Get a Free WorkTrek Demo
Let's show you how WorkTrek can help you optimize your maintenance operation.
Try for freeIf you’re in charge of maintenance at your company, you know how crucial it is to keep everything running smoothly.
Unexpected breakdowns can be a nightmare, causing delays and costing you a ton of money.
That’s why efficient maintenance planning is so important.
Today, we will share five best practices to help you streamline your maintenance planning and keep your operations on track.
Here’s what you need to do.
Having a Designated Maintenance Planner
Imagine having a go-to expert dedicated to making your maintenance activities run smoothly.
That’s precisely what a designated maintenance planner does.
With this key person in place, everyone knows who to turn to with questions, and there’s clear accountability for maintenance outcomes.
A maintenance planner schedules tasks efficiently, reducing downtime and boosting your team’s productivity.
This can save your company a significant amount of money.
Seasoned experts in managing maintenance and reliability agree on that.
Erik Hupjé, founder and Managing Director at Reliability Academy, is one of them. He calls maintenance planners the unsung heroes that save your company money.
Despite this, he further points out that planners are often undervalued and misunderstood in many organizations.
Why is that so?
Hupjé identifies several reasons.
Many organizations mistake planners for administrative personnel. They burden them with tasks like chasing missing parts and processing purchase requisitions.
This administrative perception also overlooks the technical expertise needed. Without it, planners struggle to plan work effectively, which leads to inefficient resource use and increased downtime.
Furthermore, planners are often paid the same as technicians.
Technicians might even earn more due to overtime. This pay discrepancy devalues the planner’s role, making attracting and retaining top talent difficult.
The planner role is also seen as a dead-end administrative job rather than a career advancement step. This discourages technicians from even wanting to become planners.
However, all these problems can be solved with a better understanding of the maintenance planner’s role and the necessary skill set.
Here’s what to look for:
Hands-on experience | Your planner should have experience as a maintenance technician. They’ll understand the equipment and what it takes to keep things running smoothly. Without this expertise, there’s a risk of misdiagnosing issues and applying ineffective maintenance solutions that can lead to frequent breakdowns. |
Strong management skills | Organizational and management skills are essential for planning and coordinating maintenance activities. Without these skills, maintenance tasks can become chaotic, with overlapping responsibilities and missed deadlines. |
Analytical skills | Monitoring maintenance KPIs and using data to fine-tune the maintenance plan is also important. This ensures your maintenance schedule is based on solid information and trends. Without analytical skills, your planner may rely on guesswork, often resulting in inefficient maintenance schedules and overlooked problems. |
Great communication | Good communication skills help your planner coordinate with technicians and other departments. Poor communication, on the other hand, leads to misunderstandings and delays. |
So, the first thing to do for more efficient maintenance planning is to bring a dedicated maintenance planner on board with the skillset we just described.
This person will plan, organize, and oversee all maintenance tasks, help you cut downtime, and save your company valuable time and money.
It’s a smart move that pays off significantly.
Standardizing the Maintenance Process
Standardization is your best friend in maintenance.
When you standardize your processes, everything becomes more predictable and easier to manage.
Imagine each technician in your plant following their maintenance routine.
It’s a recipe for missed steps, inconsistent results, and constant confusion.
But when you implement standardized processes—like using maintenance checklists—you ensure every task is done right, every time.
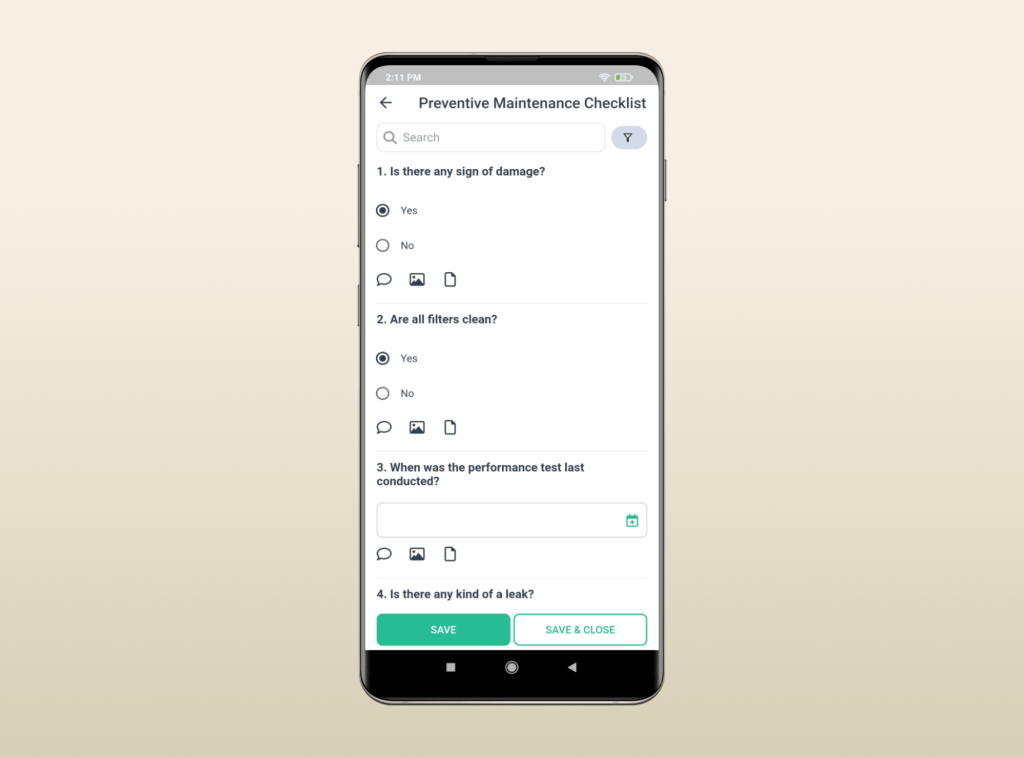
This minimizes errors and reduces unplanned downtime, keeping your operations running smoothly.
To learn more about how you can make such a checklist yourself, look at our article on building the ultimate preventive maintenance checklist.
Standard operating procedures (SOPs) are another excellent tool for standardizing maintenance, as they provide step-by-step guidelines for tasks across your facility.
Whether cleaning machinery in a food processing plant or performing complex repairs, SOPs ensure everyone is on the same page and follows precise procedures.
But remember, keeping SOPs up-to-date is key.
As Jason Jansen, Maintenance Planner at Glencore, wisely advises, regularly reviewing SOPs keeps them effective amid changing maintenance strategies and equipment updates.
Using the exact replacement parts is another way to standardize maintenance. This makes inventory management easier and ensures parts compatibility and reliability.
And let’s not forget technology.
Tools like computerized maintenance management system (CMMS) software are revolutionizing maintenance and helping you standardize processes.
Ardagh Group, a glass and metal packaging company, achieved great success after implementing this technology.
Their success story shows how CMMS can standardize procedures across global facilities, optimize preventive maintenance, and deliver significant cost savings.
Tony Leombruno, Reliability Manager at Ardagh Group, explains how CMMS helped them:
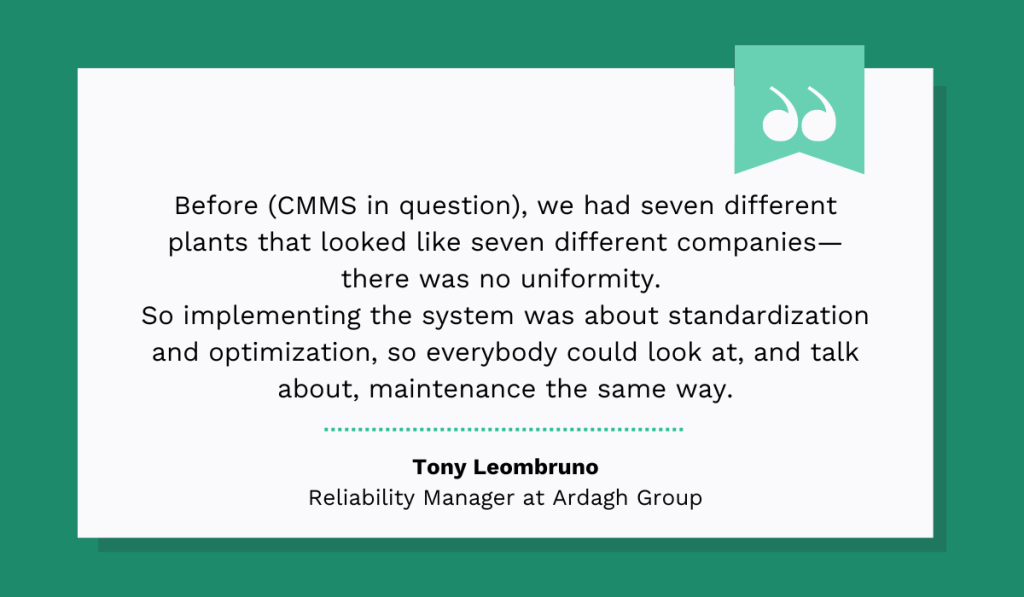
It all boils down to creating a more efficient and predictable maintenance process.
And SOPs, checklists, standardized parts, and technology help you achieve that.
Planning Maintenance Ahead of Time
Have you ever noticed that the ice cream machine at McDonald’s always seems to be out of order?
This common issue makes you wonder if they plan their maintenance beforehand.
If they did, those machines might work more consistently, avoiding inconvenience for customers and preventing lost sales of about $625 daily.
But McDonald’s isn’t alone in facing challenges like these with their equipment.
Across industries, more than half of companies still rely on “run-to-failure” maintenance, according to the Plant Engineering study from 2020.
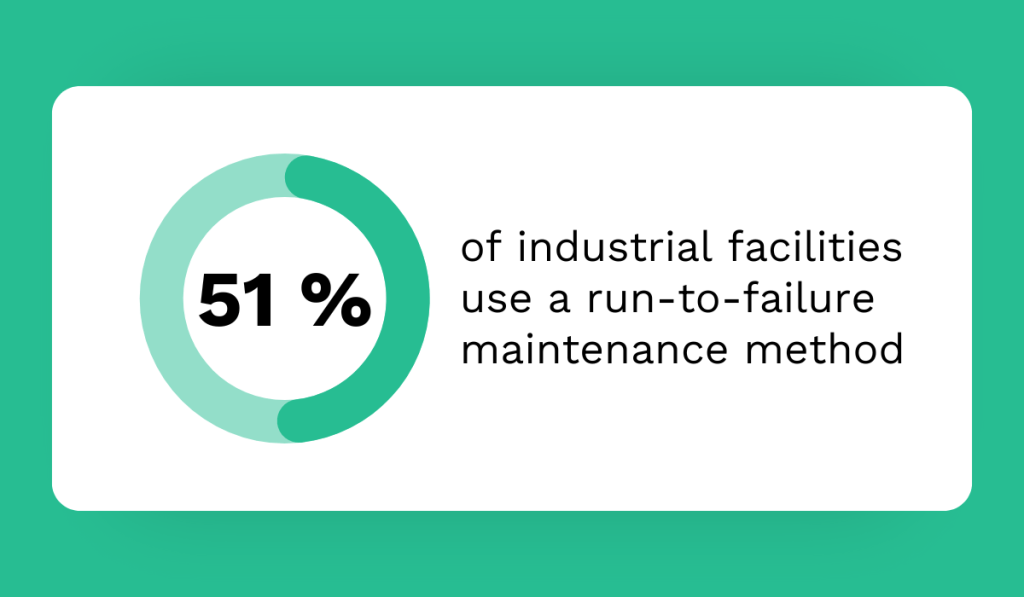
What is the “run-to-failure” approach?
We wouldn’t even call this “an approach.”
It simply means waiting until equipment breaks down before performing any maintenance.
Without question, this means unexpected downtime, higher repair costs, and paused operations.
However, if you’re a maintenance manager, you surely understand the importance of avoiding these disruptions.
And planning maintenance ahead of time is the way to do it:
- It extends equipment life
- Allows for more effective budgeting
- Planned maintenance reduces downtime
- It helps you avoid the high costs of emergency repairs
Not only that, but planning ensures all necessary resources, equipment, and personnel are prepared and scheduled.
It makes it easier to follow safety protocols, which protect employees and minimize accidents.
So, if you are one of those companies that like to run their equipment to failure, now is the time to start planning maintenance.
How?
To make it work for you, follow these steps.
First, using a system like CMMS to keep all maintenance records in one place would be wise.
To plan future tasks and know when each asset needs attention, you must know when the last maintenance is and what was done.
Then, with the help of the same system, you can schedule tasks for employees and assets, create work orders, and track progress.
And have it all in one place.
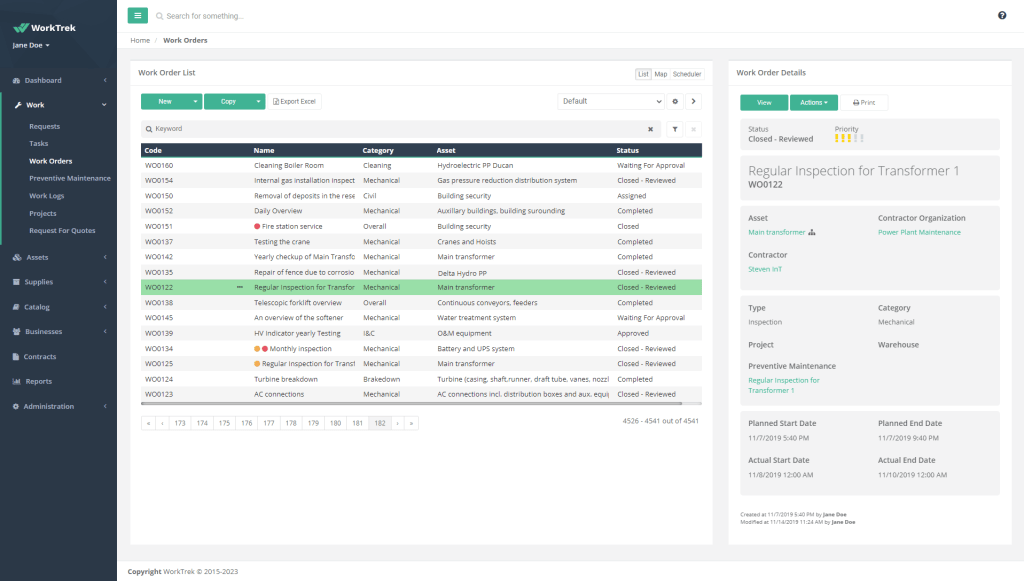
Additionally, you can plan maintenance during slower times to minimize disruption and keep your operations humming without unexpected stops.
Finally, when you have a maintenance plan, you can ensure you have spare parts, tools, and skilled staff on hand.
Overall, if you want to ensure smoother operations, happier customers and employees, and healthier assets, it’s always better to plan.
Prioritizing Tasks That Ensure Operations Continuity
However, not all maintenance tasks are equal.
Some tasks simply must be prioritized.
Some, particularly those involving critical assets, are essential for maintaining uninterrupted operations.
Neglecting these tasks can lead to dire consequences, including unplanned downtime, hefty repair costs, and even safety hazards.
Let’s delve into the numbers.
According to Siemens’ 2022 True Cost of Downtime report, unplanned downtime is increasingly costly across industries.
For instance:
As you can see, if your crucial assets experience unexpected downtime due to inadequate planning, the financial losses can be staggering.
But, effective prioritization of maintenance tasks isn’t just about cost savings and operational continuity.
It’s also about ensuring workplace safety, safeguarding against reputational damage, and preventing environmental harm.
Consider the Dunn County oil well incident, where equipment failure resulted in a significant wastewater spill.
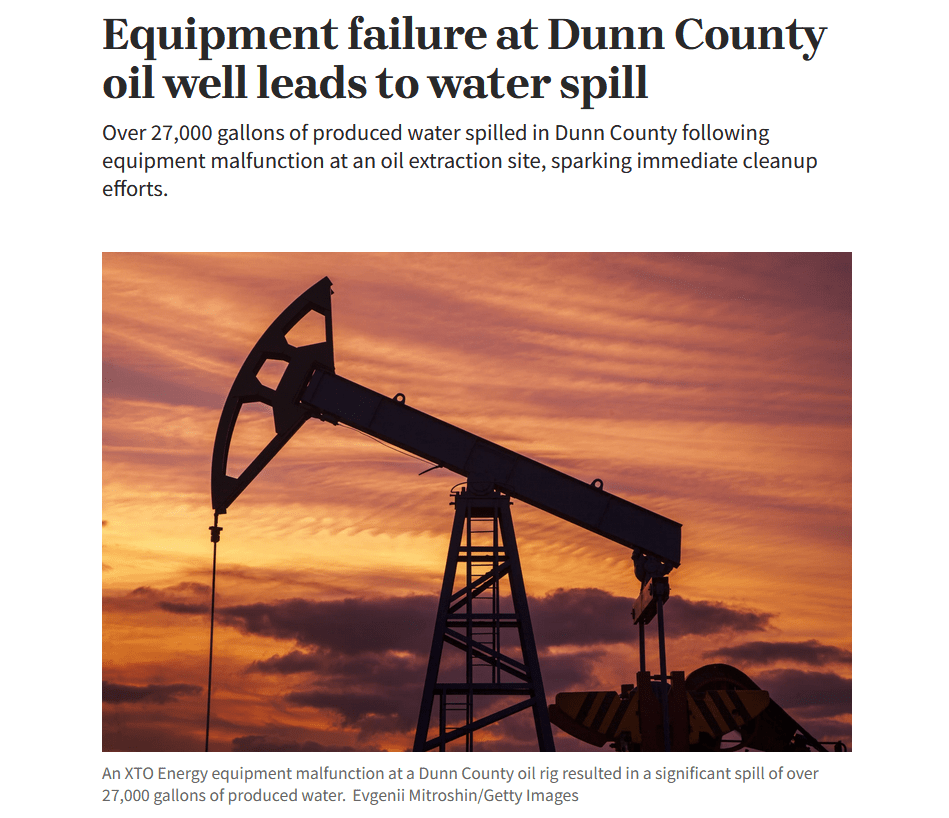
The water contained salts, oil residues, chemicals, and other harmful materials.
Improper containment and treatment of such spills can harm aquatic life, degrade soil health, and impact nearby water sources used for drinking and irrigation.
Thus, inadequate equipment maintenance can lead to immediate cleanup costs and tarnish a company’s reputation and environmental credentials.
So, what can you do to prevent this?
It’s simple: prioritize maintenance tasks.
How?
Begin by categorizing assets based on criticality, considering safety risks, potential downtime impact, repair costs, and environmental implications.
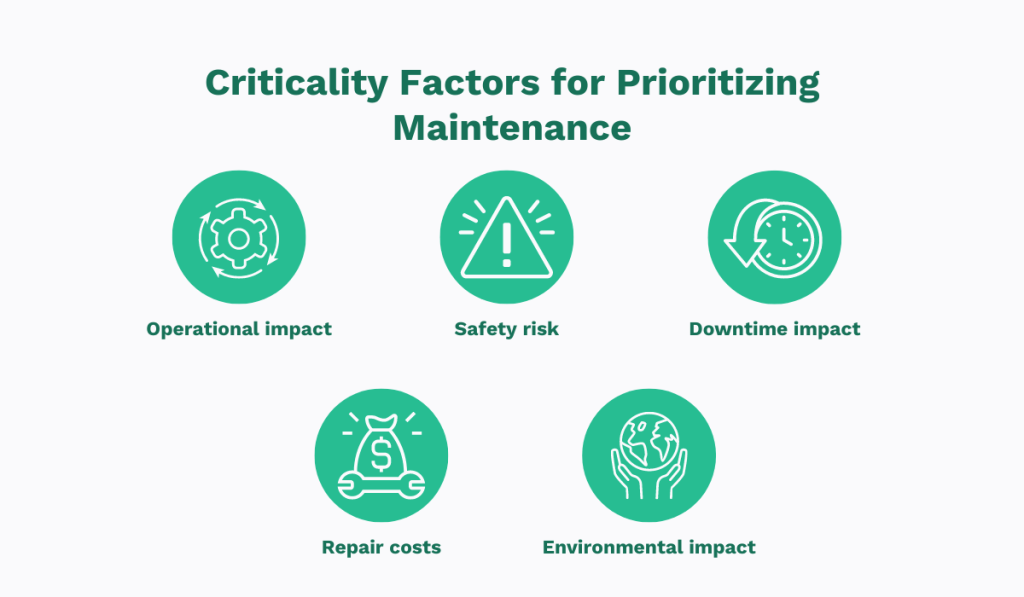
When you identify and then focus on critical assets, you will ensure they receive the necessary attention and maintenance to operate optimally.
Moreover, implementing predictive maintenance techniques such as vibration analysis systems, infrared thermography, and condition monitoring sensors allows you to anticipate equipment failures before they happen.
The bottom line is clear: prioritizing maintenance tasks is not just a financial strategy but a comprehensive approach to ensuring operational continuity, safety, and environmental responsibility.
So, start prioritizing your maintenance tasks today!
Using Software for Maintenance Management
Planning maintenance ahead and knowing which assets to prioritize is essential for efficient maintenance management.
But let’s be honest—if you have hundreds of assets that need maintenance, keeping track of all those tasks can be overwhelming.
It’s even worse if you’re still using pen and paper or Excel, which is prone to many errors and mismanagement.
That’s where computerized maintenance management software (CMMS) proves its worth.
This tool centralizes asset records, streamlines work order management, and helps maintenance planners, and managers make data-driven decisions.
Luckily, many companies recognize this.
According to Plant Engineering’s 2022 survey, 59% of companies already use CMMS.
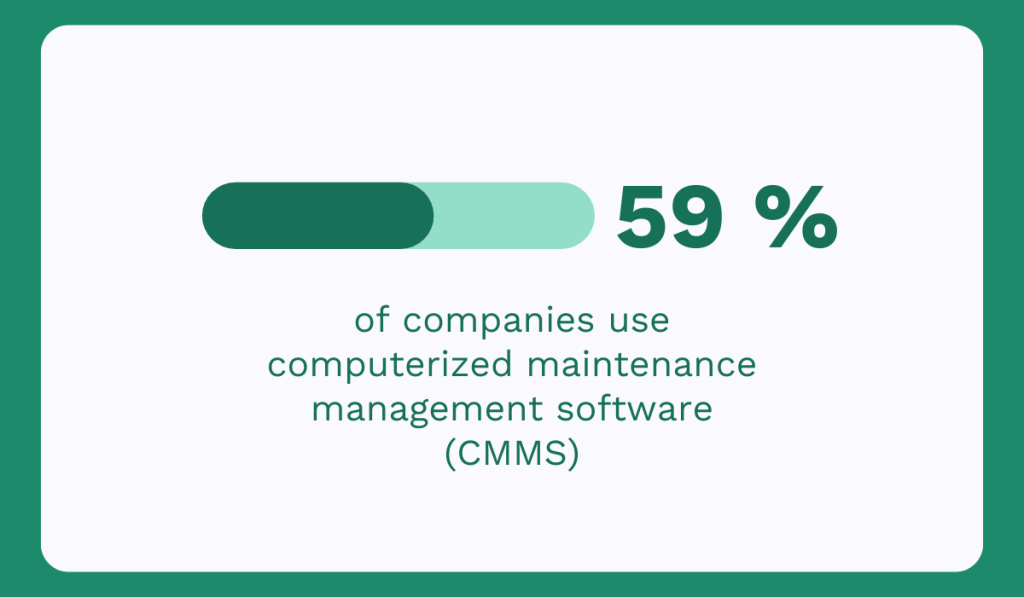
If you, too, want to boost your maintenance efficiency and ditch paper-based processes, it’s the right time to consider implementing such software.
Our CMMS, WorkTrek, is the right solution for you.
WorkTrek offers a suite of features that make maintenance planning more straightforward and more efficient.
Here’s a quick look at what it can do.
With WorkTrek’s scheduling calendar, you can easily create and assign work orders, track their progress, and delegate tasks to specific team members.
You can even set urgency levels for tasks and ensure all critical maintenance is done on time.
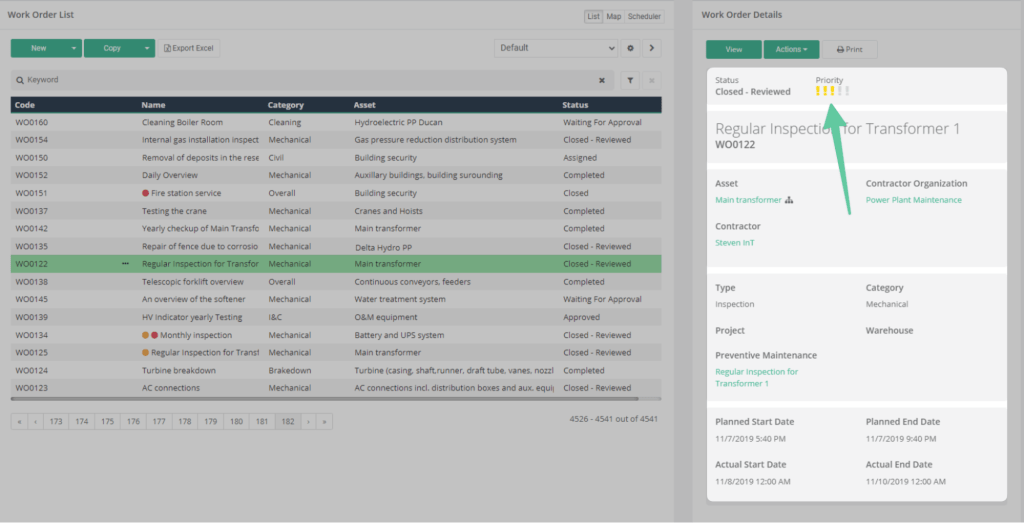
Moreover, all asset information, including maintenance history, manuals, and specifications, is stored in one accessible location.
This ensures that your maintenance teams have immediate access to all critical data to perform their job better.
On top of that, WorkTrek lets you schedule preventive maintenance at set intervals to catch minor equipment issues before they become expensive problems.
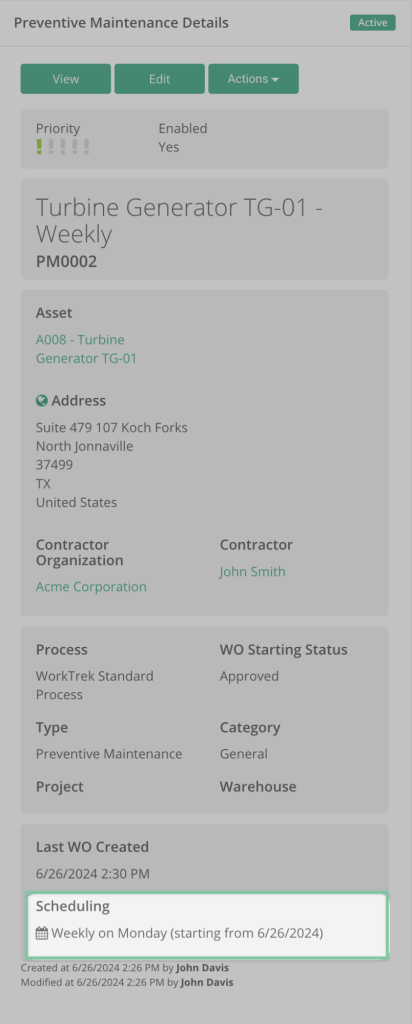
You can even integrate meters with the PM feature to automatically create maintenance work orders based on meter readings without manual input.
WorkTrek also lets you manage all your maintenance planning on the go.
The mobile interface allows you to create, assign, and track work orders from any location, increasing flexibility and efficiency.
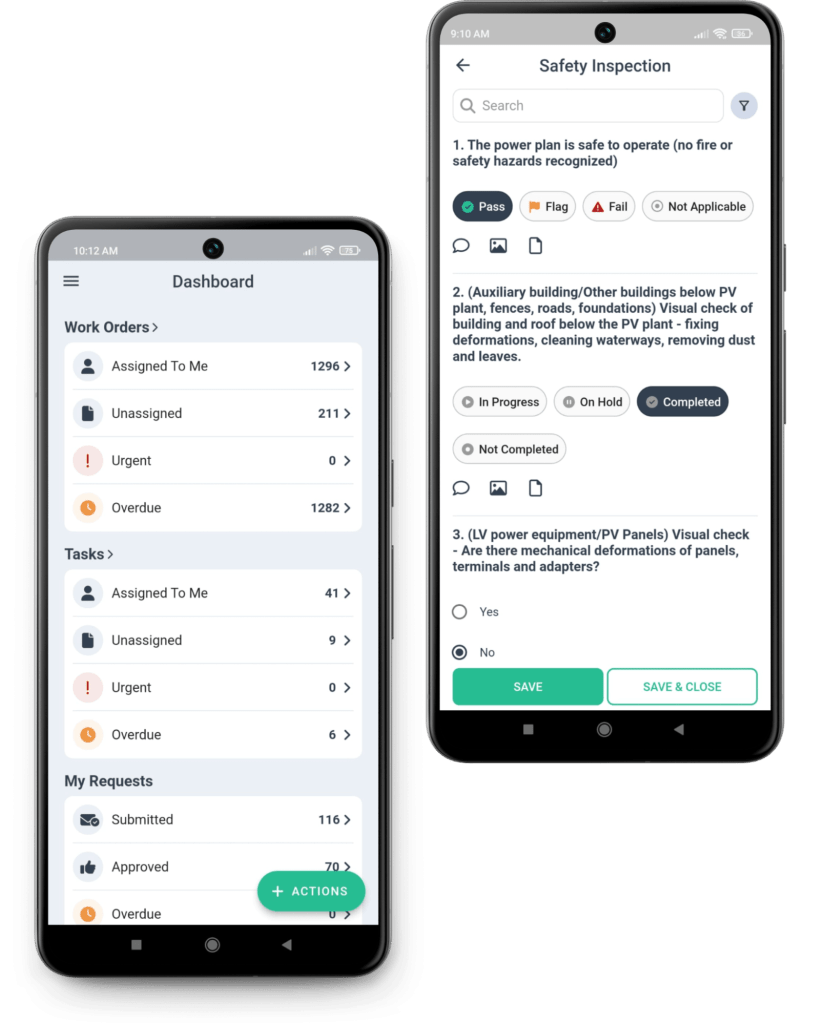
It’s simple: with WorkTrek, you can transform your maintenance planning from a cumbersome, paper-based process to a streamlined, efficient digital system.
This saves you time, reduces errors, and prioritizes your maintenance tasks.
And you know what that means?
No unplanned downtime and costly repairs.
Only healthy assets, better visibility into all your maintenance tasks, and more efficient operations.
Conclusion
As we saw today, efficient maintenance planning comes down to having a dedicated maintenance planner who will plan tasks and prioritize them effectively.
If you haven’t assigned a maintenance planner yet, consider assigning your best technician to this important role.
Arm your team with SOPs and checklists and enjoy a standardized maintenance process where everyone is on the same page.
Add the right software to the mix, and you’ll streamline your maintenance planning further and make it more data-driven.
Combine these practices and steer clear of danger!