What is an Equipment Maintenance Strategy?
Equipment maintenance strategies refer to organizations’ systematic approaches to preserve their equipment’s functionality, reliability, and lifespan. These strategies involve planning, implementing, and optimizing various maintenance activities to prevent equipment failure, reduce downtime, and ensure operational efficiency.
Maintenance strategies are tailored to organizational needs, equipment criticality, and resource availability. They encompass a spectrum of practices, from reactive repairs to predictive maintenance enabled by advanced technologies.
Core Maintenance Approaches
Preventive Maintenance (PM)
A preventive maintenance strategy consisting of regularly scheduled inspections, adjustments, cleaning, lubrication, and parts replacement performed at predetermined intervals to prevent equipment failure. PM tasks are time or usage-based and designed to maintain equipment reliability, extend operational life, and reduce unplanned downtime. The strategy includes systematic equipment inspections, component replacements before failure, routine calibrations, and performance testing. PM programs typically use maintenance schedules based on manufacturer recommendations, historical data, and operational experience. While potentially resulting in some over-maintenance, PM remains fundamental to equipment reliability and lifecycle management.
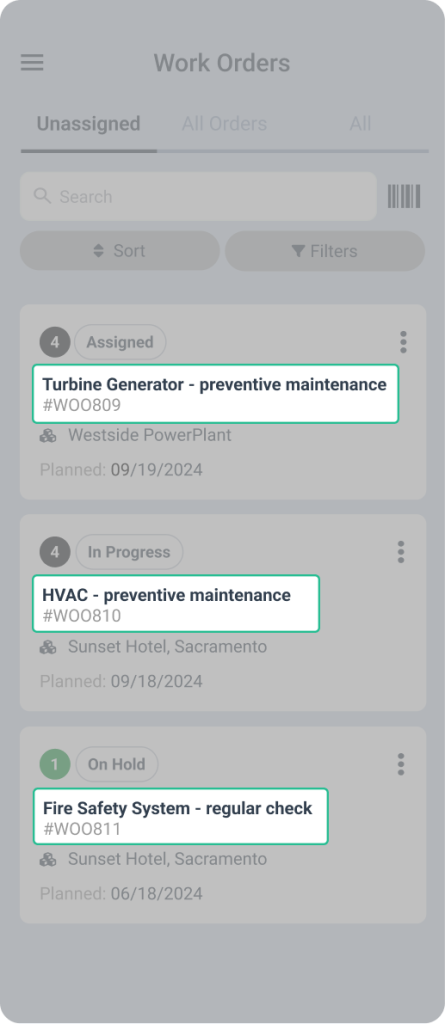
- Key Components: Fixed schedules, standard procedures, routine inspections
- Example: Monthly bearing lubrication, quarterly belt replacement
- Benefits: Reduces unexpected failures, extends equipment life
- Limitations: May perform unnecessary maintenance, labor-intensive
Predictive Maintenance (PdM)
PdM is a condition-based maintenance strategy that uses advanced monitoring techniques and data analysis to detect potential equipment failures before they occur. It employs specialized tools like vibration analysis, thermography, oil analysis, and ultrasound testing to assess equipment conditions in real-time. This approach enables maintenance based on actual equipment conditions rather than fixed schedules, optimizing component life and reducing unnecessary maintenance. PdM allows organizations to plan repairs proactively, minimize downtime, and maximize maintenance efficiency through data-driven decisions.
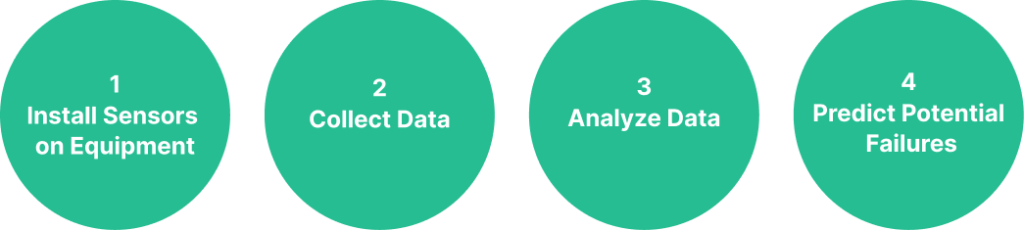
- Key Tools: Vibration analysis, thermography, oil analysis, ultrasound
- Example: Using vibration readings to predict bearing failure
- Benefits: Maximizes component life, reduces unnecessary maintenance
- Limitations: Higher initial investment, requires specialized training
Corrective Maintenance (CM)
A corrective, sometimes called reactive maintenance strategy, is performed after equipment failure occurs to restore functionality to normal operating conditions. Also known as breakdown or run-to-failure maintenance, CM involves troubleshooting, repairing, or replacing failed components. This approach is typically unplanned and may result in extended downtime, higher repair costs, and disrupted operations. While CM requires minimal upfront planning, it often leads to emergency repairs, spare parts expediting, and potential secondary damage to equipment, making it less cost-effective for critical assets.
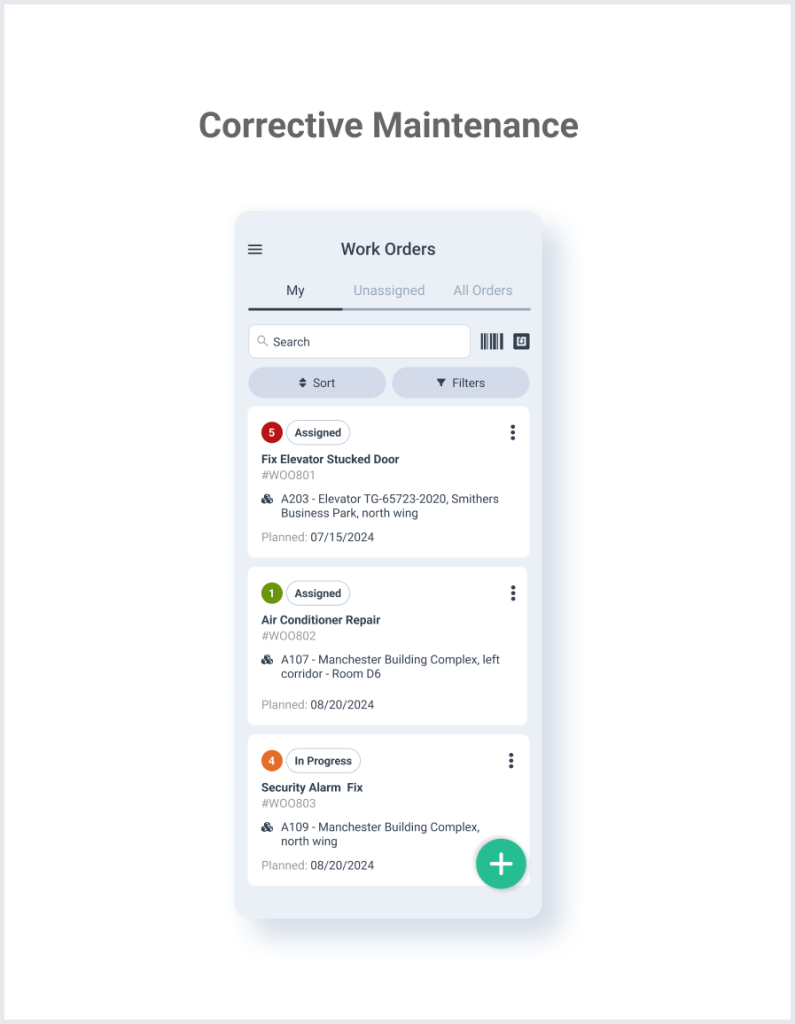
- Key Actions: Troubleshooting, repair, replacement
- Example: Replacing a failed motor
- Benefits: No upfront planning required, maximizes component life
- Limitations: Higher downtime, emergency repair costs
Reliability Centered Maintenance (RCM)
RCM is a systematic, evidence-based maintenance strategy that optimizes maintenance programs by identifying the most effective approach for each potential failure mode. It analyzes equipment function, failure patterns, and consequences to determine optimal maintenance tasks. This comprehensive approach combines multiple maintenance strategies (preventive, predictive, corrective) based on equipment criticality and failure impact. RCM prioritizes system functionality over individual component maintenance, focusing on resources that provide the most significant operational benefit and risk reduction.
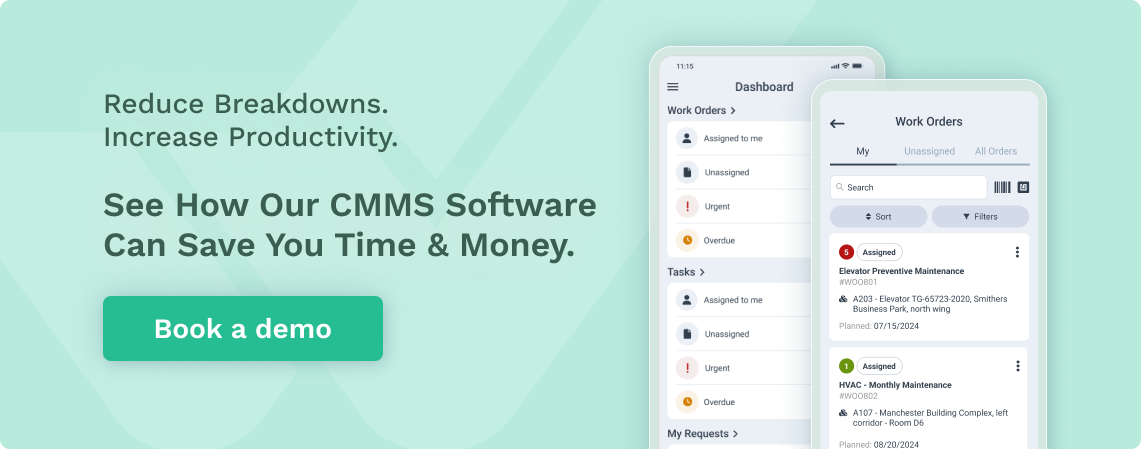
- Key Elements: Failure analysis, criticality assessment, maintenance strategy optimization
- Example: Analyzing pump failure modes to develop targeted maintenance plans
- Benefits: Optimizes maintenance resources, improves reliability
- Limitations: Complex implementation requires significant analysis
Establishing Equipment Maintenance Programs
1. Program Foundation
Equipment Assessment
Conduct comprehensive equipment inventory with criticality rankings. Document current conditions, regulatory requirements, and baseline performance metrics. Evaluate maintenance staff capabilities, training needs, and available resources.
Strategy Development
Select maintenance approaches based on equipment type and criticality. Develop standard procedures, inspection protocols, and safety requirements. Create documentation systems for tracking and reporting.
Implementation Structure
Establish maintenance intervals and work order processes. Define resource allocation and emergency protocols. Set performance metrics for reliability, costs, and efficiency tracking.
2. Support Systems
Personnel Development
Implement technical and safety training programs. Establish clear roles and documentation procedures—train staff on diagnostic techniques and emergency response.
Resource Management
Optimize spare parts inventory and vendor relationships. Create efficient storage and tracking systems. Establish parts requisition procedures that are aligned with maintenance needs.
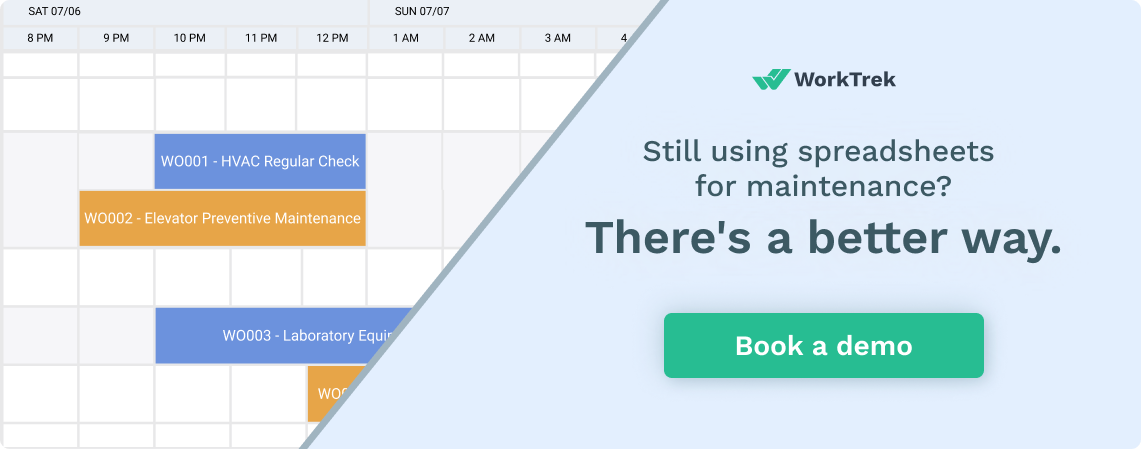
3. Quality Assurance
Performance Monitoring
Review maintenance effectiveness through regular audits: track costs and compliance requirements. Implement continuous improvement processes based on performance data.
Document Control
Maintain updated procedures and regulatory compliance records: track changes and performance metrics. Generate regular status reports for stakeholders.
Implementation Process
Start with a thorough equipment assessment. Develop clear procedures and documentation. Train personnel effectively. Monitor performance and adjust programs based on results.
4. Success Elements
Management must provide clear objectives and resource support. It must also ensure staff engagement through proper training and feedback, maintain accurate documentation, and embrace continuous improvement practices.
Get a Free WorkTrek Demo
Let's show you how WorkTrek can help you optimize your maintenance operation.
Try for free