What is Smart Maintenance?
Smart maintenance represents a sophisticated evolution in industrial and facility maintenance practices that combines traditional preventive maintenance with advanced digital technologies, data analytics, and artificial intelligence.
This approach transforms reactive “fix-it-when-it-breaks” methods into predictive and prescriptive maintenance strategies to enhance equipment effectiveness.
At its core, lean smart maintenance employs Internet of Things (IoT) sensors and remote monitoring of conditions like temperature, vibration, pressure, and performance metrics.
These sensors feed data into advanced analytics systems that use machine learning algorithms to detect patterns, predict potential failures, and optimize maintenance schedules, thereby improving equipment effectiveness.
Smart maintenance is designed to establish baseline performance parameters for equipment and then track deviations that might indicate developing problems.
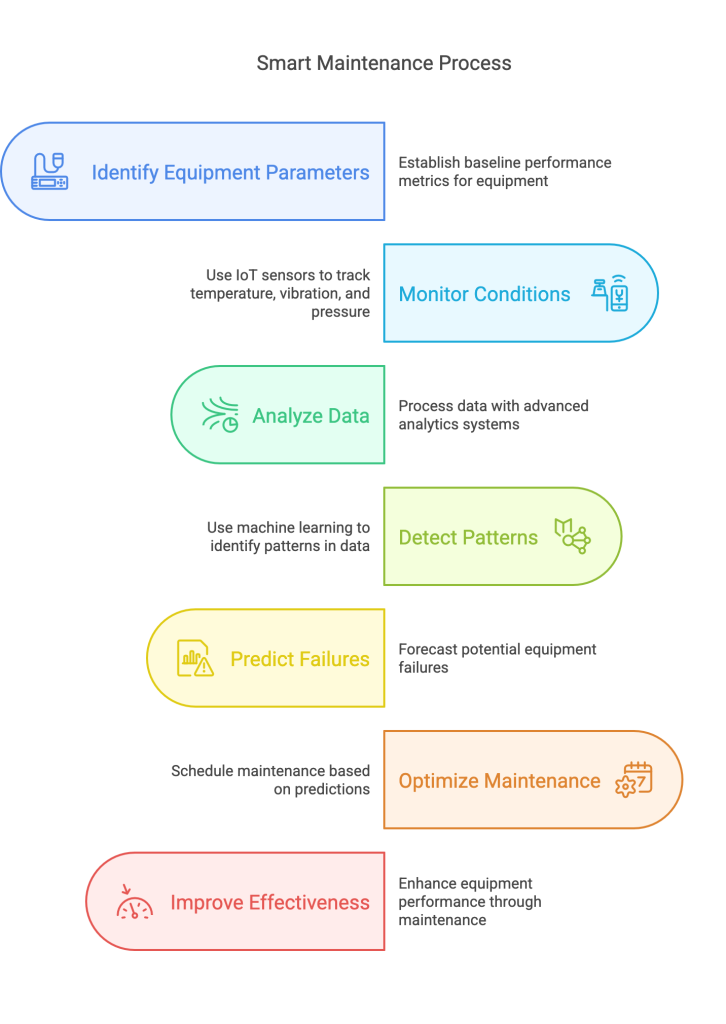
Source: WorkTrek.com
How does it work?
As a proactive maintenance approach, smart maintenance leverages data collected by IoT sensors to optimize maintenance processes and help predict equipment failures.
Smart maintenance aims to maximize uptime and reduce costs by continuously monitoring equipment conditions and analyzing vast maintenance data.
This approach goes beyond traditional preventive maintenance. It uses advanced analytics to predict and prevent equipment failures before they occur, which can help reduce overall maintenance costs.
Benefits of Smart Maintenance
The benefits of smart maintenance are numerous. It enhances efficiency and reduces costs by ensuring maintenance activities are performed only when necessary.
Predictive Maintenance
Predictive maintenance capabilities allow for early detection and troubleshooting of potential issues. This can significantly reduce unplanned downtime, eliminate the need for emergency maintenance and parts orders, and give maintenance technicians better visibility of potential issues.
Improved Inventory Management
Improved inventory management is another key advantage, as smart maintenance systems enable just-in-time ordering and provide easier access to spare parts, ensuring more accurate inventory management.
Data-Driven Insights
Smart maintenance transforms maintenance operations and improves manufacturing processes by using a streamlined, data-driven process that enhances equipment reliability and operational efficiency.
Smart Maintenance Examples
Companies are using smart maintenance to revolutionize how they maintain their equipment and infrastructure.
Here are several concrete examples of how organizations are implementing these technologies:
Manufacturing Sector
Siemens uses IoT sensors and AI algorithms in its gas turbine manufacturing facilities. Its system continuously monitors turbine vibration patterns, temperature fluctuations, and acoustic signatures. This remote monitoring has reduced unplanned downtime by approximately 30% and extended the service life of critical components by predicting potential failures weeks before they occur.
Toyota implemented a smart maintenance system in its production lines. The system uses machine learning to analyze data from thousands of points in its assembly robots. The system can detect subtle changes in motor current draw, often indicating bearing wear before physical symptoms appear.
This approach has reduced maintenance tasks and costs by 20% while improving production reliability.
Energy and Utilities
Duke Energy deployed smart sensors across its electrical grid infrastructure. These sensors collect real-time data on transformer temperatures, load conditions, and oil chemistry. Their AI system analyzes this data to predict potential failures and automatically schedules maintenance during optimal time windows. This has benefited both the company and maintenance managers since it has reduced power outages by 15% and extended the life of expensive transformers.
Chevron uses drone technology and computer vision algorithms to inspect offshore oil platforms. These drones capture thermal imagery and visual data from hard-to-reach areas, identifying potential structural weaknesses or oil leaks. Their system has reduced inspection costs by 50% while increasing the frequency and thoroughness of inspections.
Transportation
Deutsche Bahn (German Railways) uses smart sensors on its high-speed trains to monitor wheel performance, brake systems, and track conditions. Its predictive algorithms can detect when a component is beginning to fail and automatically flag the train for maintenance at the next service opportunity. This approach has reduced in-service breakdowns by 25%.
Delta Airlines implements smart maintenance systems for its aircraft fleet using engine sensors that continuously transmit performance data. The system analyzes over 5,000 parameters from each engine, predicting maintenance needs up to two months in advance. This has improved flight safety and overall equipment effectiveness while reducing maintenance costs by millions annually.
Building Management
Microsoft has implemented smart building managementsystems across its corporate campuses. These systems use sensors to monitor HVAC equipment, elevator systems, and lighting infrastructure. By predicting maintenance needs before failure, they’ve reduced energy consumption by 20% while improving occupant comfort through more reliable building systems.
Main Features of Smart Maintenance
Companies can optimize maintenance operations through smart maintenance by implementing several key strategies:
Condition Monitoring
Condition monitoring enables organizations to track equipment health in real time using IoT sensors that measure critical parameters such as vibration, temperature, pressure, and electrical current. These sensors continuously collect data as early indicators of potential failures, allowing maintenance teams to address issues before they lead to breakdowns.
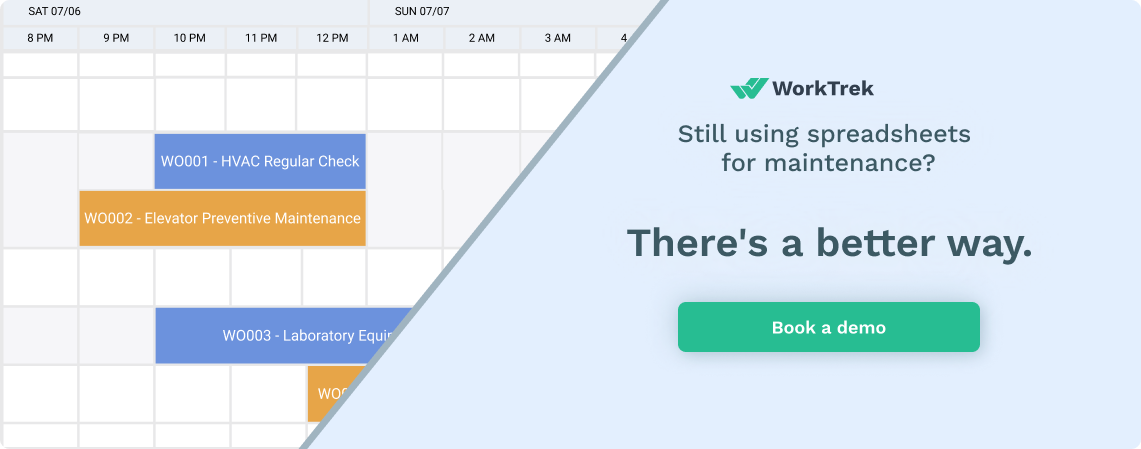
Predictive Analytics
Predictive analytics algorithms process historical and real-time data to forecast when equipment will likely fail. These models identify patterns and anomalies humans might miss, extending asset lifecycles and preventing unexpected downtime by scheduling interventions at optimal times.
Digital Twins
Digital twins create virtual replicas of physical assets that simulate performance under various conditions. Maintenance teams can test different maintenance scenarios virtually before implementing them in the real world, reducing risk and optimizing resource allocation.
Mobile Maintenance
Mobile maintenance management equips technicians with digital tools that provide equipment histories, repair procedures, and real-time guidance while in the field. These solutions improve first-time fix rates and reduce repair times by ensuring technicians have all the necessary information.
Augmented Reality
Augmented reality delivers visual maintenance instructions through wearable devices, which is particularly valuable for complex equipment where technicians need precise guidance. This technology reduces errors and accelerates training by overlaying digital information onto physical assets.
Asset Performance
Asset performance management systems integrate maintenance data with operational and financial metrics to evaluate the effectiveness of maintenance strategies. These platforms help organizations balance maintenance costs against production requirements and equipment reliability goals.
By implementing these smart maintenance approaches, companies typically experience 20-30% reductions in maintenance costs, 30-50% decreases in equipment downtime, and 20-40% extensions in asset lifespan while improving overall operational efficiency, safety, and product quality.
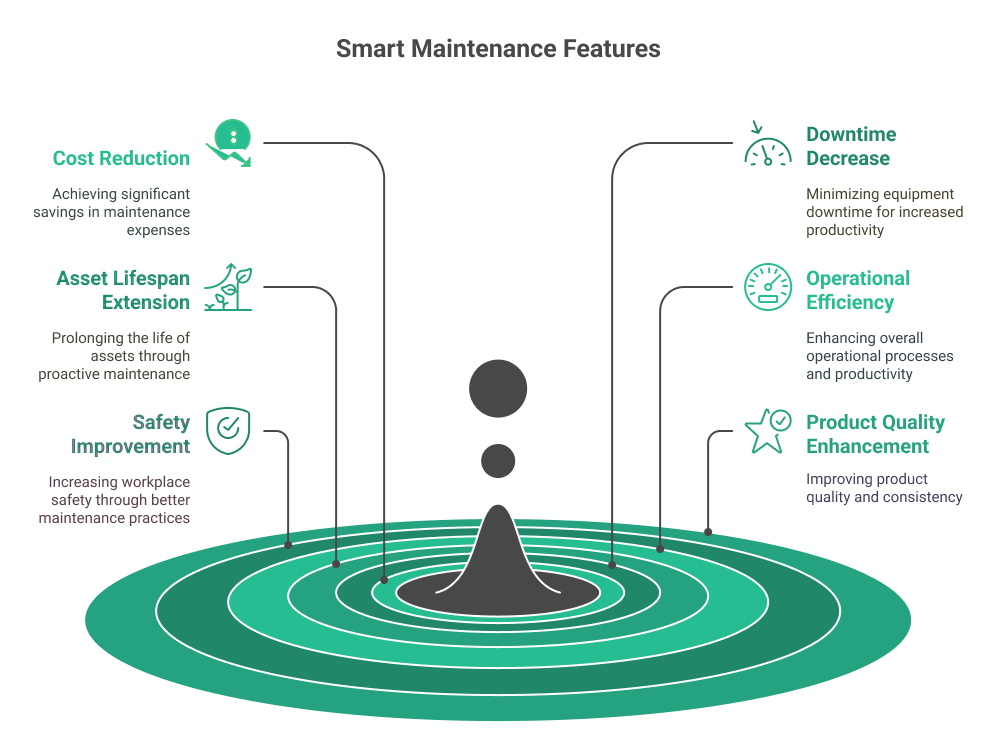
Technologies used for Smart maintenance
Data Collection Technologies
Technologies that gather data about equipment conditions and performance are at the foundation of any smart maintenance system.
This includes Internet of Things (IoT) sensors that measure various parameters such as vibration, temperature, pressure, sound, and electrical current.
More sophisticated systems might employ computer vision systems with high-speed cameras to detect visual anomalies or acoustic sensors that can identify unusual equipment sounds that might indicate developing problems.
Data Transmission Infrastructure
The collected data needs reliable pathways to reach processing systems. This typically involves industrial communication protocols running over wired and wireless networks like OPC UA (Open Platform Communications Unified Architecture) or MQTT (Message Queuing Telemetry Transport).
Modern facilities often implement 5G private networks to handle the high bandwidth and low latency requirements of real-time monitoring.
Data Storage and Processing Systems
The vast amount of sensor data requires robust storage solutions, typically implemented through edge computing devices and cloud infrastructure.
Edge computing devices process time-sensitive data near the source, while cloud systems handle longer-term storage and more complex analytics. Industrial historians store time-series data with high fidelity, allowing detailed equipment performance analysis.
Analytics and Intelligence Platforms
Smart maintenance comes from sophisticated analytics platforms that process the collected data.
These smart-systems employ machine learning algorithms to detect patterns and anomalies, often using techniques like neural networks for complex pattern recognition or random forests for prediction tasks. Digital twin technology creates virtual replicas of physical assets, allowing for simulation and testing of different maintenance scenarios.
Maintenance Management Software
Computerized Maintenance Management Systems (CMMS) like WorTrek are the backbone for successful smart maintenance strategies.
By creating a centralized digital repository of equipment data, maintenance histories, and asset information, CMMS provides the foundation necessary for more advanced predictive capabilities.
Computerized maintenance management systems can help reduce reactive maintenance and quickly develop a preventive maintenance plan. For instance, when certain values exceed predetermined thresholds, the system can automatically generate work orders, shifting maintenance from calendar-based to condition-based activities.
CMMS platforms are the perfect system to store all historical maintenance data. The historical data accumulated within a CMMS becomes invaluable for predictive analytics. Maintenance records provide the training data for machine learning algorithms to identify patterns preceding equipment failures.
Mobile and Wearable Technologies
Field technicians need tools to access and interact with the smart maintenance system.
This includes ruggedized tablets or smartphones running maintenance apps, augmented reality headsets that can overlay repair instructions onto physical equipment, and smart watches or other wearables that can receive alerts and track maintenance activities.
Integration and Middleware
All these technologies need to work together seamlessly to function effectively. This requires integration platforms and middleware to handle different data formats, protocols, and systems. API management platforms ensure secure and efficient communication between various components of the smart maintenance ecosystem.
Security Technologies
Given the critical nature of maintenance operations, robust cybersecurity technologies are essential. This includes network security solutions, encryption for data in transit and at rest, identity and access management systems, and security information and event management (SIEM) platforms that can detect and respond to potential security threats.
Predictive Maintenance and Reliability Analytics Tools
Specific reliability engineering tools help analyze equipment failure patterns and optimize maintenance strategies to complete the picture.
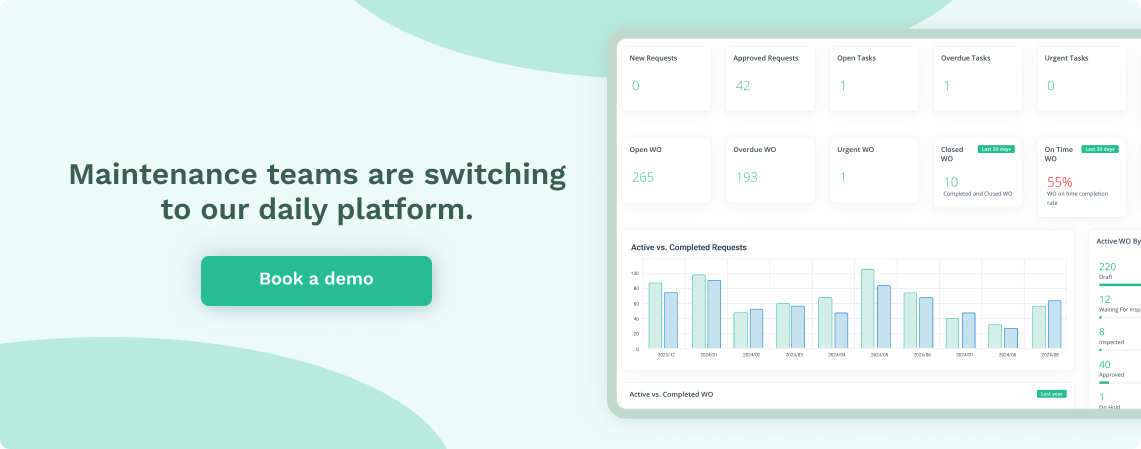
These might include reliability-centered maintenance (RCM) software that helps determine the most appropriate maintenance approach for each piece of equipment or root cause analysis tools that help identify and address the underlying causes of equipment failures.
Best Practices for Implementing Smart Maintenance
Implementing smart maintenance requires a thoughtful, strategic approach that balances technological innovation with organizational readiness. Here are the key best practices that successful organizations follow when transitioning to smart maintenance:
Start with a Clear Business Case
Begin by identifying specific maintenance challenges and quantifying their business impact. Calculate potential ROI from improvements in equipment uptime, extended asset life, reduced emergency repairs, and optimized maintenance schedules. This business case should articulate clear, measurable objectives that align with broader organizational goals and provide a foundation for measuring success.
Prioritize Critical Assets First
Rather than attempting a complete overhaul of all maintenance systems at once, identify your most critical assets—those with the highest failure consequences, greatest maintenance costs, or most significant impact on operations. This focused approach allows organizations to demonstrate value quickly and build expertise before scaling to less critical systems.
Invest in the Right Technology Infrastructure
Smart maintenance depends on a robust technological foundation. This includes reliable sensors to capture meaningful data, secure network connectivity to transmit information, sufficient data storage capacity, and powerful analytics platforms. When selecting technologies, prioritize interoperability with existing systems and scalability to accommodate future growth.
Develop a Data Strategy
Data powers smart maintenance, so organizations need a comprehensive data collection, storage, analysis, and governance strategy. Define what data you need, how frequently to collect it using maintenance software, where to store it, how long to retain it, and who should have access to it. Establish data quality standards and cleaning processes to ensure the insights derived are reliable.
Build Cross-Functional Teams
Smart maintenance bridges traditional divides between maintenance, operations, IT, and business leadership. Form cross-functional teams combining maintenance expertise, data science knowledge, and IT capabilities. This collaboration ensures maintenance remains the focus while appropriately leveraging technological capabilities.
Implement Change Management Programs
The shift to smart maintenance represents a significant cultural change for many maintenance teams accustomed to reactive approaches. Develop comprehensive change management programs and standard operating procedures (SOP) that explain the benefits of the new approach, provide adequate training, establish clear roles and responsibilities, and recognize early adopters who embrace the latest methods.
Start with Pilot Projects
Begin with small-scale pilot projects that can demonstrate value quickly with minimal risk. These pilots provide learning opportunities to refine approaches before wider implementation and provide tangible examples of success in building organizational support. Carefully document lessons learned from these pilots to inform larger rollouts.
Integrate with Enterprise Systems
Smart maintenance and smart factories should not operate in isolation. Integrate your maintenance systems with enterprise resource planning (ERP), manufacturing execution systems (MES), and asset management platforms to create a unified view of operations and improve organizational decision-making.
Establish New Performance Metrics
Traditional maintenance metrics like the mean time between failures (MTBF) or maintenance costs remain important, but smart maintenance enables new key performance indicators. Develop metrics around predictive accuracy, asset health indices, and maintenance avoidance to evaluate the effectiveness of your smart maintenance program properly.
Continuously Evolve Capabilities
Smart maintenance is not a one-time implementation but an ongoing journey of improvement. Continuously refine predictive models with new data, upgrade sensors and analytics capabilities as technology evolves, and regularly reassess your approach against industry best practices and emerging maintenance methodologies.
By following these best practices, organizations can transform their maintenance operations from reactive cost centers into strategic contributors to operational excellence and business performance.
Get a Free WorkTrek Demo
Let's show you how WorkTrek can help you optimize your maintenance operation.
Try for free