What is a Facility Manager?
A Maintenance Manager is a skilled professional responsible for overseeing all maintenance operations within an organization. They ensure the optimal functioning of facilities, equipment, and infrastructure while maintaining safety standards and operational efficiency. They serve as the bridge between upper management and maintenance staff, coordinating resources to prevent equipment failures and minimize downtime.
Core Responsibilities for Facility Managers
First and foremost, Maintenance Managers develop and implement comprehensive maintenance strategies, including preventive, predictive, and corrective maintenance programs. They create and oversee maintenance schedules, ensuring regular inspections and repairs are conducted to prevent equipment failures and extend asset life cycles.
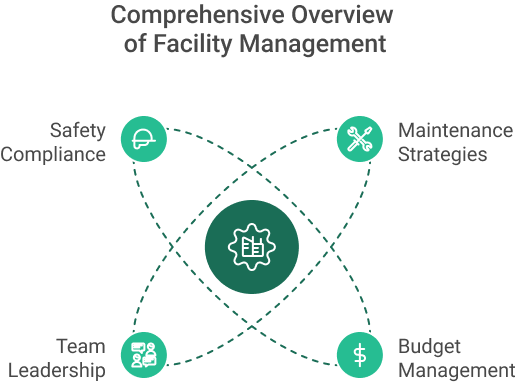
Budgets
Budget management is a crucial aspect of their role. They must allocate resources effectively, control maintenance costs, and justify expenditures while maintaining quality standards. This includes forecasting maintenance budgets, tracking expenses, and identifying cost-saving opportunities without compromising safety or efficiency.
Team Leadership
Team leadership forms another vital component of their duties. Maintenance Managers recruit, train, and supervise maintenance staff, ensuring proper skill development and safety compliance. They coordinate work assignments, establish performance metrics, and guide maintenance technicians while fostering a positive work environment.
Safety
Safety compliance is paramount in their role. They must ensure all maintenance activities adhere to relevant safety regulations, OSHA standards, and company policies. This includes implementing safety protocols, conducting regular safety training, and maintaining proper documentation of all safety-related activities.
Inventory Management
Inventory management falls under their purview, requiring them to maintain optimal levels of spare parts, tools, and maintenance supplies. They establish relationships with vendors, negotiate contracts, and ensure critical components are available when needed to minimize equipment downtime.
Documentation
Documentation and reporting are essential responsibilities. Maintenance personnel maintain detailed records of maintenance activities, equipment histories, and performance metrics. This data helps them make informed decisions about equipment replacement, process improvements, and resource allocation.
Emergency Response
Emergency response management is another critical aspect. Maintenance Managers must develop and implement emergency maintenance procedures, ensuring quick response times to equipment failures or facility issues that could impact operations.
Strategic Planning
Strategic planning involves working closely with other department heads to align maintenance activities with organizational goals. They participate in capital planning, equipment procurement decisions, and facility expansion projects, providing valuable technical expertise.
Continuous Improvement
Continuous improvement is fundamental to their role. They must stay current with industry trends, new technologies, and best practices in maintenance management. This includes implementing new maintenance techniques, adopting maintenance management software, and optimizing processes for greater efficiency.
Communication with Stake Holders
Stakeholder management requires excellent communication skills, as they must regularly interact with various departments, vendors, contractors, and upper management. They regularly update maintenance activities, project status, and budget performance while addressing concerns and coordinating cross-functional initiatives.
Quality Control
Quality control is an ongoing responsibility, ensuring all maintenance work meets established standards and specifications. To maintain high standards of maintenance operations, they conduct regular audits, inspect completed work, and implement quality assurance measures.
Jack of All Trades
This comprehensive role requires a unique blend of technical expertise, leadership skills, and business acumen. Successful Maintenance Managers must balance multiple priorities while ensuring the reliable operation of facilities and equipment, making them integral to an organization’s operational success.
Educational and Certification Requirements for Facility Managers
Educational Background
A bachelor’s degree typically serves as the foundation for a maintenance manager role, with common fields including engineering, facilities management, business administration, and construction management. While some organizations may accept an associate degree with extensive experience, professional certifications such as CMRP, FMP, or CFM significantly enhance qualifications and demonstrate expertise in the field.
Experience Requirement
Most employers seek candidates with 5-10 years of progressive maintenance experience, including at least 3-5 years in supervisory positions. This experience should encompass hands-on maintenance operations, project management, budget control, and Computerized Maintenance Management Systems (CMMS) proficiency. A strong track record of successful project completion and team leadership is essential.
Technical Competencies
Maintenance Managers must possess comprehensive knowledge of mechanical and electrical systems and a thorough understanding of safety regulations and OSHA requirements. Their expertise should cover maintenance planning, preventive and predictive maintenance techniques, quality control systems, and energy management. Familiarity with building codes and regulations ensures compliance and operational excellence.
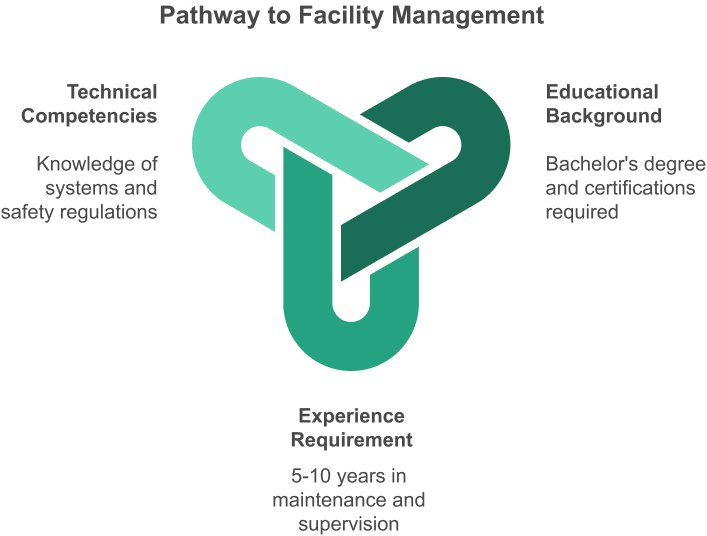
Soft Skills
Essential Soft Skills Success in this role demands strong leadership abilities and excellent communication skills. Maintenance Managers must excel in problem-solving, demonstrate sound decision-making capabilities, and effectively manage time and resources. The ability to handle pressure, resolve conflicts, and maintain positive relationships with team members and stakeholders is vital.
Industry Knowledge
Different sectors require specific expertise. Manufacturing environments demand understanding of production processes, healthcare facilities require knowledge of medical equipment and regulations, commercial buildings focus on HVAC and building automation systems, while industrial settings emphasize heavy equipment and processes. This specialized knowledge is often gained through targeted experience and training.
Professional Growth
Ongoing professional development through industry conferences, technical training programs, and management courses is essential. Active participation in professional associations and regular updates to safety certifications help maintain current knowledge and industry best practices. This commitment to continuous learning ensures Maintenance Managers stay effective in their evolving roles.
Get a Free WorkTrek Demo
Let's show you how WorkTrek can help you optimize your maintenance operation.
Try for free