What is machine availability?
Machine availability is a crucial performance metric that measures when equipment or machinery is ready and can perform its intended function when needed.
Think of it like a baseball player’s readiness to play—just as a team needs its players available for games, a factory needs its machines ready for production.
To understand machine availability deeply, we must break it down into its core components and calculation methods.
The basic formula for machine availability is:
Availability = (Total Time – Downtime) / Total Time × 100%
However, this seemingly simple formula contains several important nuances that deserve exploration.
Let’s break down each element:
Total Time represents the complete duration we expect the machine to operate. In a factory running 24/7, this might be all 8,760 hours in a year.
However, the total time would exclude off-hours and planned shutdowns for a facility that operates only one shift per day.
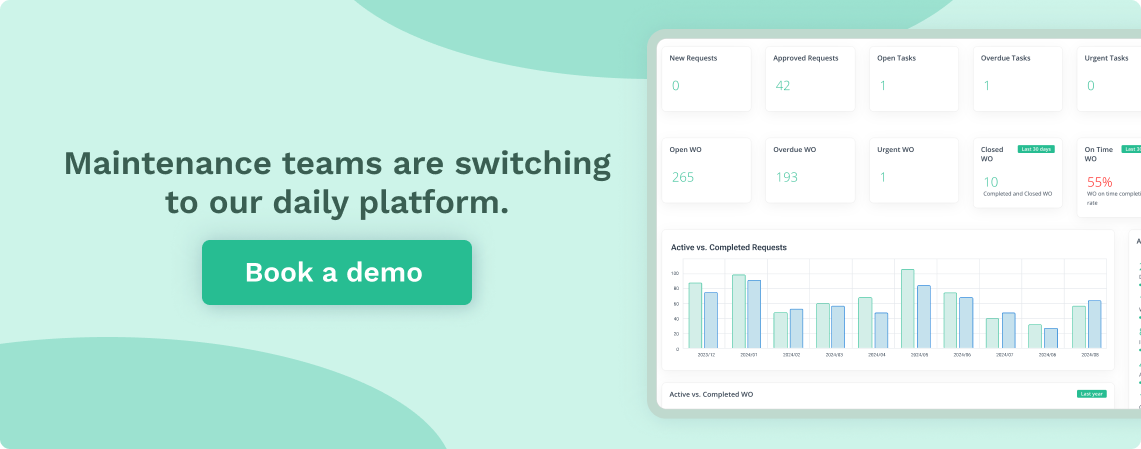
Machine Availability Calculator
Machine Availability Calculator
Downtime encompasses all periods when the machine isn’t operational, but it’s crucial to understand that not all downtime is created equal. It typically includes:
Planned Downtime:
- Scheduled maintenance
- Setup and adjustment time
- Planned upgrades or modifications
- Operator breaks and shift changes
- Planned production changes
Unplanned Downtime:
- Equipment failures
- Emergency repairs
- Material shortages
- Operator unavailability
- Utility failures (power, compressed air, etc.)
- Quality issues requiring stoppage
The interpretation of machine availability becomes more meaningful when we understand its relationship with other performance metrics.
For instance, a machine might be “available” but not producing at full capacity, so availability is often considered alongside performance efficiency and quality rates in calculating Overall Equipment Effectiveness (OEE).
Factors Affecting Machine Availability
Impact of Maintenance Strategy The choice of maintenance approach significantly influences availability. A purely reactive maintenance strategy might lead to more unplanned downtime, while a well-implemented predictive maintenance program could maximize availability by addressing issues before they cause failures.
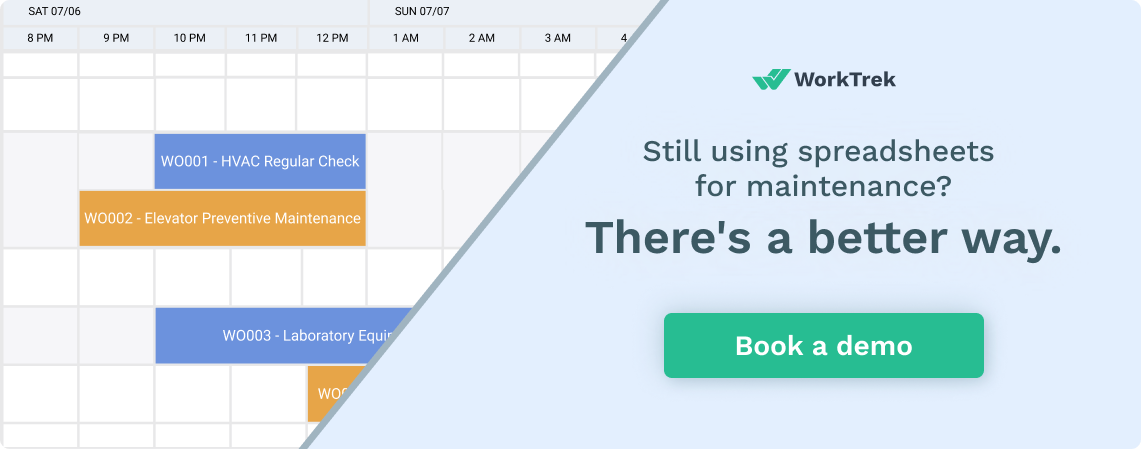
Design and Engineering Considerations
- Redundant systems can maintain availability even during component failures
- Modular designs enable faster repairs and maintenance
- Built-in monitoring systems help predict and prevent failures
- Access points for maintenance affect repair times
Operational Practices Daily operations can significantly impact the availability
- Operator training and skill levels
- Standard operating procedures
- Regular cleaning and inspection routines
- Quick response procedures for common issues
- Spare parts management
Modern Approaches to Improving Availability
Digital Technologies Contemporary manufacturing facilities are increasingly using advanced technologies to optimize availability:
- IoT sensors for real-time monitoring
- AI-powered predictive maintenance systems
- Digital twins for simulation and optimization
- Automated maintenance scheduling
- Remote monitoring and diagnostics
Data Analytics Modern availability management relies heavily on data
- Historical performance analysis
- Failure pattern recognition
- Predictive modeling
- Root cause analysis
- Performance benchmarking
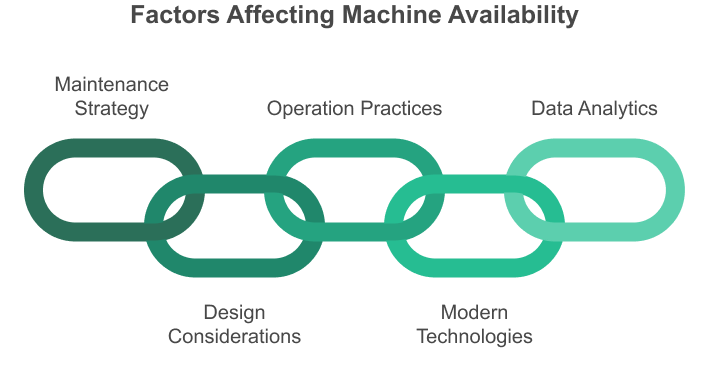
Business Impact of Equipment Availability
Understanding machine availability is crucial because it directly affects:
- Production capacity and output
- Operating costs
- Product quality
- Customer satisfaction
- Revenue generation
- Return on investment
Best Practices for Maximizing Availability
To achieve optimal machine availability, organizations should:
- Implement comprehensive maintenance strategies
- Invest in operator training and development
- Maintain accurate records of downtime and its causes
- Use appropriate monitoring and measurement systems
- Regularly analyze performance data
- Continuously improve maintenance procedures
- Maintain adequate spare parts inventory
- Develop strong vendor relationships for support
Get a Free WorkTrek Demo
Let's show you how WorkTrek can help you optimize your maintenance operation.
Try for free