What is Just-in-Time Maintenance (JIT)?
Just-in-Time (JIT) in inventory management is a strategy designed to enhance efficiency and reduce waste by receiving goods only as they are needed in the production process. This approach minimizes a business’s inventory, significantly lowering storage costs and reducing the risk of overstocking or obsolescence.
Imagine a bakery that only orders flour when it has a confirmed order for bread. Instead of storing large quantities of flour, the bakery coordinates closely with its suppliers to ensure that flour arrives just in time for baking. This system reduces storage costs and ensures that the flour is always fresh, directly aligning with customer demand.
JIT inventory management relies heavily on precise coordination with suppliers to ensure that materials arrive exactly when needed. This promotes a streamlined production flow, allowing businesses to respond swiftly to customer demand without the burden of excess inventory.
By aligning inventory levels closely with production schedules, companies can achieve more efficient inventory management and reduce unnecessary costs.
How does it work?
Just-in-time maintenance is a proactive maintenance strategy that synchronizes maintenance activities with actual equipment needs, scheduling work to be performed exactly when needed—no earlier or no later.
This approach eliminates waste by performing maintenance at the optimal moment, determined by real-time condition monitoring and predictive analytics rather than fixed time intervals.
To better understand this concept, imagine a car’s maintenance schedule. Instead of changing the oil every 3,000 miles regardless of condition, a JIT approach would monitor the oil’s actual condition and only schedule a change when the oil begins showing signs of degradation but before it causes engine damage.
This ensures maximum component life while preventing unnecessary maintenance. Additionally, JIT maintenance impacts the entire supply chain by requiring precise coordination and collaboration among suppliers to ensure timely availability of parts and services.
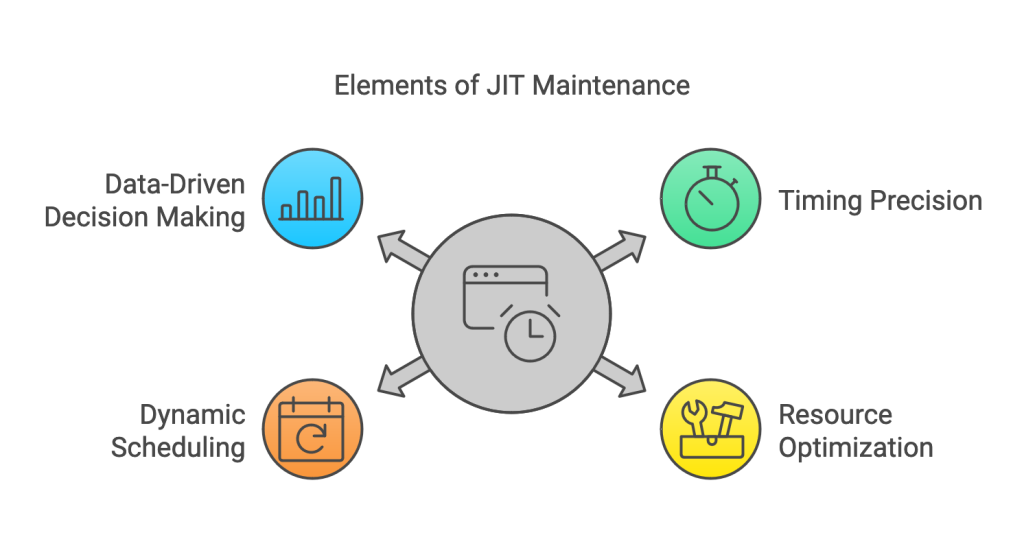
Understanding JIT maintenance also requires recognizing its relationship to broader maintenance concepts. It’s often implemented alongside predictive maintenance strategies and requires robust condition monitoring systems. Think of it as part of a larger ecosystem where various maintenance approaches work together to optimize equipment reliability and cost-effectiveness.
Benefits of Implementing JIT
Implementing JIT inventory management offers a multitude of benefits that can transform a business’s operational efficiency and financial health:
- Reduced Inventory Holding Costs: By minimizing the amount of inventory held, businesses can significantly reduce storage costs, insurance, and depreciation expenses. This reduction in inventory carrying costs frees up valuable resources that can be better utilized elsewhere.
- Improved Efficiency: JIT promotes a streamlined production flow, enabling businesses to respond quickly to customer demand. Without the burden of excess inventory, production processes become more agile and adaptable to market changes.
- Increased Customer Satisfaction: Ensuring that products are available when customers need them can greatly enhance customer satisfaction and loyalty. JIT helps businesses meet customer demand promptly, leading to higher levels of customer satisfaction.
- Reduced Waste: JIT aims to eliminate waste in all forms, including excess inventory, overproduction, and unnecessary movements. By focusing on producing only what is needed, businesses can operate more sustainably and cost-effectively when it is required.
- Improved Cash Flow: Reducing inventory levels means less capital is tied up in stock. This improvement in cash flow allows businesses to invest in other areas, such as innovation, marketing, or expanding their product lines.
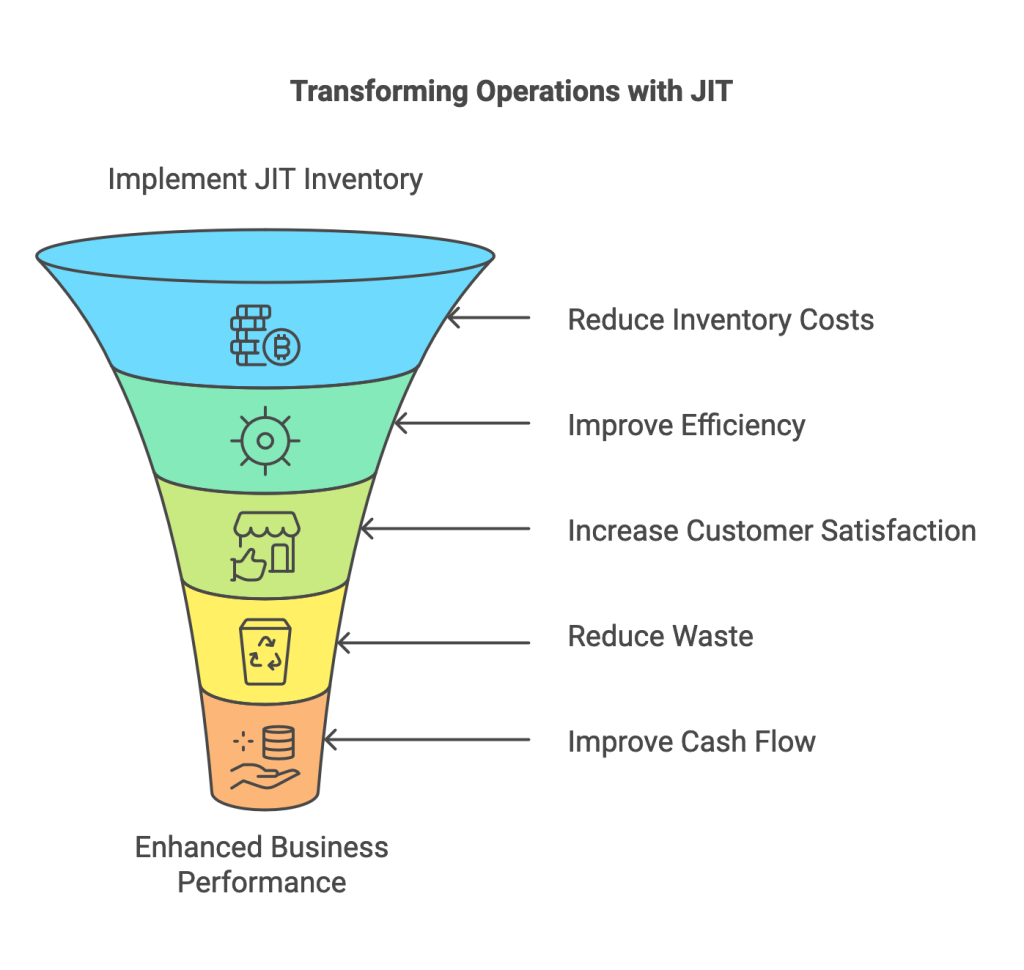
By implementing JIT inventory management, businesses can achieve more efficient inventory management, reduce costs, and enhance their ability to meet customer demand, ultimately leading to a more robust and responsive supply chain.
JIT Maintenance Best Practices
The foundation of successful JIT maintenance starts with robust condition monitoring. Organizations must implement comprehensive monitoring systems that track key performance indicators of equipment health.
This includes installing sensors to measure vibration, temperature, pressure, and other relevant parameters. Consider this as giving your equipment a continuous health check-up, similar to how modern medical devices monitor vital signs. The Toyota Production System (TPS) has significantly influenced JIT maintenance practices by emphasizing waste reduction and efficient production flows.
Data Collection
Data collection and analysis form the next crucial layer. Organizations should establish systems to collect, store, and analyze real-time equipment performance data.
Accurate demand forecasts are essential for effective data collection and analysis in JIT maintenance, as they enable alignment of production with current market needs.
This requires sophisticated software platforms to process large amounts of data and identify patterns indicating potential failures. The analysis should consider multiple factors, including historical performance, operating conditions, and maintenance history, like how doctors consider various health indicators to predict potential medical issues.
Predictive Modeling and Accurate Demand Forecasting
Predictive modeling becomes essential for correctly timing maintenance activities. Organizations can use advanced analytics and machine learning algorithms to develop accurate predictions of when equipment will need maintenance.
These models should continuously learn and improve from new data, becoming more precise over time. For example, if a bearing typically fails after 5,000 hours of operation, the model might identify specific vibration patterns that indicate failure is approaching 4,800 hours.
Integrate Supply Chain
Supply chain integration plays a critical role in JIT maintenance success. Organizations need to develop strong relationships with reliable suppliers who can deliver parts and materials quickly when needed.
The JIT inventory system ensures the timely delivery of parts and materials by aligning production schedules with supply delivery, enhancing efficiency, and minimizing waste. This often involves setting up automated ordering systems triggered by predictive maintenance alerts.
The supply chain should be flexible enough to handle routine and emergency maintenance needs, similar to how hospitals maintain relationships with medical suppliers for planned procedures and emergencies. The importance of time jit inventory lies in synchronizing inventory arrivals with maintenance needs, reducing waste, and optimizing efficiency.
Training for Continuous Improvement
Employee training and empowerment represent another crucial practice. Maintenance technicians need training not just in maintenance procedures but also in using monitoring systems, interpreting data, and making decisions based on predictive analytics.
They should understand both the technical aspects of their work and the principles of JIT maintenance. This might involve regular training sessions, certification programs, and hands-on experience with monitoring systems.
Inventory Management Documentation
Documentation and standardization help ensure consistency in JIT maintenance implementation. Organizations should develop detailed procedures for monitoring, analysis, decision-making, and maintenance execution.
These procedures should be documented and regularly updated based on experience and changing conditions. Think of this as creating a detailed playbook everyone follows while remaining flexible enough to adapt to specific situations.
Team Communication
Communication systems form a critical backbone of JIT maintenance. All stakeholders – from operators to maintenance technicians to management – need clear channels for sharing information about equipment conditions, maintenance needs, and resource availability. This might involve implementing digital communication platforms that automatically notify relevant personnel when maintenance is needed.
Measure Performance
Performance measurement and continuous improvement complete the best practices framework. Organizations should track key metrics such as equipment reliability, maintenance costs, downtime reduction, and parts inventory levels. Regular analysis of these metrics helps identify areas for improvement and adjust strategies accordingly. This creates a feedback loop that continuously refines the JIT maintenance system.
Risk Management
Risk management strategies should also be incorporated into JIT maintenance practices. While JIT aims to minimize inventory and optimize timing, organizations need backup plans for critical equipment and potential emergencies.
This might involve maintaining minimal critical spare parts inventories or having emergency service agreements with suppliers.
Get a Free WorkTrek Demo
Let's show you how WorkTrek can help you optimize your maintenance operation.
Try for free