What is Maintenance Inspection?
A maintenance inspection is a systematic process of examining, evaluating, and documenting the condition of physical assets, equipment, or facilities. This process involves trained personnel using specific tools, techniques, and procedures to assess various aspects of the asset, including its physical condition, performance metrics, safety features, and compliance with established standards. The inspection encompasses visual examination and technical measurements, often utilizing specialized diagnostic equipment such as vibration analyzers, thermal cameras, or ultrasonic devices.
To understand this better, think of a maintenance inspection as similar to a medical check-up for equipment. Just as a doctor examines various aspects of your health through different tests and observations, maintenance inspectors evaluate multiple components and systems to build a complete picture of an asset’s “health.”
The scope of a maintenance inspection typically includes:
- Physical examination of components for wear, damage, or deterioration
- Performance testing to verify proper operation
- Measurements of critical parameters like temperature, pressure, or vibration
- Documentation of findings, including photographs and sensor readings
- Assessment against established standards and specifications
- Recommendations for necessary repairs or preventive actions
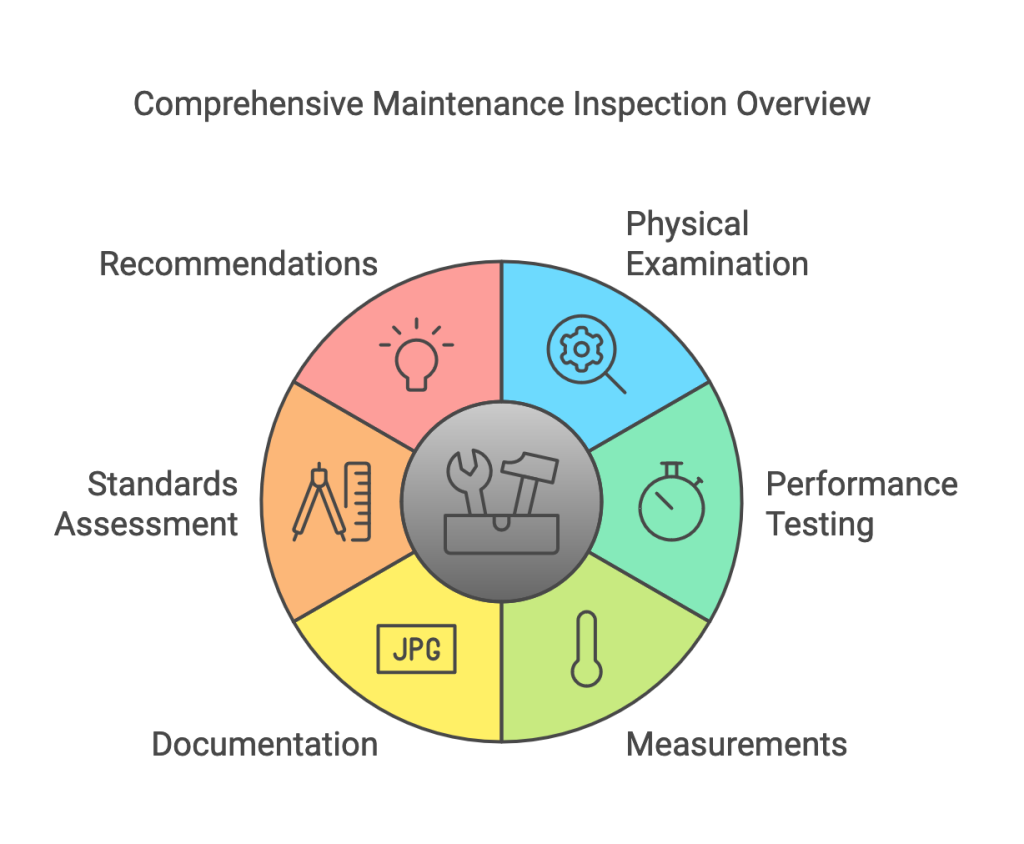
The outcome of a maintenance inspection produces actionable intelligence about the asset’s condition, helping organizations make informed decisions about maintenance activities, repairs, or replacements. This information becomes part of the asset’s historical record, contributing to long-term maintenance planning and lifecycle management.
For example, during a maintenance inspection of an industrial air compressor, an inspector might check the belt tension, measure motor amperage, analyze oil samples, test safety shutoffs, inspect air filters, and evaluate the overall performance against manufacturer specifications.
Types of Maintenance Inspections
Preventive Maintenance
Preventive Maintenance Inspections are scheduled, and routine examinations are conducted at predetermined intervals. For example, a manufacturing facility might inspect its production line equipment every 100 operating hours to check for wear patterns, lubrication levels, and alignment issues.
Predictive Maintenance
Predictive maintenance inspections utilize advanced monitoring techniques and data analysis to forecast potential failures. Consider how vibration analysis on rotating equipment can detect bearing wear before it causes a breakdown or how thermal imaging can identify electrical hotspots in switchgear before they lead to failures.
Condition-Based Inspections
Condition-based inspections are performed based on the actual state of the equipment rather than a fixed schedule. For instance, oil analysis results might trigger an inspection of a gearbox when particulate levels exceed acceptable thresholds.
Compliance Inspection
Compliance Inspections ensure adherence to regulatory requirements and safety standards. These might include annual fire safety system inspections or pressure vessel certifications required by law.
Emergency Inspection
Emergency Inspections occur after unexpected events or failures to assess damage and determine necessary repairs. Think of the detailed inspection required after a piece of equipment experiences an unexpected shutdown or after environmental events like flooding.
Best Practices for Maintenance Organizations
Successful maintenance organizations implement several key practices to ensure effective inspections:
Documentation
Standardize all documentation. Organizations should develop and maintain detailed inspection checklists and procedures that ensure consistency across different inspectors and shifts. These documents should clearly outline inspection points, acceptance criteria, and required actions for various findings.
Training
Training and certification programs help ensure inspectors possess the necessary skills and knowledge. This includes technical expertise and proper use of inspection tools and techniques. For example, thermographers should be certified to interpret infrared images properly, and ultrasound technicians should understand wave propagation principles.
Data Management
Data management systems enable organizations to track inspection histories, trends, and outcomes. Modern computerized maintenance management systems (CMMS) can schedule inspections, store results, and analyze patterns to improve maintenance strategies over time.
Quality Control
Quality control measures should be implemented, such as periodic audits of inspection procedures and results. This might involve having senior technicians review inspection reports or conducting parallel inspections to verify findings.
Importance to Maintenance Organizations
Cost control is perhaps the most significant benefit. Organizations can avoid expensive emergency repairs and production downtime by identifying and addressing issues early. For example, detecting a failing bearing during a routine inspection might cost a few hundred dollars to replace, while waiting for catastrophic failure could result in tens of thousands in repairs and lost production.
Safety enhancement is another crucial aspect. Regular inspections help identify potential hazards before they cause accidents or injuries. This is particularly important in the construction, manufacturing, and transportation industries, where equipment failures can have severe consequences.
Regular inspections significantly improve asset longevity. Equipment that receives consistent attention and maintenance based on inspection findings typically operates more efficiently and lasts longer. This extends the return on investment for capital equipment and reduces the frequency of major replacements.
Proper inspection programs maintain regulatory compliance. Many industries face strict regulatory requirements for equipment safety and operational standards. Well-documented inspection programs help organizations demonstrate their compliance and avoid costly penalties.
Understanding the intricate relationship between these aspects helps maintenance organizations develop comprehensive inspection programs that protect assets, ensure safety, and optimize operational efficiency.
Get a Free WorkTrek Demo
Let's show you how WorkTrek can help you optimize your maintenance operation.
Try for free