What is Maintenance Planning?
Maintenance Planning is a systematic approach to organizing, scheduling, and executing maintenance activities to ensure equipment reliability and optimal performance. The maintenance planning process involves determining what maintenance work needs to be done, when it should be performed, and what resources are required.
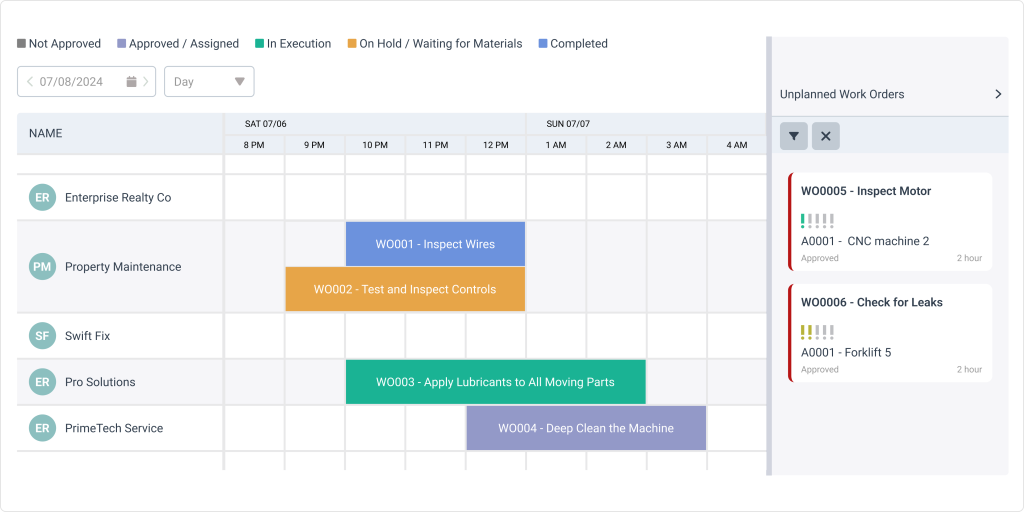
žThink of it like planning the ongoing care of your home—rather than waiting for things to break, you develop a structured approach to inspecting, repairing, and replacing components based on their condition and importance.
Definition and Importance
Maintenance planning is a critical process that involves identifying, scheduling, and organizing maintenance activities to ensure assets operate efficiently and reliably. It is essential for successful asset management, as it complements maintenance scheduling to ensure efficient and cost-effective maintenance.
Maintenance planning and scheduling can help organizations reduce downtime, minimize costs, and ensure the reliability and longevity of assets. It can also help with asset availability and optimize allocating resources.
Think of maintenance planning as the backbone of your maintenance strategy. It involves identifying what maintenance tasks must be performed, scheduling them at the right times, and organizing the necessary resources to carry them out.
This structured approach ensures that maintenance activities are timely and efficient, reducing the likelihood of unexpected equipment failures and costly repairs.
Benefits of Maintenance Planning Process
Implementing effective maintenance planning and scheduling can benefit organizations. One benefit is reduced downtime, as potential issues can be identified and addressed before they lead to equipment failures.
Additionally, maintenance planning helps optimize resource allocation, ensuring that maintenance teams are working efficiently and productively. This, in turn, leads to cost savings, as the need for emergency repairs and replacements is minimized.
In essence, maintenance planning is about being proactive rather than reactive. It involves identifying potential problems before they occur and taking steps to prevent them, ensuring that assets remain reliable and operational for as long as possible.
How’s the Maintenance Planning Process Used?
Maintenance Planning operates through several interconnected processes. A maintenance plan is crucial for organizing tasks, resources, and timelines to ensure equipment operates efficiently.
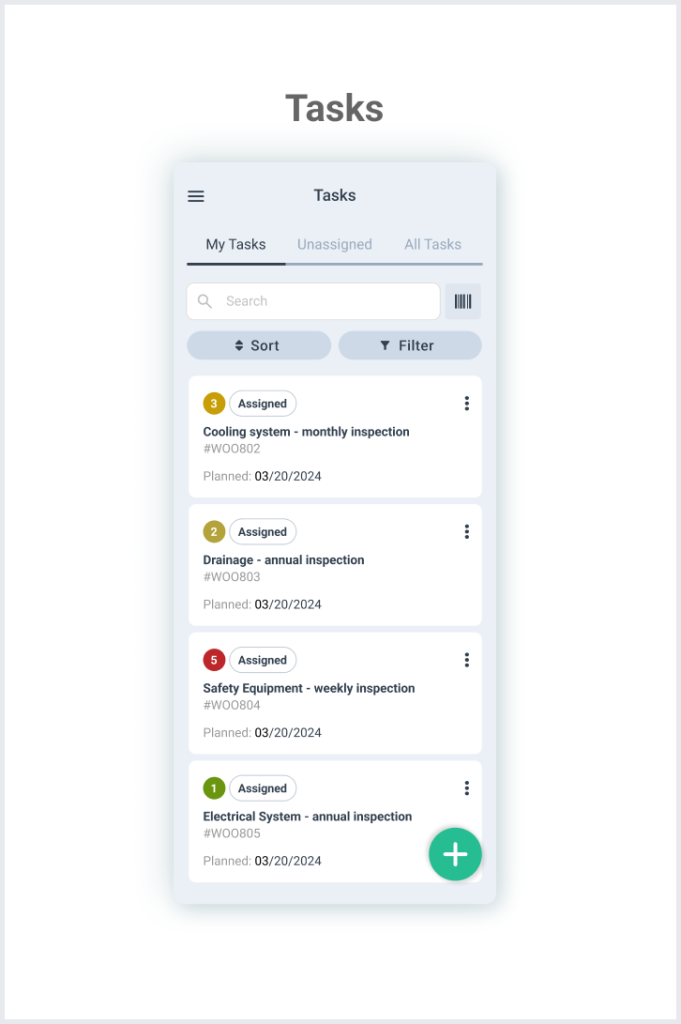
Identify Work
Work Identification involves determining what maintenance tasks are needed. This comes from multiple sources: equipment inspections, operator reports, predictive maintenance data, and manufacturer recommendations. For example, a manufacturing facility might identify needed maintenance through vibration analysis of critical motors, visual inspections of conveyor belts, and automated sensor readings from production equipment.
Maintenance planners are critical in organizing and coordinating these activities to ensure efficiency and effectiveness.
Assess Work
Resource Assessment determines what’s needed to complete each maintenance task. The maintenance department plays a crucial role in organizing and planning these activities, ensuring that required skills, tools, parts, documentation, and time requirements are considered. A maintenance planner at a power plant might determine that a pump overhaul requires two technicians with specific certifications, specialized tools, replacement seals, and a four-hour window when the system can be taken offline.
Maintenance Scheduling
Scheduling coordinates maintenance activities with production needs and resource availability. Maintenance scheduling principles are essential guidelines that enhance productivity in maintenance operations. This involves balancing urgent repairs with preventive maintenance while considering equipment criticality and operational impact. For instance, a food processing plant might schedule major equipment maintenance during planned production downtime to minimize disruption.
Prepare for Work
Work Preparation ensures everything needed for maintenance tasks is ready before work begins. This includes gathering parts, tools, permits, and safety equipment, plus coordinating with operations and other departments. A refinery maintenance planner would ensure all safety permits are approved, required parts are on hand, and specialized equipment is reserved before scheduling critical equipment maintenance. Effective coordination between operations and maintenance teams is crucial to align operational schedules and resource availability, ensuring the successful execution of maintenance plans.
Types of Maintenance Planning Strategies
Organizations can use several types of maintenance planning strategies to achieve their maintenance goals. These include:
Predictive Maintenance
Predictive maintenance involves using advanced technologies, such as machine sensors and data analytics, to forecast potential equipment failures. This approach enables organizations to prevent equipment breakdowns and reduce downtime proactively.
Predictive maintenance requires significant investment in technology and personnel but can provide substantial cost savings and improved asset reliability.
Imagine being able to predict when equipment is likely to fail and taking action before it happens. That’s the power of predictive maintenance.
Organizations can continuously monitor equipment conditions and analyze data to identify patterns and trends that indicate potential issues. This allows maintenance teams to address problems before they escalate, reducing the risk of unexpected breakdowns and costly repairs.
Preventive Maintenance
Preventive maintenance, also known as proactive maintenance, involves periodically inspecting or repairing equipment to avoid debilitating malfunctions. This approach is typically time-based or event-driven.
Preventive maintenance aims to increase the lifespan of assets by avoiding malfunctions and reducing the need for costly repairs.
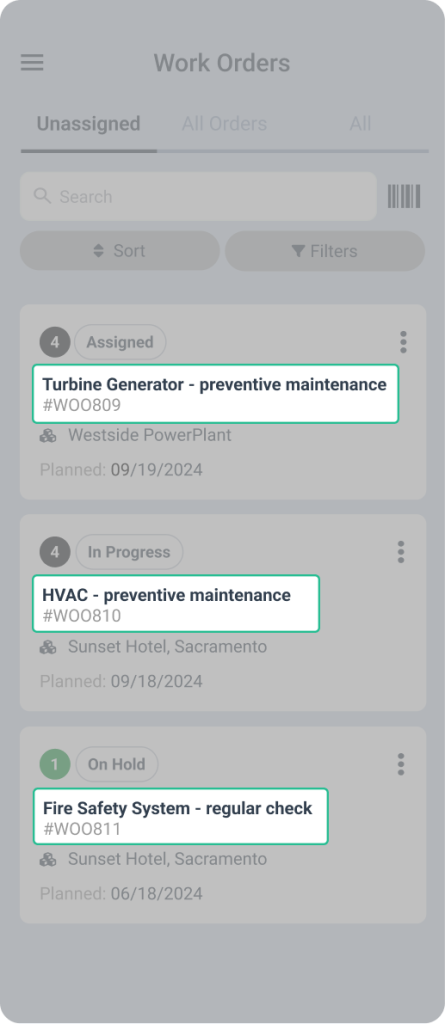
Think of preventive maintenance as regular check-ups for your equipment. Just as you would schedule routine medical exams to catch health issues early, preventive maintenance involves scheduling regular inspections and maintenance tasks to keep equipment in optimal condition.
By addressing minor issues before they become major problems, organizations can extend the lifespan of their assets and ensure they operate reliably.
When to use Maintenance Planning
This approach works particularly well in:
Complex industrial environments where equipment downtime is costly.
Maintenance plans are crucial in optimizing operations across different sectors, including oil and gas, mining, and power generation. Chemical processing plants, for example, benefit from careful maintenance planning to minimize production interruptions.
Facilities with multiple interdependent systems
Airports must coordinate maintenance across numerous systems, such as baggage handling, security equipment, and building services.
Operations where safety and regulatory compliance are critical.
Nuclear power plants require meticulous maintenance planning to ensure safety and meet regulatory requirements.
Environments with expensive or critical equipment.
Manufacturing facilities with high-value production equipment need well-planned maintenance to protect their investment and improve equipment performance.
Benefits of Effective Maintenance Planning
Effective maintenance planning has several benefits, including:
- Reduced downtime: By identifying and addressing potential issues ahead of time, organizations can reduce downtime and minimize the impact of equipment failures.
- Increased efficiency: Maintenance planning enables organizations to optimize resource allocation and streamline maintenance activities, increasing efficiency and productivity.
- Improved safety: Organizations can improve safety and reduce the risk of accidents by identifying potential hazards and taking proactive measures to mitigate them.
- Cost savings: Maintenance planning can help organizations reduce costs by minimizing the need for costly repairs, reducing energy consumption, and extending the lifespan of assets.
- Increased equipment lifespan: By performing regular maintenance and addressing potential issues ahead of time, organizations can extend the lifespan of their equipment and reduce the need for costly replacements.
Organizations can achieve these benefits by implementing effective maintenance planning and scheduling and improving their overall maintenance performance. Maintenance planning is not just about keeping equipment running; it’s about optimizing the entire maintenance process to ensure that resources are used efficiently, costs are minimized, and assets remain reliable and safe.
Implementation strategies:
Successful maintenance planning implementation typically involves:
Establishing a Planning Organization that defines roles and responsibilities. This might include dedicated planners, schedulers, and coordinators working together to manage maintenance activities. Planning is crucial for creating structured plans that optimize resource allocation and minimize downtime.
Developing Standard Procedures for common maintenance tasks. These procedures detail step-by-step instructions, safety requirements, and resource needs for routine work.
Creating Planning Horizons that determine how far in advance different types of work should be planned. Emergency work might be planned hours ahead, while major overhauls could be planned months in advance.
Technology Tools to Improve Maintenance Planning
Implementing Supporting Systems including:
- Computerized Maintenance Management Systems (CMMS)
- Asset management databases
- Inventory control systems
- Work order tracking systems
- Resource scheduling tools
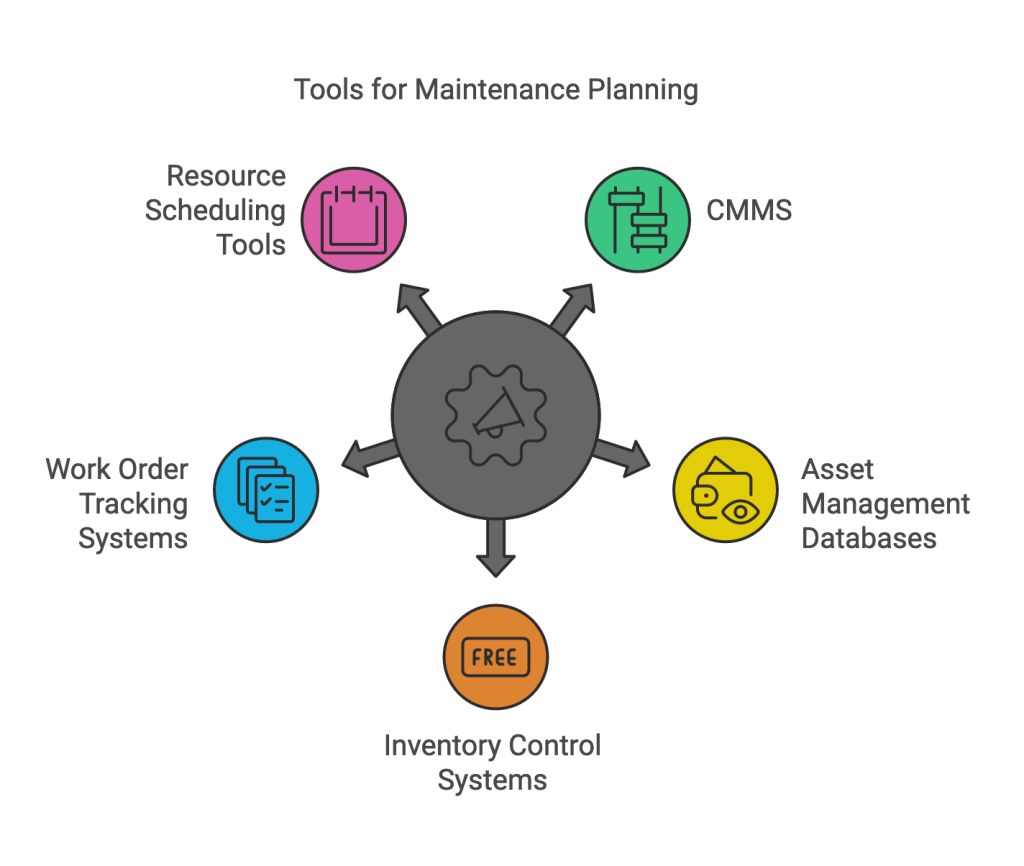
Common Challenges
Emergency work disrupting planned maintenance requires effective prioritization systems and emergency response procedures. Maintenance managers might dedicate specific resources to emergency work while protecting planned maintenance schedules.
Reactive maintenance, a strategy that follows a ‘run-to-failure’ approach, is often used when equipment is nonessential or operations are low-cost.
Resource constraints need careful management through prioritization and scheduling. Successful organizations often cross-train personnel and maintain flexible resource pools.
Regular planning meetings and integrated information systems can address communication gaps between maintenance, operations, and other departments.
The benefits of successful implementation include:
- Improved equipment reliability
- Reduced maintenance costs
- Better resource utilization
- Enhanced safety performance
- More predictable maintenance budgets
- Improved regulatory compliance
- Better coordination with operations
- Improved key performance indicators
- Better spare parts management
What are some Advanced Concepts to Consider for Preventive Maintenance?
Integration with Reliability Centered Maintenance (RCM) to optimize maintenance strategies based on equipment criticality and failure modes. The maintenance team is crucial in executing tasks efficiently and effectively, ensuring that maintenance plans are implemented smoothly.
Risk-based Planning considers the probability and consequence of equipment failure when prioritizing work.
Planning Performance Metrics that measure effectiveness through indicators like schedule compliance, work order backlog, and emergency work percentage.
Get a Free WorkTrek Demo
Let's show you how WorkTrek can help you optimize your maintenance operation.
Try for free