What is Equipment Lifcycle?
The equipment lifecycle refers to the various stages an asset or piece of equipment goes through, from acquisition to disposal. These stages typically include acquisition, installation, operation, maintenance, and end-of-life (disposal or replacement). Understanding and managing equipment lifecycles is crucial for effective asset management, as it helps organizations optimize maintenance strategies, predict costs, and plan for future investments.
The first phase of the lifecycle is acquisition, where equipment is purchased based on business needs. After installation, the equipment enters its operational phase, during which it is used for its intended purpose.
During this period, the equipment requires regular maintenance, including preventive, predictive, and corrective tasks, to ensure reliability and efficiency.
As the equipment ages, the need for maintenance typically increases, and its performance may begin to degrade. This is all part of the asset lifecycle.
At this point, organizations must assess whether to maintain or replace the asset with a newer, more efficient model. The final stage of the lifecycle is disposal, where the equipment is decommissioned, sold, or recycled.
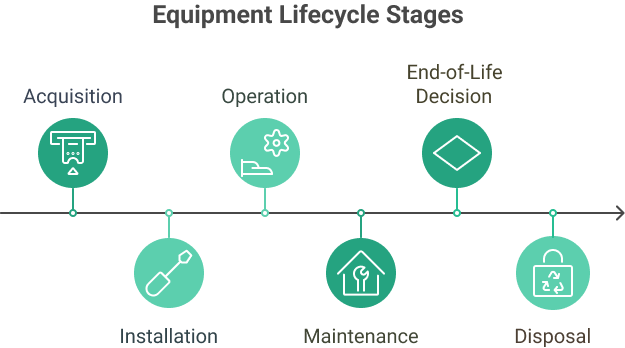
By tracking the equipment lifecycle, organizations can make informed decisions about maintenance schedules, budgeting, and asset replacement, ultimately reducing costs and ensuring reliable operations.
Definition of Equipment Lifecycle
The equipment lifecycle refers to the entire lifespan of a physical asset, from its initial planning and acquisition to its eventual disposal or retirement. This lifecycle encompasses various stages, including planning, procurement, operation, maintenance, and disposal, each playing a crucial role in maximizing the asset’s usefulness and efficiency.
This helps optimize equipment utilization and improve the asset life cycle.
Understanding the equipment lifecycle is essential for organizations to manage their assets effectively and ensure that each piece of equipment delivers optimal performance throughout its lifespan.
Importance of Equipment Lifecycle Management
Effective equipment lifecycle management is vital for businesses to optimize operations, reduce costs, and improve productivity. By implementing a well-structured strategy, organizations can extend the lifespan of their equipment, minimize downtime, and ensure compliance with regulatory requirements.
Moreover, equipment lifecycle management enables businesses to make informed decisions about equipment procurement, maintenance, and disposal, ultimately improving operational efficiency and profitability. This strategic approach helps forecast equipment needs, budget future investments, and maintain high operational readiness.
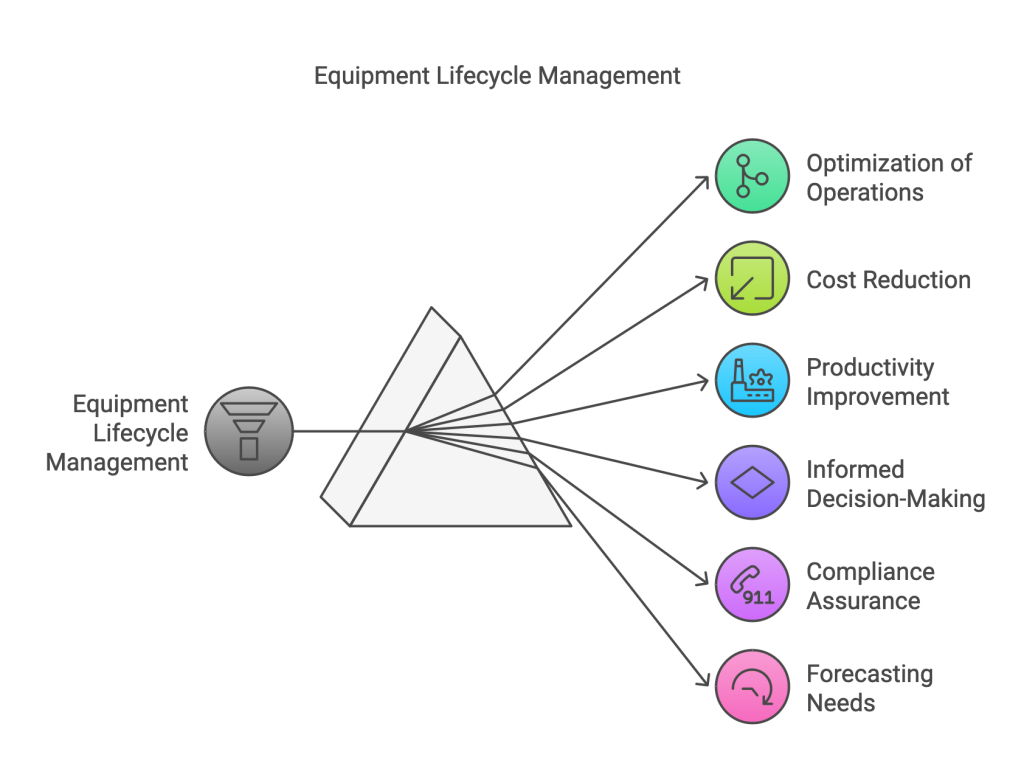
Equipment Lifecycle Steps
Below are the steps in for equipment lifecycle management:
Equipment Management Planning & Acquisition
Requirement Analysis
This initial phase sets the foundation for equipment success. Organizations must conduct thorough needs assessments to determine specific requirements, considering current and future operational demands.
Technical specifications should align with business objectives while maintaining realistic budget constraints.
Additionally, new equipment should be considered during the requirement analysis to ensure alignment with business strategy and operational efficiency.
Key Points
- Define performance needs
- Set reliability targets
- Establish budget constraints
- List environmental requirements
Procurement Actions
The procurement process involves detailed vendor evaluations, focusing on reliability history, support capabilities, and total cost of ownership rather than just purchase price. Critical considerations include maintenance support infrastructure, spare parts availability, and warranty terms. Additionally, effective equipment tracking is essential to monitor the location and usage of machinery, ensuring efficient procurement and lifecycle management.
Key Points
- Review vendor qualifications
- Compare technical specifications
- Evaluate maintenance support
- Check parts availability
- Negotiate warranty terms
Site Preparation
Site preparation requirements must be identified early, including utility needs, space constraints, and environmental conditions.
Site Preparation Key Points:
- Confirm site requirements
- Plan utility connections
- Schedule installation
- Order initial spare parts
Success in this phase depends on thorough documentation of requirements, clear communication with stakeholders, and careful evaluation of all technical and commercial aspects. Organizations should develop a comprehensive implementation plan before finalizing purchase decisions, ensuring all necessary resources and support systems are in place.
2. Implementation
Installation
Implementation transforms planning into operational reality by carefully executing installation and setup procedures. This phase requires strict adherence to manufacturer specifications while establishing equipment maintenance protocols and training programs. Key activities include site preparation, equipment installation, initial calibration, and performance verification.
Key Points
- Follow manufacturer guidelines
- Complete safety checks
- Perform initial calibration
- Document baseline readings
- Verify performance metrics
Documentation
Documentation systems must be established, including maintenance procedures, safety protocols, and equipment specifications. Training programs should cover operational and maintenance aspects, ensuring staff competency before equipment deployment.
The implementation team must verify all safety systems, document baseline readings, and establish performance metrics for ongoing monitoring. Documenting equipment management practices is essential for effective lifecycle management. It provides valuable insights into the economic impact of equipment and aligns business processes with the equipment lifecycle.
Key Points
- Create equipment records
- Write maintenance procedures
- Develop safety protocols
- List critical spares
- Establish PM schedules
Training & Documentation
Success factors include proper resource allocation, clear communication channels, and thorough documentation of all setup procedures. Quality control measures should be implemented throughout this phase to ensure all specifications are met and the equipment is ready for operational use.
Key Points
- Train operators
- Train maintenance staff
- Document procedures
- Verify competencies
- Test emergency responses
3. Operation
The operational phase represents the primary value-delivery period of the equipment lifecycle. This phase focuses on maintaining optimal performance through structured maintenance programs and continuous monitoring.
Daily Activities
Daily activities include operating equipment, monitoring performance, and executing preventive maintenance tasks. Maintenance strategies should combine preventive, predictive, and corrective approaches based on equipment criticality and failure modes.
Monitor Equipment Performance
Key performance indicators must be tracked regularly, including equipment performance data, reliability metrics, downtime analysis, and maintenance costs.
Document and Record Issues
Operators and maintenance staff must follow established procedures while documenting deviations or issues. Spare parts inventory requires active management to ensure availability without excessive carrying costs.
Perform Inspections and Track Metrics
Success during this phase depends on consistent program execution, accurate record-keeping, and prompt response to performance issues. Regular reviews of maintenance effectiveness help identify opportunities for program optimization and cost reduction.
Key Points
- Monitor performance
- Record issues
- Perform inspections
- Track metrics
- Follow maintenance schedule
Optimization and Predictive Maintenance
The optimization phase focuses on continuously improving equipment performance and reliability throughout the equipment’s lifecycle. Organizations identify opportunities for enhancement through analysis of operational data, maintenance history, and cost information.
Key activities include reviewing failure patterns, analyzing maintenance effectiveness, and improving reliability.
This phase requires a data-driven approach to decision-making, using performance metrics to justify and validate changes. Optimization efforts might include adjusting maintenance intervals, upgrading components, or improving operational procedures. Energy efficiency improvements and cost reduction initiatives are common focus areas.
Success factors include practical data analysis, clear improvement objectives, and measurable results. Organizations should maintain a structured approach to implementing changes, ensuring each modification is appropriately evaluated and documented.
Regular reviews of optimization efforts help ensure sustained improvements in equipment performance.
Challenges in Equipment Management
Equipment management poses several challenges, including manual work, managing equipment costs and expenses, scheduling maintenance, and tracking equipment. These challenges can lead to inefficiencies, increased costs, and reduced productivity.
For instance, manual equipment tracking can result in errors and omissions, making it challenging to maintain accurate records and track equipment performance. Additionally, scheduling maintenance without a structured plan can lead to unexpected equipment failures and downtime.
Addressing these challenges requires a systematic approach to equipment management, incorporating best practices and leveraging technology to streamline processes.
The Role of Technology in Equipment Lifecycle
Technology plays a significant role in equipment lifecycle management, enabling businesses to streamline operations, improve efficiency, and reduce costs.
Equipment lifecycle management software, for instance, provides a centralized platform for tracking equipment performance, scheduling maintenance, and managing inventory. This software allows for real-time monitoring and data analysis, facilitating proactive maintenance and reducing the risk of equipment failures.
Additionally, predictive maintenance, remote maintenance, and digitized equipment management transform how businesses manage their equipment.
Predictive maintenance uses data analytics to predict equipment failures before they occur, allowing for timely interventions.
Remote maintenance enables technicians to diagnose and fix issues without being physically present, saving time and resources.
By leveraging these technological advancements, businesses can make data-driven decisions, optimize operations, and enhance overall equipment performance.
5. End-of-Life
The final phase determines equipment disposition through careful analysis of multiple factors. Organizations must evaluate current performance, maintenance costs, and reliability trends against replacement options.
Obsolescence risk, spare parts availability, and support requirements factor into decision-making. Planning for equipment retirement includes decommissioning procedures, environmental considerations, and knowledge transfer to new systems.
Cost analysis should compare continued maintenance against replacement options, considering direct and indirect costs. The retirement process must address environmental regulations, safety requirements, and proper disposal procedures.
Success in this phase requires early planning, thorough documentation, and practical knowledge transfer. Organizations should capture lessons learned to improve future equipment selection and management. The transition to replacement equipment must be carefully managed to minimize operational impact and ensure continued business performance data.
Get a Free WorkTrek Demo
Let's show you how WorkTrek can help you optimize your maintenance operation.
Try for free