What is Condition Monitoring?
Condition monitoring refers to continuously or periodically collecting data about an asset’s operational conditions, such as temperature, vibration, noise, or fluid levels, to detect early signs of wear, damage, or potential failure. This approach allows maintenance teams to monitor equipment health in real time and plan maintenance activities based on actual conditions rather than predefined schedules.
Condition monitoring is a powerful technique that allows maintenance teams to closely monitor critical equipment’s health and performance, enabling them to detect potential issues before they lead to costly breakdowns. At its core, condition monitoring involves the continuous or periodic measurement and analysis of key parameters that indicate the condition of a machine or system. These parameters can include vibration, temperature, pressure, oil analysis, and electrical signals.
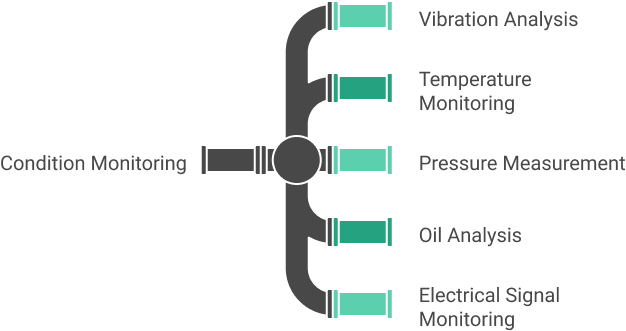
By collecting and analyzing this data over time, maintenance professionals can establish a baseline of normal operation for each piece of equipment. Deviations from this baseline can be an early warning sign of developing problems, such as wear, misalignment, or lubrication issues. This allows the maintenance team to investigate further and take proactive steps to address the issue before it escalates into a major failure.
Benefits of Condition Monitoring
One key benefit of condition monitoring is that it enables a shift from reactive to predictive maintenance. Instead of waiting for equipment to break down and then scrambling to repair it, maintenance teams can use the insights gained from condition monitoring to plan and schedule maintenance activities in advance.
This helps minimize unplanned downtime and allows maintenance at the most convenient and cost-effective times, such as during scheduled shutdowns.
Condition monitoring delivers critical benefits to maintenance organizations:
Early Detection: Identifies equipment issues before failure through vibration analysis, oil testing, thermography, and performance monitoring.
Cost Reduction: This minimizes unplanned downtime, emergency repairs, and catastrophic failures, as well as spare parts inventory and labor costs.
Reliability Improvement: Extends equipment life through optimized maintenance timing. Increases asset availability and production efficiency.
Data-Driven Decisions: Provides real-time equipment health data, enabling predictive maintenance strategies and better resource allocation.
Safety Enhancement: Reduces accident risks by identifying hazardous conditions early. Supports compliance with safety regulations.
Improved ROI: ROI typically shows a 10-fold return through reduced maintenance costs and improved equipment reliability.
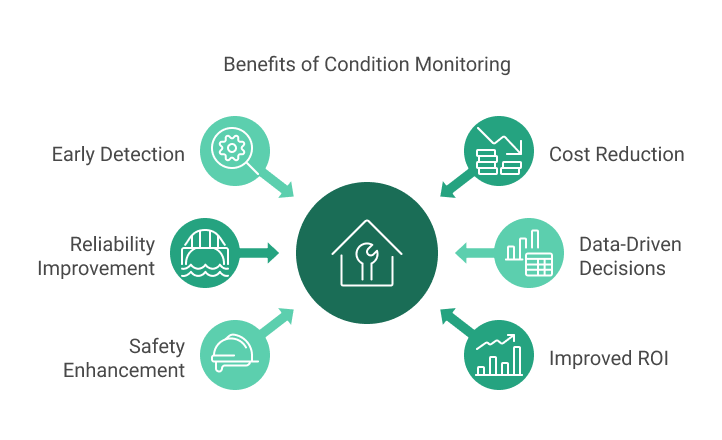
Tools for Condition Monitoring
To make the most of condition monitoring, maintenance organizations need to have the right tools and technologies in place. Some of the most commonly used tools for condition monitoring include:
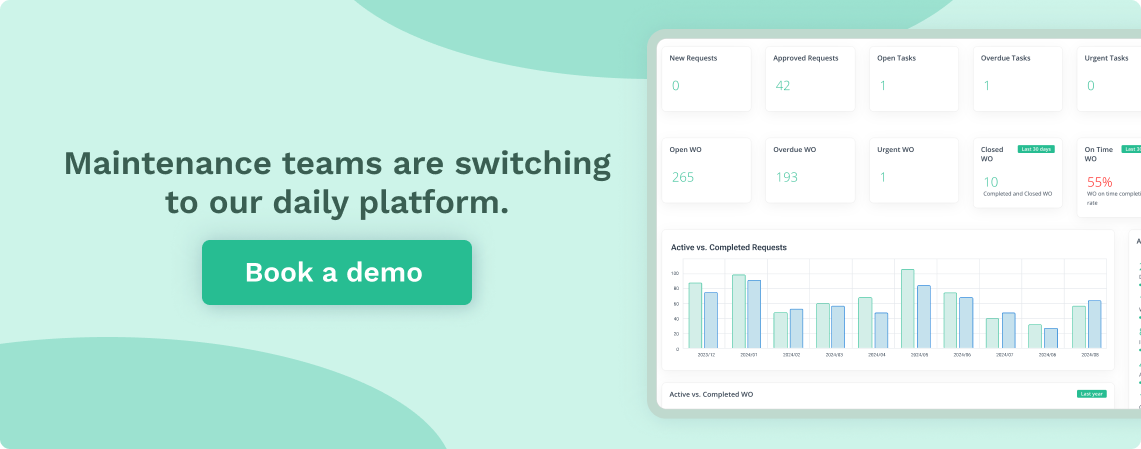
Vibration Analyzers
Vibration analyzers measure and analyze vibrations in rotating machinery. By detecting changes in vibration patterns, these tools help identify imbalances, misalignments, and wear before they lead to equipment failure.
Thermography Cameras
Thermography cameras, also known as infrared cameras, detect heat patterns in equipment. Excessive heat can indicate potential issues such as electrical faults, bearing failures, or friction problems, enabling maintenance teams to address them proactively.
Ultrasonic Detectors
Ultrasonic detectors pick up high-frequency sounds often emitted by equipment defects, such as leaks, electrical discharges, or failing bearings. These detectors allow technicians to identify problems that might not be audible to the human ear.
Oil Analysis Kits
Oil analysis involves sampling and analyzing lubricants from machinery. Changes in oil properties, such as contamination or chemical breakdown, can indicate internal wear or the presence of foreign particles, signaling the need for maintenance.
Pressure and Temperature Sensors
These sensors continuously monitor equipment pressure and temperature levels. Deviations from normal operating ranges can indicate developing issues, providing an early warning system for maintenance teams.
Condition Monitoring Software
Specialized software collects, analyzes, and visualizes condition monitoring data. These tools help maintenance teams interpret complex data trends, making planning and executing maintenance activities easier.
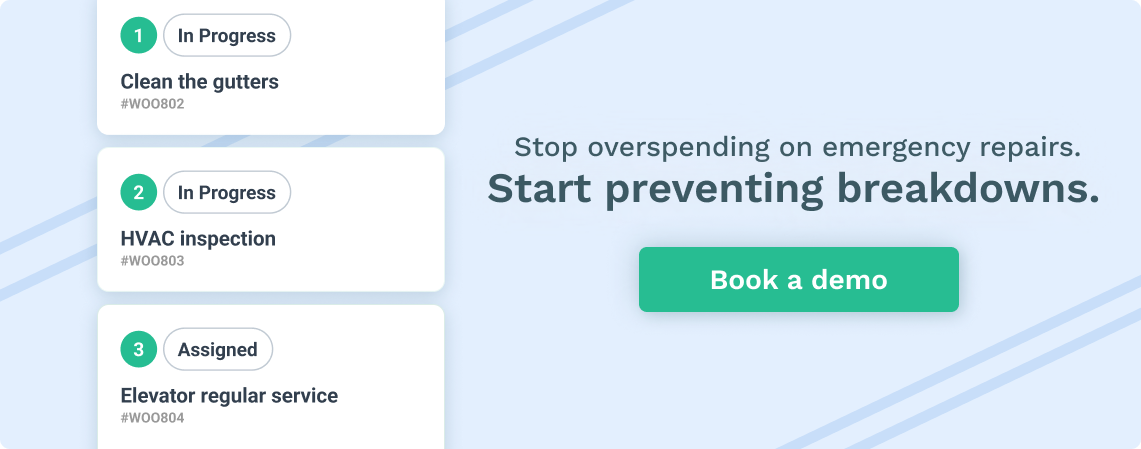
How can maintenance organizations use Condition Monitoring?
In addition to these tools, maintenance teams also need software platforms to collect, store, and analyze the data generated by condition monitoring. These platforms can range from simple spreadsheets to sophisticated enterprise asset management (EAM) systems that integrate with other business systems.
By leveraging condition monitoring and the right tools, maintenance organizations can optimize their maintenance strategies in several ways. First, they can prioritize maintenance activities based on the actual condition of equipment rather than relying on fixed schedules or guesswork. This helps ensure that maintenance resources are allocated where needed most.
Second, condition monitoring can help extend the equipment’s life by detecting and addressing issues early before they cause significant damage. Over time, this can lead to significant cost savings by reducing the need for expensive repairs or replacements.
Finally, by reducing unplanned downtime and increasing overall equipment reliability, condition monitoring can help maintenance organizations contribute to the bottom line by improving production efficiency and reducing operational costs.
In conclusion, condition monitoring is a valuable approach that can help maintenance teams to keep equipment running smoothly, avoid costly failures, and optimize their maintenance strategies. By investing in the right tools and technologies and using the insights gained from condition monitoring to drive decision-making, maintenance organizations can deliver significant value to their businesses.
Get a Free WorkTrek Demo
Let's show you how WorkTrek can help you optimize your maintenance operation.
Try for free