What is Planned Shutdown?
A planned shutdown, outage, or downtime is a deliberately scheduled period during which a facility, production line, or equipment is removed for comprehensive maintenance, repairs, upgrades, or modifications.
The maintenance team’s project management process carefully orchestrates this strategic pause in operations to minimize disruption while maximizing the efficiency of maintenance activities.
During a planned shutdown, maintenance teams can safely access and work on equipment that would be dangerous or impossible to maintain during normal operations. It also helps to publish the maintenance schedules for the rest of the organization.
This includes replacing worn components, conducting thorough inspections, performing calibrations, and implementing system upgrades.
Successful shutdowns consider the following:
- Safety considerations
- Unplanned downtime
- Necessary Resources
- Spare parts availability
- Well-communicated planned downtime
- Clearly define time frame
Think of it as similar to scheduling your car for extensive service – rather than just quick repairs while running errands, and you set aside dedicated time for thorough maintenance.
How to schedule planned shutdown?
The planning phase for these shutdowns typically begins months in advance and should consider all operational demands. It involves creating detailed schedules, securing necessary parts and materials, coordinating multiple contractors and maintenance teams, defining the shutdown scope, and establishing clear safety protocols.
Maintenance planners must carefully balance the cost of lost production time against the benefits of preventive maintenance and system improvements.
Key aspects of planned shutdowns include:
The scope definition phase
This is where teams identify all tasks that must be completed during the shutdown period. This might range from routine maintenance like cleaning and lubrication to major equipment replacement or facility upgrades projects.
Resource Allocation
Resource allocation involves determining the personnel, tools, parts, and materials needed for each task. This includes scheduling internal maintenance staff and specialized contractors who may be required for specific jobs.
Risk Assessment
Risk assessment and safety planning to ensure all work can be completed without endangering personnel or equipment. This includes creating detailed lockout-tagout procedures, confined space entry permits, and other safety documentation.
Critical Path Scheduling
Critical path scheduling to determine the optimal sequence of work activities. Some tasks must be completed in a specific order, while others can be performed simultaneously to reduce the overall shutdown duration.
A well-executed planned shutdown can significantly improve equipment reliability, reduce emergency repairs, and extend the operational life of facility assets.
However, poor planning or execution can result in extended downtime, cost overruns, and potential safety incidents.
Thus, shutdown planning and management are among the most critical responsibilities in maintenance organizations.
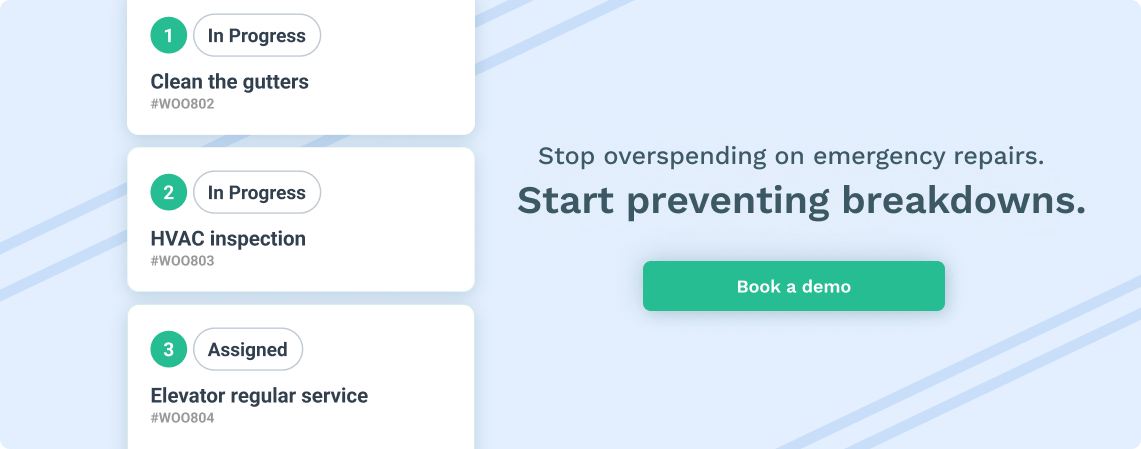
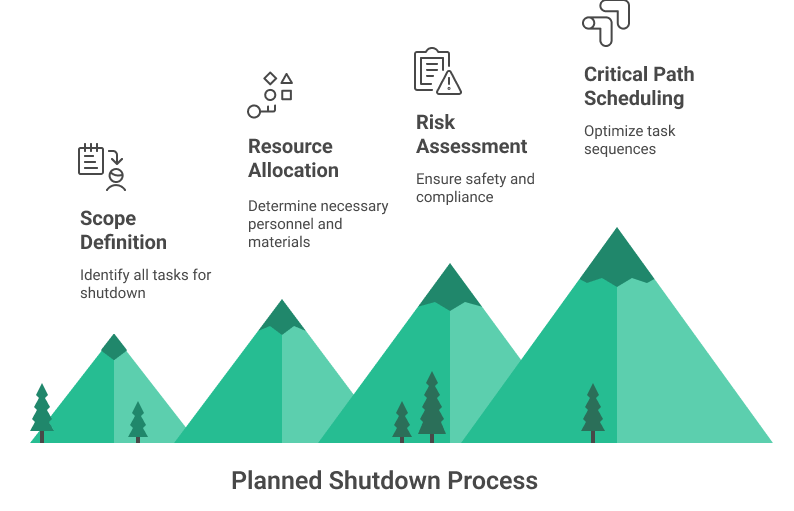
Purpose of Planned Shutdown
In maintenance organizations, planned shutdowns serve multiple critical purposes.
The primary objective is to perform extensive maintenance activities that cannot be executed while equipment runs, such as internal inspections, major repairs, or system-wide upgrades.
These shutdowns are scheduled to minimize production impact and optimize resource utilization.
It is important to understand the key differences between planned and unplanned shutdowns. Planned shutdowns are scheduled in advance to ensure minimal disruption, whereas unplanned shutdowns occur unexpectedly and can lead to significant financial losses and operational disruptions.
Industry Examples of Shutdown Maintenance
Oil Refineries and Production
In oil refineries, planned shutdowns (often called “turnarounds”) are massive undertakings that typically occur every 3-5 years. For instance, the Shell Deer Park refinery in Texas conducts major turnarounds that can last 30-45 days.
During this time, entire process units are systematically shut down, cleaned, inspected, and repaired. Workers might replace massive heat exchangers, rebuild distillation columns, or upgrade control systems.
These shutdowns often involve thousands of workers and can cost hundreds of millions of dollars, but they’re essential for maintaining safe and efficient operations.
Power Plants
Power plants provide another fascinating example. Consider nuclear power plants, which undergo planned shutdowns called “refueling outages” approximately every 18-24 months.
During these periods, which typically last 20-30 days, the reactor is powered down, and about one-third of the fuel assemblies are replaced. At the same time, maintenance teams perform thousands of other tasks that can’t be done while the reactor is running.
For example, the Tennessee Valley Authority’s Browns Ferry Nuclear Plant uses these outages to inspect reactor vessels, upgrade safety systems, and maintain emergency generators.
Automotive
In the automotive industry, manufacturers often schedule annual shutdown periods. Toyota’s manufacturing plants traditionally conduct their major planned shutdowns during summer.
During these periods, which might last two weeks, they perform comprehensive maintenance on assembly line robots, replace worn conveyor systems, and upgrade manufacturing equipment.
They might also use this time to reconfigure production lines for new vehicle models.
Food and Beverage
Food and beverage processing plants offer yet another perspective. Consider a large brewery like Anheuser-Busch’s facility in St. Louis.
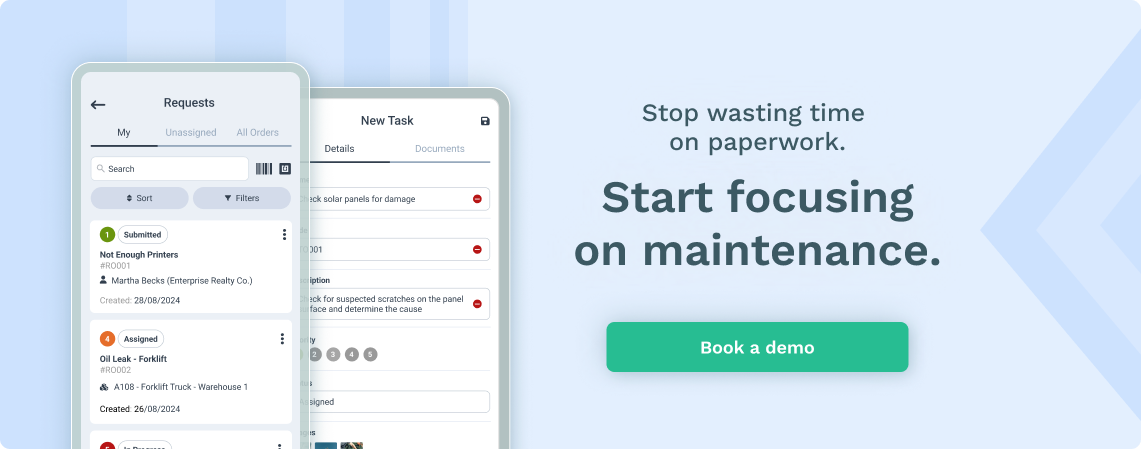
They schedule planned shutdowns during slower seasons to thoroughly clean and maintain their brewing vessels, bottling lines, and packaging equipment. These shutdowns are crucial for maintaining product quality and meeting strict food safety requirements.
During a typical week-long shutdown, teams might replace worn pump seals, calibrate filling machines, and thoroughly sanitize all product contact surfaces.
Amusement and Theme Parks
Theme parks also conduct planned shutdowns, though they often do them ride-by-ride rather than closing the entire park.
Disney World, for instance, regularly schedules “refurbishment periods” for its attractions. During these periods, which can last anywhere from a few weeks to several months, they perform mechanical maintenance, refresh themed elements, and update technology.
The “It’s a Small World” ride at Disney parks typically undergoes an annual shutdown for several weeks to maintain its complex audio-animatronic systems and repair or replace worn boat components.
Mining
Mining operations provide a particularly intensive example of planned shutdowns. The Chuquicamata copper mine in Chile, one of the world’s largest open pit mines, conducts major shutdowns of its processing facilities every few years.
During these periods, which can last up to a month, they replace giant crusher liners, rebuild conveyor systems, and maintain the massive mills that grind the ore. These shutdowns require precise coordination of hundreds of workers and heavy equipment in challenging conditions.
Get a Free WorkTrek Demo
Let's show you how WorkTrek can help you optimize your maintenance operation.
Try for free