What is General Maintenance?
General maintenance refers to routine tasks to keep equipment, machinery, or infrastructure in good working condition.
These tasks are essential for preventing unexpected breakdowns, maintaining performance, and ensuring the safety of the equipment and the people operating it. General maintenance includes cleaning, lubrication, tightening, adjustments, and visual inspections.
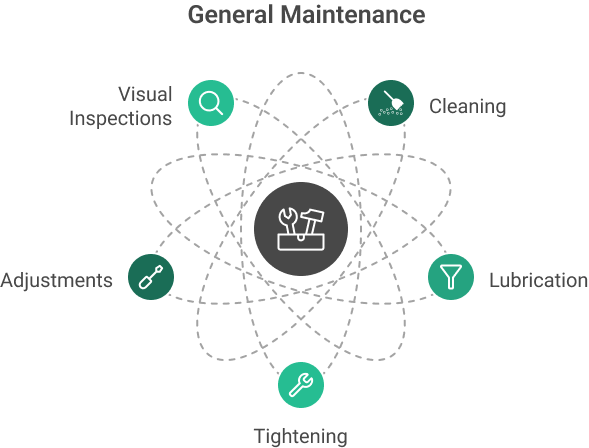
For many types of equipment, general maintenance tasks are straightforward but critical to preventing wear and tear that could lead to larger issues.
For example, lubricating moving parts in machinery can prevent friction-related damage, while regular cleaning of air filters can improve the efficiency of HVAC systems. These tasks do not usually require in-depth technical expertise but are necessary for prolonging equipment life and ensuring reliable performance.
General maintenance is often scheduled as part of a preventive maintenance program, where tasks are performed regularly based on manufacturer recommendations or operational experience.
While these tasks may seem minor, neglecting general maintenance can result in more serious problems over time, such as equipment malfunctions, reduced efficiency, or safety hazards.
By consistently performing general maintenance, organizations can avoid costly repairs, reduce downtime, and ensure that equipment remains optimal for its intended use.
How General Maintenance Works:
General maintenance follows a structured approach based on predetermined schedules and standard procedures. Think of it like regular health check-ups for equipment.
Just as you might visit a doctor annually regardless of how you feel, general maintenance happens on a set timeline regardless of equipment condition.
Stages of General Maintenance
First, planners establish standard maintenance schedules based on manufacturer recommendations, industry standards, and historical experience. For example, they might set up monthly bearing lubrication, quarterly belt inspections, and annual comprehensive equipment reviews.
Next, maintenance technicians perform regular inspections and basic maintenance tasks according to these schedules. These activities might include cleaning equipment, checking fluid levels, tightening loose components, and performing basic calibrations. For instance, an air handling unit might receive monthly filter changes and quarterly belt tension checks as part of its general maintenance routine.
Finally, technicians document all maintenance activities, creating a history that helps identify patterns and adjust maintenance schedules. This documentation becomes valuable for planning future maintenance and identifying potential problems before they become serious.
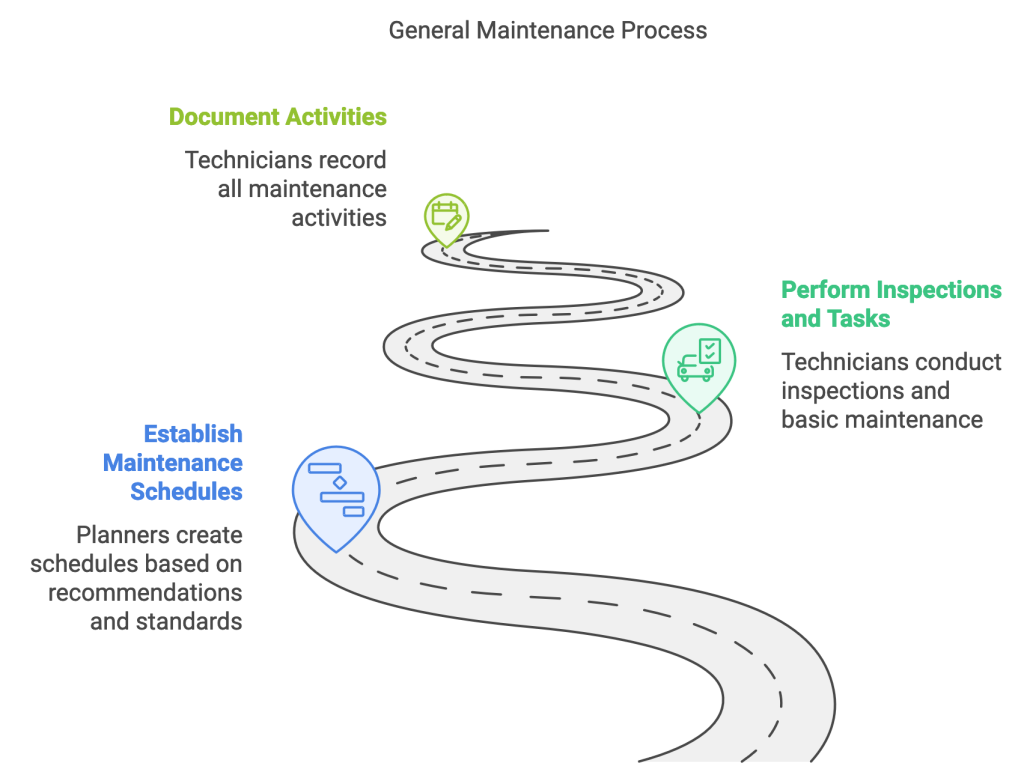
Differences from Other Maintenance Approaches:
To understand how general maintenance differs from other approaches, let’s compare it to several common maintenance strategies:
Preventive Maintenance:
While general maintenance is sometimes used interchangeably with preventive maintenance, preventive maintenance is typically more comprehensive and specifically focused on preventing equipment failure. General maintenance might include basic cleaning and inspection of a pump, while preventive maintenance would involve detailed measurements, component replacement based on wear patterns, and specific performance testing.
Predictive Maintenance:
Unlike general maintenance, predictive maintenance uses condition monitoring and data analysis to determine when maintenance is needed. While general maintenance might schedule quarterly bearing lubrication, predictive maintenance would use vibration analysis or oil analysis to determine when bearings need attention, potentially extending or reducing the maintenance interval based on actual conditions.
Reactive Maintenance:
This approach is essentially the opposite of general maintenance. Rather than performing regular maintenance tasks on a schedule, reactive maintenance only addresses equipment issues after they occur. While general maintenance might regularly clean and inspect a conveyor belt system, reactive maintenance would wait until the belt fails before taking action.
Reliability-Centered Maintenance (RCM):
RCM is more sophisticated than general maintenance. It uses a systematic approach to determine the most appropriate maintenance strategy for each piece of equipment based on its criticality and failure modes.
While general maintenance might treat all similar equipment the same way, RCM might prescribe different maintenance approaches for identical pumps based on their role in the process and the consequences of their failure.
Understanding these differences helps maintenance managers choose the most appropriate maintenance strategy for their needs. General maintenance often serves as a foundation upon which more sophisticated maintenance approaches can be built.
Many organizations use a combination of approaches, with general maintenance handling routine tasks and more advanced strategies addressing critical equipment and systems.
Get a Free WorkTrek Demo
Let's show you how WorkTrek can help you optimize your maintenance operation.
Try for free