What is Asset Lifecycle Management?
Asset Lifecycle Management (ALM) is a comprehensive approach to managing an organization’s physical assets across their entire lifespan, from acquisition through operation, maintenance, and eventual retirement or disposal. ALM involves optimizing assets’ value, cost, risk, and performance to support an organization’s strategic objectives.
ALM aims to maximize return on asset investments while managing the total cost of ownership. It makes data-driven decisions about asset procurement, utilization, care, and decommissioning. ALM takes a holistic, long-term view of assets and aligns asset management with the broader business context.
ALM Lifecycle
ALM considers the complete lifecycle of an asset, including:
- Planning: Identifying asset needs and developing acquisition strategies
- Acquisition: Procurement, installation, and commissioning of new assets
- Operation: Using assets productively to deliver value for the organization
- Maintenance: Sustaining asset performance through preventive and corrective maintenance
- Modification: Upgrading or expanding asset capabilities to meet changing requirements
- Decommissioning: End-of-life retirement, replacement, redeployment or disposal of assets
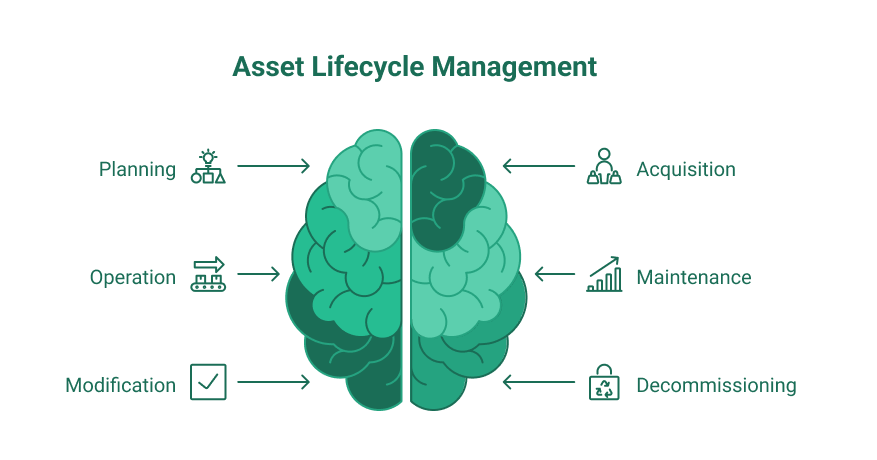
Effective ALM requires integrating financial, operational, maintenance, and risk data to guide strategic asset decisions and activities. It maximizes business value while optimizing costs, risks, capacity, quality, safety, compliance, reliability, and environmental impact across the full asset lifecycle.
Importance of Asset Lifecycle Management
- Maximizing asset value:
- ALM helps organizations get the most financial and productive value from their assets by optimizing utilization, minimizing downtime, extending useful life, and aligning assets to business needs. This improves return on asset investments.
- Managing costs:
- Using a long-term, full lifecycle view, ALM helps control asset-related costs like energy, maintenance, repairs, and capital expenditures. Optimized ALM lowers the total cost of ownership.
- Improving performance:
- ALM maximizes asset uptime, throughput, quality, and reliability to improve operational performance. Effective ALM keeps assets running optimally.
- Managing risk:
- ALM mitigates asset-related operational, safety, compliance, and financial risks through preventive maintenance, asset monitoring, and capital planning strategies.
- Capital decision-making:
- ALM provides the asset information needed for capital investment decisions like asset replacement, upgrade, or expansion. It also supports long-term capital planning.
- Compliance:
- ALM ensures assets meet regulatory, safety, quality, and environmental requirements and maintains detailed asset records for compliance reporting.
- Sustainability:
- ALM improves asset sustainability by extending asset life, managing energy use, and planning end-of-life strategies like refurbishing or recycling.
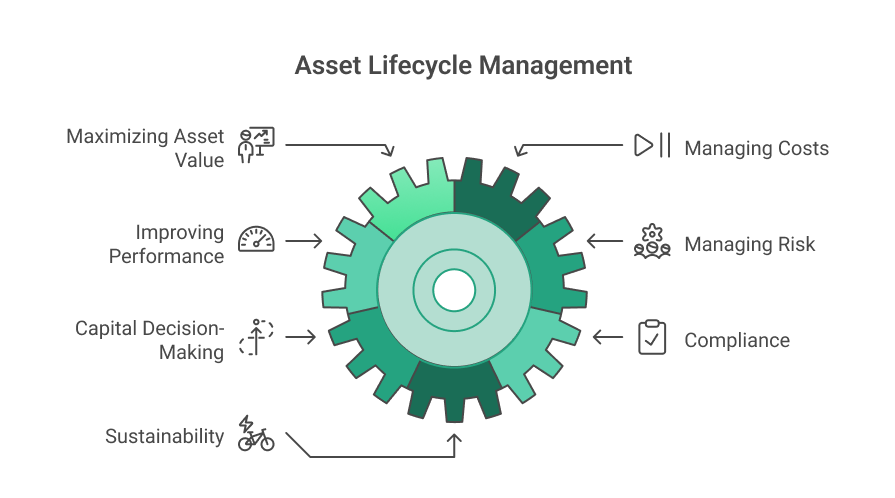
Tools to Manage ALM
Companies use various tools to track and manage the lifecycle of their physical assets, from acquisition to disposal. These tools, collectively known as Asset Life Management (ALM) systems, help organizations optimize asset performance, minimize costs, and ensure compliance with regulations and standards. Here are some of the key tools used for ALM:
- Enterprise Asset Management (EAM) Software:
- EAM software is the backbone of many ALM programs, providing a single source of truth for asset data and enabling organizations to manage the entire asset lifecycle from a centralized platform. These systems allow maintenance teams to track asset performance, schedule and execute maintenance activities, manage spare parts inventory, and generate reports and analytics to support decision-making.
- Computerized Maintenance Management Systems (CMMS):
- CMMS products are designed to help maintenance teams manage day-to-day maintenance activities more efficiently and effectively. These systems allow technicians to create and track work orders, schedule preventive maintenance tasks, and record asset maintenance history. CMMS tools can also generate reports and analytics to help maintenance managers identify trends and opportunities for improvement.
- Asset Performance Management (APM) Software:
- APM software takes ALM to the next level by leveraging advanced analytics and machine learning techniques to predict and prevent asset failures. These tools collect and analyze vast amounts of data from various sources, including sensors, control systems, and maintenance records, to identify patterns and anomalies that may indicate potential issues. By detecting these issues early, APM software can help organizations optimize maintenance strategies, reduce unplanned downtime, and extend asset lifespan. APM tools can also provide insights into asset performance across the entire fleet, enabling organizations to benchmark performance and identify best practices.
- Asset Tracking and Inventory Management Systems:
- Asset tracking and inventory management systems are essential for ensuring organizations have accurate and up-to-date information about their physical assets. These systems utilize technologies such as barcodes, RFID tags, and GPS to track the location and movement of assets in real-time and monitor inventory levels and conditions. By providing visibility into asset location and status, these tools can help organizations optimize asset utilization, reduce inventory costs, and ensure that critical assets are available when needed. Many CMMS systems, like WorkTrek, have asset tracking and inventory management built into the solution.
- Mobile Apps and Field Service Management Tools:
- Mobile apps and field service management tools are becoming increasingly important in ALM programs, as they enable maintenance technicians to access critical asset information and complete maintenance tasks from anywhere, at any time. These tools allow technicians to view work orders, access asset maintenance history, and record maintenance activities from their mobile devices, reducing paperwork and improving accuracy. Mobile apps can also enable real-time communication and collaboration between field technicians and office-based teams, ensuring that everyone has access to the latest asset data and can work together to resolve issues quickly. Field service management tools can also help organizations optimize technician schedules and routes, reducing travel time and improving efficiency.
- Predictive Maintenance and Condition Monitoring Tools:
- Predictive maintenance and condition monitoring tools are components of many ALM programs. These tools enable organizations to detect potential asset failures before they occur and optimize maintenance strategies accordingly. They utilize sensors and other monitoring devices to collect real-time data on asset performance and condition, such as vibration, temperature, and pressure. This data is then analyzed using advanced analytics and machine learning algorithms to identify patterns and anomalies that may indicate potential issues. By detecting these issues early, predictive maintenance tools can help organizations schedule maintenance activities optimally, reducing unplanned downtime and extending asset lifespan.
- Digital Twin Platforms:
- Digital twin platforms are emerging as a powerful tool for ALM, enabling organizations to create virtual replicas of physical assets and systems that can be used to simulate performance, predict potential issues, and optimize maintenance strategies. These platforms utilize data from various sources, including sensors, maintenance records, and design specifications, to create highly accurate and detailed models of assets and systems. By running simulations and analyses on these digital twins, organizations can identify potential failure modes, test different maintenance scenarios, and optimize asset performance over the entire lifecycle. Digital twin platforms can also enable collaboration between different stakeholders, such as maintenance teams, engineers, and asset managers, by providing a shared virtual environment for testing and decision-making.
Get a Free WorkTrek Demo
Let's show you how WorkTrek can help you optimize your maintenance operation.
Try for free