Get a Free WorkTrek Demo
Let's show you how WorkTrek can help you optimize your maintenance operation.
Try for freeMTTF stands for Mean Time to Failure. Engineers and manufacturers use it as a key measure of product reliability. It tells us how long a product or system will likely work before breaking down.
This metric helps companies plan maintenance and set customer expectations. A higher MTTF usually means a more reliable product. For example, a light bulb with an MTTF of 1,000 hours is expected to last longer than one with an MTTF of 500 hours.
MTTF applies to items that can’t be fixed once they fail.
A measure called Mean Time Between Failures (MTBF) is used instead for things that can be repaired. Both help businesses make better products and keep customers happy.
Calculating MTTF
To find MTTF, divide the total hours of operation by the number of failures. The formula is:
MTTF = Total Operating Hours / Number of Failures
Source: WorkTrek
For example, if 100 light bulbs run for 1000 hours total and 10 fail:
MTTF = 1000 hours / 10 failures = 100 hours
This means each bulb is expected to last about 100 hours on average.
Testing many units over time gives more accurate MTTF values. Longer test periods often lead to better estimates.
MTTF vs. MTBF
MTTF and MTBF are similar but have key differences:
- MTTF: Used for non-repairable items
- MTBF: Used for repairable systems
MTBF includes repair time, while MTTF does not. MTBF is often higher than MTTF for similar items.
Here’s a comparison chart:
Source: WorkTrek
Both metrics help predict reliability, but they’re used for different types of systems.
Listen to a Podcast on MTTF
Application in Industries
MTTF plays a crucial role in various industries. It helps organizations optimize their operations and minimize disruptions.
Manufacturing and Production
Many factories use MTTF to schedule planned maintenance. This reduces unexpected downtime on production lines and helps keep productivity high.
Some companies use MTTF to decide when to replace old equipment. They compare the MTTF of aging machines to newer models, which helps them make smart upgrades.
MTTF also guides asset management strategies. It helps firms decide which machines need the most attention, ensuring critical assets get proper care.
Software and DevOps
MTTF is a useful DevOps metric in software. It measures how long systems run without crashes or errors.
Teams use MTTF to track system stability over time. A rising MTTF often means fewer bugs and better code quality.
MTTF helps with incident management, too. It shows how often significant issues pop up. This data can guide efforts to improve system reliability.
Some teams use tools like Jira Service Management to track MTTF. These tools help spot trends and set goals for system uptime.
MTTF can also highlight areas that need more testing or redesign. This helps teams focus their efforts where they’ll have the most significant impact.
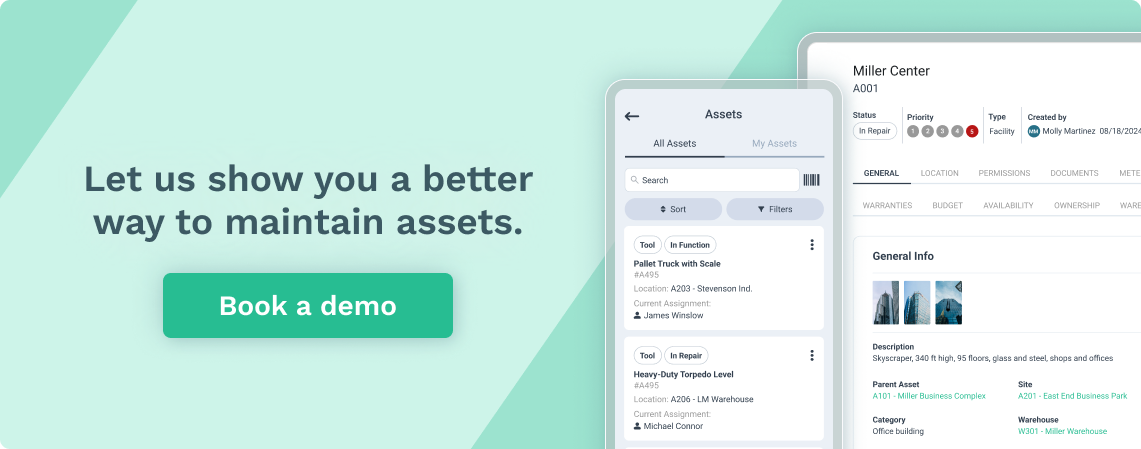
Components of MTTF
MTTF depends on the quality and durability of individual parts. Reliable components and proper maintenance are key to maximizing system uptime.
Importance of Reliable Components
Critical components like engines, fan belts, and wheels impact overall MTTF. High-quality parts last longer and break down less often, reducing repair costs and downtime.
Designers focus on making durable components. They use strong materials and smart designs to help parts withstand wear and tear.
Reliable components lead to better system performance and, in many cases, boost safety. Sturdy brakes on a car can prevent accidents.
Lifecycle of Components
Every part has an average lifespan. Some may last for years, while others need frequent replacement. Knowing these lifespans helps plan maintenance.
Regular checks can catch issues early, preventing sudden failures. Replacing parts before they break is called preventive maintenance.
Some components wear out faster than others. Fan belts and tires often need replacement sooner than engines. Tracking part lifecycles helps predict when to order replacements.
Proper care can extend component life. This might include regular cleaning or lubrication. Following manufacturer guidelines is important for maximizing part longevity.
Maintenance Strategies
Effective maintenance strategies help organizations improve equipment reliability and reduce downtime. These approaches focus on preventing failures and tracking performance metrics.
Proactive vs Reactive Maintenance
Proactive maintenance aims to prevent equipment failures before they happen. It includes scheduled inspections, part replacements, and upgrades. This approach can extend asset lifespans and cut repair costs.
Reactive maintenance only fixes equipment after it breaks down. While it may seem cheaper upfront, it often leads to more expensive repairs and longer downtimes.
Source: WorkTrek
Most companies use a mix of both strategies. They focus proactive efforts on critical assets while handling less important items reactively.
Maintenance Metrics and KPIs
Maintenance teams use key performance indicators (KPIs) to measure their effectiveness. Common metrics include:
- Mean Time Between Failures (MTBF)
- Mean Time To Repair (MTTR)
- Overall Equipment Effectiveness (OEE)
Source: WorkTrek
These KPIs help track equipment reliability, repair speed, and production efficiency. Teams can use them to spot trends and make data-driven decisions.
Benchmarking against industry standards lets organizations see how they compare to peers. This can reveal areas for improvement in their maintenance programs.
CMMS software often helps collect and analyze these metrics automatically. This makes it easier for teams to monitor performance and adjust their strategies as needed.
MTTF and Business Impact
MTTF affects a company’s bottom line and customer relationships. It plays a key role in managing downtime and costs.
Implications on Customer Satisfaction
MTTF directly impacts customer satisfaction. Frequent failures lead to unhappy customers and lost business. Companies with high MTTF have fewer outages and more reliable products.
Illustration: WorkTrek / Quote: Hubspot
Customers expect products to work without issues. Long periods between failures build trust and loyalty. This leads to positive reviews and word-of-mouth referrals.
On the flip side, low MTTF causes frustration. Customers may switch to competitors if they face too many problems. Businesses need to track MTTF as a key metric for customer happiness.
Cost Implications
MTTF has big effects on a company’s costs. Higher MTTF means less money spent on repairs and replacements. It also reduces the need for customer support staff.
Low MTTF leads to more frequent repairs, which increases labor and parts costs and can result in costly downtime for critical systems.
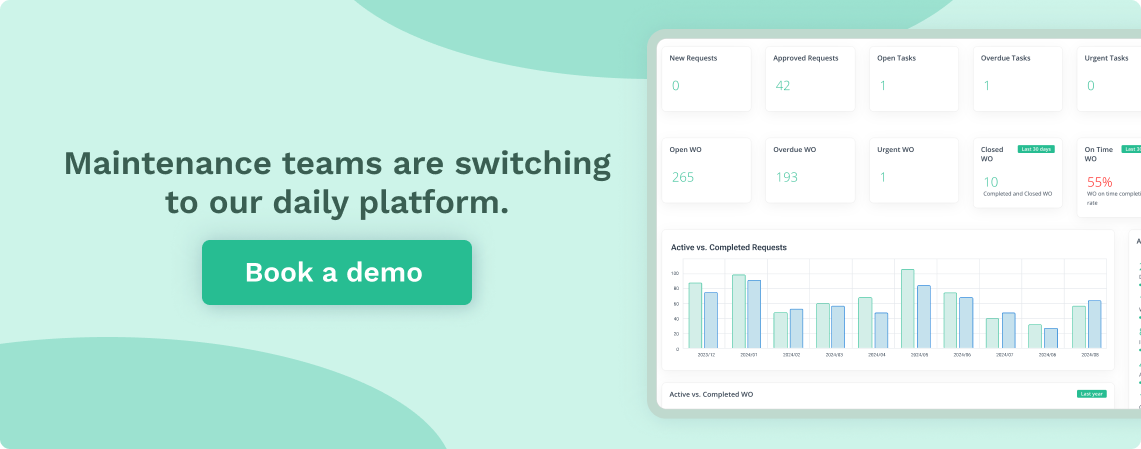
Here’s a simple breakdown of MTTF cost impacts:
- High MTTF: Lower repair costs, less downtime
- Low MTTF: Higher repair costs, more downtime
Smart companies invest in improving MTTF. This often leads to long-term cost savings. It’s a key part of running a cost-effective business.
Enhancing MTTF
Companies can take steps to improve their products’ Mean Time To Failure. This leads to better reliability and customer satisfaction.
Root Cause Analysis
Illustration: WorkTrek / Quote: Harvard Business School Online
Root cause analysis helps find the source of failures. Engineers look at broken products to spot weak points. They might use tools like fault tree analysis or fishbone diagrams.
Testing plays a significant role, too.
Products go through stress tests to find breaking points. This data helps make better designs.
Engineers also check how people use products in real life. Sometimes, customers use items in unexpected ways. This info leads to more robust designs.
Investment in Quality and Design
Investing in quality pays off. Better materials often last longer, and stronger parts can handle more wear and tear.
Smart design choices boost reliability, too. Simple designs with fewer parts often break less, and backup systems can keep products working even if one part fails.
Companies can also focus on making products easy to fix. This might mean using standard parts or making repair guides. When fixes are simple, products stay helpful longer.
Training workers well is key for quality. Skilled staff catch more issues before products leave the factory.
Modern Tools and Technologies
New tech improves MTTF tracking and prediction. Sensors on production lines gather real-time data, helping to spot issues before failures occur.
AI and machine learning analyze patterns to predict breakdowns. Digital twins simulate equipment to test different scenarios.
Maintenance teams use mobile apps to log repairs quickly. Cloud systems store vast amounts of reliable data.
Advanced diagnostics pinpoint root causes faster. This cuts downtime and boosts overall MTTF.
Automated monitoring alerts staff to potential problems. It can trigger planned maintenance before critical failures.