What is Handover Maintenance?
Handover in maintenance refers to the formal transfer of responsibility for equipment or a maintenance task from one party to another, often between maintenance shifts, teams, or contractors. It is a critical process for ensuring continuity in maintenance operations, especially in industries that operate 24/7 or where multiple teams maintain complex systems.
During a handover, the outgoing team or technician provides the incoming team with detailed information about the status of equipment, ongoing maintenance tasks, and any issues that need to be addressed. This may include details about work orders that are in progress, equipment that requires further attention, or safety hazards that need to be mitigated. The handover process often involves a checklist or logbook to ensure no critical information is overlooked.
A well-executed handover ensures that maintenance tasks are completed efficiently, reduces the likelihood of errors or miscommunication, and enhances overall safety. It also helps prevent delays in maintenance activities and ensures that equipment remains operational.
Handover Maintenance Process
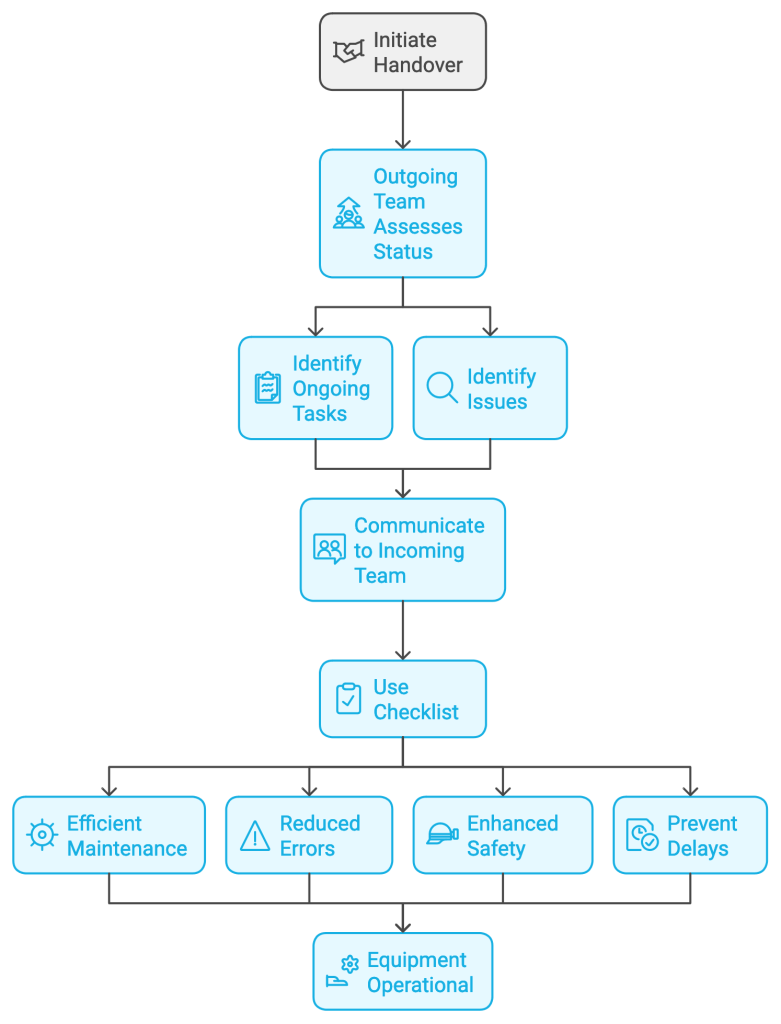
How to Implement & Manage Handover Maintenance
Communication Protocol
Implementation Maintenance organizations establish structured communication protocols for shift transitions. These protocols detail exactly what information needs to be shared and how. For instance, when the morning shift hands over to the afternoon shift, they might use a standardized digital form that covers equipment status, ongoing repairs, safety concerns, and priority tasks. This ensures no critical information is lost between shifts.
Documentation Systems
Effective handover maintenance requires robust documentation systems. Organizations implement detailed logging procedures where maintenance teams record all activities, observations, and pending tasks.
Think of this like a captain’s log on a ship – each entry builds a continuous narrative of maintenance activities. Modern organizations often use computerized maintenance management systems (CMMS) to facilitate this documentation, making it easily accessible to incoming shifts.
Equipment Status Tracking
Maintenance teams develop comprehensive methods for tracking equipment status during handovers. This involves creating detailed status boards or digital dashboards showing which equipment is running, under repair, awaiting parts, or scheduled for maintenance.
For example, a manufacturing facility might use a color-coded digital display showing green for operational equipment, yellow for equipment needing attention, and red for equipment under repair.
Priority Task Management
Organizations establish systems for managing and communicating task priorities across shifts. This includes creating clear criteria for determining task urgency and ensuring incoming teams understand which tasks need immediate attention.
For instance, a critical pump repair started by the outgoing shift would be flagged as a high priority, with detailed notes about work completed and documented next steps.
Knowledge Transfer Processes
Successful handover maintenance includes processes for sharing technical knowledge and experiences between shifts. This might involve creating detailed maintenance histories for complex equipment, documenting unusual problems encountered, and sharing solutions found.
Organizations often implement mentoring programs where experienced technicians share their knowledge with newer team members during handovers.
Safety Information
Exchange Organizations incorporate safety-related information into their handover processes. This includes sharing updates about potential hazards, changes in safety protocols, or special safety considerations for ongoing maintenance tasks.
For example, if the morning shift discovers a small oil leak, they would document the leak and any temporary safety measures implemented, ensuring the afternoon shift is fully aware of the situation.
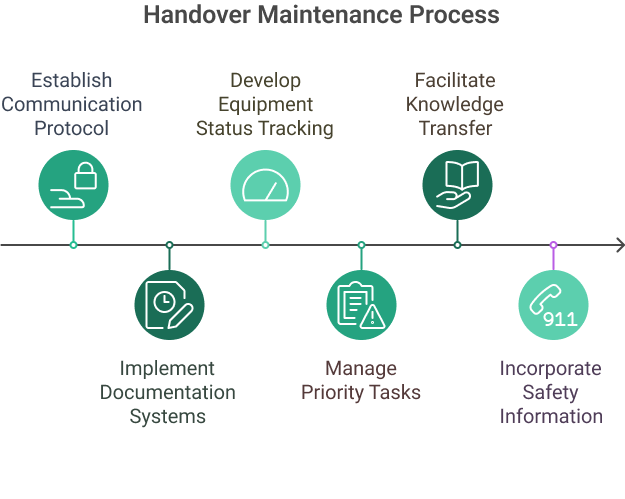
Benefits to Maintenance Organizations:
Improved Continuity of Operations
Handover maintenance ensures maintenance activities continue smoothly across shifts without interruption. When done correctly, it prevents the common problem of tasks falling through the cracks during shift changes. This continuity helps maintain equipment reliability and prevents costly downtime.
Enhanced Equipment Reliability
By consistently attending to equipment needs across all shifts, organizations can better prevent equipment failures. When each shift has complete information about equipment status and maintenance history, they can make more informed decisions about maintenance priorities and approaches.
Reduced Maintenance Errors
Clear communication and documentation during handovers reduce the likelihood of maintenance errors caused by misunderstandings or incomplete information. This leads to fewer repeated tasks, overlooked problems, or incorrect maintenance procedures.
Better Resource Utilization
With clear information about ongoing tasks and priorities, organizations can better allocate their maintenance resources across shifts. This prevents duplication of effort and ensures critical tasks receive appropriate attention regardless of shift changes.
Get a Free WorkTrek Demo
Let's show you how WorkTrek can help you optimize your maintenance operation.
Try for free