What is Material Requirements Planning (MRP)?
Material Requirements Planning is a production planning, scheduling, and inventory control system that helps organizations manage manufacturing processes. Developed in the 1960s, MRP addresses a fundamental manufacturing challenge: ensuring that the right materials are available at the right time to meet production needs while minimizing excess inventory.
Think of MRP like planning an elaborate multi-course dinner party. Just as a chef needs to determine what ingredients to buy, when to start each dish, and how to coordinate cooking times so everything is ready together, MRP helps manufacturers coordinate all the components needed to build their products.
How is it used?
MRP operates through a sophisticated process that begins with a master production schedule and works backward to determine component requirements:
First, the system takes production requirements from customer orders and forecasts, creating a master schedule showing what products must be completed and when. For instance, a bicycle manufacturer might produce 1,000 mountain bikes next month.
The system then examines each product’s bill of materials (BOM), which details every component needed. For our bicycle example, the BOM would list frames, wheels, gears, chains, and all other parts, showing how many of each are needed per bike.
MRP calculates time-phased requirements by considering lead times for each component. If frames take three weeks to arrive and wheels take two weeks, the system determines when to order each part to meet the production schedule.
The system compares these requirements against current inventory levels and already-planned orders. It considers safety stock levels and minimum order quantities and then generates recommendations for purchase orders and production orders.
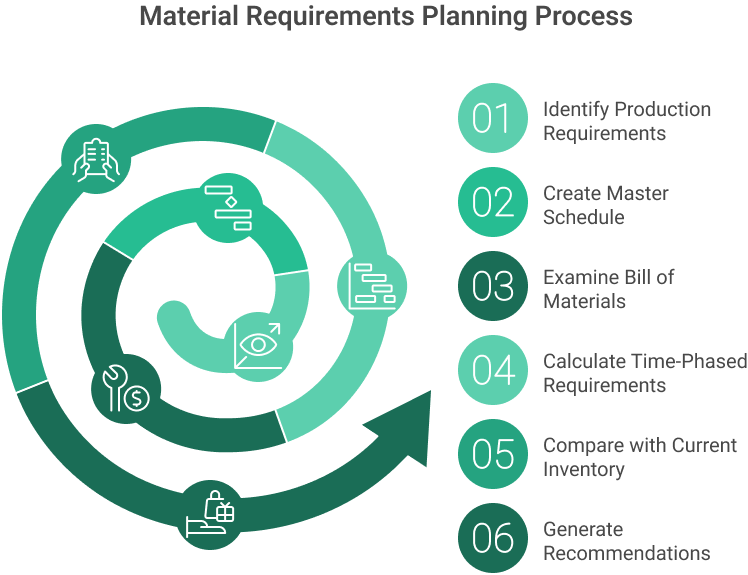
Optimal Situation to use MRP
MRP works particularly well in:
Manufacturing environments with complex products that require many components. Automotive manufacturing, for example, manages thousands of parts that must come together at precise times.
Operations with relatively predictable demand and standard products. Computer manufacturers can effectively use MRP because they know exactly what goes into each model.
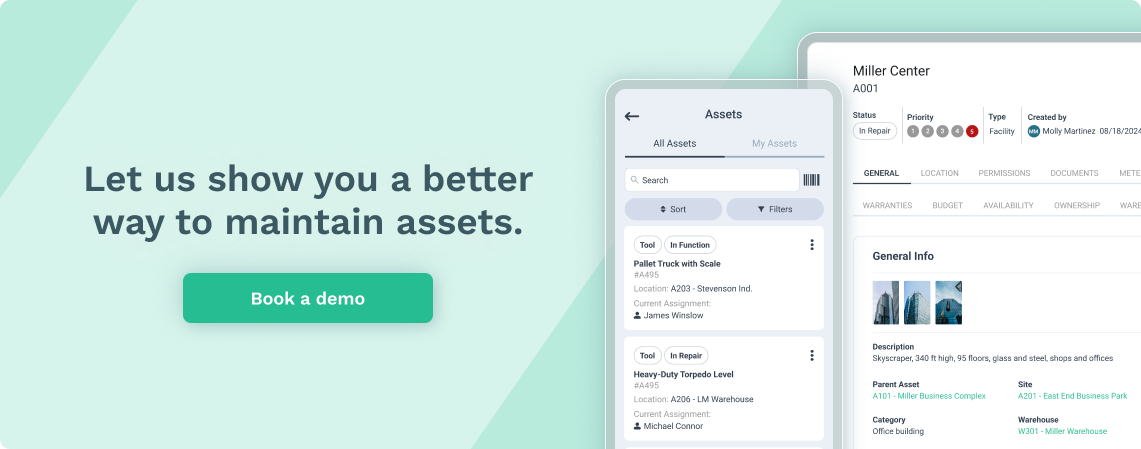
Environments where component lead times vary significantly. Electronics manufacturers might need to order some components months in advance while others are readily available.
Industries where material costs represent a significant portion of product costs. Appliance manufacturers use MRP to manage expensive components and carefully avoid excess inventory.
Implementation Strategies
Successful MRP implementation requires several key elements:
Data accuracy is crucial – organizations must maintain precise records of:
- Inventory levels for all items
- Bills of materials for all products
- Lead times for all components
- Production capacities and constraints
System integration connects MRP with other business systems. Modern implementations often integrate with:
- Customer order management systems
- Supplier management systems
- Shop floor control systems
- Financial management systems
Training programs ensure all users understand how their roles affect MRP success. Production planners learn to maintain accurate schedules, inventory personnel know the importance of accurate counts, and buyers learn to manage supplier lead times effectively.
Common Challenges and Solutions
System complexity often requires significant training and change management. Organizations typically implement MRP in phases, starting with simpler products or processes.
Data accuracy demands constant attention. Successful companies establish regular audit procedures and make accuracy a key performance metric.
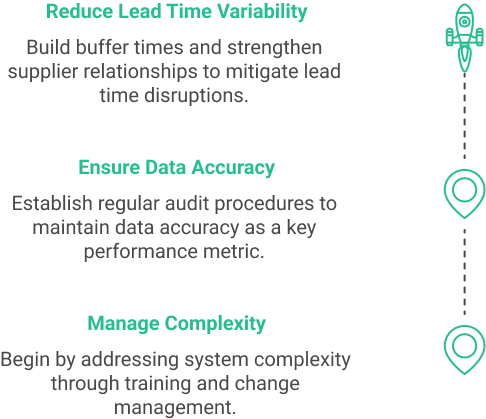
Lead time variability can disrupt MRP calculations. To improve reliability, organizations often build buffer times into their planning and develop strong supplier relationships.
The benefits of successful implementation include:
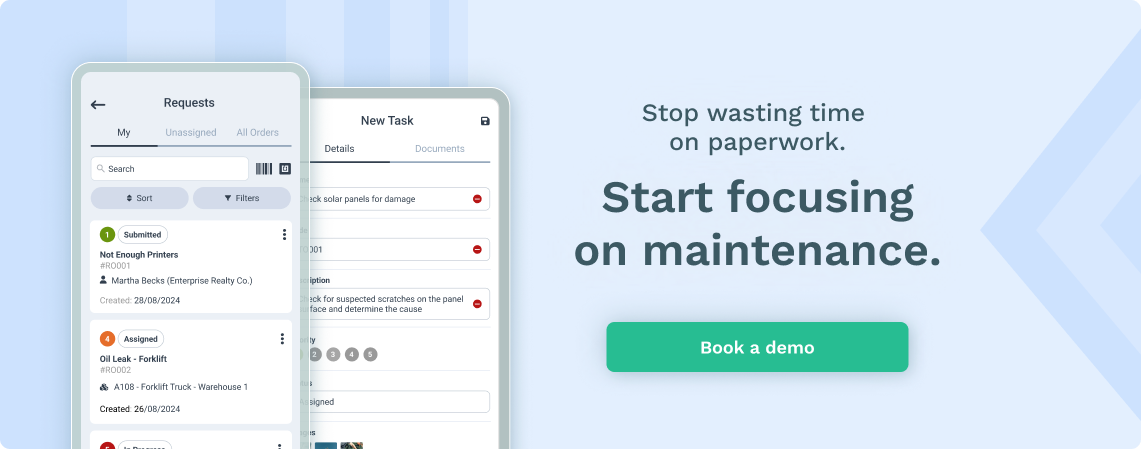
- Reduced inventory carrying costs
- Improved production efficiency
- Better on-time delivery performance
- Reduced stockouts and production delays
- More effective capacity planning
- Better coordination with suppliers
What are some Advanced MRP Features?
Modern MRP systems often include additional capabilities:
Capacity Requirements Planning (CRP)
CRP ensures that planned orders don’t exceed production capacity. The system might adjust order timing to balance workload across production centers.
What-if Analysis
What-if analysis allows planners to evaluate different scenarios. For example, how would a 20% increase in demand affect material requirements and capacity needs?
Pegging traces
Pegging traces demand components back to specific customer orders or forecast requirements, helping prioritize material allocation when supplies are limited.
Get a Free WorkTrek Demo
Let's show you how WorkTrek can help you optimize your maintenance operation.
Try for free