What is Storeroom Management?
Storeroom management is a key aspect of operations and inventory control that involves organizing, maintaining, and optimizing storage spaces for materials, supplies, and equipment.
At its core, maintenance storeroom management ensures that everything needed for operations is available when required while minimizing waste and controlling costs.
Think of it as similar to managing a well-organized kitchen pantry but on a much larger and more complex scale.
Introduction to Storeroom Management
If you are running a maintenance team, you know the importance of effective storeroom management.
By managing a well-organized storeroom ensures that maintenance personnel have access to the right tools and parts in the correct quantity, exactly when and where they need them.
This can, in turn, lead to increased productivity, reduced downtime, and lower costs.
Imagine a scenario where a critical piece of machinery breaks down, and the maintenance team can quickly locate the necessary spare parts without any delay. This can optimize your organization’s scheduled maintenance procedures and improve material management.
At its core, storeroom management involves several key concepts and best practices. These include maintaining accurate inventory records, implementing efficient organizational systems, and establishing clear procedures for receiving, storing, and distributing items.
Components of Effective Storeroom Management
Space Optimization
Imagine walking into a storeroom—every square foot matters. Good storeroom management involves arranging items to maximize vertical and horizontal space while ensuring easy access. An optimized storeroom can reduce the occurrence of lost or missing parts.
Storeroom managers can achieve this by installing appropriate shelving systems, using bin locations, and creating clear aisles for movement.
For example, frequently accessed items would be placed at easily reachable heights for storeroom workers, while seasonal or rarely used items might go to higher locations.
Inventory Control
This is like having a detailed map of everything in the storeroom. It involves tracking what comes in, what goes out, and what remains, making items easy for storeroom personnel to find.
MRO storeroom management often uses inventory management systems that automatically track stock levels, generate alerts when supplies run low, and help predict future needs based on usage patterns.
Organization Systems
Think about how a library organizes books – storeroom management uses similar principles. Items are typically categorized and labeled using systems like:
- Numerical coding
- Barcode labeling
- Color-coding
- Zone designation
This systematic organization helps workers quickly locate items and maintain accurate inventory counts.
Safety and Security of Maintenance Storeroom
A well-managed storeroom isn’t just organized – it’s safe. This includes:
- Proper storage of hazardous materials
- Adequate ventilation
- Fire safety equipment
- Access control systems
- Proper lighting
- Ergonomic considerations for material handling
Quality Control of Spare Parts
This involves maintaining the condition of stored items. For instance, certain materials might need climate control to prevent deterioration, while others might have specific shelf-life requirements that need monitoring.
The impact of effective storeroom management extends throughout an organization. When done well, it:
- Reduces time spent searching for items
- Minimizes inventory holding costs
- Prevents stockouts
- Reduces waste from expired or damaged materials
- Improves workplace safety
- Increases operational efficiency
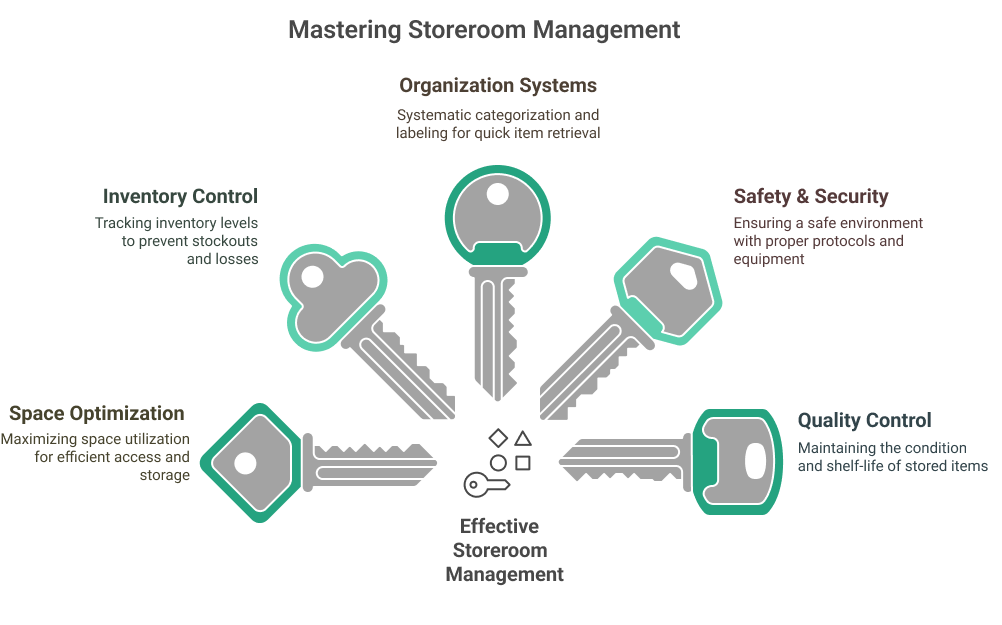
Improve and Optimize Storeroom
Setting up an easy-to-manage storeroom. Think of this like designing a small city—it needs careful planning, clear navigation, and systems that work together seamlessly. Don’t forget also to implement a culture of continuous improvement.
Plan your Storeroom
First, let’s consider the foundational planning phase. Before moving any items into the space, you’ll want to analyze your specific needs and traffic patterns. Consider what items you’ll store, if you have multiple locations, how frequently they’re accessed, and who needs to access them. This information becomes the blueprint for your storeroom layout.
Define Floorplan
Start with the floor plan for your storage area for the physical setup. The most efficient storerooms follow a “flow-through” design principle. Imagine a river flowing through your storeroom—items should move smoothly from receiving to storage to dispatch.
Also, consider the location of the production floor and easy access to the storeroom.
Create wide main aisles for key areas (think of them as main streets) at least 8-12 feet wide to accommodate equipment like forklifts and secondary aisles (like neighborhood streets) that are 4-6 feet wide for foot traffic.
Find the Right Storage System
Storage systems are crucial for maximizing space utilization. Install adjustable shelving units that can be modified as your needs change and require more storage space.
Storage height zones should be planned thoughtfully. The “golden zone” – between waist and shoulder height – should house your most frequently accessed items. This reduces strain and increases efficiency.
Unnecessary parts and items accessed less frequently can be stored higher or lower, but heavier items should always be stored at lower levels for safety reasons.
Define Organizational System
Now, let’s discuss organizational systems. Implement a clear, logical categorization system. Think of it like organizing a library—you want anyone to be able to find what they need quickly.
A common approach is to divide the storeroom into zones, each dedicated to specific categories of items. Within these zones, use a consistent labeling system that includes:
- Zone identifier (e.g., A, B, C)
- Aisle number
- Shelf level
- Position on shelf
For example, location “A-3-2-4” would mean Zone A, Aisle 3, Level 2, and Position 4.
Improve Visibility
Visibility is essential for easy management. Install proper lighting throughout the storeroom, particularly when detailed work occurs, like checking labels or paperwork. Use clear signage with large, easily readable text and consider color-coding different zones or categories of items.
Implement 5S
To maintain organization, establish a “5S” system, which comes from Japanese manufacturing principles:
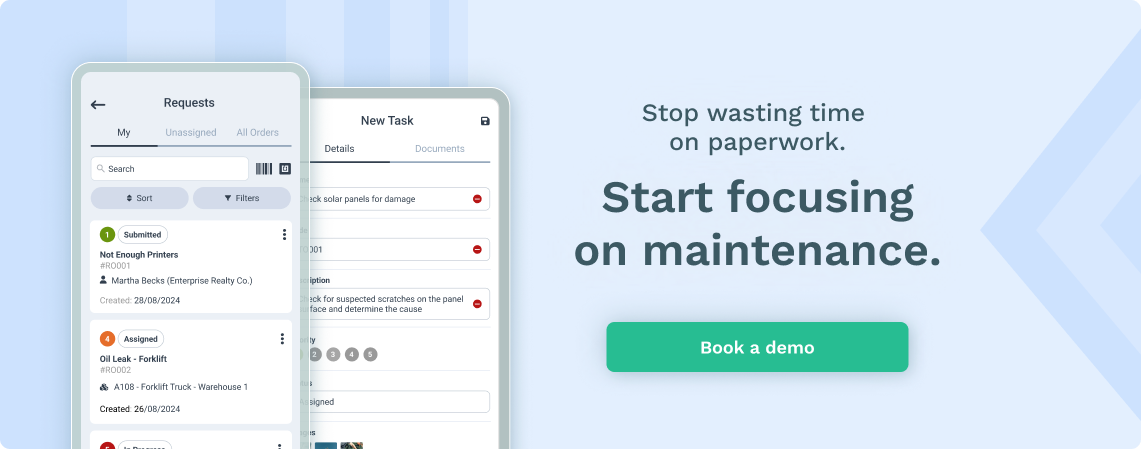
- Sort – Keep only what’s needed
- Set in Order – Arrange items for easy access
- Shine – Keep the area clean
- Standardize – Create consistent procedures
- Sustain – Maintain these practices
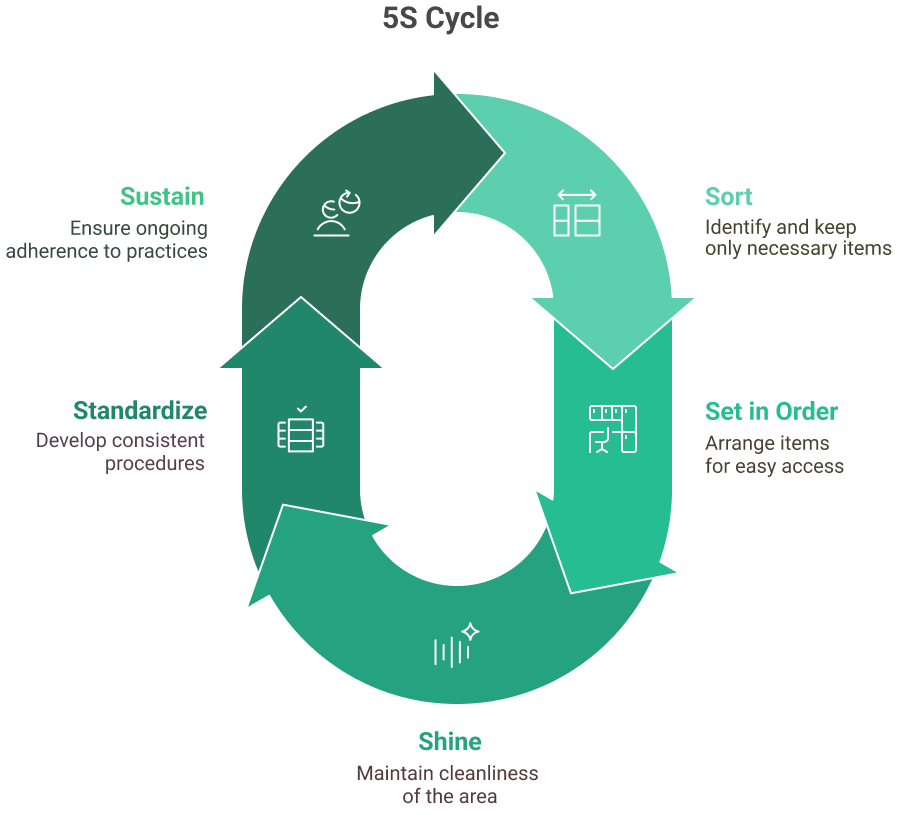
Source: WorkTrek.com
Implement Barcode System
Consider implementing a barcode system connected to inventory management software for inventory tracking. This approach can make it easier to:
- Track item locations
- Monitor stock levels
- Generate automatic reorder points
- Track usage patterns
- Conduct inventory counts
Remember to plan for future growth and changes. Leave some flexibility in your setup – perhaps 15-20% extra space – to accommodate new items or changing needs.
Think of this as leaving room for expansion in a growing city.
CMMS to the Rescue
A Computerized Maintenance Management System (CMMS) like WorkTrek can transform storeroom management by creating a digital nervous system that connects all maintenance operations and inventory control aspects.
How does it work, and why is it so powerful?
Think of a CMMS as an intelligent assistant constantly monitoring your storeroom, maintenance activities, and equipment health.
It creates connections between these elements that would be impossible to manage manually.
For example, when a maintenance technician completes a repair job, the CMMS automatically updates the inventory levels of the parts used, tracks the labor hours, and maintains a detailed history of that equipment’s maintenance.
Core Benefits of CMMS
The core benefits of CMMS for storeroom management come from its ability to automate and integrate several critical processes:
Automated Inventory Tracking
When parts arrive at your facility, the CMMS records their receipt, automatically updating inventory levels. As these parts are used in maintenance work, the system continues tracking them, maintaining real-time inventory counts.
This prevents the common problem of discovering you’re out of a critical part when you urgently need it.
Predictive Inventory Management
The CMMS learns from historical data to predict when you’ll need particular parts and quickly find obsolete parts. For instance, if you typically use 10 air filters every month, the system can automatically generate purchase orders when the stock drops below a certain level.
This predictive capability becomes even more sophisticated when combined with equipment maintenance schedules – the system knows that certain parts will be needed for upcoming preventive maintenance tasks and can ensure they’re in stock.
Work Order Integration
Perhaps one of the most powerful features is how CMMS connects work orders with inventory systems and management. When a technician creates a work order, the system can immediately check if all required parts are available.
It can automatically generate purchase requisitions to acquire the right quantity if parts are missing. This integration prevents delays in maintenance work, helps maintain optimal inventory levels, and improves storeroom performance.
Cost Tracking and Analysis
The CMMS maintains detailed records of every transaction, allowing you to analyze spending patterns and identify opportunities for cost reduction.
For example, you might discover that you’re keeping too much stock of slow-moving items or that certain parts are failing more frequently than expected, indicating a potential quality issue.
Document Management
Modern CMMS systems like WorkTrek can store and manage important documents related to parts and equipment, such as:
- Manufacturer specifications
- Safety data sheets
- Warranty information
- Installation guides
- Vendor contracts
- Supplier databases
This digital documentation is instantly accessible when needed, eliminating time spent searching paper files.
Location Tracking
Advanced CMMS systems can track not just what you have but where everything is located. This is particularly valuable in large facilities with multiple storerooms or storage locations.
Technicians can quickly find the exact location of needed parts, reducing searching time and improving maintenance efficiency.
Vendor Management
The system can maintain approved vendors’ records, performance history, pricing, and delivery times. This information helps in making informed purchasing decisions and managing supplier relationships effectively.
Reporting and Analytics
A CMMS provides deep insights into your storeroom operations through detailed reports and analytics. You can track key performance indicators such as:
- Inventory turnover rates
- Stock-out frequencies
- Order fulfillment times
- Carrying costs
- Usage patterns by department or equipment type
These insights help in making data-driven decisions about storeroom management strategies.
How to set effective Storeroom Management in a CMMS
How can you use a CMMS system to set up inventory tracking?
Think of this process as building a digital twin of your physical storeroom—the system must accurately represent every item, location, and movement.
Starting with Part Master Data
The foundation of good inventory tracking begins with creating comprehensive part records. In WorkTrek, each part record should include:
Critical Information Fields:
First, you’ll need to enter the basic identifying information for each part:
- Part number (your internal number)
- Manufacturer part number
- Description (both short and detailed)
- Unit of measure
- Category/classification
- Storage location(s)
- Cost information (including both standard and last purchase costs)
Create Inventory Control Parameters
The next step is to set the inventory control parameters:
- Minimum stock level (reorder point)
- Maximum stock level
- Economic order quantity
- Lead time for ordering
- Critical spare designation (if applicable)
Storage Location Setup
In WorkTrek, or any other CMMS system, you’ll want to create a hierarchical location structure that mirrors your physical storeroom. For example:
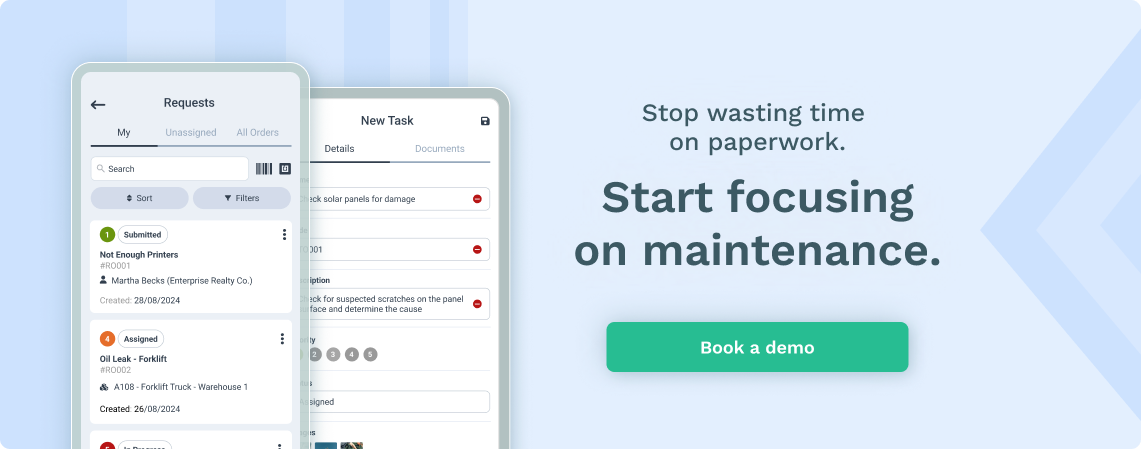
Building > Storeroom > Zone > Aisle > Shelf > Bin
This detailed location tracking helps with the following:
- Physical inventory counts
- Part picking efficiency
- Multiple storage location management
- Bin location optimization
Setting Up Inventory Transactions
Configure the transaction types in WorkTrek to track every movement:
- Receipts (purchases, returns from jobs)
- Issues (to work orders, departments)
- Transfers (between locations)
- Adjustments (after cycle counts)
- Returns (to vendors)
Each transaction type should require the following:
- Date and time
- Person performing transaction
- Quantity
- Reference document (PO, work order, etc.)
- Cost (where applicable)
- Notes/comments field
Establishing Reorder Points
CMMS allows you to set up automated reorder notifications. To configure these effectively:
1. Analyze historical usage data (if available) to determine:
- Average daily/weekly/monthly usage
- Maximum usage periods
- Seasonal variations
2. Calculate safety stock levels considering:
- Lead time from suppliers
- Criticality of the part
- Cost of stockouts vs. carrying cost
3. Set up automatic reorder notifications based on:
- Minimum stock levels
- Economic order quantities
- Lead times
Cycle Counting Setup
Configure your cycle counting program in WorkTrek:
1. Establish count frequencies based on:
- ABC classification (A items counted more frequently)
- Part value
- Critical spare designation
- Usage frequency
2. Set up count schedules:
- Daily counts for high-value/critical items
- Weekly counts for medium-value items
- Monthly or quarterly counts for low-value items
3. Configure count sheets to include:
- Current system quantity
- Last count date
- Last transaction date
- Serial numbers (if applicable)
- Lot numbers (if applicable)
Integration with Work Orders
Connect your inventory tracking with the maintenance workflow:
1. Set up parts reservations for planned work:
- Link parts to asset PM schedules
- Create pick lists for planned work
- Reserve quantities for upcoming jobs
2. Configure automatic inventory updates when:
- Parts are issued to work orders
- Unused parts are returned
- Emergency parts are used
Reporting and Analytics Setup
Finally, configure key reports and dashboards to monitor:
- Stock levels and reorder points
- Inventory accuracy metrics
- Stock-out occurrences
- Slow-moving inventory
- Inventory value
- Usage trends
- Transaction history
Get a Free WorkTrek Demo
Let's show you how WorkTrek can help you optimize your maintenance operation.
Try for free