What is Mean Time Between Failure (MTBF)?
Mean Time Between Failures (MTBF) is a key performance indicator measuring the average time an asset or piece of equipment operates before it experiences a failure. It is commonly used to assess equipment reliability, particularly in industries where asset uptime is critical, such as manufacturing, aerospace, and energy production. The higher the MTBF, the more reliable the equipment is.
MTBF is calculated by dividing the equipment’s total operational time by the number of failures. For example, if a machine runs for 1000 hours and fails twice, the MTBF would be 500 hours.
MTBF is a critical metric in maintenance planning because it helps organizations predict when failures are likely to occur, allowing them to schedule preventive maintenance or replacements before breakdowns happen. It is also used to evaluate the effectiveness of maintenance strategies—if MTBF increases over time, it indicates that maintenance efforts are improving asset reliability.
While MTBF provides valuable insights into equipment reliability, it is most useful when combined with other metrics, such as Mean Time to Repair (MTTR), to give a complete picture of maintenance performance.
How is MTBF Calculated?

MTBF measures the average time between system failures during normal operation. The basic formula for MTBF is:
MTBF = Total Operating Time / Number of Failures
However, to understand this properly, let’s break down how you would calculate this in practice:
First, you need to gather your operational data over a significant period. Let’s say you’re monitoring 100 identical devices for 1,000 hours each. Your total operating time would be 100,000 hours (100 devices × 1,000 hours).
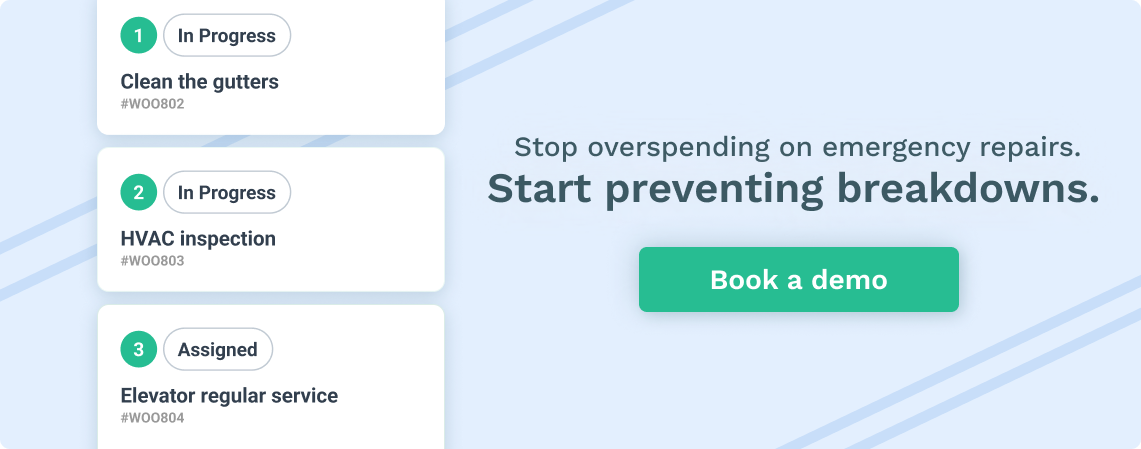
Next, you count the number of failures that occurred during this period. Let’s say you observed 20 failures across all devices. Using our formula:
MTBF = 100,000 hours / 20 failures = 5,000 hours
This means that, on average, you can expect a failure every 5,000 operating hours.
Some important considerations when calculating MTBF:
- Operating Time vs. Calendar Time: Only count actual operating time, not idle time or maintenance periods. If a machine runs 8 hours per day, you wouldn’t count the other 16 hours.
- What Constitutes a Failure: You need to define what counts as a failure clearly. Does a minor glitch count in a computer system, or only complete system crashes? These definitions significantly impact your calculations.
- Repair Time: MTBF doesn’t include repair time. That’s a separate metric called Mean Time To Repair (MTTR). Together, MTBF and MTTR give you the full picture of system availability.
A practical example would be helpful here: Imagine you’re managing a fleet of delivery trucks. Over one year, you track three trucks:
- Truck A: 3,000 hours operation, 2 failures
- Truck B: 2,800 hours operation, 1 failure
- Truck C: 3,200 hours operation, 3 failures
Total operating time = 9,000 hours Total failures = 6
MTBF = 9,000 / 6 = 1,500 hours
This means you can expect, on average, one truck to fail every 1,500 operating hours.
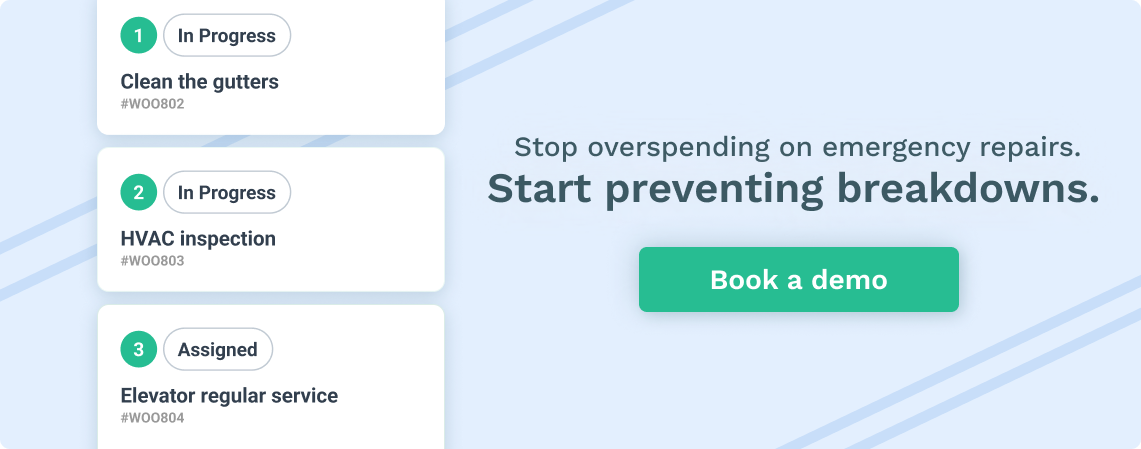
MTBF Calculator
Calculate Mean Time Between Failures (MTBF) by entering your operational data below.
Results:
Get a Free WorkTrek Demo
Let's show you how WorkTrek can help you optimize your maintenance operation.
Try for free