What is Non-Destructive Testing?
Non-Destructive testing (NDT) refers to various analytical techniques used to evaluate and inspect materials, components, or systems without damaging the original item being tested.
Think of it like a doctor using an X-ray or ultrasound to examine a patient—they can see what’s happening inside without having surgery.
In industrial applications, NDT allows inspectors to detect internal or surface defects, measure thickness, determine material properties, and assess structural integrity while keeping the test piece fully functional.
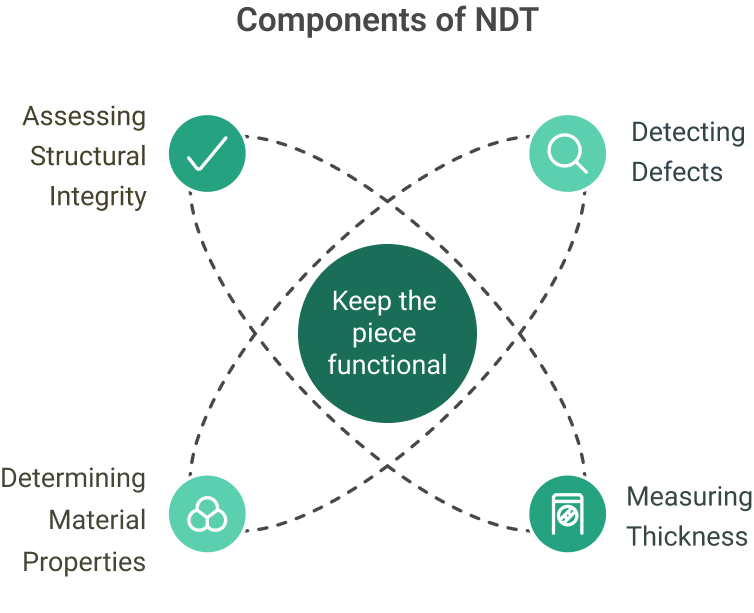
This is particularly valuable for examining critical aerospace, manufacturing, and infrastructure components, where destroying a part for inspection would be impractical and costly.
The term “non-destructive” contrasts with destructive testing methods, where test pieces must be permanently altered or broken to evaluate their properties.
For instance, while a destructive test might involve cutting a welded joint to examine its internal structure, NDT techniques like radiography or ultrasonic testing can reveal the same information while preserving the weld’s integrity.
Various NDT methods exist, each suited to different inspection needs. Common examples include visual testing, magnetic particle inspection, liquid penetrant testing, radiographic testing, ultrasonic testing, and eddy current testing.
Each method uses different physical principles to reveal specific discontinuities or material characteristics.
Non-Destructive Testing Methods
Let me explain the main NDT testing methods used in the industry today. Each method serves specific inspection needs and works on different physical principles.
Visual Testing (VT)
This is the most basic and widely used NDT method. Inspectors examine the surface of materials either directly with their eyes or using optical tools like borescopes and magnifying glasses. Think of it like a very detailed visual inspection you might do when buying a used car – looking for obvious damage, wear patterns, or irregularities. While simple, VT requires significant expertise to spot subtle indicators of potential problems.
Magnetic Particle Testing (MT)
This method works specifically on ferromagnetic materials like steel. Imagine spreading iron filings on a magnet—they align with the magnetic field. Similarly, in MT, we magnetize the test piece and apply magnetic particles (usually in a liquid suspension). If there are any surface or near-surface defects, the magnetic field leakage attracts these particles, making the defects visible. It’s particularly effective for finding small surface cracks in welds or machinery parts.
Liquid Penetrant Testing (PT)
This method is excellent for finding surface-breaking defects in any non-porous material. Think about how water seeps into cracks in concrete – PT works similarly. A colored or fluorescent liquid penetrant is applied to the surface and given time to seep into any defects.
After cleaning the surface, a developer is applied to draw the penetrant back out, making defects visible. Aerospace commonly uses this method to inspect turbine blades and structural components.
Radiographic Testing (RT)
This works much like medical X-rays. Radiation passes through the test piece and onto a detector (film or digital), creating an image showing internal features.
Denser areas appear darker, while defects like voids or cracks appear lighter. This method excels at finding internal defects in welds and castings. Industrial radiography typically uses stronger radiation sources than medical X-rays to penetrate thicker materials.
Ultrasonic Testing (UT)
Like the sonar submarines use, UT sends high-frequency sound waves into materials. These waves bounce back when they hit defects or material boundaries.
By analyzing these echoes, inspectors can locate and size internal flaws, measure thickness, and evaluate material properties. Modern UT equipment can create detailed 3D images of internal structures, making it invaluable for inspecting complex components.
Eddy Current Testing (ET)
This method uses electromagnetic induction to detect surface and near-surface defects in conductive materials. When an alternating magnetic field is applied to a conductor, it generates circular electrical currents (eddy currents).
Defects disturb these currents, creating detectable changes in the magnetic field. It’s particularly useful for inspecting heat exchanger tubes and aircraft structures, as it can work through thin coatings and doesn’t require direct contact.
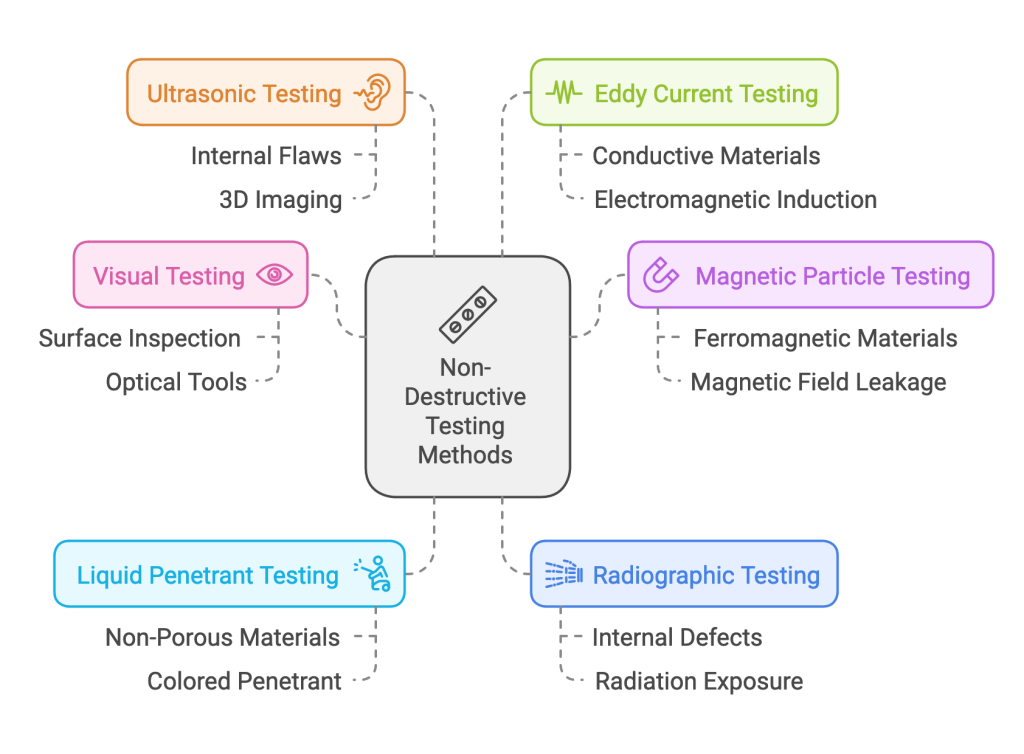
How do Maintenance Organizations use NDT?
Maintenance organizations use NDT as a critical predictive and preventive maintenance tool. Let me explain how this works in practice.
At its core, NDT helps maintenance teams make informed decisions about equipment health without disrupting operations. Think of it like a doctor using various diagnostic tools to assess a patient’s health and make treatment decisions.
Just as a doctor might use blood tests, X-rays, and physical examinations to build a complete picture of asset condition, maintenance teams use different NDT methods.
NDT serves as an early warning system in preventive maintenance. For example, ultrasonic testing might be used to measure the thickness of a pipe wall in a chemical plant.
By tracking these measurements over time, maintenance teams can predict when the pipe will need replacement before it fails. This allows them to schedule maintenance during planned downtimes rather than dealing with emergency repairs.
Condition-based maintenance programs rely heavily on NDT for decision-making. Consider a large industrial gearbox in a manufacturing facility.
Using a combination of vibration analysis and oil analysis (both forms of NDT), maintenance teams can detect early signs of wear, misalignment, or lubrication issues. This information helps them determine whether immediate intervention is needed or the equipment can safely continue operating.
NDT also plays a crucial role in quality assurance after repairs. When a critical weld is repaired, for instance, radiographic testing might be used to verify the repair’s integrity before returning the equipment to service.
This verification step helps prevent premature failures and ensures maintenance work meets the required standards.
Risk-based inspection programs use NDT findings to optimize maintenance schedules. By identifying high-risk areas through initial NDT inspections, maintenance teams can focus their resources where they’re most needed. For example, if corrosion mapping of a storage tank reveals certain areas are deteriorating faster than others, inspection frequencies can be adjusted accordingly.
Many maintenance organizations integrate NDT results into their computerized maintenance management systems (CMMS). This integration allows them to:
- Track equipment degradation trends over time
- Plan maintenance activities based on actual conditions rather than just time intervals
- Document compliance with safety and regulatory requirements
- Build historical data for better failure prediction
- Justify maintenance budgets with quantitative data
Get a Free WorkTrek Demo
Let's show you how WorkTrek can help you optimize your maintenance operation.
Try for free