What is Automated Maintenance?
Automated maintenance involves using technology, software, and systems to schedule, monitor, and perform maintenance activities with minimal human intervention. It uses automation tools such as sensors, Internet of Things (IoT) devices, and specialized maintenance software to streamline workflows, track equipment conditions, and initiate maintenance tasks.
Automated maintenance aims to improve efficiency, reduce downtime, and extend the lifespan of assets.
In an automated maintenance system, predictive maintenance algorithms may analyze real-time data from equipment to detect potential issues before they fail. For example, IoT sensors can monitor temperature, vibration, or pressure levels, automatically triggering alerts or maintenance tasks when abnormal patterns are detected. Computerized Maintenance Management Systems (CMMS) often form the backbone of automated maintenance by scheduling routine maintenance and generating work orders without manual input.
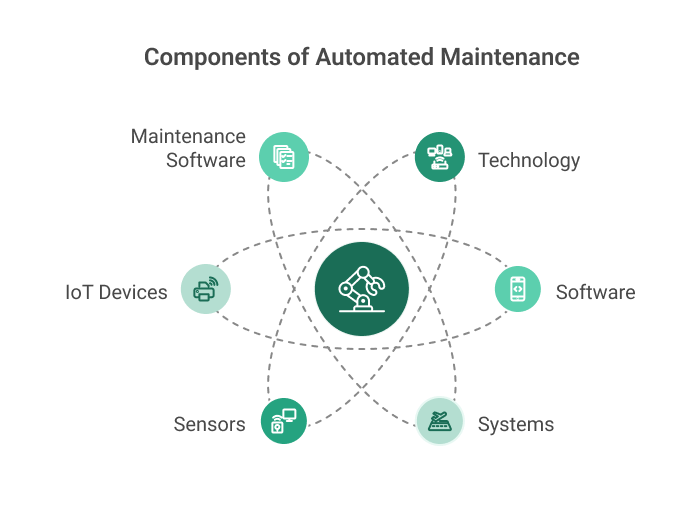
Automated maintenance enables condition-based maintenance, where service is performed based on the actual condition of the asset rather than fixed intervals. This approach reduces unnecessary maintenance, improves asset reliability, and optimizes resource allocation. It also plays a crucial role in preventive and predictive maintenance strategies, helping organizations move from reactive to proactive maintenance.
Additionally, automated systems improve data accuracy by reducing the likelihood of human errors in scheduling or reporting. Maintenance teams benefit from real-time visibility into asset health and maintenance status, which enables faster response times and better decision-making.
Automated maintenance is commonly used in manufacturing, utilities, and transportation industries, where complex equipment needs continuous monitoring and rapid intervention. By minimizing manual tasks and using data-driven insights, organizations can reduce maintenance costs, avoid unexpected failures, and achieve higher operational efficiency.
Best Practices for Automated Maintenance
Here are some best practices for implementing automated maintenance in a maintenance organization:
- Identify automation opportunities: Conduct a thorough analysis of maintenance processes and tasks to identify areas where automation can provide the most significant benefits.
- Select appropriate technologies: Choose automation technologies that align with your organization’s needs, such as sensors, IoT devices, AI-powered analytics, and robotic systems.
- Integrate with existing systems: Ensure that automated maintenance solutions integrate seamlessly with your existing CMMS, ERP, and other relevant systems to enable data sharing and streamlined workflows.
- Implement predictive maintenance: Use sensor data and advanced analytics to predict potential asset failures and proactively schedule maintenance, reducing unplanned downtime.
- Establish data governance: Develop policies and procedures for collecting, storing, and analyzing data generated by automated maintenance systems to ensure data quality, security, and privacy.
- Train staff on automation: Train maintenance staff on how to work alongside and leverage automated systems effectively, fostering a culture of acceptance and continuous learning.
- Start with pilot projects: Begin with small-scale pilot projects to validate the effectiveness of automated maintenance solutions before scaling up to full implementation.
- Monitor and optimize performance: Continuously monitor the performance of automated maintenance systems and use the insights gained to optimize processes, fine-tune algorithms, and improve overall effectiveness.
- Ensure safety and compliance: Implement appropriate safety measures and ensure compliance with relevant regulations when deploying automated maintenance technologies, particularly in hazardous environments.
- Develop a long-term roadmap: Create a strategic roadmap for the gradual implementation of automated maintenance aligned with organizational goals and resource availability.
- Foster collaboration: Encourage collaboration between maintenance, IT, and other relevant departments to ensure smooth implementation of automated maintenance initiatives and ongoing success.
- Regularly review and update: Periodically assess the performance of automated maintenance systems and update them as needed to keep pace with evolving technologies and business requirements.
By following these best practices, maintenance organizations can effectively harness the power of automation to improve asset reliability, reduce costs, and enhance overall maintenance efficiency.
Benefits and Drawbacks of Automated Maintenance
Benefits of Automated Maintenance:
- Increased Efficiency: Automated maintenance systems can perform tasks faster, more consistently, and with less downtime than manual procedures. Automation reduces the time and effort required for routine inspections, data collection, and maintenance execution.
- Improved Accuracy: Automated systems minimize human errors in data entry, analysis, and maintenance activities. They ensure maintenance tasks are performed according to precise specifications and schedules, reducing the risk of missed or incorrect maintenance.
- Predictive Capabilities: Automated systems can continuously monitor equipment performance and condition data, enabling early detection of potential failures. This allows for proactive maintenance interventions that prevent breakdowns and extend asset life.
- Enhanced Safety: Automating maintenance tasks reduces the need for human intervention in hazardous or hard-to-reach areas, minimizing the risk of worker injuries and accidents associated with manual maintenance activities.
- Centralized Data Management: Automated systems capture and store maintenance data in a centralized database, providing a single source of truth for asset information. This facilitates data analysis, reporting, and decision-making across the organization.
- Compliance and Documentation: Automated systems can be programmed to enforce and document compliance with regulatory requirements, industry standards, and company policies related to maintenance, safety, and environmental protection.
- Cost Savings: While implementing automation may incur upfront costs, it can lead to long-term cost savings through increased productivity, reduced downtime, optimized maintenance schedules, and extended asset life. Automation also frees up human resources for higher-value tasks.
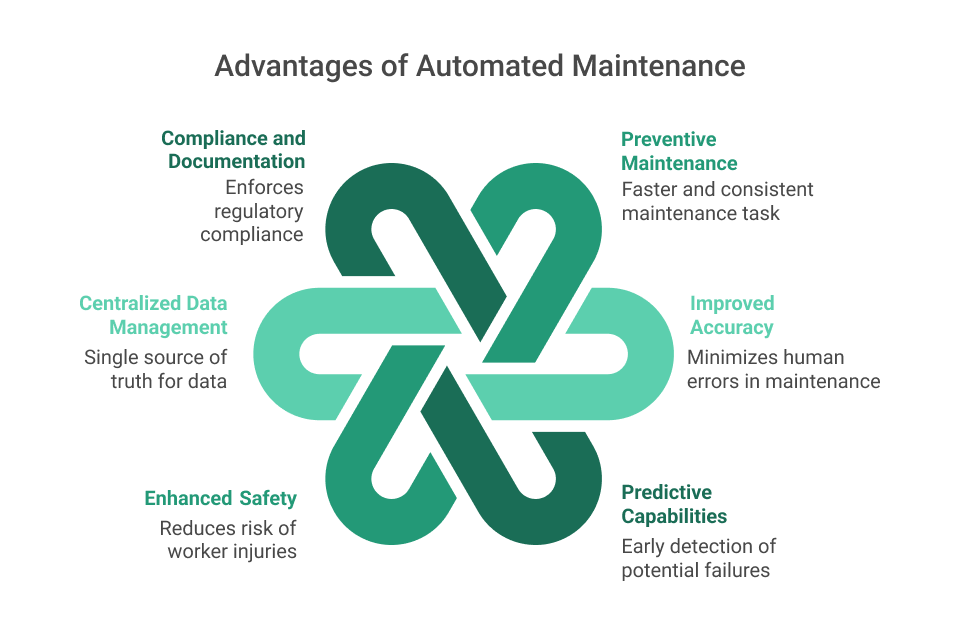
Drawbacks of Automated Maintenance:
- Initial Investment: Implementing automated maintenance systems requires significant upfront costs for hardware, software, sensors, and integration. This can be a barrier for organizations with limited budgets or those who have not yet proven the ROI of automation.
- Technical Complexity: Automated systems can be complex to design, install, configure, and maintain. They often require specialized skills and training that may not be readily available in-house. Dependence on external vendors or consultants can increase costs and risks.
- Integration Challenges: Integrating automated maintenance systems with existing equipment, control systems, and IT infrastructure can be challenging. Incompatibilities, data silos, and cybersecurity concerns can hinder the full realization of automation benefits.
- Job Displacement Concerns: Workers concerned about job security may resist the adoption of automated maintenance. While automation can augment human capabilities, it may also replace certain manual roles, requiring reskilling or redeployment efforts.
- Overreliance and Skill Erosion: Excessive reliance on automated systems can gradually erode human expertise and problem-solving skills in maintenance. This can create vulnerabilities if automated systems fail or encounter novel situations that require human intervention.
- Cybersecurity Risks: Automated maintenance systems, especially those connected to the internet or enterprise networks, can introduce new cybersecurity risks. Inadequate protection against unauthorized access, data breaches, or system manipulations can compromise maintenance effectiveness and asset integrity.
- Maintenance of Automation: Automated systems require regular maintenance, updates, and calibration to ensure optimal performance and reliability. Neglecting the maintenance of automation infrastructure can lead to cascading failures and defeat the purpose of automation.
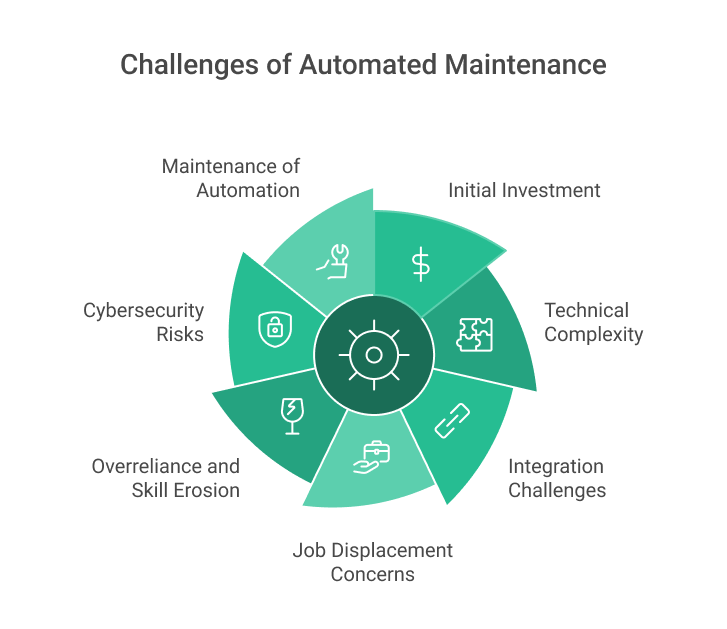
Get a Free WorkTrek Demo
Let's show you how WorkTrek can help you optimize your maintenance operation.
Try for free