What is Maintenance Backordering?
Maintenance Backordering refers to placing orders for maintenance, repair and operations (MRO) parts or materials not currently in stock or available from suppliers. Backordering occurs when the demand for a specific part or material exceeds the available on-hand inventory and supplier lead time.
When a stockout happens for a part needed for planned maintenance, repairs, or projects, the maintenance planner or storeroom manager must create a backorder to replenish inventory. The backorder initiates a purchase requisition or purchase order to the designated supplier with a request for expedited fulfillment. Until the backordered parts arrive, the associated maintenance work order is put on hold, delayed or de-prioritized.
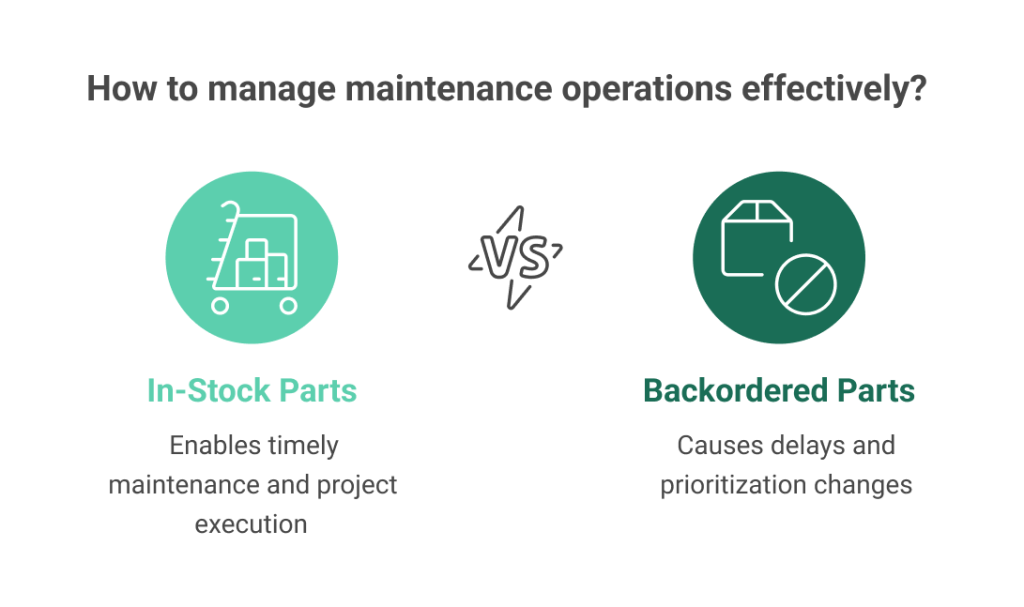
Backordering is an exception process in maintenance supply chain management, as the goal is to maintain optimal spare part inventory levels to avoid stockouts. However, the criticality and variability of maintenance parts demand, coupled with budget constraints, make some level of back ordering inevitable.
Effective back ordering processes aim to minimize the impact of stockouts on maintenance schedules and asset downtime.
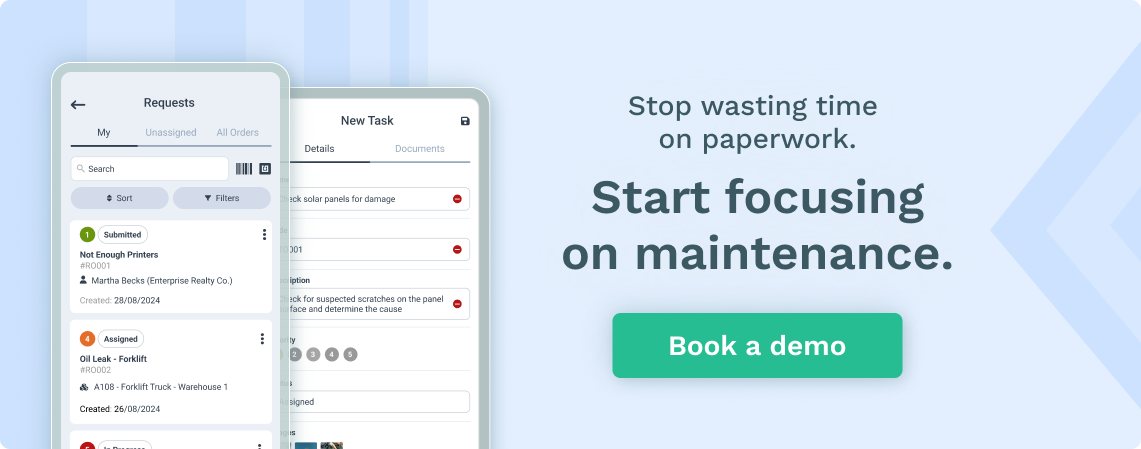
Key Steps in Maintenance Backordering
Key steps in maintenance back ordering include:
- Identifying stockouts: Flagging parts at or below reorder points and needed for scheduled work.
- Prioritizing backorders: Ranking backorders based on maintenance priority and asset criticality.
- Expediting purchases: Engaging suppliers to accelerate backorder fulfillment.
- Communicating status: Notifying stakeholders of backorder status and expected receipt dates.
- Adjusting plans: Rescheduling affected maintenance work based on backorder lead times.
- Receiving and kitting: Promptly receive, inspect, and stage backordered parts for use.
- Capturing root causes: Analyzing reasons for stockouts and adjusting stocking levels or reorder points.
Maintenance back ordering is a reactive process that organizations strive to minimize through proactive demand planning, inventory optimization, and close supplier collaboration.
Importance of Maintenance Backordering
While not ideal, back ordering is an important maintenance and reliability process for several reasons:
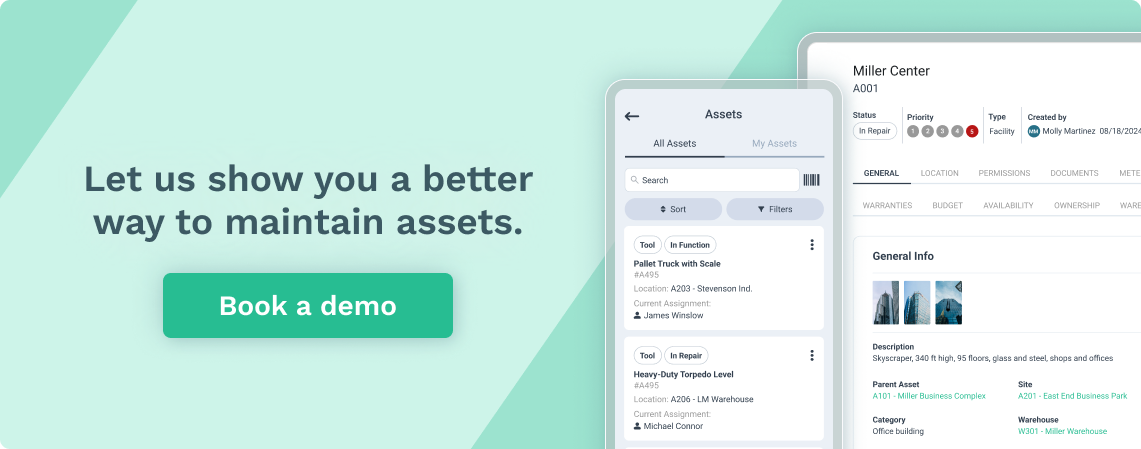
- Ensuring part availability: Backordering provides a systematic mechanism to procure out-of-stock parts needed for critical maintenance work. While not as timely as having parts in stock, back ordering ensures eventual part availability to complete required maintenance.
- Communicating shortages: Backordering highlights current spare part stockouts and their impact on maintenance operations. This visibility informs decisions about maintenance priorities, scheduling, and inventory investments.
- Reducing carrying costs: Backordering is a trade-off between part availability and inventory carrying costs. While some back ordering is disruptive, it can be less costly than overstocking expensive, slow-moving “insurance” spares. The right balance optimizes overall MRO inventory value.
- Strengthening supplier relationships: Frequent back ordering of the same parts provides objective data to negotiate with suppliers on lead times, consignment stock, or vendor-managed inventory arrangements. It can unlock supplier resources to improve maintenance part flow.
- Driving reliability improvements: Recurring backorders of parts for the same assets may justify reliability, maintainability, or supply chain improvement efforts. These include asset design changes, PM optimization, part standardization, or strategic sourcing.
Types of Maintenance Backordering
Maintenance Backordering can be categorized in several ways:
- Planned vs. Unplanned Backordering:
- Planned backordering covers parts consciously not stocked due to high cost, low demand or long lead time. Procurement initiates backorders per maintenance forecasts and agreements on acceptable lead times.
- Unplanned backordering happens when parts thought to be in stock are unexpectedly unavailable due to stockouts, stock discrepancies, or higher-than-forecast demand.
- Stocked vs. Non-Stocked Part Backordering:
- Stocked part backordering happens when inventory for parts normally kept in stock is temporarily exhausted. Demand temporarily exceeds the established reorder point and safety stock levels.
- Non-stocked part backordering occurs for parts not set up as regular stock items. These are typically expensive, slow-moving, or readily available parts not economical to keep in inventory.
- Priority-Based Backordering:
- Emergency backordering happens for parts needed for priority breakdowns, safety problems, or compliance issues. Premium prices and expediting costs are justified by the severe impact of downtime.
- Routine backordering covers parts for less urgent corrective or preventive maintenance work. Standard reordering and fulfilment processes are followed based on agreed lead times.
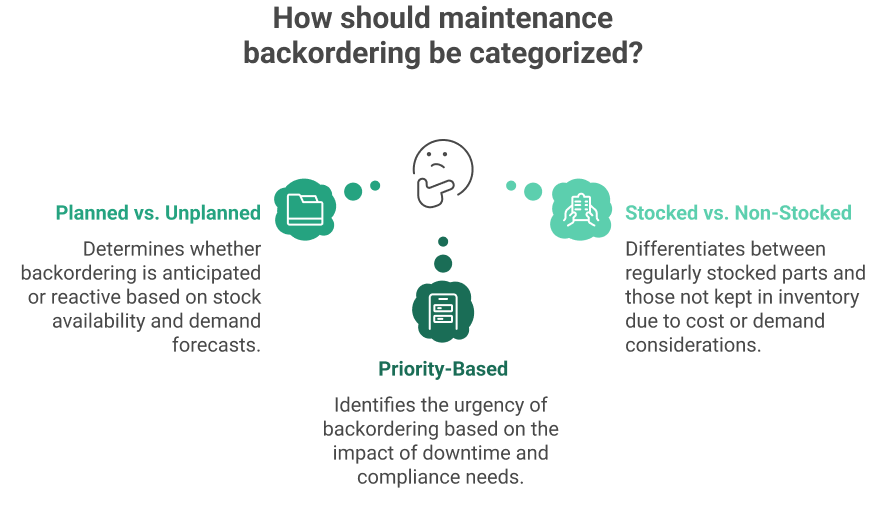
Tools to manage Maintenance Backorders
Below are product categories that can help you to manage maintenance backorders:
- Computerized Maintenance Management Systems (CMMS): CMMS include procurement and inventory management modules that identify part requirements, flag stockouts, and generate backorders linked to specific work orders.
- Enterprise Asset Management (EAM) Software: EAM systems provide more advanced MRO supply chain planning capabilities, including automatic reorder point calculations, vendor lead time tracking, and backorder prioritization and communication features.
- Inventory Optimization Tools: These specialized applications analyze part demand patterns, criticality, and supply chain variables to determine optimal stocking levels and minimize backorders while balancing carrying costs.
- e-Procurement Platforms: Web-based procurement portals automate placing backorders with suppliers, tracking order status, and expediting fulfillment through electronic data interchange (EDI) and supplier collaboration tools.
- Logistics Management Systems: These systems help manage complex, multi-echelon MRO supply chains, including internal and external backorder tracking, freight optimization, and warehouse management.
Get a Free WorkTrek Demo
Let's show you how WorkTrek can help you optimize your maintenance operation.
Try for free