What is a CMMS?
A Computerized Maintenance Management System (CMMS) is a software solution that manages, tracks and optimizes maintenance operations. CMMS software allows organizations to schedule preventive maintenance, generate work orders, track asset performance, and maintain an inventory of spare parts and materials. It centralizes all maintenance-related data, making managing complex maintenance operations easier, increasing asset reliability, and reducing downtime.
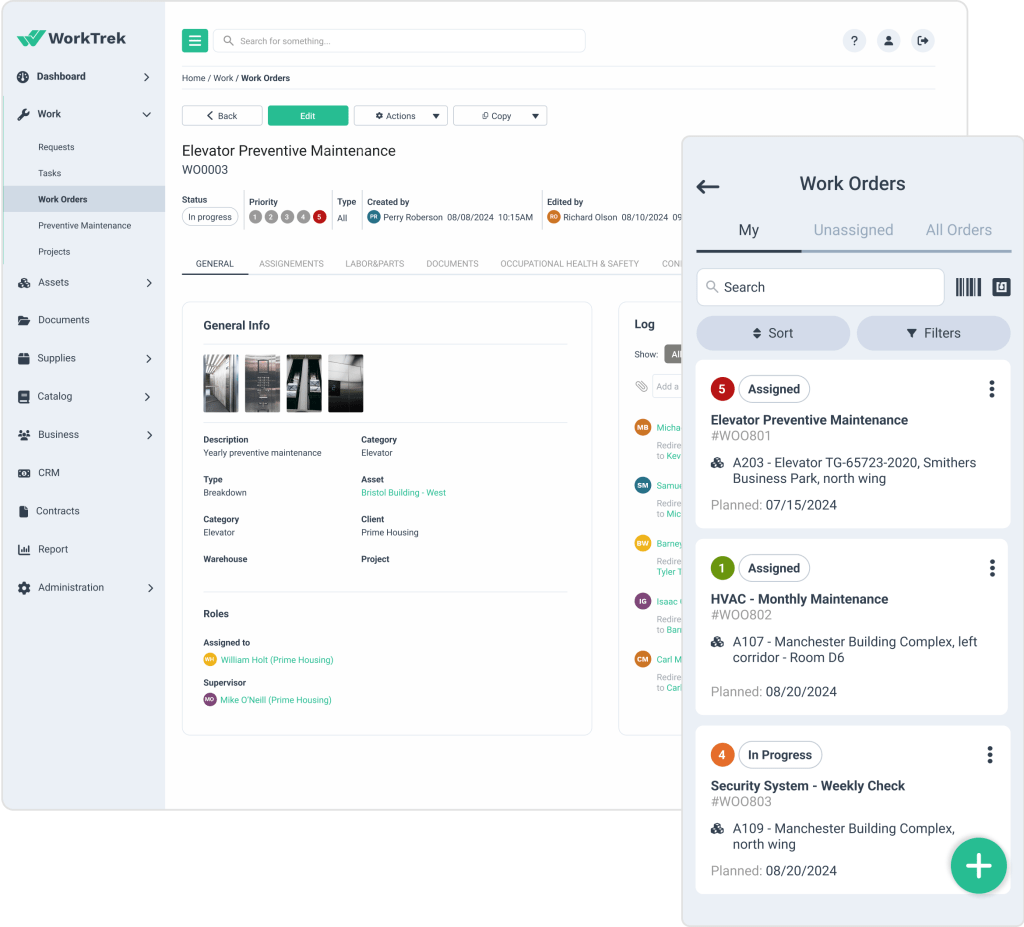
Data and Illustration: WorkTrek
CMMS software helps organizations automate many manual tasks, such as scheduling maintenance activities based on time intervals or usage data. It also provides detailed reporting on maintenance activities, costs, asset performance, and downtime. This data can be used to identify trends, optimize maintenance schedules, and reduce the frequency of equipment failures.
By using a CMMS, organizations can ensure that maintenance is carried out on time, improve compliance with safety and regulatory standards, and extend the lifespan of critical assets. The system also provides visibility into maintenance costs, helping organizations make data-driven resource allocation and budget planning decisions. CMMS is widely used across manufacturing, healthcare, and facilities management to improve operational efficiency.
What exactly is a CMMS?
Think of a CMMS as the central nervous system for maintaining all the equipment and assets in an organization. Just as your brain coordinates different body systems and responds to various signals, a CMMS coordinates maintenance activities and responds to equipment needs.
At its foundation, a CMMS starts with a comprehensive asset registry. This is like creating a detailed family tree of every equipment in your facility. Each asset gets its digital identity card containing vital information such as:
Serial numbers and model specifications Location within the facility Purchase date and cost Warranty information Operating parameters Maintenance history Expected lifespan
The system then helps manage maintenance in three main ways:
Preventive Maintenance
First, it handles preventive maintenance scheduling. Imagine having a smart calendar that knows exactly when each piece of equipment needs attention. The CMMS automatically generates work orders based on various triggers: time intervals (like changing air filters every three months), meter readings (like servicing a machine after 1000 hours of operation), or specific conditions (like when vibration sensors detect unusual patterns).
Reactive Maintenance
Second, it manages reactive maintenance when equipment breaks down. When a problem occurs, workers can quickly report issues through the system. The CMMS then creates a work order, assigns it to the appropriate maintenance staff, tracks the repair progress, and records all actions taken. This is similar to how a hospital’s system manages patient care – from initial complaints to treatment and follow-up.
Parts Management
Third, it serves as a central data hub for maintenance operations. The system continuously collects and analyzes data about:
Parts inventory and usage Labor hours and costs Equipment downtime Maintenance frequency Repair histories Resource allocation
This data helps managers make informed decisions about maintenance strategies. For example, if the system shows that a particular machine requires frequent unexpected repairs, managers might decide to replace it rather than continue costly maintenance.
3rd Party Integration
A modern CMMS often integrates with other systems, too. It might connect with:
Procurement systems to automatically order replacement parts when inventory runs low Building automation systems to receive real-time equipment performance data Mobile devices so technicians can access and update information from anywhere Accounting systems to track maintenance-related expenses
Automation of Maintenance
The practical impact of all this automation and coordination is significant. Consider a manufacturing facility with hundreds of machines. Without a CMMS, maintaining all this equipment would be like trying to conduct an orchestra without a conductor or sheet music – chaos would likely ensue. The CMMS brings order by ensuring nothing falls through the cracks and resources are used efficiently.
Types of Organizations that Benefit from CMMS
Manufacturing facilities are among the most obvious beneficiaries of CMMS. Consider a large automotive plant with thousands of pieces of equipment, from massive assembly line robots to precise testing instruments. For them, CMMS isn’t just helpful—it’s essential for preventing costly production delays. When a single hour of downtime might cost tens of thousands of dollars, having a system that can predict and prevent equipment failures becomes invaluable.
Healthcare Companies
Healthcare institutions also rely heavily on CMMS, though in a different way. Hospitals must maintain critical equipment like MRI machines, ventilators, and surgical tools—equipment where failure isn’t just costly but potentially life-threatening. Their CMMS must ensure perfect compliance with strict regulatory requirements and maintain detailed maintenance records for auditing purposes. Think about how a hospital’s CMMS might track the sterilization history of surgical equipment or monitor the calibration schedule for diagnostic machines.
Schools and Universities
Educational institutions, from small schools to large universities, find CMMS particularly valuable for facility management. They need to maintain everything from HVAC systems and elevators to laboratory equipment and sports facilities. During summer breaks, for instance, their CMMS helps coordinate massive maintenance projects that can’t be done during the school year. It’s like orchestrating a complex renovation project with hundreds of moving parts, all needing to be completed before students return.
Property Managers
Property management companies use CMMS to maintain multiple buildings and handle tenant requests efficiently. Imagine managing a portfolio of 50 commercial buildings—without a CMMS, keeping track of preventive maintenance schedules, tenant complaints, and routine inspections would be nearly impossible. The system helps them transition from reactive maintenance (fixing things when they break) to preventive maintenance (addressing issues before they become problems).
Government Agencies
Municipalities and government facilities benefit enormously from CMMS for managing public infrastructure. Consider a city’s water treatment plant—they must maintain pumps, filters, and monitoring equipment while ensuring compliance with environmental regulations. Their CMMS helps track maintenance history for each component and ensures all maintenance activities are properly documented for regulatory purposes.
Fleet and Transportation
Transportation companies, such as airlines or railway operators, use CMMS to maintain their fleets and infrastructure. An airline’s CMMS, for example, tracks maintenance schedules for each aircraft, ensuring compliance with strict safety regulations while minimizing aircraft downtime. It’s like having a detailed health record for each plane, showing every inspection, repair, and replacement part.
Hospitality
Even smaller organizations can benefit from CMMS if they have significant maintenance needs. A mid-sized hotel, for instance, might use CMMS to manage maintenance of rooms, elevators, kitchen equipment, and swimming pool systems. The system helps them track recurring maintenance tasks and respond quickly to guest complaints about facilities.
Food and Beverage
Food and beverage manufacturers have unique CMMS needs related to food safety compliance. Their systems must track cleaning schedules, equipment sanitization, and maintenance activities while ensuring all work meets strict food safety standards. Think of it as maintaining a detailed diary of every interaction with equipment that touches food products.
History of CMMS Systems
Let me walk you through the fascinating evolution of CMMS systems, which mirrors the broader development of computer technology and industrial maintenance practices.
The roots of CMMS trace back to the 1960s, during the early days of computerization. Before this era, maintenance management was entirely paper-based, with workers using manual logbooks, wall charts, and filing cabinets full of equipment documentation. Imagine maintenance managers trying to coordinate complex industrial operations using nothing but paper cards and clipboards – it was time-consuming and prone to errors.
The first real CMMS systems running on mainframe computers emerged in the late 1960s and early 1970s. These early systems were incredibly basic by today’s standards, essentially serving as digital versions of paper records. They required punch cards for data entry and could only handle simple tasks like recording equipment details and basic maintenance schedules. Think of them as digital filing cabinets – better than paper, but still quite limited.
The 1980s brought a significant transformation with the rise of personal computers. This era saw the first generation of modern CMMS software that could run on individual machines rather than mainframes. These systems introduced more sophisticated features like work order tracking and inventory management. However, they were still standalone applications – each computer had a separate database, making sharing information across an organization challenging.
The 1990s marked a revolutionary period with the advent of client-server architecture and relational databases. This technological leap allowed CMMS systems to become truly collaborative tools. Multiple users could now access and update the same maintenance database simultaneously. It’s similar to how a modern bank allows multiple tellers to access customer accounts at the same time – a huge improvement over having separate, unconnected records.
The internet age of the late 1990s and early 2000s brought web-based CMMS solutions. These systems could be accessed from any computer with an internet connection, dramatically improving flexibility and accessibility. This period also saw the integration of more advanced features like automated scheduling, detailed reporting capabilities, and integration with other business systems.
The mobile revolution of the 2010s transformed CMMS once again. Maintenance technicians could now access and update information directly from their smartphones or tablets while working in the field. Imagine a technician being able to pull up equipment manuals, update work orders, and order replacement parts – all while standing next to the machine they’re repairing.
Future of CMMS Systems
Looking toward the future, we’re seeing the emergence of even more sophisticated capabilities. For instance, some modern CMMS systems are beginning to incorporate digital twins – virtual replicas of physical equipment that can simulate different maintenance scenarios and predict outcomes.
- Internet of Things (IoT) sensors that continuously monitor equipment performance and automatically trigger maintenance requests when needed.
- Artificial Intelligence and Machine Learning algorithms that predict equipment failures before they occur.
- Augmented Reality interfaces that can overlay maintenance information onto physical equipment.
- Cloud computing capabilities that offer unprecedented scalability and accessibility
Advanced analytics tools that help optimize maintenance strategies and resource allocation.
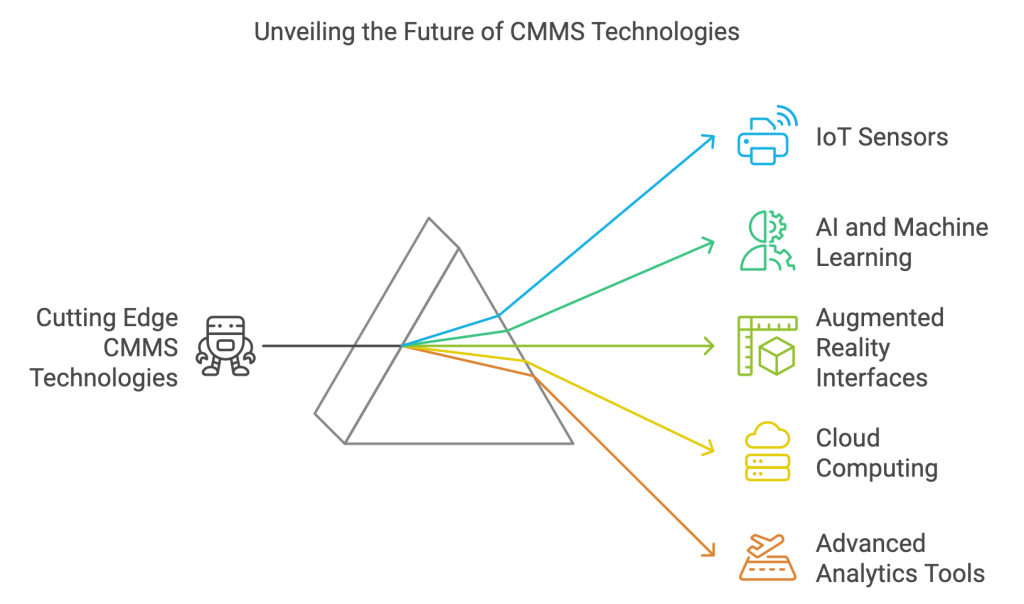
The evolution of CMMS systems reflects a broader trend in maintenance philosophy – from reactive (fix it when it breaks) to preventive (regularly scheduled maintenance) to predictive (fix it just before it breaks) approaches. Each technological advancement has enabled more sophisticated maintenance strategies, increasing efficiency and reliability in industrial operations.
Get a Free WorkTrek Demo
Let's show you how WorkTrek can help you optimize your maintenance operation.
Try for free