What is Just-in-Time (JIT) Inventory?
Just-in-time inventory management is a strategic approach in which materials, components, and products are received exactly when needed in the production process or for service delivery.
This methodology originated from Toyota’s production system in the 1970s. The core principle is eliminating waste by maintaining minimal inventory levels and creating a pull-based system where demand triggers supply.

Think of it like a restaurant that receives fresh ingredients each morning based on expected daily orders rather than storing weeks’ worth of perishables. The goal is to hold enough inventory to meet immediate needs while minimizing carrying costs and reducing waste.
How is it used?
JIT implementation requires careful coordination across the entire supply chain. Organizations establish reliable relationships with suppliers who can deliver materials frequently and consistently.
They typically set up systems to automatically trigger orders when inventory reaches predetermined levels.
For example, an automotive manufacturer might arrange for seats to arrive at the assembly line precisely when needed for each car being built. This requires:
- Sophisticated demand forecasting systems
- Real-time inventory tracking
- Strong supplier relationships with clear communication channels
- Efficient transportation and logistics networks
- Quality control processes at every stage
Optimal JIT Inventory Scenarios
JIT works best in environments with specific characteristics:
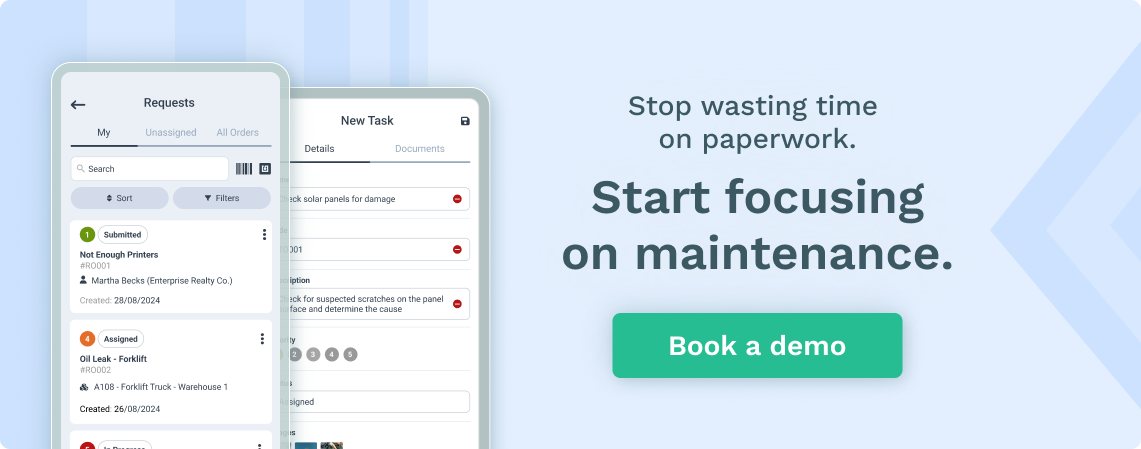
Predictable demand patterns are essential, as sudden spikes can disrupt the entire system. Think of industries like automobile manufacturing, where production schedules are planned well.
Geographic proximity to suppliers is important – the closer your suppliers are, the more reliable your delivery times will be. This is why many automotive suppliers locate their facilities near major assembly plants.
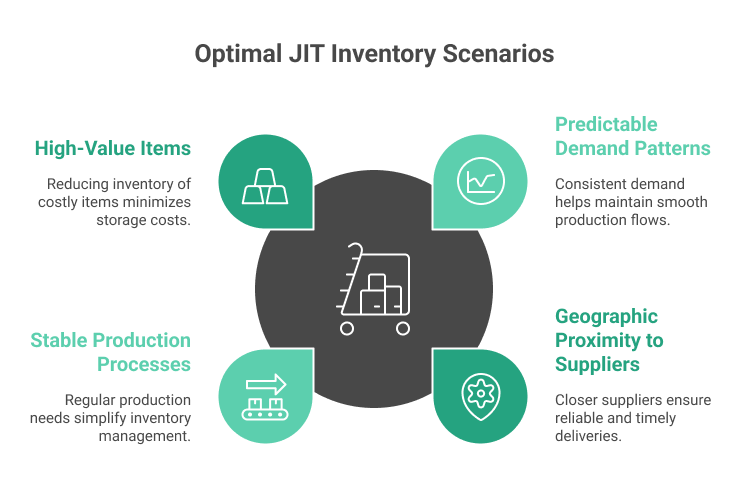
Stable production processes where the same items are needed regularly make JIT more effective. For instance, a smartphone manufacturer producing consistent models can better predict component needs than a custom furniture maker.
High-value items that are expensive to store make excellent candidates for JIT. Computer chip manufacturers, for example, benefit greatly from reducing inventory of these costly components.
How maintenance organizations can leverage JIT
They can schedule parts delivery for routine maintenance to coincide with planned maintenance activities. Instead of storing large quantities of air filters or lubricants, they can arrange regular deliveries based on maintenance schedules.
For predictive maintenance, organizations can use condition monitoring data to anticipate when parts will be needed. Modern sensors and analytics can predict component failure weeks in advance, allowing time to order replacement parts just before they’re required.
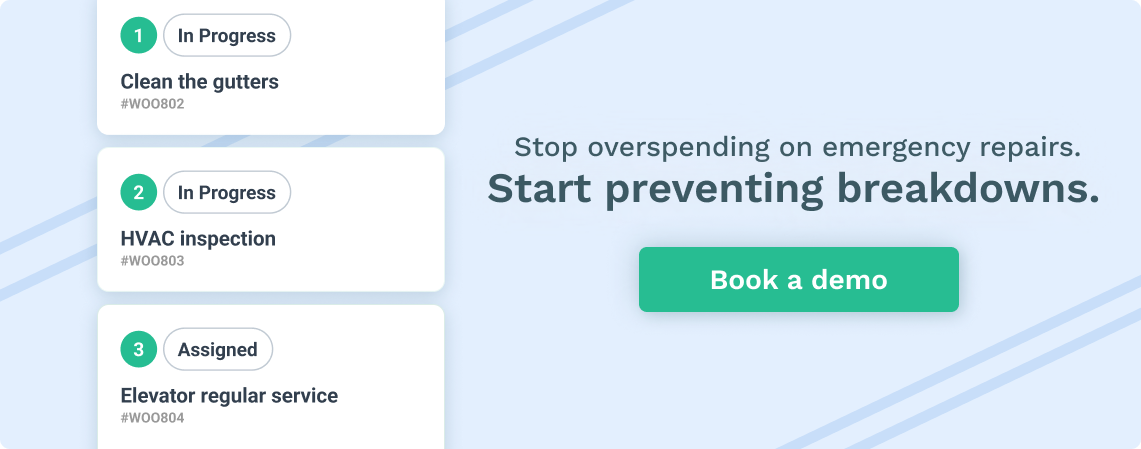
However, maintenance organizations should maintain some critical spare inventory for emergency repairs. The key is identifying which parts need to be stored on-site versus which can be obtained quickly.
A practical example would be a facilities maintenance team that:
- Keeps minimal stock of common items like light bulbs and filters
- Orders specialty parts based on equipment inspection results
- Maintains relationships with local suppliers for same-day delivery of standard parts
- Only stores critical spares that would cause significant downtime if not immediately available
The success of JIT in maintenance depends heavily on:
- Accurate forecasting of maintenance needs
- Strong preventive maintenance programs
- Reliable supplier networks
- Good historical data on equipment performance
- Risk assessment of potential failures
Get a Free WorkTrek Demo
Let's show you how WorkTrek can help you optimize your maintenance operation.
Try for free