What is Lean Inventory Management?
Lean Inventory Management is a methodology that focuses on minimizing inventory waste while ensuring materials and products are available when needed. This approach evolved from lean manufacturing principles but specifically addresses inventory control. The core philosophy is to maintain only the necessary inventory to meet current demand, treating excess inventory as a waste that ties up capital and creates inefficiencies.
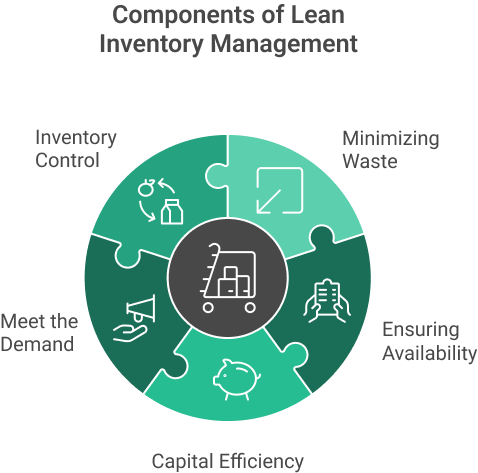
Think of Lean Inventory Management as maintaining your kitchen pantry with perfect efficiency. Instead of stocking up on everything you might need, you keep just enough ingredients for your planned meals, with a small safety stock for unexpected situations. You know exactly what you have, where it is, and when you’ll need to replenish it.
How is it Used?
Organizations implement Lean Inventory Management through several key strategies:
Visual Management Systems create transparency in inventory levels and movement. For example, manufacturing facilities might use Kanban cards or electronic displays showing real-time inventory status. When inventory reaches a predetermined level, it automatically triggers reordering processes.
ABC Analysis helps prioritize inventory control efforts by categorizing items based on their value and usage frequency.
For example, an electronics manufacturer might classify expensive microprocessors as ‘A’ items requiring tight control, while basic fasteners might be ‘C’ items with simpler management processes.
Cycle Counting replaces annual physical inventories with regular, targeted counts. Rather than shutting down operations for a complete count, teams might verify the accuracy of different inventory segments throughout the year, focusing more frequently on high-value items.
Pull Systems ensure materials flow based on actual demand rather than forecasts.
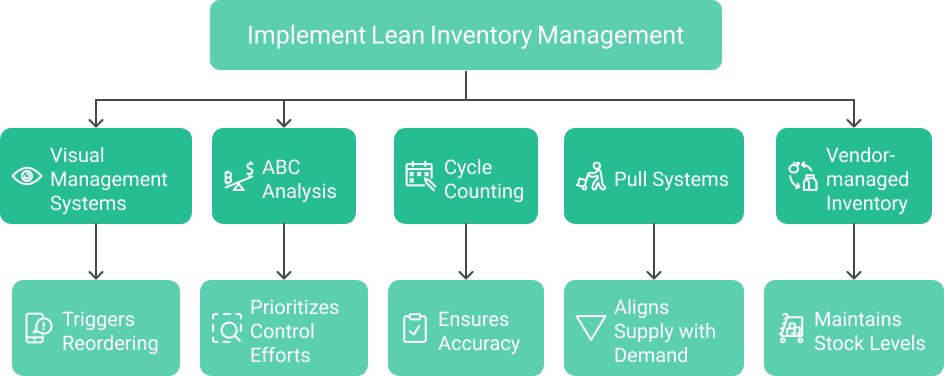
For example, a furniture manufacturer might only order new raw materials when a customer orders to deplete existing stock rather than maintain large buffer inventories.
Vendor-managed inventory programs transfer responsibility for maintaining appropriate stock levels to suppliers.
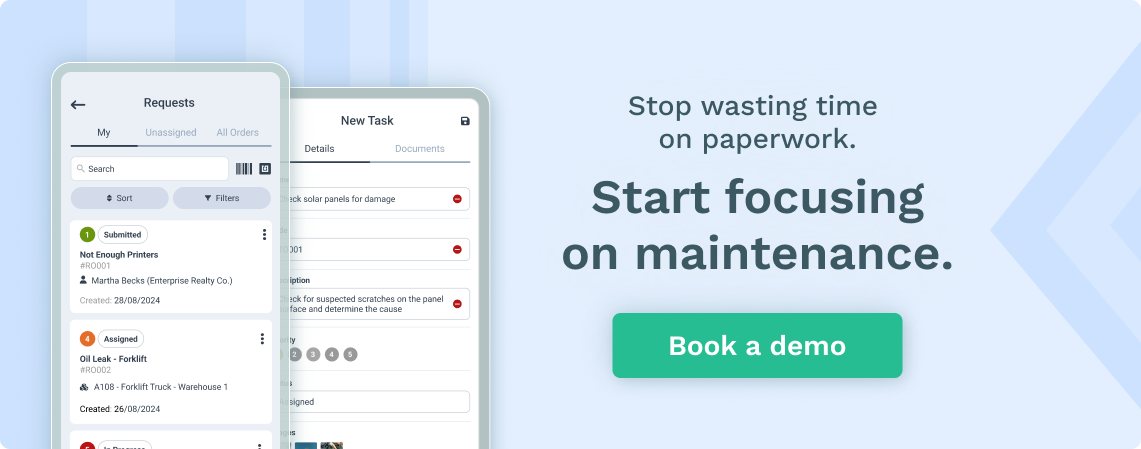
An automotive parts supplier might monitor customer inventory levels and automatically replenish components based on agreed-upon parameters.
When to use Lean Inventory Management?
This approach works particularly well in:
Operations with predictable demand patterns where usage rates can be accurately calculated. Consumer packaged goods manufacturing often benefits from this predictability.
Environments where storage space is limited or expensive. Urban warehouses or manufacturing facilities might implement lean inventory practices to maximize valuable floor space.
Industries with perishable or time-sensitive materials. Food processing companies can reduce waste by maintaining minimal inventories of fresh ingredients.
Businesses with strong supplier relationships that enable reliable, frequent deliveries. Electronics manufacturers often develop close partnerships with key component suppliers to support lean inventory practices.
Implementation Strategies
Value Stream Mapping examines the entire inventory process from supplier to customer. Teams analyze how materials flow through the organization, identifying opportunities to reduce waste and improve efficiency.
Standardized Work Procedures ensure consistent handling and management of inventory. This might include specific processes for receiving, storing, picking, and cycle counting materials.
Information System Integration connects inventory management with other business processes. Modern systems might link point-of-sale data directly to inventory and ordering systems, enabling automated replenishment.
Employee Training develops the skills needed to maintain lean inventory practices. Workers learn to use management systems, perform cycle counts, and understand the importance of inventory accuracy.
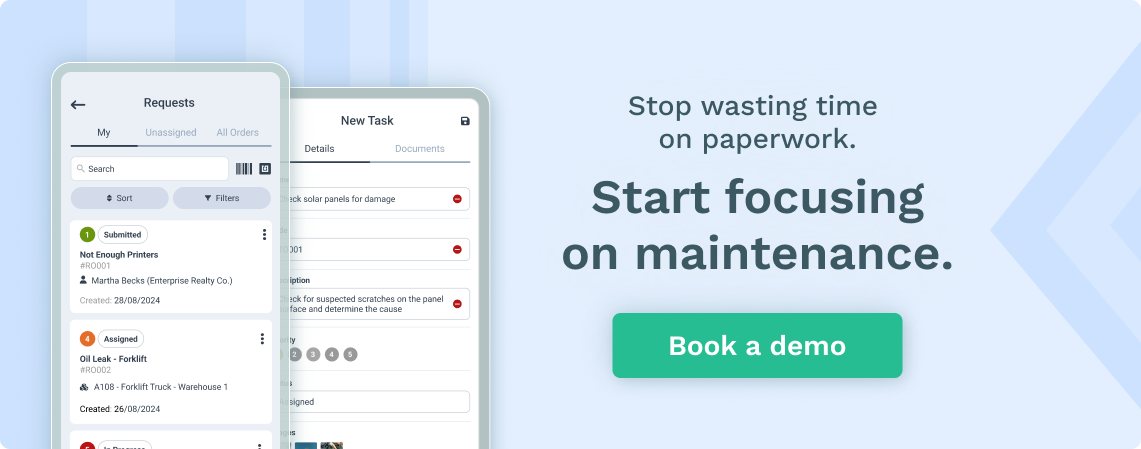
Performance Measurement tracks key metrics like inventory turns, carrying costs, and stock-outs. Regular monitoring helps identify areas for improvement and justifies continued investment in lean practices.
Common Challenges and Solutions
Implementation often faces several obstacles:
Resistance to reducing safety stock levels can be addressed by carefully analyzing usage patterns and gradually reducing buffer inventories.
Coordination with suppliers requires clear communication and possibly new contractual arrangements. Organizations might start with pilot programs involving key suppliers before expanding.
System integration complexities need careful planning and possibly investment in new technology. Companies often implement changes in phases to manage risk and verify benefits.
What are the Benefits to Maintenance Organizations?
- Reduced carrying costs through lower inventory levels
- Improved cash flow by freeing up working capital
- Better space utilization in warehouses and production areas
- Reduced risk of obsolescence and spoilage
- More accurate inventory records
- Improved supplier relationships and performance
- Enhanced customer satisfaction through better product availability
Get a Free WorkTrek Demo
Let's show you how WorkTrek can help you optimize your maintenance operation.
Try for free