What is Maintenance Management?
Maintenance Management is a systematic approach to overseeing and controlling the maintenance activities within an organization to ensure optimal performance, reliability, and longevity of assets and equipment.
A maintenance manager plays a central role in ensuring operational efficiency by managing budgets, overseeing compliance with regulations, and engaging directly with staff and contractors. This role requires a blend of technical expertise, leadership abilities, and a strong understanding of financials to optimize maintenance practices and ensure equipment longevity.
Think of it as an orchestra conductor, coordinating elements such as asset management and maintenance activities to create a harmonious operation.
Definition and Scope
Maintenance management is a systematic approach to maintaining an organization’s physical assets, equipment, and facilities. It encompasses various activities, including planning, scheduling, and executing maintenance tasks and managing maintenance personnel, inventory, and budgets.
Maintenance technicians are key in managing spare parts inventory and streamlining maintenance operations. Having the right supplies readily available minimizes downtime and facilitates smoother workflow and collaboration.
The scope of maintenance management includes all aspects of maintenance, from routine repairs and replacements to predictive and preventive maintenance and from individual equipment to entire facilities.
Effective maintenance management is critical to ensuring physical assets’ reliability, efficiency, and safety, minimizing downtime, and reducing maintenance costs. It involves technical, administrative, and managerial skills and requires a deep understanding of the organization’s operations, assets, and maintenance needs.
By implementing a structured maintenance management process, organizations can ensure that their assets are well-maintained, leading to improved performance and longevity.
Main Objectives of Maintenance Management
The objectives of maintenance management encompass several interconnected goals. A well-structured maintenance process is essential to achieving these objectives, ensuring that all maintenance activities are organized and proactive.
Proactive maintenance strategies are crucial in moving organizations from a reactive stance to a more sustainable and predictive model of equipment care.
First and foremost, it aims to maximize equipment availability and reliability while minimizing downtime. Just as a car needs regular oil changes to run smoothly, industrial equipment requires consistent care to operate efficiently.
Second, maintenance management optimizes resource allocation, ensuring that labor, parts, and tools are used effectively.
Third, it focuses on cost control by preventing expensive breakdowns and extending asset life cycles.
Finally, it strives to maintain safety standards and regulatory compliance, such as the fact that regular health check-ups help prevent severe medical conditions.
Brief History of Maintenance Management
Maintenance was purely reactive in the earliest days of the Industrial Revolution (late 1700s to early 1800s). Machines were run until they broke down, a practice known as the “run-to-failure” approach.
Workers would only fix equipment after it stopped working, leading to unpredictable downtime and significant production losses.
The early 1900s saw the emergence of preventive maintenance, primarily influenced by the rise of mass production, particularly Henry Ford’s assembly lines. During this period, the concept of a maintenance task became more defined, with regular inspections and scheduled activities becoming standard practice. Organizations realized that regular inspections and scheduled maintenance could prevent many breakdowns. This period introduced the concept of planned maintenance intervals, much like how we service modern cars at regular mileage points.
The post-World War II era (1950s-1960s) brought significant advances in the aviation industry with the introduction of Reliability-Centered Maintenance (RCM).
The United Airlines maintenance team developed this approach to improve aircraft safety and reliability. It focused on understanding how equipment fails and what can be done to prevent failures. This marked a shift from time-based maintenance to condition-based maintenance.
The 1970s and 1980s saw the rise of Total Productive Maintenance (TPM) in Japan. TPM revolutionized maintenance by involving machine operators in basic tasks rather than relying solely on maintenance specialists.
This approach, pioneered by Toyota, emphasized that everyone in the organization shares responsibility for equipment care.
The digital revolution of the 1990s and 2000s introduced Computerized Maintenance Management Systems (CMMS). These systems allowed organizations to track maintenance activities, schedule work orders, and manage inventory more efficiently.
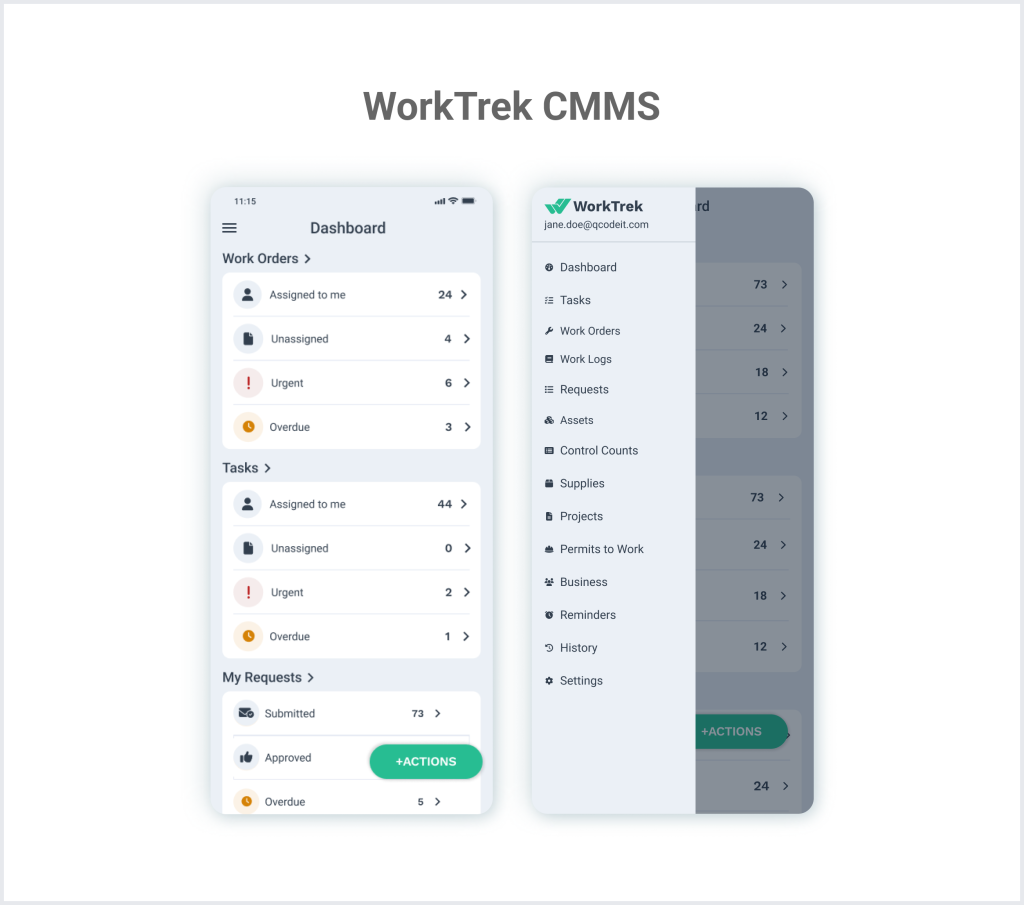
This period also saw the emergence of Predictive Maintenance (PdM), which uses data analysis to predict when equipment might fail.
Today, we’re in the era of Industry 4.0, where Internet of Things (IoT) sensors, artificial intelligence, and machine learning are transforming maintenance management.
Modern systems can monitor equipment health in real-time, predict failures with increasing accuracy, and even automatically schedule maintenance activities based on actual equipment conditions rather than fixed schedules.
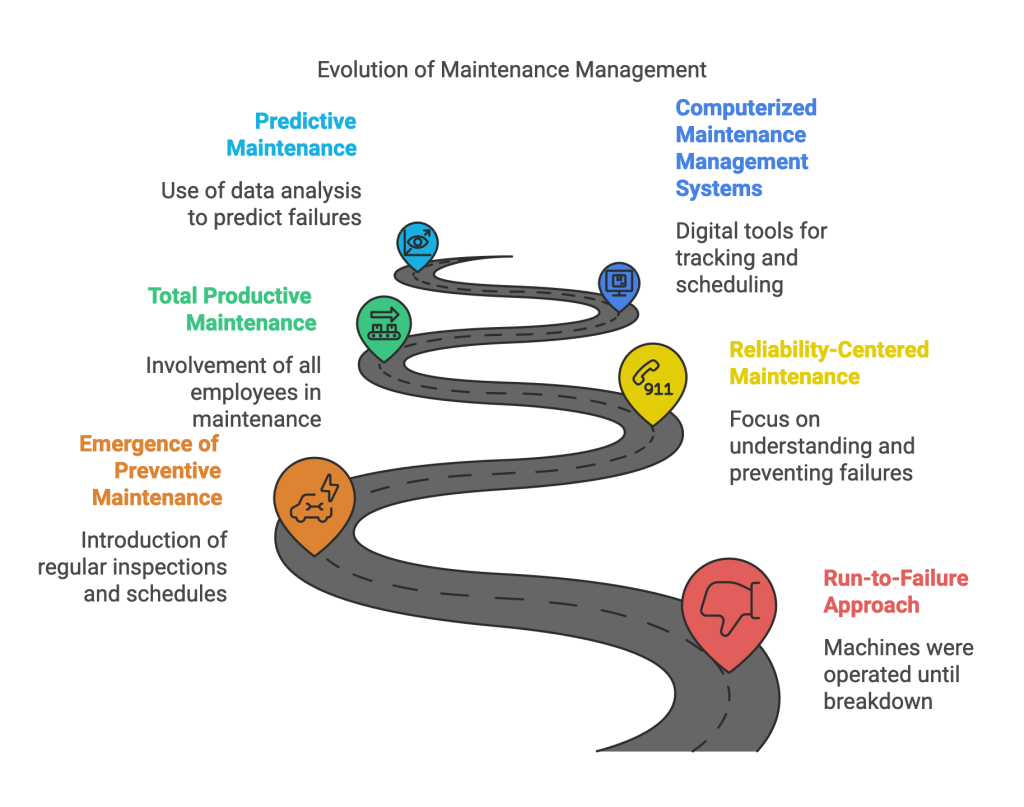
Why is Maintenance Management Important?
The importance of maintenance management cannot be overstated in modern operations. Consider a manufacturing plant: without proper maintenance, production lines could suddenly halt, causing missed deadlines and lost revenue.
More critically, poor maintenance can lead to workplace accidents or environmental incidents. Effective maintenance management helps organizations make data-driven decisions about equipment replacement and upgrades.
It’s like having a skilled financial advisor who helps you make informed investment decisions.
Benefits of Maintenance Management
Maintenance management’s benefits span multiple organizational dimensions, creating immediate and long-term value. Let’s explore these advantages in detail:
Financial Benefits
Maintenance management directly impacts an organization’s bottom line by reducing unexpected equipment failures, which can be extremely costly. When organizations implement proper maintenance strategies, they typically see significant cost savings.
Beyond direct repair costs, preventative maintenance helps avoid expensive emergency repairs, rush parts ordering, and overtime labor costs. Organizations also benefit from extended equipment life, which delays the need for capital investments in replacement equipment.
Operational Efficiency
Well-maintained equipment operates at peak performance levels, producing higher production rates and better quality output. For instance, a manufacturing plant with comprehensive maintenance programs typically sees a 20-30% increase in equipment efficiency.
This improved efficiency comes from reduced downtime, faster production speeds, and fewer quality defects caused by equipment issues. Equipment that receives regular maintenance also consumes less energy, leading to lower utility costs.
Safety Improvements
Proper maintenance management significantly enhances workplace safety. Regular equipment inspections and maintenance help identify potential hazards before they cause accidents.
Studies have shown that organizations with robust maintenance programs experience up to 70% fewer safety incidents than those with reactive maintenance approaches. This protects workers and reduces insurance costs and potential legal liabilities.
Asset Reliability
When organizations implement systematic maintenance management, they gain much better control over their asset reliability. Equipment uptime typically increases by 10-40% from reactive to planned maintenance strategies.
This improved reliability leads to more predictable business operations, better production planning, and increased customer satisfaction through more reliable delivery schedules.
Data-Driven Decision Making
Modern maintenance management systems provide valuable data that helps organizations make better decisions about their equipment. By tracking repair histories, costs, and performance metrics, organizations can identify problematic equipment, optimize maintenance schedules, and make more informed decisions about equipment replacement.
This data-driven approach typically leads to 20-25% better maintenance planning and budgeting accuracy.
Environmental Impact
Proper maintenance, which includes proactive maintenance strategies, leads to more efficient equipment operation, reducing energy consumption and fewer environmental impacts. Well-maintained equipment typically uses 5-15% less energy than poorly maintained equipment.
Additionally, proper maintenance extends equipment life, reducing the environmental impact of manufacturing and disposing of replacement equipment.
Workforce Engagement
Organizations implementing effective maintenance management systems often see improved workforce engagement. Maintenance workers and technicians have clearer responsibilities and better tools to do their jobs effectively.
Operating staff become more involved in equipment care through programs like Total Productive Maintenance. This increased engagement typically leads to 15-25% improvement in workforce productivity and higher job satisfaction rates.
Competitive Advantage
All these benefits combine to create significant competitive advantages. Organizations with effective maintenance management can often offer better prices due to lower operating costs, more reliable delivery due to fewer equipment failures, and higher quality products due to better-performing equipment.
This comprehensive improvement in operations typically translates to 2-5% higher profit margins than competitors with less effective maintenance programs.
Types of Maintenance Management
There are several types of maintenance management, each with its approach and benefits. Understanding these types can help organizations choose the most suitable strategy for their needs:
- Reactive Maintenance: This approach only involves fixing equipment after breaking it down. While it might seem cost-effective initially, it often leads to higher long-term costs due to unexpected downtime and emergency repairs. Reactive maintenance is typically suitable for non-critical, easily replaceable equipment.
- Preventive Maintenance: This strategy involves regular, scheduled maintenance based on time or usage intervals. Like following a car’s recommended service schedule, preventive maintenance aims to minimize breakdowns and extend the lifespan of assets. Time-based and meter-based preventive maintenance are standard methods used in this approach.
- Condition-Based Maintenance: This type of maintenance monitors the performance and condition of assets to determine when maintenance is needed. Organizations can address potential issues by tracking efficiency and performance before they lead to failures. This proactive approach helps maintain optimal equipment performance and reduces unnecessary maintenance tasks.
- Predictive Maintenance Strategies: Predictive maintenance utilizes advanced sensors and data analysis to predict when equipment might fail. This approach ensures maintenance is performed only when necessary, reducing downtime and increasing equipment lifespan. It’s akin to modern cars, which use sensors to alert drivers when service is needed based on actual usage and conditions.
- Reliability-Centered Maintenance: This comprehensive approach evaluates each asset individually to determine the most effective maintenance strategy. By understanding equipment criticality and failure patterns, organizations can implement tailored maintenance plans that maximize efficiency and production capacity.
By combining these different types of maintenance management, organizations can create a hybrid approach that optimizes asset performance and optimizing maintenance costs.
How to Choose the Right Maintenance Management Strategy?
Choosing the right maintenance management strategy requires careful consideration of several factors. Understanding the different types of maintenance management is crucial for selecting the most appropriate strategy for your organization. First, assess your organization’s specific needs and constraints. A hospital’s maintenance needs for critical life-support equipment will differ significantly from a small warehouse’s needs for material handling equipment. Consider these key aspects:
Asset Criticality
Evaluate how crucial each piece of equipment is to your operations. Critical equipment that could cause severe disruptions if it fails might need more intensive preventive maintenance.
Resource Availability
Consider your available maintenance staff, expertise, tools, and budget. A sophisticated predictive maintenance program might be ideal but impractical if you lack the necessary resources.
Operational Context
Think about your operating environment, production schedules, and access to equipment. A 24/7 operation might need different maintenance approaches compared to a single-shift facility.
Implementing Maintenance Management
Setting up an Efficient Maintenance Department
Creating an efficient maintenance department is crucial for effective maintenance management. Here are some essential steps to set up a well-structured maintenance department:
- Develop a Maintenance Strategy: Start by developing a maintenance strategy that aligns with the organization’s goals and objectives. This strategy should outline the types of maintenance management to be implemented and the specific maintenance tasks required for each asset.
- Assign Roles and Responsibilities: Clearly define the roles and responsibilities of maintenance personnel, including maintenance managers, technicians, and workers. Each team member should understand their duties and how they contribute to the overall maintenance strategy.
- Establish Maintenance Schedules: Create detailed preventive and predictive maintenance schedules. These schedules should be based on asset criticality, usage patterns, and manufacturer recommendations to ensure timely and effective maintenance.
- Implement a CMMS: Utilize a computerized maintenance management system (CMMS)like WorkTrek to track and manage all maintenance activities. A CMMS can help streamline work order management, inventory control, and enterprise asset management, making maintaining an organized and efficient maintenance department easier.
- Provide Training and Support: Ensure that all maintenance personnel receive adequate training and support to perform their jobs effectively. Regular training sessions can help maintenance workers stay updated on the latest maintenance techniques and best practices.
By following these steps and implementing continuous improvement, organizations can establish an efficient maintenance department well-equipped to manage maintenance operations effectively. This structured approach enhances maintenance efficiency and contributes to improved asset reliability and reduced maintenance costs.
Maintenance Management Software
What is Maintenance Management Software?
Maintenance management software, otherwise known as a computerized maintenance management system (CMMS), is a centralized platform designed to streamline and manage maintenance operations across an organization.
This software automates various maintenance processes, including asset tracking, maintenance scheduling, and work order management, all from a single interface.
By leveraging maintenance management software, organizations can enhance their maintenance efficiency, reduce downtime, and ensure that all maintenance tasks are performed promptly and organized.
Computerized Maintenance Management System (CMMS)
A computerized maintenance management system (CMMS) is a powerful tool that helps organizations manage their maintenance operations more effectively. It provides a centralized platform for tracking and managing all maintenance activities, including work orders, inventory, and asset performance.
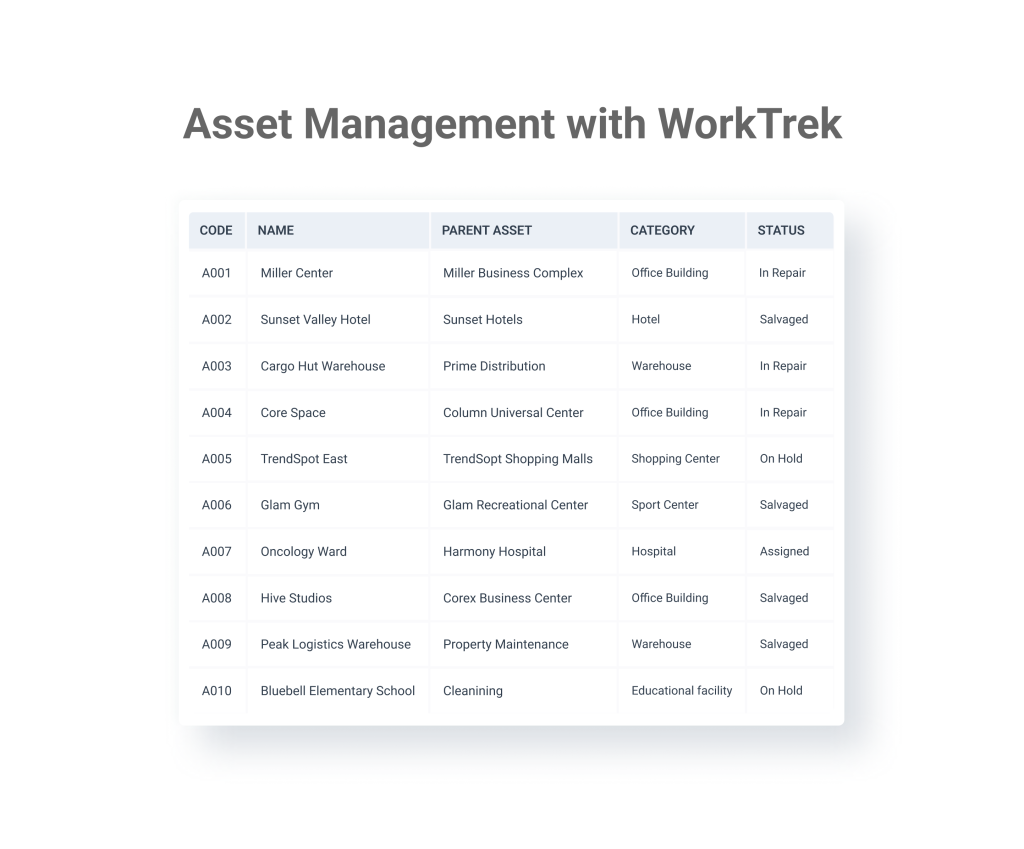
Using a CMMS can reduce maintenance costs, improve asset reliability, and increase overall productivity. The system allows maintenance managers to schedule preventive and predictive maintenance tasks, monitor equipment health, and generate detailed reports on maintenance activities.
This data-driven approach enables better decision-making and helps organizations optimize their maintenance processes.
Get a Free WorkTrek Demo
Let's show you how WorkTrek can help you optimize your maintenance operation.
Try for free