What is Calendar-Based Maintenance?
Calendar-based maintenance is a specific type of preventive maintenance strategy where maintenance activities are scheduled to occur at fixed calendar intervals, such as daily, weekly, monthly, quarterly, semi-annually, or annually.
It represents one of the most straightforward approaches to maintaining equipment. The primary calendar-based scheduling mechanism is the passage of time as measured by calendar dates rather than equipment usage, operating hours, or condition monitoring.
Calendar-based maintenance operates on the principle that regular maintenance at predetermined calendar intervals will help prevent equipment failures, extend asset life, and maintain optimal performance.
Facility managers benefit from structured tools like maintenance calendars, which are usually part of a preventive maintenance task schedule. These calendars ensure that industrial equipment remains operational and efficient, reducing unexpected downtime and breakdowns.
Unlike usage-based maintenance (which triggers maintenance based on operating hours or cycles) or condition-based maintenance (which monitors the actual condition of assets), calendar-based maintenance follows a rigid schedule determined solely by the calendar, regardless of how much the equipment has been used or its current condition.
How Calendar-Based Maintenance Works
Calendar-based maintenance works by creating a schedule that outlines the specific maintenance tasks to be performed regularly. The schedule is typically based on the manufacturer’s recommendations or industry standards.
Maintenance teams use the schedule to plan and execute maintenance tasks, ensuring that equipment is properly maintained and functioning optimally. This maintenance management approach involves setting up a detailed calendar specifying when each task should be performed, whether daily, weekly, monthly, or annually.
By following this calendar-based approach, maintenance teams can systematically address all necessary tasks, ensuring that no aspect of equipment maintenance is overlooked.
Key Characteristics of Calendar-Based Maintenance:
Several defining features distinguish calendar-based maintenance:
- Fixed Calendar Intervals: Maintenance is performed according to a predetermined schedule, often based on calendar dates, operating hours, or production cycles. These intervals are typically established using manufacturer recommendations, industry standards, historical data, or regulatory requirements.
- Independence from Usage: Unlike condition-based approaches, calendar-based maintenance occurs regardless of the actual condition of the equipment, which can sometimes result in unnecessary maintenance on well-functioning equipment or insufficient maintenance on rapidly deteriorating assets.
- Standardized Schedule: Calendar-based maintenance follows standardized procedures and checklists, ensuring consistency and thoroughness in maintenance activities regardless of who performs them.
- Ease of Planning: Calendar-based schedules’ predictable nature allows for straightforward, long-term planning of maintenance resources, labor, and parts.
- Simplicity of Implementation: Calendar-based maintenance can be implemented without sophisticated monitoring equipment or complex decision-making frameworks.
- Regulatory Compliance: Many regulatory requirements specify calendar-based inspection and maintenance intervals, making this approach necessary for compliance in specific industries.
- Risk of Unnecessary Servicing: If not properly managed, calendar-based maintenance can lead to unnecessary servicing. This over-reliance on fixed schedules without considering actual equipment conditions can result in excessive maintenance actions, higher costs, and potential downtimes.
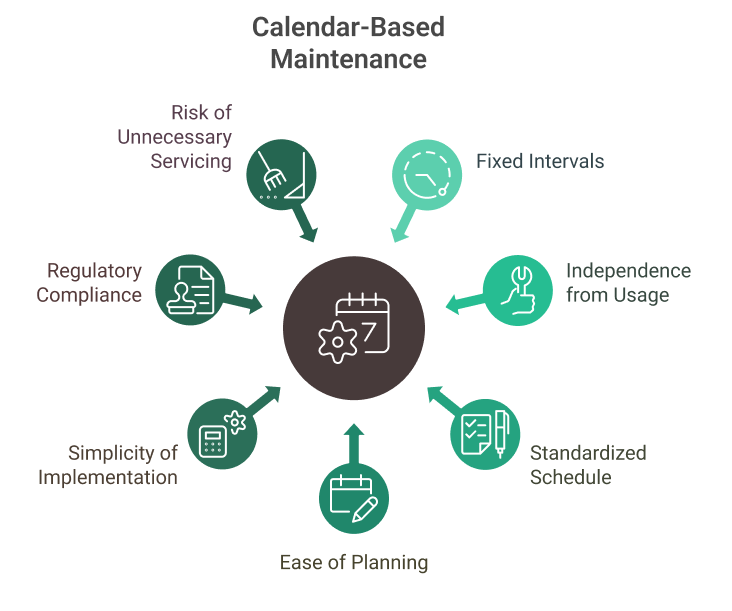
Benefits of Calendar-Based Maintenance
Calendar-based maintenance offers several benefits, including:
- Improved Equipment Reliability: Regular maintenance tasks help to prevent equipment failure and reduce downtime. By addressing potential issues before they escalate, maintenance teams can ensure that equipment remains operational and reliable.
- Increased Operational Efficiency: Maintenance teams can optimize equipment performance and reduce energy consumption by performing maintenance tasks at regular intervals. This leads to smoother operations and less disruption to production schedules.
- Cost Savings: Preventive maintenance can help to reduce maintenance costs by identifying and addressing potential issues before they become major problems. This proactive approach can extend the lifespan of equipment and reduce the need for expensive emergency repairs.
- Improved Safety: Regular maintenance tasks can help to identify and address potential safety hazards, reducing the risk of accidents and injuries. Ensuring that equipment is in good working order protects employees and the facility.
Types of Preventive Maintenance in Calendar-Based Maintenance:
Calendar-based maintenance can be categorized into various kinds based on frequency and purpose:
- Routine Maintenance: Regular, frequent tasks performed daily, weekly, or monthly (e.g., cleaning, lubrication, inspection).
- Periodic Maintenance: Less frequent but more comprehensive maintenance performed quarterly, semi-annually, or annually (e.g., overhauls, major inspections).
- Seasonal Maintenance: Maintenance activities aligned with seasons or weather conditions (e.g., HVAC system preparation for summer or winter).
- Regulatory-Driven Maintenance: Regulatory agencies or insurance providers require Inspections or maintenance activities at specific calendar intervals.
- Warranty-Preserving Maintenance: Maintenance is performed at intervals specified by equipment manufacturers to maintain warranty coverage.
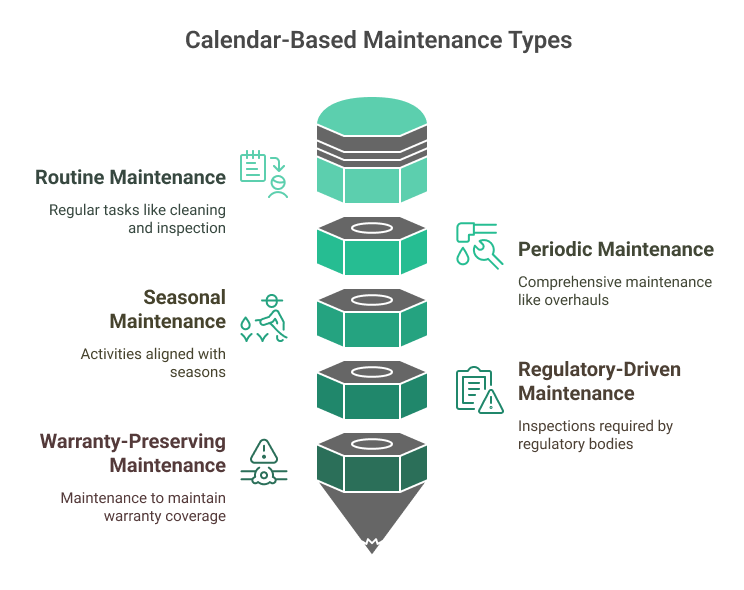
In addition to these types, predictive maintenance can complement calendar-based maintenance by using real-time data from IoT sensors to optimize servicing schedules, enhancing efficiency and extending equipment lifespan.
Equipment Best Suited for Calendar-Based Maintenance
Calendar-based maintenance is not equally effective for all types of equipment. It is most appropriate for:
- Equipment with Time-Based Degradation: Assets that deteriorate primarily due to the passage of time rather than usage, such as rubber components that harden or degrade with age, regardless of use.
- Weather or Season-Affected Equipment: Systems that need preparation or adjustment for seasonal changes, such as HVAC systems, irrigation systems, or outdoor equipment.
- Regulatory-Controlled Equipment: Assets subject to regulations requiring inspections or maintenance at specified calendar intervals, such as fire protection systems or emergency generators.
- Rarely Used Critical Equipment: Emergency systems or backup equipment must be ready to function when needed but may see little regular use, such as backup generators or fire pumps.
- Equipment with Minimal Usage Variation: Assets that operate consistently on a regular schedule, so calendar time roughly corresponds to operating time.
- Equipment with Time-Sensitive Consumables: Systems that use materials with calendar-based expiration dates, such as chemicals or certain filters.
- Simple Mechanical Systems: Basic equipment with well-understood failure mechanisms and minimal complexity.
Routine maintenance involves scheduling preventive maintenance tasks at regular intervals to ensure equipment reliability.
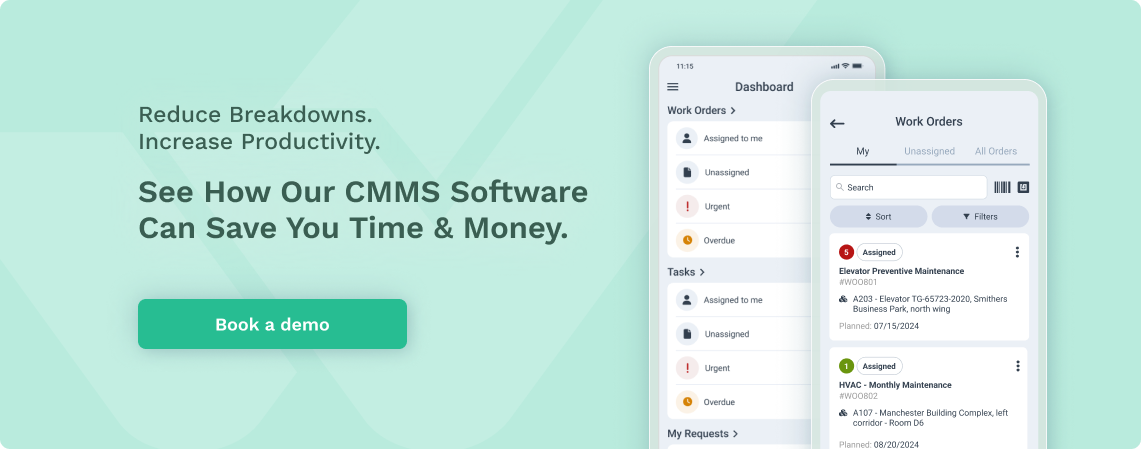
Examples of Equipment Well-Suited for Calendar-Based Maintenance
Calendar-based maintenance is well-suited for equipment that requires regular maintenance, such as:
- HVAC Systems: Regular maintenance tasks like filter changes and coil cleaning can help optimize system performance and reduce energy consumption. This ensures that the HVAC system operates efficiently and reliably throughout the year.
- Vehicles: Regular maintenance tasks, such as oil changes and tire rotations, can help extend the vehicle’s life and reduce maintenance costs. Keeping vehicles in good condition prevents breakdowns and ensures they operate safely.
- Machinery: Regular maintenance tasks, such as lubrication and inspection, can help to optimize equipment performance and reduce downtime. Properly maintained machinery operates more efficiently and is less likely to experience unexpected failures.
Best Practices for Calendar-Based Maintenance
Implementing an effective calendar-based maintenance program requires thoughtful planning and disciplined execution. Here are the key best practices:
1. Establish Appropriate Maintenance Intervals
The foundation of effective calendar-based maintenance is setting the right intervals for different maintenance activities:
- Consult Manufacturer Guidelines: Begin with the manufacturer’s recommended maintenance schedules, which are typically based on extensive testing and experience.
- Consider Environmental Factors: Adjust standard intervals based on environmental conditions such as humidity, temperature extremes, dust, or corrosive atmospheres that might accelerate deterioration.
- Balance Maintenance Costs and Risk: More frequent maintenance reduces risk but increases costs; less frequent maintenance saves immediate costs but may increase failure risk and total lifecycle costs.
- Incorporate Regulatory Requirements: Ensure compliance with industry regulations and insurance requirements that may specify minimum maintenance frequencies.
- Review Historical Data: Use failure history to refine maintenance intervals for specific equipment or systems in your operating environment.
2. Develop Comprehensive Maintenance Schedules
A well-organized maintenance calendar is essential for implementation:
- Create a Master Calendar: Develop a comprehensive annual maintenance calendar showing all scheduled maintenance activities across the organization.
- Distribute Workload Evenly: Avoid scheduling too many maintenance activities in the same period, which could overwhelm maintenance resources.
- Align with Operational Needs: Schedule maintenance during planned shutdowns, off-hours, or periods of lower activity when possible.
- Plan for Seasonal Considerations: Account for weather conditions and seasonal factors that might affect the ability to perform certain maintenance tasks.
- Establish Maintenance Windows: Designate specific periods for maintenance activities to minimize disruption to operations.
- Include Preparation Time: Build-in time for planning, parts procurement, and preparation before the maintenance dates.
3. Create Detailed Maintenance Procedures
For each maintenance task, develop standardized procedures that:
- Provide step-by-step instructions for completing each maintenance task
- Specify required tools, parts, materials, and safety equipment
- Include acceptance criteria or performance standards to verify successful completion
- Incorporate safety precautions and lockout/tagout procedures
- Address common issues or troubleshooting steps
- Include reference materials such as diagrams or photographs
4. Implement Effective Resource Management
Ensure that resources are available when needed for scheduled maintenance:
- Staff Planning: Schedule adequate qualified personnel for each maintenance activity.
- Parts and Materials Management: Ensure necessary parts and supplies are on hand for scheduled maintenance.
- Tool and Equipment Availability: Coordinate specialized tools or testing equipment for scheduled tasks.
- Contractor Coordination: Schedule outside contractors or specialists well in advance for specialized maintenance.
- Backup Planning: Have contingency plans for unexpected issues or emergencies that might disrupt scheduled maintenance.
5. Establish Clear Accountability and Communication
Ensure all stakeholders understand their roles and responsibilities:
- Assign Responsibility: Designate who is responsible for scheduling, performing, and verifying each maintenance task.
- Communicate the Schedule: Ensure all stakeholders (maintenance personnel, operations, management) know upcoming maintenance activities.
- Provide Advance Notice: Give adequate notice to operations about scheduled maintenance that might impact production or services.
- Document Completion: Record all required maintenance activities, findings, and follow-up actions.
- Review and Follow-Up: Regularly review completed maintenance to ensure it was correctly performed and address any issues identified.
6. Monitor Compliance and Effectiveness
Regular assessment of the maintenance program is crucial:
- Track Compliance: Monitor adherence to the maintenance schedule, documenting any missed or delayed maintenance.
- Analyze Failures: Investigate equipment failures to determine if they could have been prevented by adjusting maintenance intervals or procedures.
- Collect Performance Data: Gather data on equipment reliability, downtime, and maintenance costs to assess the effectiveness of the maintenance program.
- Conduct Regular Audits: Periodically audit the maintenance program to ensure it meets organizational needs and regulatory requirements.
- Solicit Feedback: Get input from maintenance personnel and equipment operators on the effectiveness of current maintenance practices.
7. Continuously Improve the Maintenance Program
A calendar-based maintenance program should evolve:
- Adjust Intervals Based on Experience: Refine maintenance frequencies based on equipment performance and failure history.
- Update Procedures: Modify maintenance procedures to incorporate new techniques, tools, or best practices.
- Integrate New Technologies: Consider adopting condition monitoring or other technologies to complement calendar-based maintenance.
- Review and Revise: Regularly review the entire maintenance program to identify opportunities for improvement.
- Benchmark Against Industry Standards: Compare your maintenance practices with industry and best practices.
Overcoming Challenges in Calendar-Based Maintenance
While calendar-based maintenance offers several benefits, there are also challenges to overcome. Some of the common challenges include:
- Ensuring That Maintenance Tasks Are Performed on Schedule: Maintenance teams must ensure that maintenance tasks are performed on schedule, without exception. This requires diligent planning and adherence to the maintenance calendar.
- Managing Maintenance Schedules: Maintenance teams must manage multiple maintenance schedules, ensuring all equipment is maintained correctly. This involves coordinating tasks and resources to avoid conflicts and ensure timely completion.
- Identifying and Addressing Potential Issues: Maintenance teams must identify and address potential issues before they become major problems. Regular inspections and monitoring are essential to catch early signs of wear or malfunction.
- Balancing Preventive and Corrective Maintenance: Maintenance teams must balance preventive and corrective maintenance tasks to ensure that equipment is properly maintained and functioning optimally. This requires a strategic approach to prioritize tasks and allocate resources effectively.
By understanding the benefits and challenges of calendar-based maintenance, maintenance teams can optimize their maintenance strategies and improve equipment reliability, operational efficiency, and cost savings.
Using a CMMS to Manage Calendar-Based Maintenance
A Computerized Maintenance Management System (CMMS) like WorkTrek significantly enhances the implementation and management of calendar-based maintenance. Here’s how a CMMS supports this maintenance strategy:
1. Automated Scheduling and Reminders
A CMMS transforms calendar-based maintenance from a manual process to an automated system:
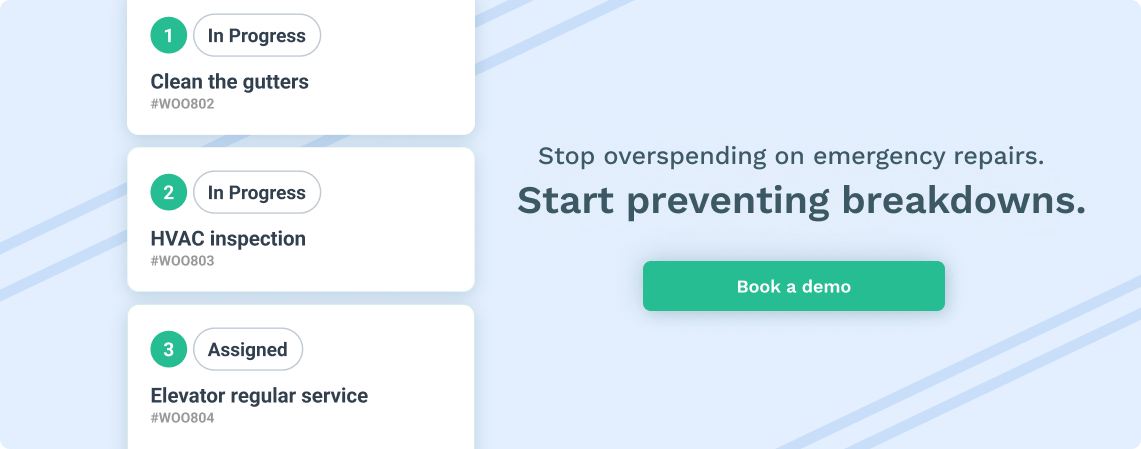
- Automated Work Order Generation: The CMMS automatically creates work orders based on predefined calendar schedules without manual intervention.
- Recurring Maintenance Setup: Establish maintenance tasks that repeat at specified calendar intervals (daily, weekly, monthly, quarterly, or yearly).
- Advanced Notification: Send automatic reminders about upcoming scheduled maintenance to supervisors and technicians.
- Schedule Visualization: Provide graphical calendar views of all scheduled maintenance activities for better planning and resource allocation.
- Flexible Scheduling Options: Allow maintenance scheduling by specific dates, days of the week, weeks of the month, or other calendar patterns.
- Holiday and Exception Handling: When scheduling recurring maintenance, account for holidays, facility shutdowns, or other special dates.
2. Maintenance Calendar Management
A CMMS provides powerful tools for managing the maintenance calendar:
- Master Maintenance Calendar: Maintain a comprehensive calendar showing all scheduled maintenance activities across the facility or organization.
- Calendar Filtering and Views: You can filter the maintenance calendar by equipment, location, technician, priority, or other criteria.
- Schedule Conflict Detection: Identify potential conflicts when multiple maintenance activities are scheduled for the same period.
- Resource Loading Visualization: View resource allocation across the calendar to ensure balanced workloads.
- Schedule Adjustment Tools: Easily reschedule or adjust maintenance dates while maintaining the overall pattern of recurring maintenance.
- Multi-Site Coordination: Coordinate maintenance schedules across multiple facilities or locations.
3. Equipment and Asset Management
A CMMS provides a centralized repository for all equipment information:
- Equipment Registry: Maintain detailed asset records, including specifications, location, and critical information.
- Maintenance History: Track all maintenance activities performed on each piece of equipment over its entire lifecycle.
- Equipment Hierarchies: Organize equipment into systems and subsystems to manage complex maintenance relationships.
- Documentation Storage: Store equipment manuals, procedures, drawings, and other documentation for easy access.
- Warranty Tracking: Monitor warranty status and requirements for maintenance to maintain coverage.
- Equipment-Specific Schedules: Assign different maintenance frequencies to different types of equipment based on criticality and requirements.
4. Work Order Management
A CMMS streamlines the complete work order lifecycle:
- Standardized Work Orders: Create template work orders for recurring calendar-based maintenance tasks.
- Detailed Task Instructions: Include comprehensive procedures, checklists, and safety information in work orders.
- Parts and Materials Requirements: Specify all parts, materials, and tools needed for each maintenance task.
- Labor Planning: Assign appropriate technicians based on skills, certifications, and availability.
- Work Order Prioritization: Establish priority levels for different maintenance activities.
- Completion Tracking: Monitor the status of all work orders from creation to completion.
- Mobile Access: Provide technicians with mobile access to work orders in the field for real-time updates and documentation.
5. Compliance and Documentation
A CMMS ensures regulatory compliance and thorough documentation:
- Compliance Tracking: Monitor adherence to required maintenance schedules for regulatory compliance.
- Automatic Documentation: Generate and store complete records of all maintenance activities.
- Electronic Signatures: Capture approvals and verifications for completed maintenance tasks.
- Audit Trails: Maintain a detailed history of all changes to maintenance schedules and work orders.
- Inspection Checklists: Include regulatory inspection requirements in maintenance procedures.
- Certificate Management: Track certifications and required recertification dates for equipment.
- Reporting Capabilities: Generate reports for regulatory agencies or insurance providers demonstrating compliance with required maintenance.
6. Data Analysis and Continuous Improvement
A CMMS enables data-driven optimization of calendar-based maintenance:
- Performance Metrics: Track key performance indicators such as schedule compliance, mean time between failures, and maintenance costs.
- Failure Analysis: Record and analyze failure modes to identify patterns that might suggest needed changes to maintenance schedules.
- Cost Tracking: Monitor labor hours, part costs, and downtime associated with calendar-based maintenance.
- Schedule Optimization: Use actual performance data to optimize maintenance intervals.
- Trend Analysis: Identify patterns in equipment performance and maintenance requirements over time.
- Dashboards and Reporting: Generate visual representations of maintenance performance for management review.
7. Best Practices for CMMS in Calendar-Based Maintenance
To maximize the benefits of a CMMS for calendar-based maintenance:
- Start with a Clean Calendar: Implement a well-thought-out maintenance calendar for all equipment and requirements.
- Standardize Maintenance Classifications: Develop consistent categorization for maintenance types, priorities, and frequencies.
- Build a Comprehensive Asset Database: Ensure all equipment is properly cataloged with accurate information before implementing schedules.
- Develop Templates: Create standardized templates for common maintenance tasks to ensure consistency.
- Establish Clear Workflows: Define processes for work order management from creation through verification and closure.
- Train All Users: Provide thorough training for all personnel who will interact with the CMMS.
- Start Simple and Expand: Begin with basic calendar-based schedules and add complexity gradually as users become familiar with the system.
- Integrate with Other Systems: Connect the CMMS with enterprise resource planning (ERP), inventory management, or other relevant systems.
- Regular System Reviews: Periodically review CMMS configuration to ensure it continues to meet the organization’s needs.
8. Special Considerations for Calendar-Based Maintenance in a CMMS
Calendar-based maintenance has some unique aspects in a CMMS:
- Date Calculation Methods: Understand how the CMMS calculates the next due dates for recurring maintenance (e.g., fixed intervals vs. based on completion date).
- Schedule Flexibility: Determine acceptable windows for completing maintenance tasks (e.g., ±7 days from the scheduled date).
- Maintenance Grouping: Consider grouping maintenance tasks with similar frequencies to improve efficiency.
- Season-Specific Tasks: Configure special handling for seasonal maintenance only during specific months.
- Notification Configuration: Set up a notification hierarchy to ensure that overdue maintenance receives appropriate attention.
- Schedule Recovery: Establish procedures for getting back on schedule when maintenance is delayed.
Get a Free WorkTrek Demo
Let's show you how WorkTrek can help you optimize your maintenance operation.
Try for free