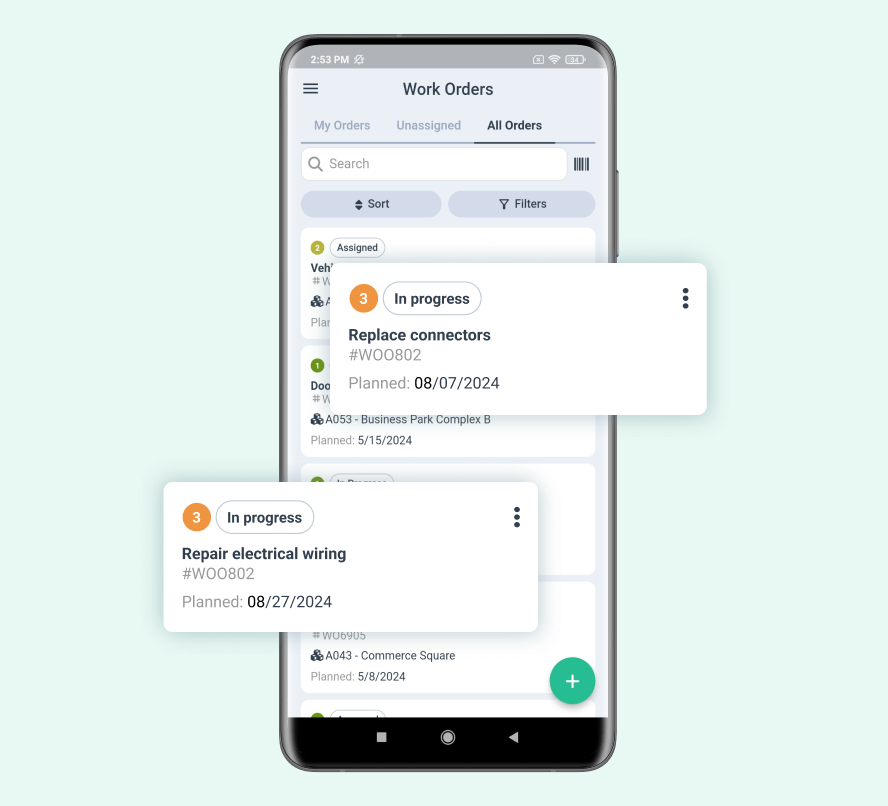
For instance, if an industrial pump reaches 1,000 operating hours, the CMMS can create a work order for inspection and preventive maintenance without human intervention.
This automation reduces delays between problem identification and resolution while ensuring no maintenance tasks fall through the cracks.
Asset Management, Lifecycle Tracking, and History
Think of CMMS as creating a detailed medical record for each piece of equipment. Every maintenance action, repair, modification, and inspection is logged with timestamps, technician information, and detailed notes.
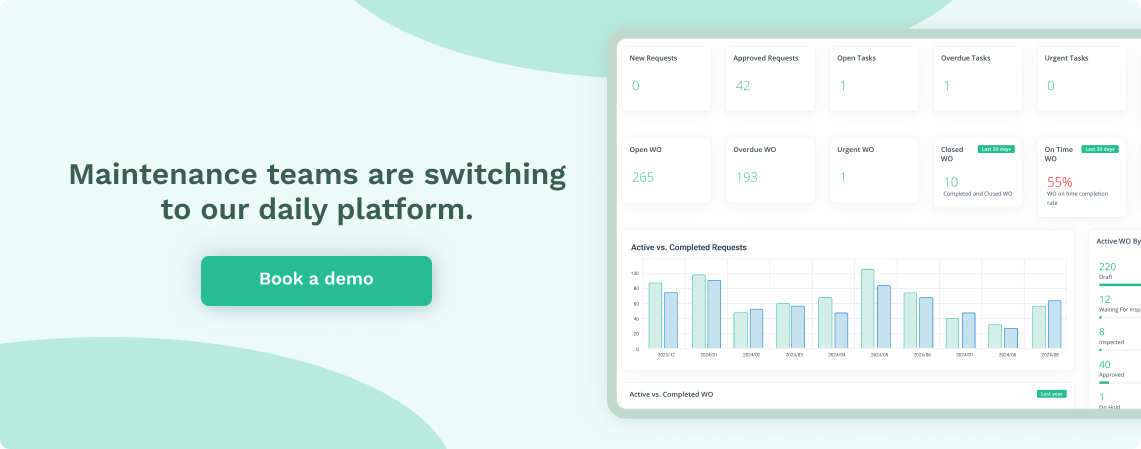
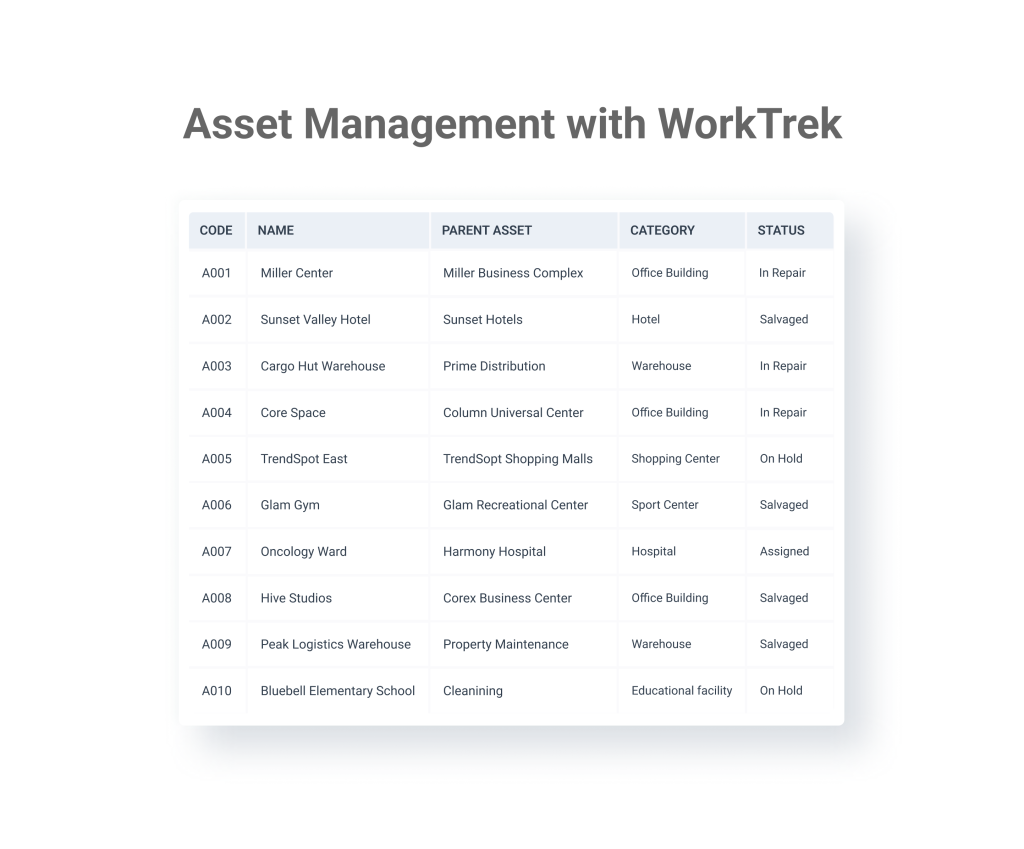
This comprehensive history serves multiple purposes: technicians can review past issues when troubleshooting problems, managers can identify recurring issues that might indicate a need for equipment replacement, and organizations can make data-driven decisions about asset lifecycle management.
For example, if a motor shows increasing repair frequency and costs over time, the CMMS data can justify and inform replacement timing.
Inventory Management and Resource Optimization
CMMS sophisticatedly manages spare parts and materials. The system tracks inventory levels, automatically triggers reorder points, and links parts to specific equipment and maintenance procedures.
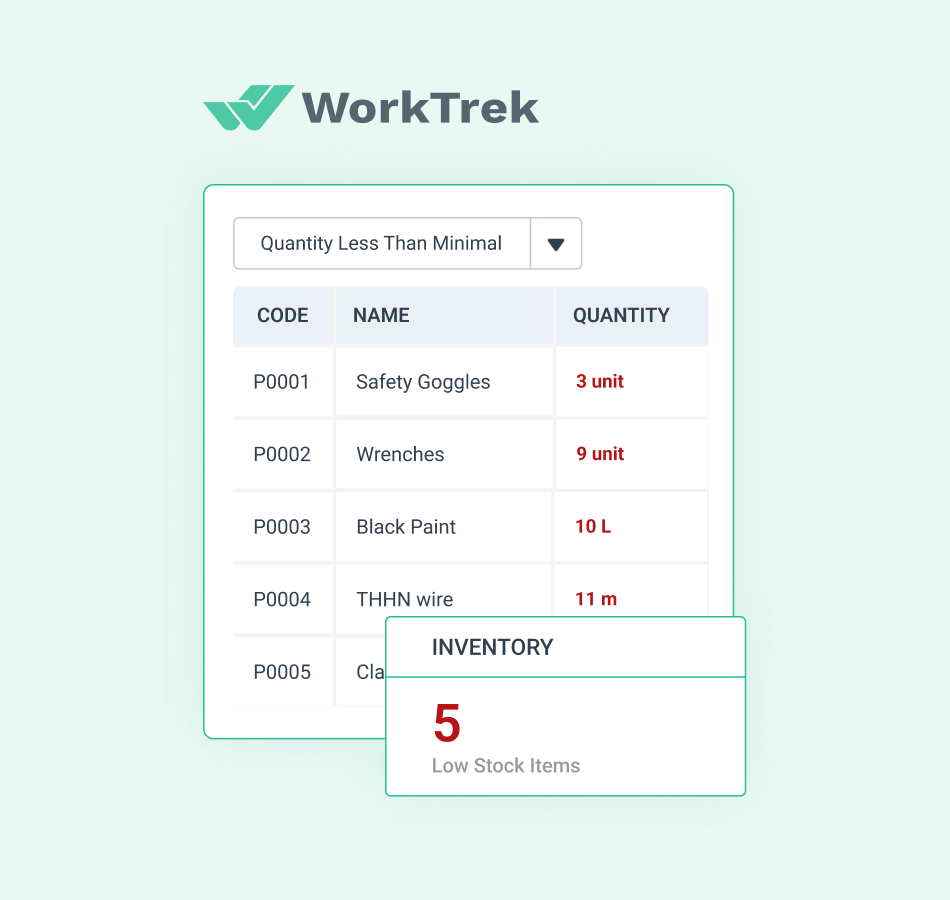
This integration prevents maintenance delays due to missing parts and reduces carrying costs from excess inventory. Consider a manufacturing facility that maintains critical spare parts for production equipment – the CMMS can ensure optimal stock levels based on usage patterns, lead times, and criticality of the equipment.
Preventive Maintenance Scheduling
Rather than reactive maintenance, CMMS enables systematic preventive maintenance planning. The system can schedule maintenance tasks based on multiple parameters: calendar time, equipment runtime, production cycles, or even environmental conditions.
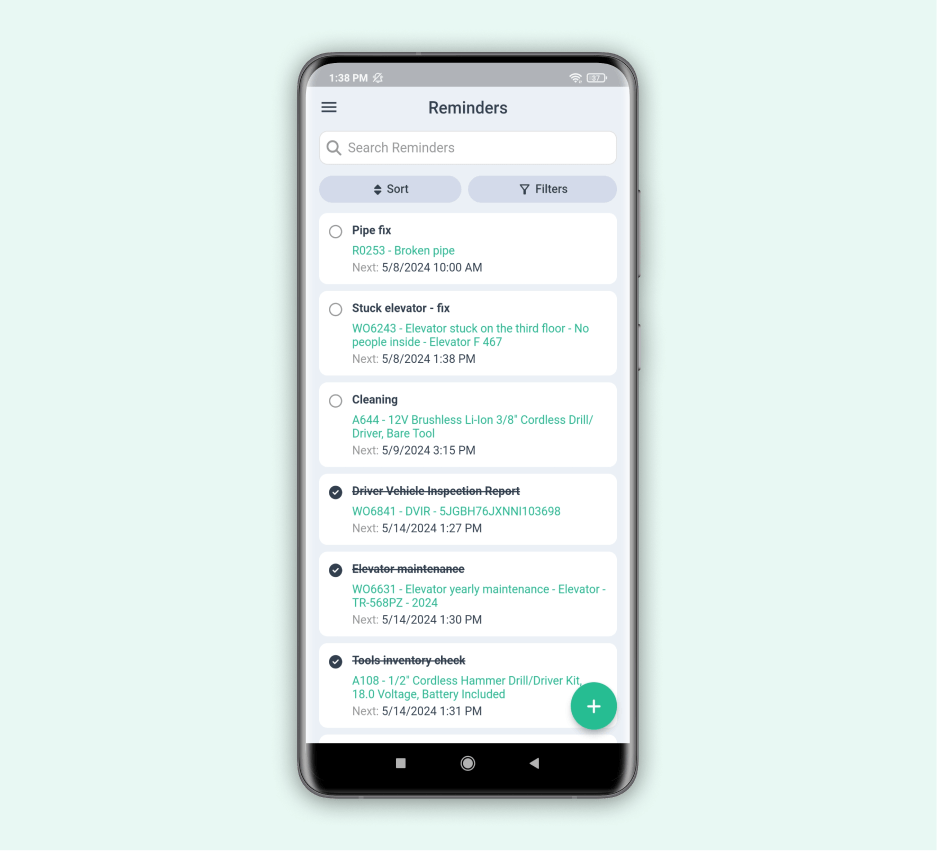
This structured approach helps organizations move from a reactive “fix it when it breaks” mindset to a proactive maintenance strategy that prevents failures before they occur.
For example, a CMMS might coordinate the scheduling of related maintenance tasks to minimize production downtime.
Performance Analysis and Reporting
CMMS provides powerful analytical capabilities by converting maintenance data into actionable insights. The system can generate reports on key performance indicators like equipment reliability, maintenance costs, labor utilization, and mean time between failures.
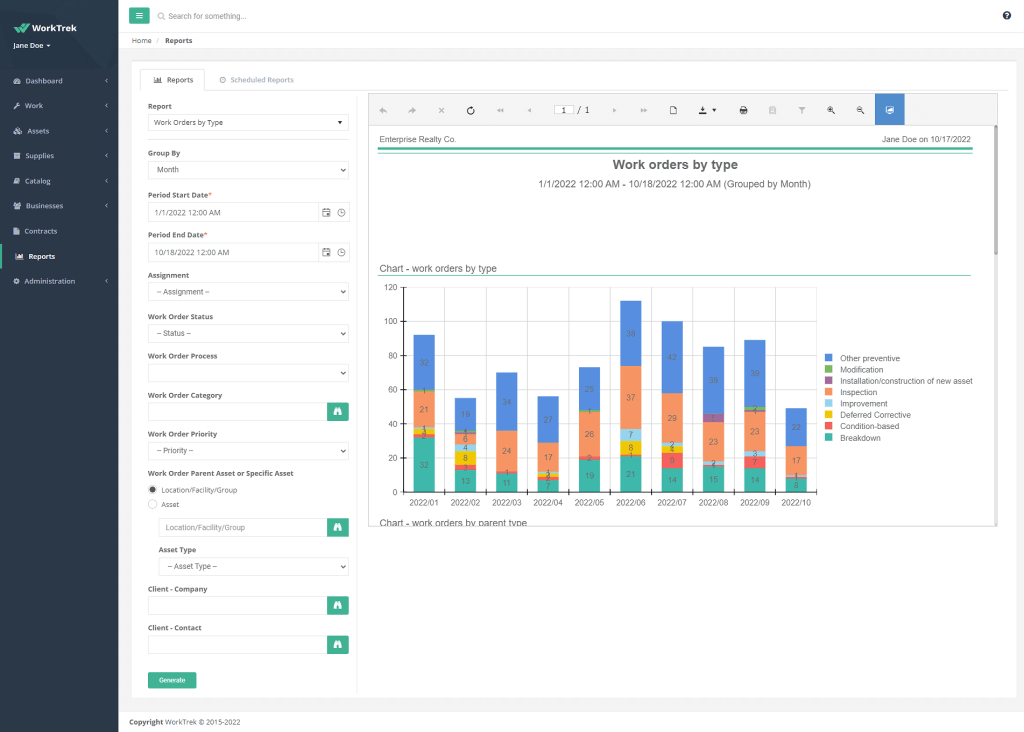
These metrics help organizations identify trends, optimize maintenance strategies, and make informed decisions about resource allocation. For instance, analyzing labor hours across different types of equipment can reveal which assets require the most maintenance attention and guide staffing decisions.
Compliance and Documentation
CMMS is a crucial tool for maintaining compliance records in regulated industries. The system can automatically document maintenance activities, store certificates, track calibration requirements, and generate compliance reports.
This systematic record-keeping is particularly valuable during audits or inspections. For example, a healthcare facility can use CMMS to demonstrate consistent maintenance of critical medical equipment by regulatory requirements.
Mobile Access and Real-Time Updates
Modern CMMS platforms typically offer mobile capabilities, allowing technicians to access and update maintenance information from the field.
This real-time connectivity improves efficiency by eliminating paper-based processes and reducing administrative overhead. Technicians can access equipment manuals, maintenance procedures, and historical data while working on equipment, and they can immediately update work order status and document their actions through mobile devices.
Integration with Other Systems
CMMS can integrate with other enterprise systems, such as Enterprise Resource Planning (ERP), Building Management Systems (BMS), or Industrial Internet of Things (IIoT) platforms, to create a more comprehensive operational picture.
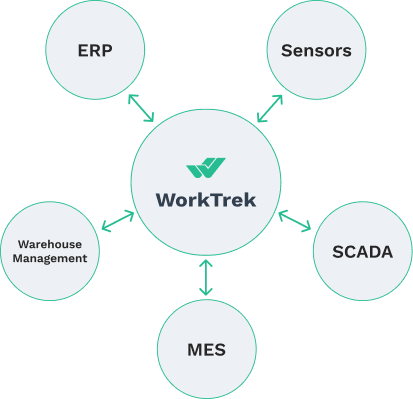
For example, when connected to IoT sensors, the CMMS can receive real-time equipment performance data and automatically trigger maintenance actions based on actual operating conditions rather than fixed schedules.
These capabilities can improve maintenance efficiency, asset reliability, and operational performance.
The key is to view CMMS as a digital tool enabler of more sophisticated and effective maintenance management practices.
Common Misconceptions about Operation and Maintenance
Common Misconceptions: The most prevalent misconceptions about O&M include:
- “Operation” and “maintenance” are separate functions that can be managed independently. In reality, these functions are deeply interconnected. How a system is operated directly impacts its maintenance needs, and maintenance practices affect operational capabilities.
- Second Misconception: O&M is purely reactive. Modern O&M incorporates predictive and preventive strategies to optimize system performance and prevent failures before they occur.
- O&M costs are fixed overhead expenses. However, they can be strategically managed through proper planning, condition monitoring, and optimization of operational practices.
Scientific and Engineering Principals of O&M
Let me explain the core scientific and engineering principles that underpin Operation and Maintenance, including how that asset functions. These principles draw from multiple disciplines and help us understand why O&M practices work the way they do.
Thermodynamics and Energy Systems
At its heart, O&M deals heavily with the laws of thermodynamics. Every piece of equipment or system loses efficiency over time due to the Second Law of Thermodynamics, which states that entropy (disorder) in a system always increases. This fundamental principle explains why:
- Equipment naturally degrades over time
- Friction leads to wear in moving parts
- Energy efficiency decreases without proper maintenance
- Heat dissipation must be managed in operational systems
Materials Science and Degradation
The behavior of materials under stress and environmental conditions forms another crucial scientific foundation. Understanding these principles helps predict and prevent failures:
Material Fatigue: Cyclic loading causes microscopic changes in material structure, leading to crack formation and propagation. This explains why regular inspections must focus on high-stress areas and why components have finite lifespans even under normal operation.
Corrosion Mechanisms: Electrochemical reactions between materials and their environment cause gradual degradation. This underlies the importance of protective coatings, environmental controls, and regular inspection of susceptible components.
Wear Mechanisms: The science of tribology explains how surfaces interact during operation. This includes:
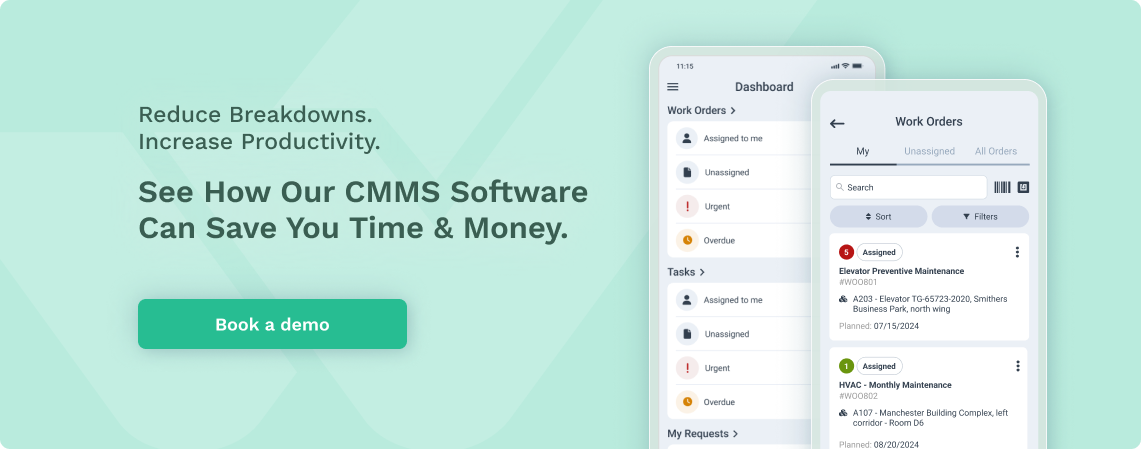
- Adhesive wear (surface bonding and tearing)
- Abrasive wear (surface scratching)
- Erosive wear (particle impact damage)
- Fatigue wear (repeated surface stress)
Systems Engineering Principles
O&M relies heavily on systems thinking and engineering principles:
Reliability Engineering: This field applies probability and statistics to predict and prevent failures. Key concepts include:
- Bathtub curve behavior (early failures, useful life, wear-out period)
- Reliability block diagrams for system analysis
- Failure Mode and Effects Analysis (FMEA)
- Redundancy and backup systems
Control Theory: The mathematical principles behind system control help us understand:
- System stability and response
- Feedback loops in operation
- Process control optimization
- Performance monitoring and adjustment
Fluid Dynamics and Heat Transfer
For many systems, especially in HVAC and industrial processes, these principles are crucial:
- Reynolds number affects flow characteristics
- Heat exchanger effectiveness depends on flow patterns
- Pump and fan laws govern system performance
- Pressure drops and flow distribution impact system efficiency
Electrical Engineering Principles
Understanding electrical systems is vital for O&M:
- Ohm’s Law and Circuit Behavior
- Power factor and energy efficiency
- Insulation degradation mechanisms
- Electromagnetic interference effects
Chemical Engineering Principles
Many O&M activities involve chemical processes:
- Chemical equilibrium in treatment systems
- Reaction kinetics in process equipment
- Mass transfer in separation processes
- pH control and corrosion prevention
Data Science and Analytics
Modern O&M increasingly relies on:
- Statistical process control
- Pattern recognition in condition monitoring
- Predictive modeling using machine learning
- Time series analysis for trend prediction
These scientific principles come together in practical applications. For example, when maintaining a pump system:
- Vibration analysis uses physics principles to detect misalignment
- Oil analysis applies chemistry to assess wear patterns
- Thermal imaging uses heat transfer principles to identify problems
- Performance curves rely on fluid dynamics
- Motor analysis applies electrical engineering principles
Understanding these scientific foundations helps maintenance professionals:
- Make better decisions about maintenance timing
- Choose appropriate monitoring techniques
- Predict potential failure modes
- Select optimal operating conditions
- Implement effective preventive measures
Real World Industry Examples of O&M
Power Plant Operations
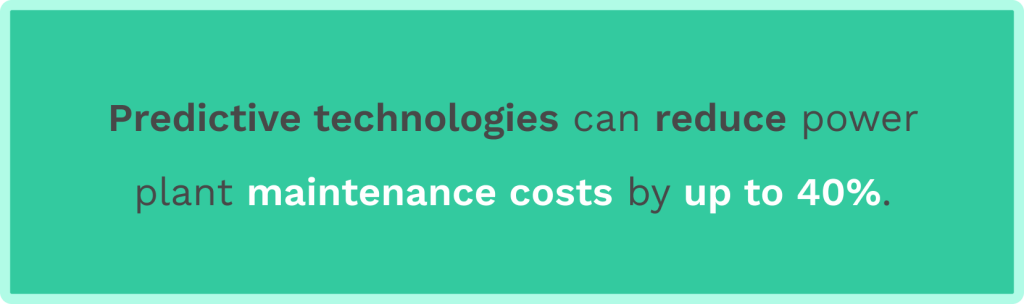
The Tennessee Valley Authority’s Cumberland Fossil Plant provides an excellent case study of comprehensive O&M practices in power generation. The plant implemented a predictive maintenance program that reportedly reduced forced outages by 25% over three years.
Their program integrated vibration analysis, thermography, and oil analysis to predict equipment failures before they occurred.
Building Management
The Empire State Building underwent a major retrofit and O&M overhaul that demonstrates the impact of proper O&M practices. According to various industry reports, the building’s O&M improvements included:
- Modernization of all 68 elevators with energy-efficient drives
- Installation of an advanced building management system
- Renovation of all 6,500 windows to improve thermal performance
- Implementation of tenant energy monitoring systems
Through these combined O&M initiatives, the project reportedly reduced energy costs by 38%, though you should verify current figures.
Water Treatment Facilities
The Orange County Water District’s Groundwater Replenishment System in California represents advanced O&M practices in water treatment. The facility’s O&M program includes:
- Real-time monitoring systems for water quality
- Predictive maintenance on reverse osmosis membranes
- Automated chemical dosing systems
- Comprehensive staff training programs
Manufacturing Sector
Toyota’s Total Productive Maintenance (TPM) system serves as a benchmark for manufacturing O&M. Their Georgetown, Kentucky plant implemented TPM principles that reportedly resulted in:
- Increased equipment effectiveness
- Reduced maintenance costs
- Improved product quality
- Enhanced worker safety
The specific metrics from these implementations would need to be verified against current sources.
Transportation Infrastructure
The Hong Kong Mass Transit Railway (MTR) system is often cited for its exceptional O&M practices. Their approach includes:
- Condition-based maintenance using IoT sensors
- Predictive analytics for track maintenance
- Automated inspection systems
- Integrated asset management systems
Their reported 99.9% on-time performance is often attributed to these comprehensive O&M practices, though current figures should be verified.
Healthcare Facilities
The Cleveland Clinic’s facilities management program demonstrates O&M best practices in healthcare settings. Their program encompasses:
- Advanced building automation systems
- Real-time equipment monitoring
- Integrated maintenance scheduling
- Energy optimization programs
The clinic reportedly significantly reduced energy consumption and maintenance costs, though specific figures should be verified.
Data Center Operations
Google’s data centers provide an interesting example of innovative O&M practices. They reportedly use machine learning algorithms to optimize:
- Cooling system operations
- Power usage effectiveness
- Equipment maintenance scheduling
- Energy consumption patterns
Their published case studies suggest these practices reduced energy usage by 40%, though current figures should be verified.
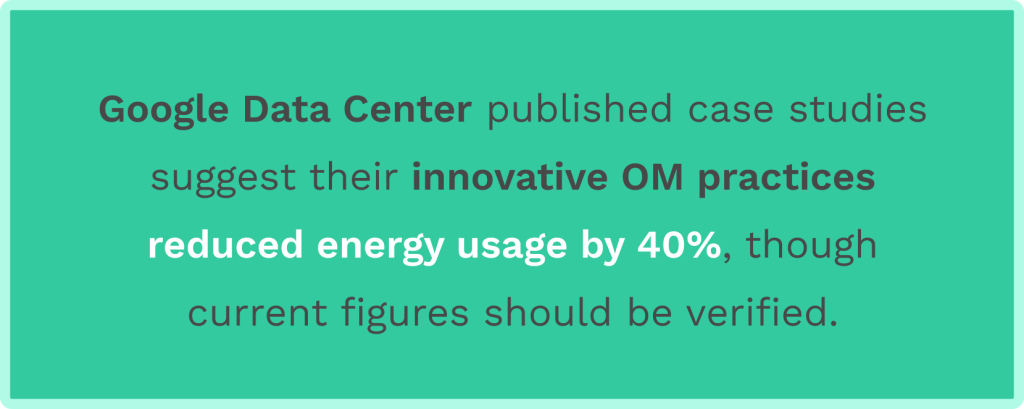
These examples illustrate several key principles of effective O&M:
- Integration of modern technology with traditional maintenance practices
- Focus on preventive and predictive maintenance rather than reactive repairs
- Use of data analytics to optimize operations
- Emphasis on staff training and development
- Clear documentation and standard operating procedures
Best Practices for O&M
- Implement a Computerized Maintenance Management System (CMMS): A CMMS can help streamline maintenance operations, track inventory and spare parts, and improve quality control and safety.
- Conduct Regular Inspections and Audits: Regular inspections and audits can help identify potential issues before they become major problems.
- Provide Training and Development Opportunities: Training and development opportunities for maintenance personnel can help them improve their skills and knowledge, leading to more efficient and effective maintenance operations.
- Monitor and Analyze Maintenance Data: Monitoring and analyzing maintenance data can help identify trends and patterns, allowing for more informed decision-making and improved maintenance operations.
Challenges and Opportunities in O&M
- Aging Infrastructure: Many facilities and assets are aging, requiring more frequent maintenance and repairs.
- Limited Resources: Limited resources, including budget and personnel, can make implementing and maintaining an effective O&M program challenging.
- Technological Advancements: Technological advancements, like the Internet of Things (IoT) and artificial intelligence (AI), can improve maintenance operations and asset management opportunities.
- Changing Regulations and Standards: Changing regulations and standards can require facilities and assets to adapt and modify their O&M programs to ensure compliance.
- Workforce Development: The need for skilled maintenance personnel can provide opportunities for workforce development and training programs.