What is Meat Time to Repair (MTTR)?
Mean Time to Repair (MTTR) is a maintenance metric that measures the average time it takes to repair equipment after a failure occurs. MTTR is used to evaluate the efficiency of maintenance teams in restoring equipment to operational conditions and is a key performance indicator for maintenance response times.
MTTR is calculated by dividing the total repair time by the number of failures. For example, if a piece of machinery breaks down five times and the total repair time is 10 hours, the MTTR would be 2 hours.
A low MTTR indicates that maintenance teams can respond quickly and efficiently to equipment failures, minimizing downtime and disruption to operations. Conversely, a high MTTR may signal inefficiencies in the repair process, such as delays in diagnosing the problem, sourcing spare parts, or completing the repair.
Improving MTTR is a priority for many organizations, as faster repair times lead to increased equipment availability, higher productivity, and lower downtime costs. Strategies to reduce MTTR include improving technician training, ensuring that spare parts are readily available, and implementing better diagnostic tools to speed up troubleshooting.
MTTR Calculator
Mean Time To Repair (MTTR) measures the average time required to repair a failed system and return it to operational status. This includes:
- Detection time
- Diagnosis time
- Repair time
- Testing time
Results:
How is MTTR Calculated?

Source: WorkTrek
Let me explain how Mean Time To Repair (MTTR) is calculated and why it’s a crucial maintenance and reliability engineering metric.
MTTR measures the average time it takes to repair a system and return it to full operation after a failure. Think of it as measuring how long your car typically spends in the repair shop each time something goes wrong.
The basic formula for MTTR is:
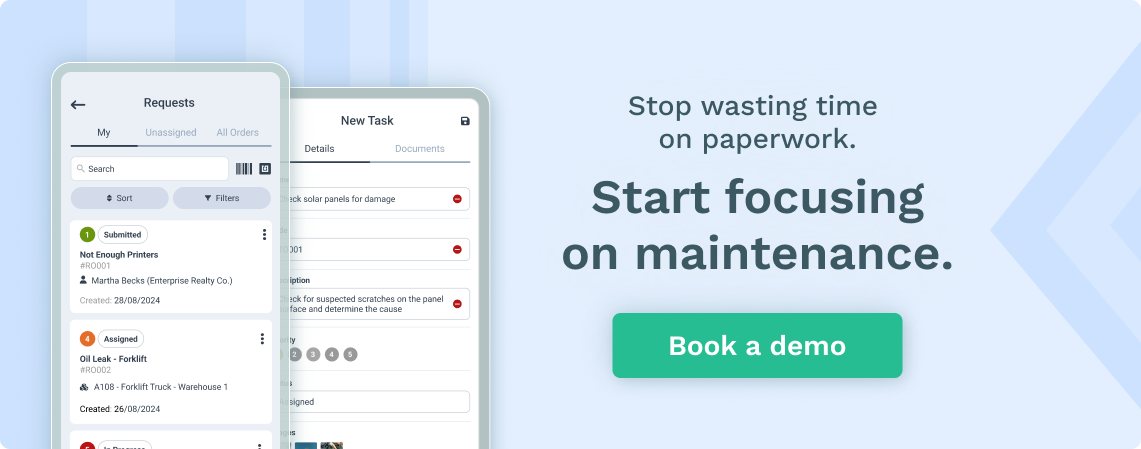
MTTR = Total Repair Time / Number of Repairs
However, to truly understand MTTR calculation, we need to break down what counts as “repair time.” The repair clock starts running the moment a failure is detected and includes four key phases:
- Detection Time: The time it takes to realize there’s a problem. For example, if a machine fails at 9:00 AM but nobody notices until 9:15 AM, those 15 minutes count toward the repair time.
- Diagnosis Time: The period spent figuring out what’s wrong. Just like a doctor examining a patient, technicians need time to identify the root cause of the failure.
- Actual Repair Time: The hands-on time spent fixing the problem, including getting parts and making the repair.
- Testing Time: The time needed to verify that the repair worked and the system is operating correctly.
Let’s walk through a practical example:
Imagine you’re managing a production line that had three failures last month:
First failure:
- Detection: 15 minutes
- Diagnosis: 45 minutes
- Repair: 2 hours
- Testing: 30 minutes
Total: 3.5 hours
Second failure:
- Detection: 5 minutes
- Diagnosis: 30 minutes
- Repair: 1 hour
- Testing: 25 minutes
Total: 2 hours
Third failure:
- Detection: 10 minutes
- Diagnosis: 1 hour
- Repair: 3 hours
- Testing: 50 minutes
Total: 5 hours
To calculate MTTR:
Total Repair Time = 3.5 + 2 + 5 = 10.5 hours
Number of Repairs = 3
MTTR = 10.5 hours / 3 = 3.5 hours
This means that, on average, it takes 3.5 hours to get your system back up and running after a failure.
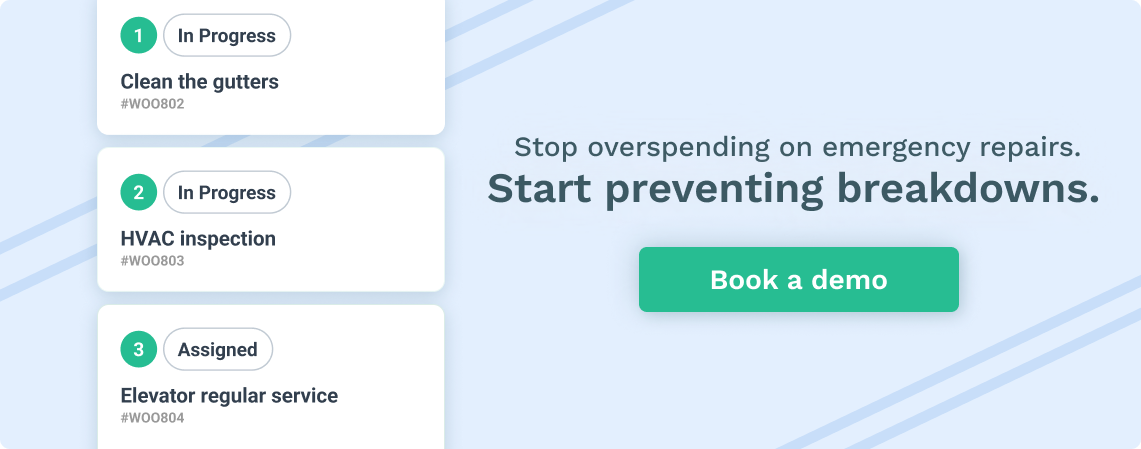
Understanding your MTTR helps in several ways:
- It shows how efficient your maintenance team is
- It helps identify where delays commonly occur (detection, diagnosis, repair, or testing)
- It can justify investments in better monitoring systems (to reduce detection time) or diagnostic tools (to reduce diagnosis time)
- It helps set realistic expectations for downtime when failures occur
One important note: MTTR should be considered alongside metrics like Mean Time Between Failures (MTBF). Together, they give you a complete picture of system reliability and maintainability.
For example, a system with a high MTBF and a high MTTR might still have significant downtime issues that need to be addressed.
Get a Free WorkTrek Demo
Let's show you how WorkTrek can help you optimize your maintenance operation.
Try for free