What is Economic Order Quantity?
EOQ is an inventory management formula used to determine the ideal order quantity that minimizes inventory costs, such as ordering, holding, and stockout costs. EOQ aims to find the perfect balance between ordering too frequently, which increases ordering costs, and holding excessive inventory, which raises holding costs.
The EOQ formula considers factors like the demand rate, cost per order, and carrying cost per unit. Businesses can reduce unnecessary expenses and optimize inventory levels by calculating the most cost-effective order size.
Using EOQ helps companies maintain a consistent supply of products while minimizing the overall inventory management cost. It primarily benefits businesses with steady demand patterns and reliable lead times.
By applying the EOQ model, organizations can improve cash flow, reduce storage expenses, and ensure they have enough stock to meet customer needs without excessive overstock.
EOQ Calculator
EOQ = √((2DS)/H)
Optimal Order Quantity: 224 units
Why is it Important to Maintenance Organizations?
The Economic Order Quantity (EOQ) is a critical concept for maintenance organizations as it directly impacts their operations, finances, and efficiency.
Below are key reasons why EOQ matters:
1. Cost Optimization
EOQ helps minimize total inventory costs by balancing ordering and holding costs. Each purchase order has associated administrative costs, such as maintaining equipment while storing excess inventory, which incurs warehousing expenses, insurance, and opportunity costs. Using EOQ, maintenance managers can determine the most cost-effective quantity to order, reducing overall operational expenses.
2. Material Management
Maintenance organizations need to balance having enough spare parts and materials without tying up excessive capital in inventory. EOQ helps optimize order quantities by considering storage costs, order processing costs, and demand patterns. Critical components like bearings or filters need to be available when needed, but ordering too many increases carrying costs and risks obsolescence.
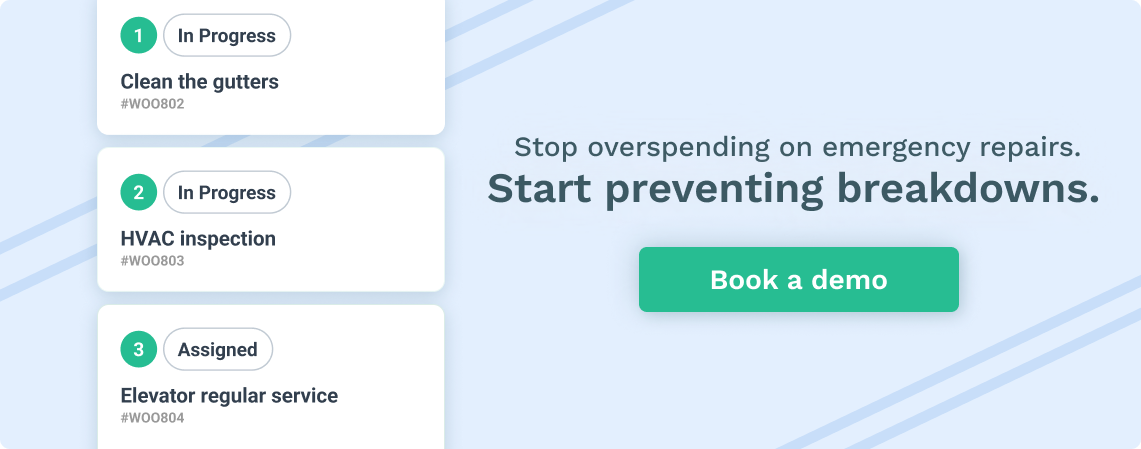
3. Storage Space Utilization
Maintenance facilities often have limited storage space. EOQ calculations help determine optimal order sizes for available storage while ensuring adequate stock levels. This is particularly important for bulky items like motors, belts, or lubricants that consume significant warehouse space.
4. Labor Efficiency
Proper EOQ implementation reduces the time staff spends on inventory management. Instead of frequently placing small orders or dealing with excess inventory, maintenance teams can focus on their core responsibilities. This leads to better resource allocation and improved maintenance efficiency.
5. Service Level Management
EOQ helps maintain appropriate service levels by ensuring critical parts are available when needed. Stockouts can lead to extended equipment downtime, production losses, and emergency purchasing at premium prices. Maintenance organizations can better meet their service level agreements and equipment availability targets by optimizing order quantities.
6. Supplier Relationships
Using EOQ helps establish consistent ordering patterns with suppliers. Regular, predictable orders often lead to better pricing, improved delivery terms, and stronger supplier relationships. This can result in priority treatment during critical situations and better vendor service.
7. Budgeting and Financial Planning
EOQ provides a systematic approach to predicting and controlling inventory investments. This helps maintenance organizations better forecast their budget requirements, plan cash flow, and justify inventory-related expenses to management. It also aids in identifying opportunities for cost reduction and efficiency improvements.
8. Risk Management
EOQ calculations can incorporate factors like lead time variability and the critical nature of parts. This helps maintenance organizations maintain appropriate safety stock levels for critical components while minimizing inventory for less crucial items. This risk-based approach ensures business continuity while optimizing inventory investment.
Challenges of EOQ
While economic order quantity (EOQ) offers numerous benefits to maintenance organizations, several challenges must be considered.
Data Accuracy
One significant challenge is the accuracy of data inputs. EOQ calculations rely on precise demand forecasts, ordering, and holding costs. Inaccurate or outdated data can lead to suboptimal order quantities and potential inventory issues. Additionally, EOQ assumes a constant and known demand rate, which may not always be true in maintenance environments where demand can be sporadic or unpredictable.
Complex Inventory Management and Inventory Tracking
Another challenge is the complexity of inventory management in maintenance organizations. EOQ is primarily designed for individual items, but maintenance inventory often consists of various parts and supplies with varying demand patterns and lead times. Managing multiple EOQ calculations for different items can be time-consuming and resource-intensive. Moreover, EOQ does not account for interdependencies between items, such as when certain parts are required together for a specific maintenance task.
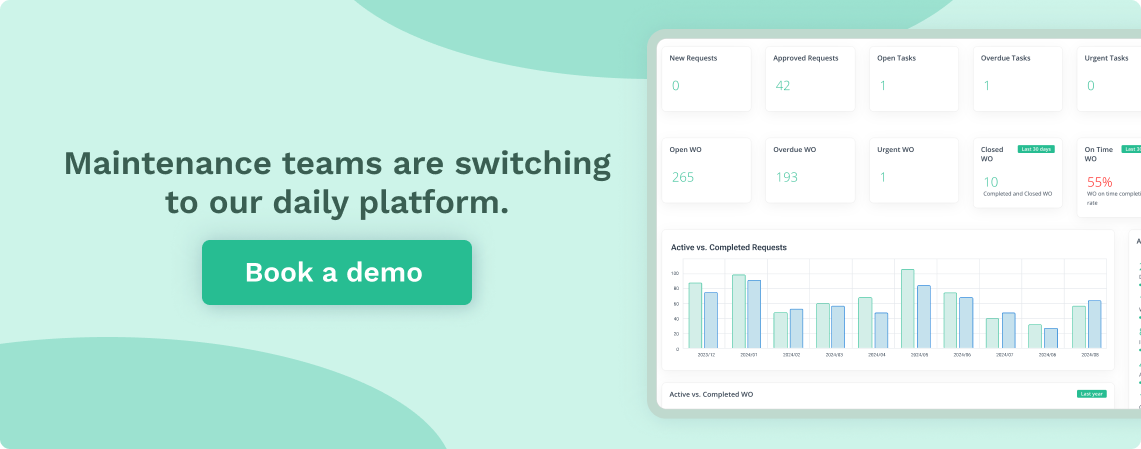
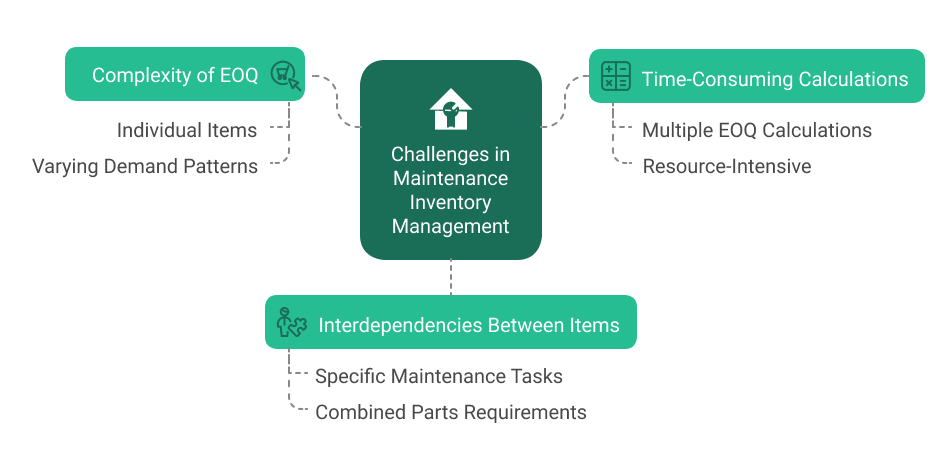
Implementing EOQ also requires a robust inventory tracking system and regular monitoring. Maintenance organizations must have the necessary technology and processes in place to accurately track inventory levels, usage rates, and reorder points. Without proper tracking and monitoring, the benefits of EOQ may not be fully realized, and the risk of stockouts or overstocking increases.
Cost Changes
Furthermore, EOQ assumes the cost of ordering and holding inventory remains constant. However, these costs can fluctuate due to various factors, such as changes in supplier prices, storage costs, or transportation fees. Maintenance organizations must periodically review and update their EOQ calculations to ensure they remain accurate and reflect the current cost structure.
Focus on Critical Parts
Lastly, EOQ focuses primarily on optimizing inventory costs and may not fully consider other important factors in maintenance organizations, such as the criticality of certain parts or the impact of stockouts on equipment downtime. Balancing cost optimization with the need for high availability and reliability of maintenance parts and supplies can be a delicate challenge.
To overcome these challenges, maintenance organizations should invest in robust inventory management systems, regularly review and update their EOQ parameters, and consider complementary inventory management techniques such as safety stock, vendor-managed inventory, or just-in-time delivery. By doing so, they can harness the benefits of EOQ while mitigating the associated challenges and ensuring optimal inventory management practices.
Get a Free WorkTrek Demo
Let's show you how WorkTrek can help you optimize your maintenance operation.
Try for free