Get a Free WorkTrek Demo
Let's show you how WorkTrek can help you optimize your maintenance operation.
Try for freeKey Takeaways:
- More than 40% of maintenance teams are understaffed.
- Filling out work orders manually is time-consuming for technicians.
- Standardized workflows boost technician productivity by 30%.
- Companies using digital work order systems report 20% to 30% fewer breakdowns.
Do you often find work orders piling up, deadlines missed, or critical repairs slipping through the cracks?
If you do, it’s likely a result of poor work order management.
But don’t worry—by adopting the right best practices, you can avoid these issues and transform your maintenance operations.
Here are the five best practices for effective work order management.
Standardizing Workflows
Work order management can quickly become chaotic when every technician follows their own system.
Without a standardized process, critical details get missed, priorities become unclear, and inefficiencies pile up.
The solution is a structured workflow that ensures consistency across all maintenance tasks.
Start by defining a clear work order process—from request submission to completion.
This includes setting up approval steps, assigning responsibilities, and ensuring work orders contain all necessary details before technicians begin the job.
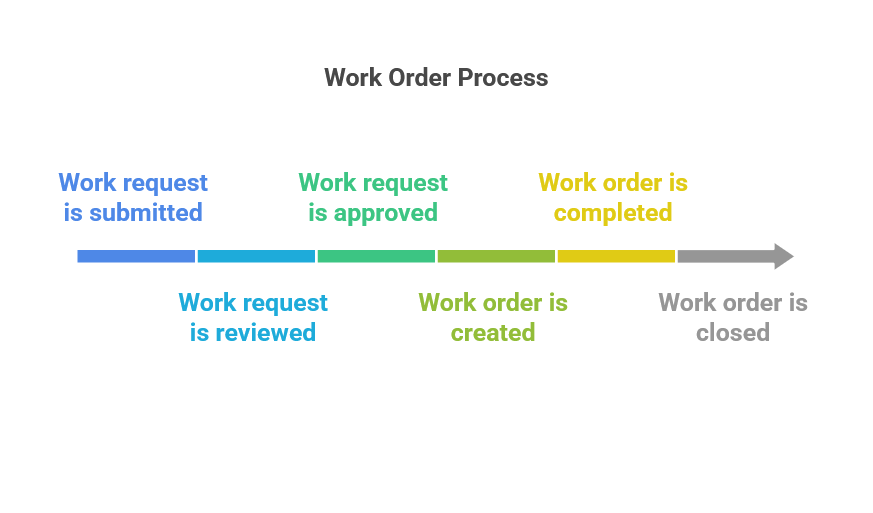
When everyone follows the same structured approach, work orders move smoothly without unnecessary delays.
Secondly, standardize your work order formats to ensure consistency across different types of maintenance tasks.
Whether it’s corrective, preventive, or predictive maintenance, or even cleaning and inspections, each work order should have a predefined structure tailored to the task at hand.
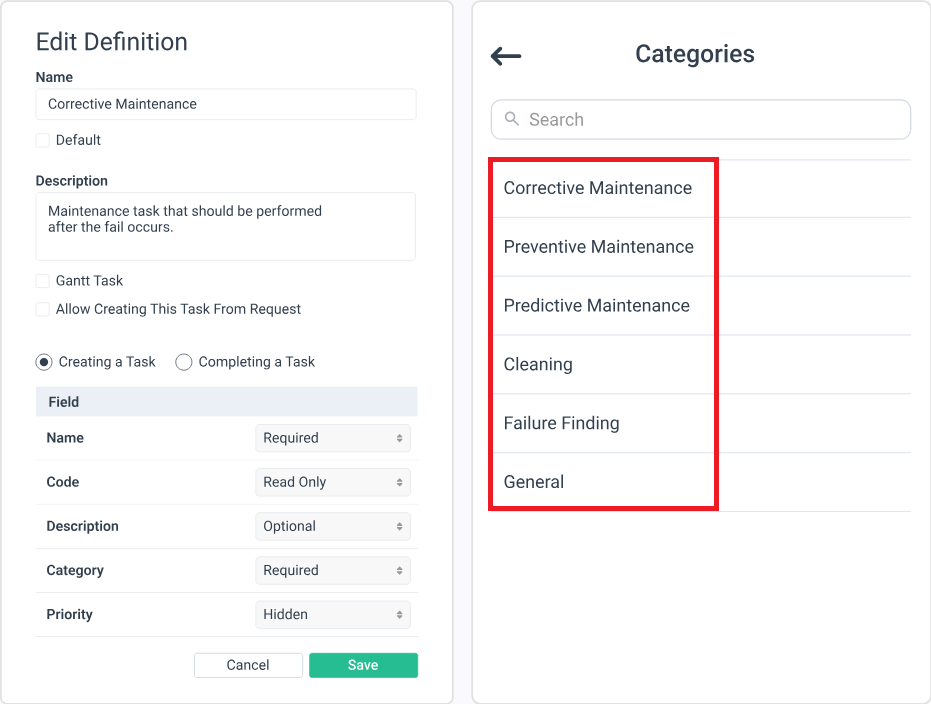
The information should include a clear problem description, the asset linked to it, the assigned technician, a list of required parts, planned expenses, and health and safety instructions.
Here is an example of a work order template with all these fields waiting to be filled out in a few clicks:
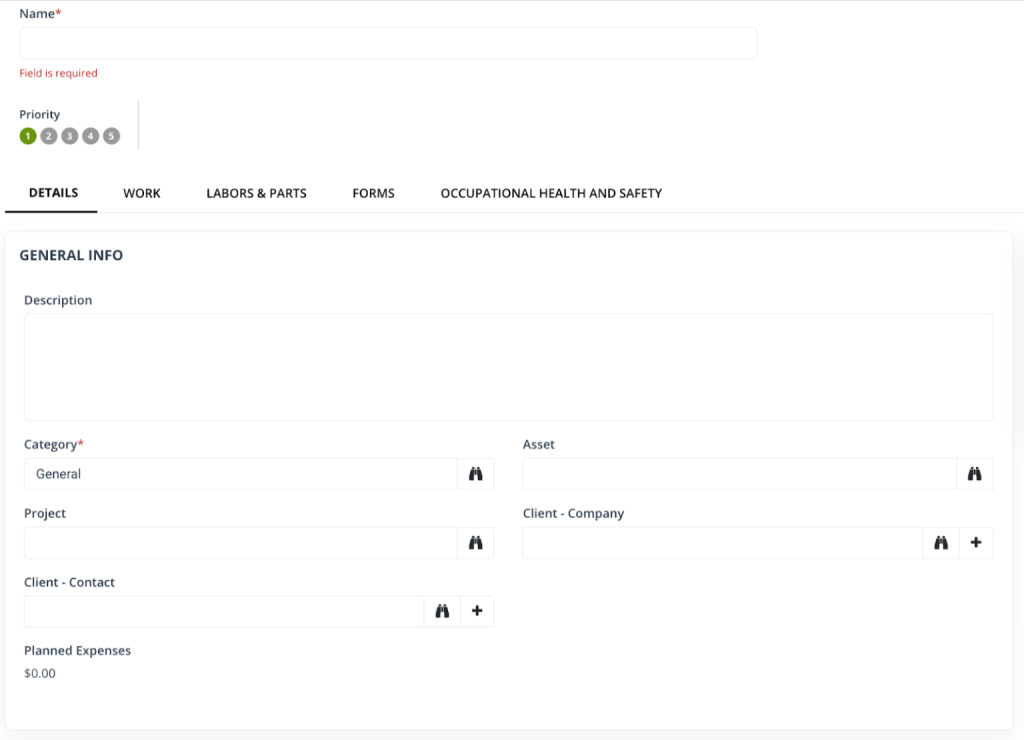
You can also create checklists or step-by-step guidelines to ensure nothing is overlooked and add it to the “Work” section.
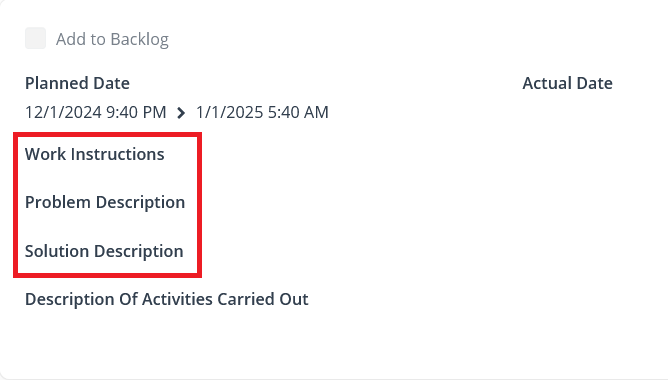
A dedicated template like this will ensure that all the necessary details are recorded, minimizing back-and-forth clarifications.
Beyond using standardized work order templates, you should also make sure everyone in your team uses the same language when describing tasks or parts.
For example, if technicians describe an issue vaguely—like saying a machine is “not working”—diagnosing the problem takes longer.
However, teams can quickly assess and address the issue with a standardized reporting format that includes failure codes (exemplified below), affected components, and priority levels.
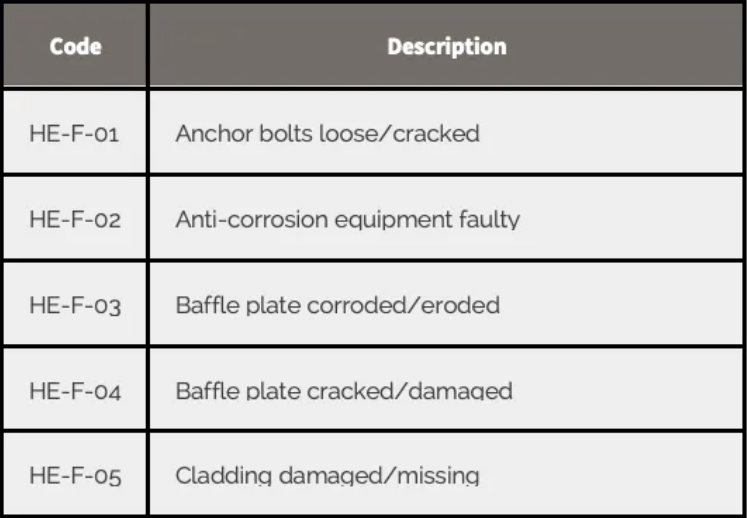
Finally, standardization should be an ongoing effort.
Regularly review workflows, update templates as needs evolve, and ensure that documentation remains accessible to everyone.
Maintaining Accurate Records
A well-organized workflow is only effective if maintenance records are accurate.
Poor documentation leads to missing service histories, repeated work, and compliance risks.
That’s why detailed, up-to-date records are essential for both tracking past work and making informed maintenance decisions.
At a basic level, every work order should log:
- Asset details and problem descriptions
- Parts used and corrective actions taken
- Assigned technician and time spent on the task
Historical records containing this information drive smarter maintenance planning.
You can identify recurring equipment failures, spot inefficiencies, and optimize preventive maintenance schedules by analyzing past work orders.
On the flip side, maintenance teams are left guessing about past repairs without complete records.
This, of course, slows down troubleshooting.
However, it can also lead to unnecessary expenses, such as replacing recently serviced parts.
Accurate records play a crucial role in regulatory compliance, too.
In industries like aviation, for example, maintenance logs must be well-documented and auditable.
Retired A&P Mechanic and Army helicopter pilot James Edward Piper explains why:
“During annual inspections, the mechanic will check the aircraft logbooks and will not release the aircraft for flight unless in order. All this is for safety, and all this is needed when the aircraft is sold or bought. And yes, this is by law.”
The same applies to other sectors in industrial maintenance.
If an inspection occurs and records are incomplete, companies risk failing compliance checks or facing liability issues.
Beyond that, maintenance records impact warranty claims.
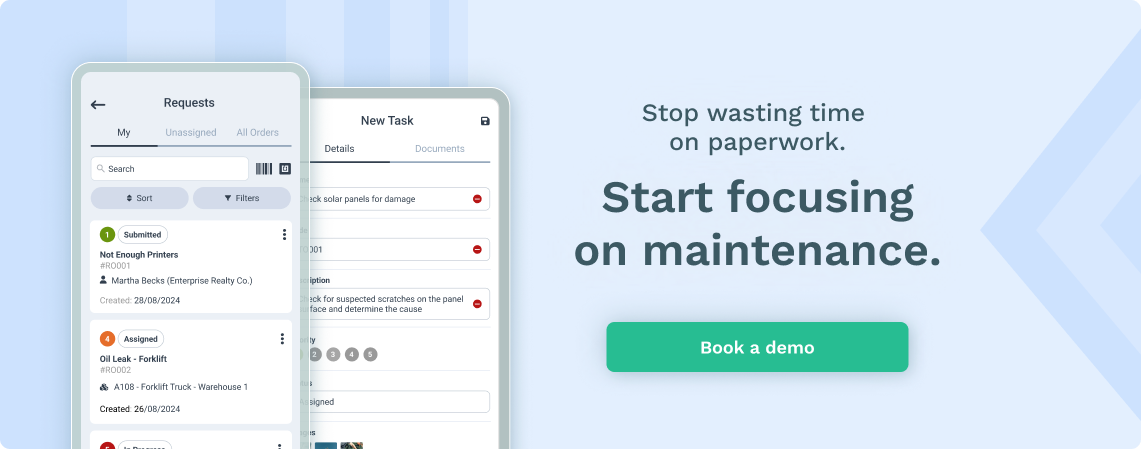
Namely, many equipment warranties require proof of regular servicing before covering repairs or replacements.
So, if documentation is missing, companies could lose out on thousands of dollars in potential claims, like in the example below:

This is why work orders should be stored digitally, not just on paper.
Paper-based records are easily misplaced, and spreadsheets often become outdated.
Conversely, digital work order management systems ensure that all maintenance history is centralized, searchable, and accessible in real time.
And before all else—it significantly reduces errors.
For example, Cleanaway, an Australian waste management company, processed around 220,000 paper-based work orders annually.
However, as their Executive General Manager Preet Brar pointed out, work orders filled manually by technicians were full of errors and lacked information:
By shifting to a digital record-keeping system, they improved work order accuracy, streamlined workflows, and increased technicians’ productivity.
Good record-keeping isn’t just about storing data.
It creates a reliable foundation for proactive maintenance, compliance, and cost savings.
And this is where technology plays a key role.
Using Work Order Management Systems
As we’ve seen, managing work orders manually is a headache.
Paper-based processes cause delays, work requests get lost, and technicians waste time tracking down information instead of fixing equipment.
A major U.S.-based oil and gas company with 90,000 employees faced these exact challenges.
Their maintenance teams worked in silos, struggling to coordinate preventive and corrective tasks across different departments.
Without a centralized system, they ran into serious issues:
- Unplanned maintenance led to rework and overtime.
- Work requests often went missing or remained unattended.
- Duplicate data entry slowed everything down, leading to errors.
- Operators had no reliable way to report issues or assign work by priority.
- Inventory costs skyrocketed due to unexpected downtime and production delays.
- There was no system for tracking work orders, backlogs, or maintenance completion rates.
- Planning major equipment overhauls was chaotic, making it difficult to manage inventory and costs.
To solve these challenges, they implemented a mobile work order management system.
And the results were truly game-changing:
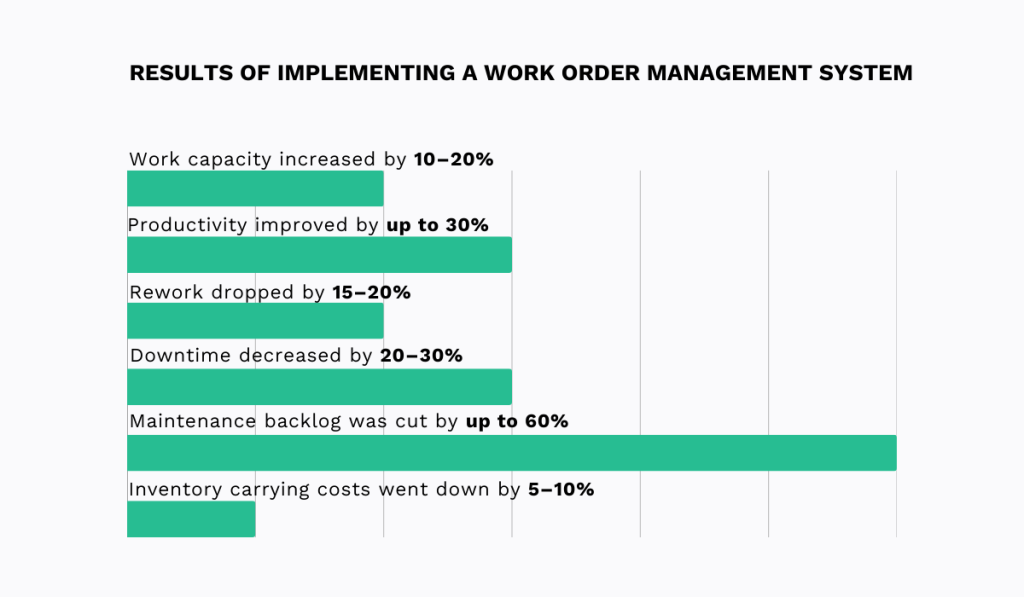
From this example alone, it’s clear that work order management systems eliminate inefficiencies by centralizing all maintenance-related data, automating processes, and giving real-time visibility into work progress.
Let’s now take a look at one such solution.
WorkTrek, for example, has all the key features for effective work order management.
For starters, it allows maintenance teams to create, schedule, and prioritize work orders while keeping all critical details—like asset history, time tracking, and materials used—organized in one place.
Multiple viewing options, including list, map, and scheduler formats, make it easy to stay on top of all work orders.
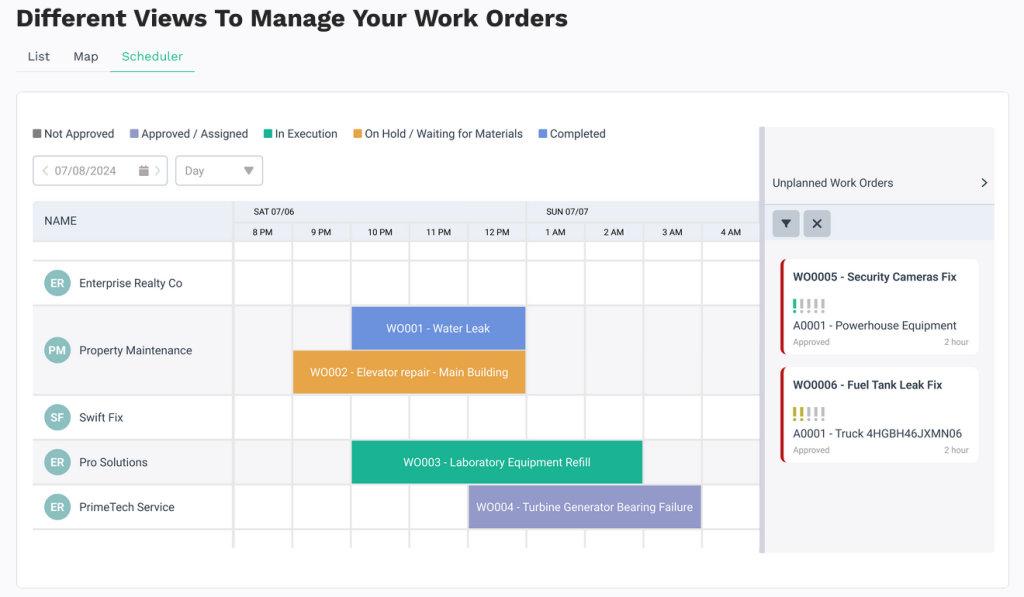
Moreover, technicians can upload photos, documents, and notes directly into the system from their phones.
This enables them to provide real-time updates and flag issues as they arise.
With commenting, tagging, and notifications, teams can communicate instantly, reducing delays and ensuring that critical work is completed on time.
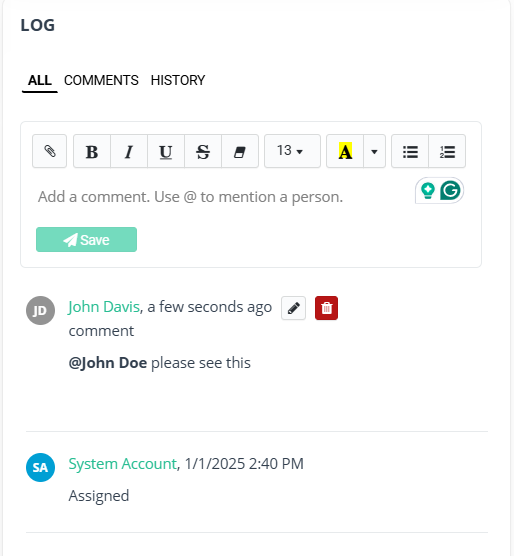
Additionally, WorkTrek lets you add standardized digital checklists and forms in each work order.
That way, you can ensure that every maintenance task follows the proper procedures, reducing errors and improving compliance.
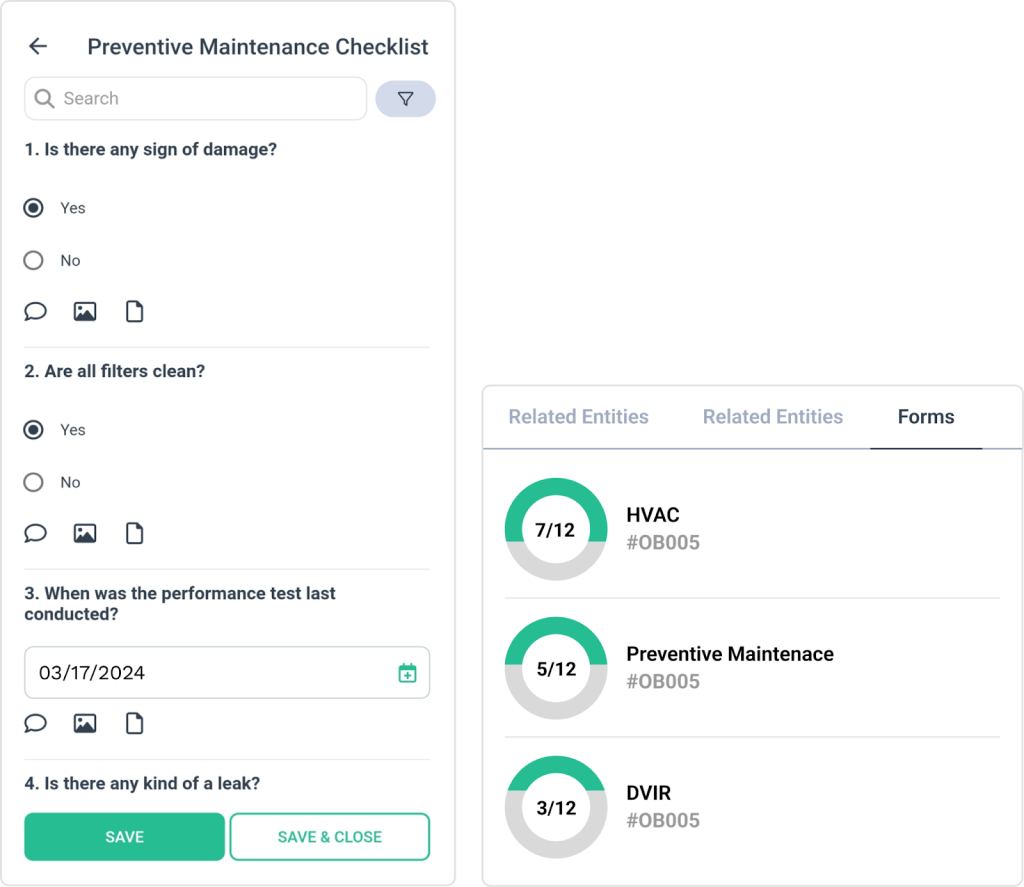
Plus, customizable workflows make it easy to adapt the system to different types of work orders—whether for preventive maintenance, emergency repairs, or inspections.
All in all, if you switch to a modern work order management system, you won’t just organize work orders better.
You will boost efficiency, reduce downtime, and make maintenance operations more predictable and cost-effective.
Prioritizing Based on Urgency
Not all maintenance tasks are equally urgent.
Some demand immediate attention, while others can wait.
But without a clear system for prioritization, everything starts to feel like an emergency, ultimately leading to inefficiency, stress, and potential downtime.
In fact, 98.2% of people struggle with prioritizing tasks, according to a survey by Reclaim.ai.
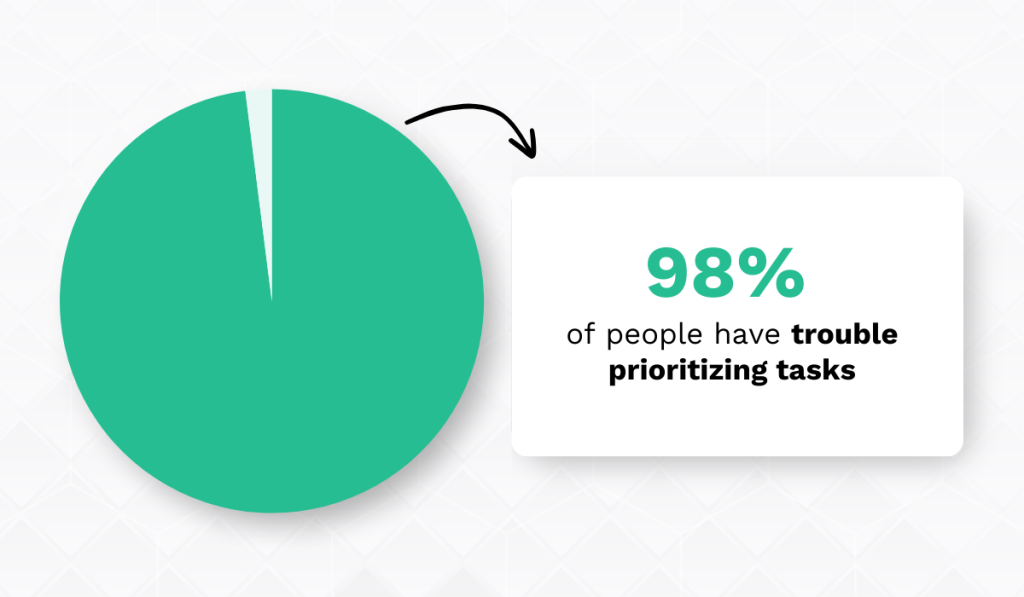
While the study focused on general workweek tasks, the same challenge applies to maintenance.
And when work orders aren’t properly prioritized, teams waste time juggling competing demands instead of focusing on what truly matters.
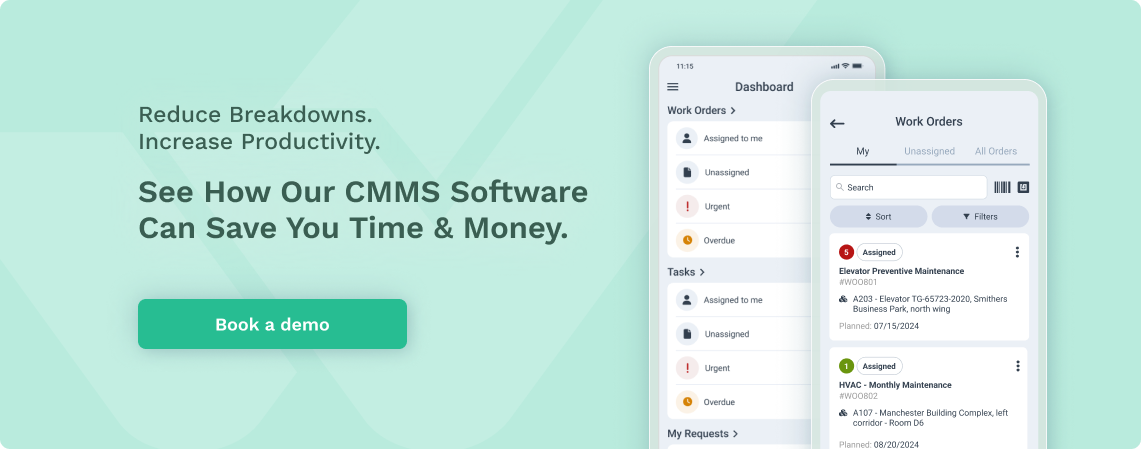
The solution is a structured approach.
Every work order should have a priority level based on these three factors:
- Safety risks
- Operational impact
- Downtime potential
Now, different organizations may define urgency in their own way, but here are some general guidelines for prioritizing maintenance:
Priority level | Definition | Examples | Action |
---|---|---|---|
Emergency | Immediate risk to safety, production, or operations. | Loss of power or water supplies, HVAC failure, natural disasters, fire, key asset breakdowns, and major security problems. | Respond immediately, regardless of other tasks. |
High priority | Not an emergency yet, but will cause issues soon if left unresolved. | Leaking roofs, high-use equipment that is not performing well, repairs to key assets, and safety inspections. | Handle as soon as possible to prevent escalation. |
Medium priority | Preventive maintenance or routine repairs. | Lubricating equipment, replacing air filters, and scheduled inspections. | Complete within scheduled maintenance timelines. |
Low priority | Fill-in work but not vital to day-to-day operations. | Repainting walls, fixing minor leaks, and installing office furniture. | Schedule when resources allow. |
For example, a work order for a water leak in a high-traffic area would be marked as an emergency, as seen in this work order:
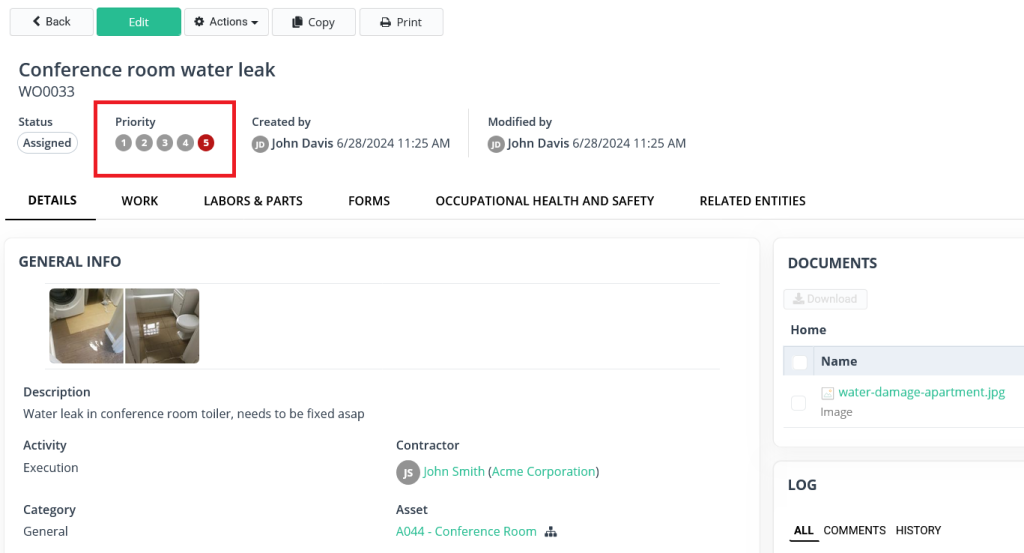
A technician using the system would see the red priority level on their mobile app, making it clear that this task comes first.
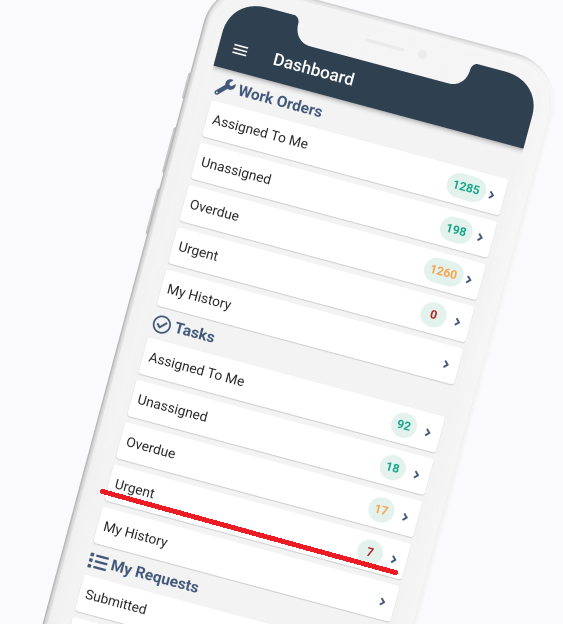
Without prioritization, urgent repairs are bound to get buried under routine tasks.
A structured system prevents this.
Which approach makes more sense to you?
Optimizing Workforce Allocation
Optimizing workforce allocation is a key part of effective work order management.
Even with the best work order system, if tasks aren’t assigned strategically, productivity suffers, delays pile up, and resources go to waste.
This challenge is even greater when teams are understaffed, which is a growing problem in maintenance and facilities management.
Namely, a 2021 Plant Engineering maintenance study found that 34% of managers see a lack of resources or staff as one of their main future challenges.
The State of Facilities Management Technology 2024 report confirms this, with almost 43% of facility managers reporting their teams are understaffed.
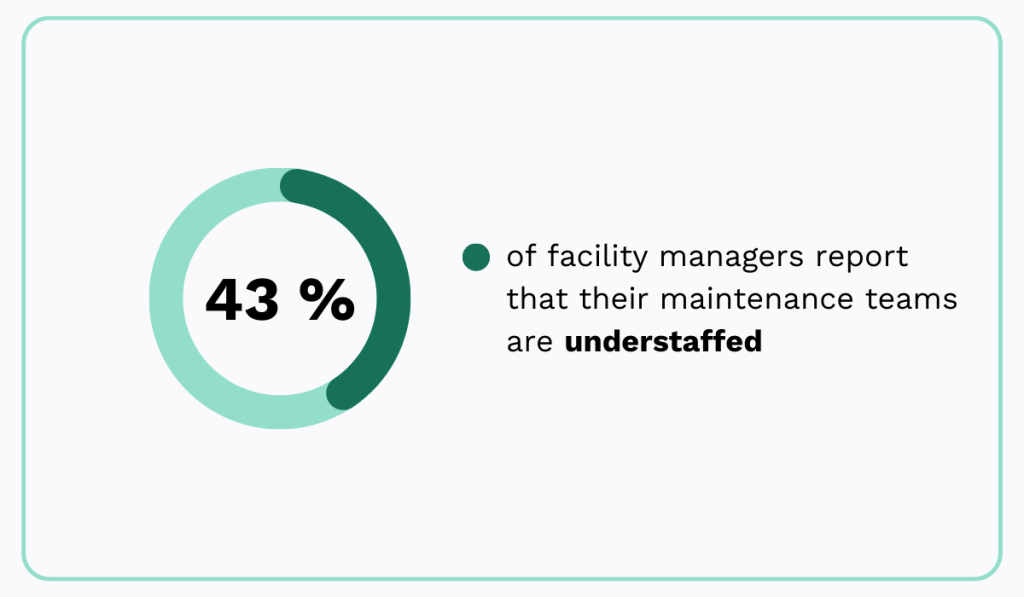
When every worker counts, proper workforce allocation becomes even more important.
So, how can you optimize the process?
Skill level should always be the starting point.
Assigning specialized jobs to the right technicians prevents mistakes, rework, and wasted time.
A system that tracks technician skills ensures that complex repairs go to the most experienced team members, while routine tasks are handled by those who are still building their expertise.
Availability is another key factor.
Overloading one technician while others have open schedules leads to delays and burnout.
But a scheduler—like the one below—that provides a clear view of workloads helps managers distribute tasks evenly.
Ultimately, this ensures that no one is overwhelmed while urgent work still gets done on time.
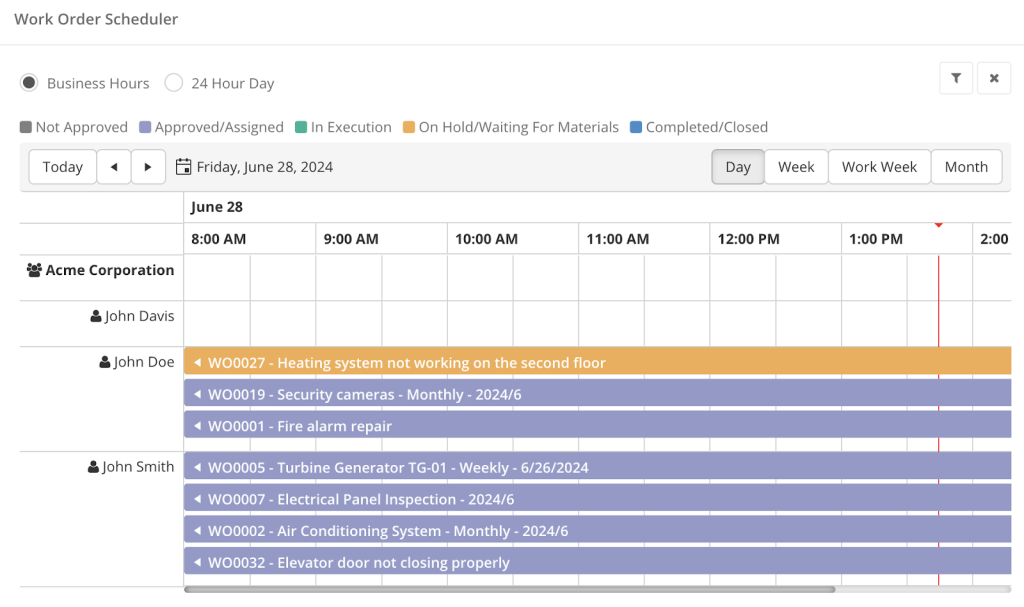
Location is another important factor.
If a critical repair is needed, dispatching a technician who’s already nearby makes more sense than sending someone from across the facility—or worse, from a completely different site.
A work order system with real-time map tracking allows teams to assign the closest available technician, cutting down travel time and improving response rates.
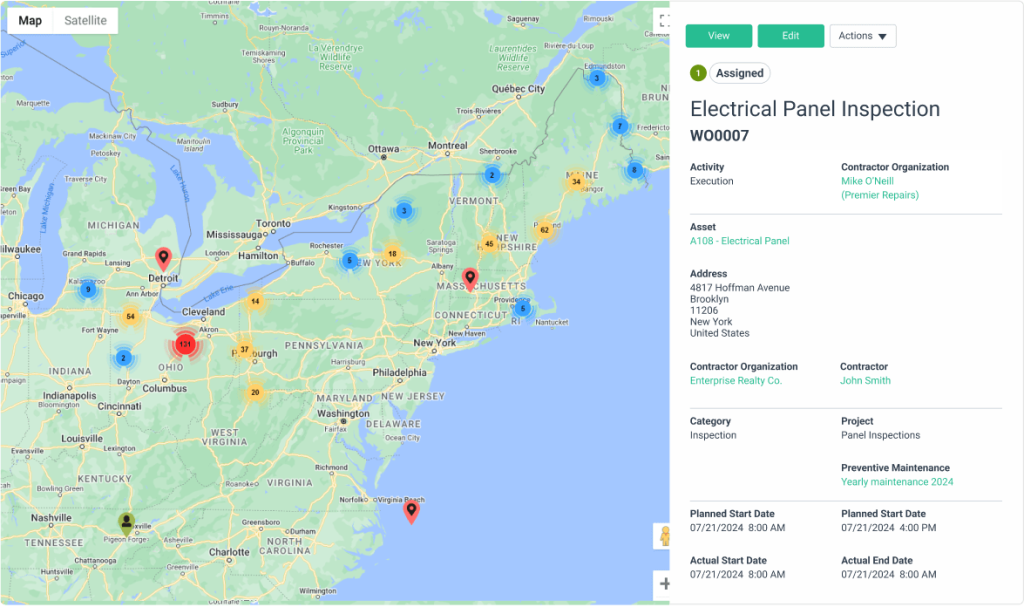
At its core, optimizing workforce allocation is about making the best use of available resources.
With the right approach and system, maintenance work gets done faster, with fewer disruptions, and without overburdening the team.
In a time of real concern about staff shortages, strategic task management keeps everything running efficiently, even when teams are stretched thin.
Conclusion
Managing work orders shouldn’t be a constant struggle.
When processes are messy, delays and inefficiencies pile up.
But with standardized workflows, accurate records, and the right technology, work order management can become a well-run operation.
So, if your current system feels disorganized, start with one change: go digital.
A modern work order system helps you stay ahead of problems, respond faster, and centralize everything in one place.
The result will be fewer breakdowns, lower costs, and a more reliable facility.