Get a Free WorkTrek Demo
Let's show you how WorkTrek can help you optimize your maintenance operation.
Try for freeAre you tired of unexpected equipment breakdowns and all the disruptions they come with?
If you are, your maintenance strategy might be lacking, or you might not have one in the first place.
However, a good maintenance strategy can help you avoid costly issues and ensure your equipment stays in good working condition.
Today, we will tell you all you need to know about it.
From why it matters and how it can benefit you to the factors to consider when choosing the right strategy for your facility’s needs.
Let’s begin.
Maintenance Strategy Defined
A maintenance strategy is a plan that guides how you care for the equipment and systems you use daily.
It defines when and how maintenance should happen to keep everything—from machinery, tools, and all other assets—in top shape.
The goal is to prevent breakdowns, minimize downtime, reduce costs, and ensure safety.
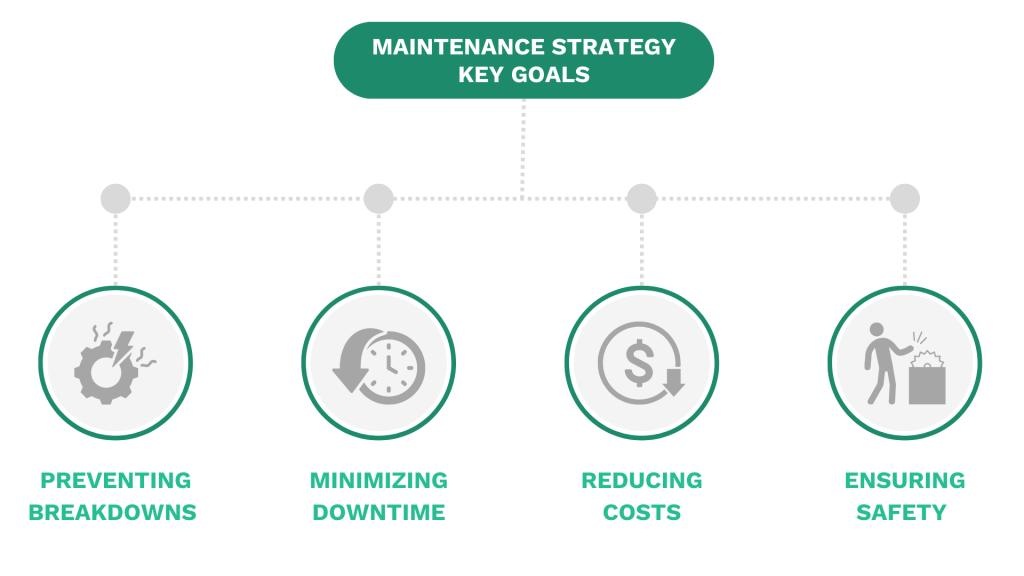
Various strategies, like scheduling regular checks at set intervals or performing maintenance based on the equipment’s condition, can be used.
Each approach is tailored to specific equipment needs and has pros and cons, which we’ll explore later.
But here’s the thing: a maintenance strategy shouldn’t be fixed.
Instead, it depends on your equipment, how it’s used, and the environment it’s in.
That’s why you need good data on your equipment and some experience to decide on the best strategy—or strategies.
Christopher Wilcox, Maintenance Manager at Univar Solutions, a leading global chemical and ingredient distributor, points this out:
He further explains that, for instance, you might begin with a preventive maintenance schedule based on manufacturer guidelines.
However, as you gather data, you may discover areas that lead to unplanned maintenance.
This information can help you refine your maintenance schedule, prioritize tasks, and find the best maintenance strategy for your equipment.
Why You Need a Good Maintenance Strategy
Nothing disrupts productivity faster than equipment failure. When a machine fails unexpectedly, everything stops.
And the cost of such unplanned downtime is staggering.
According to a 2023 ABB survey, unplanned downtime can cost industrial or manufacturing companies an average of $125,000 per hour.
But as Virve Viitanen, Head of Global Customer Care and Support at ABB Motion Services, points out, the real shock is how frequently unplanned downtime happens.
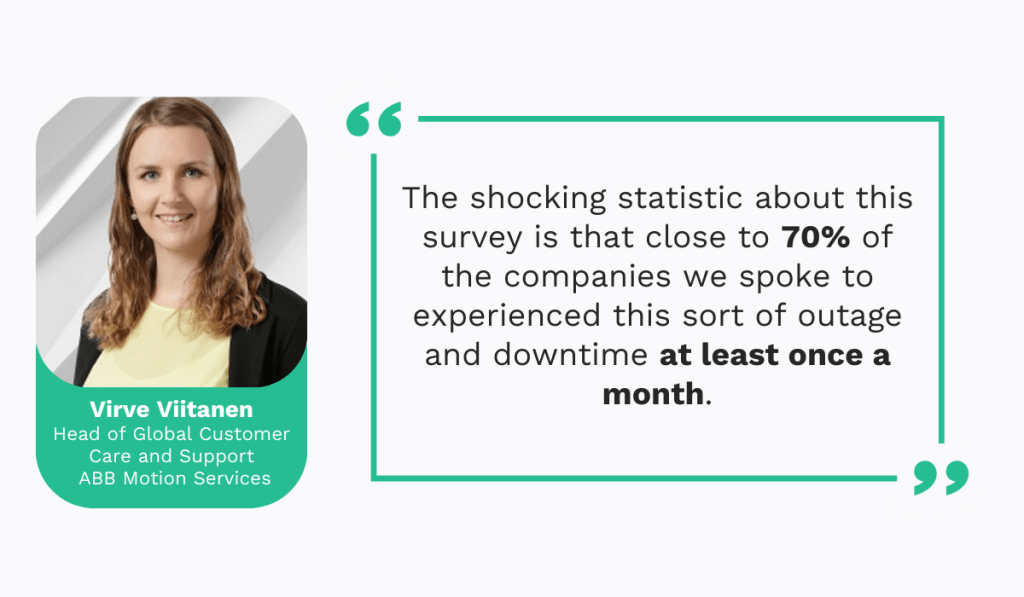
And it’s getting worse.
A 2024 report on the state of industrial maintenance found that 30% of companies saw an increase in the cost of unplanned downtime, adding even more pressure to their operations.
This cost isn’t just about fixing broken equipment—it includes lost production, labor, and even penalties for missed deadlines.
But here’s the good news!
A solid maintenance strategy, like preventive maintenance, can catch these potential issues before they become full-blown breakdowns.
The same report confirmed that, in the last 12 months, 45% of companies reported a decrease in unplanned downtime.
So, while the cost of unplanned downtime rises, it’s happening less often.
And for 65% of them, the key reason for less frequent downtime was evolving their maintenance strategy to stay ahead of problems.
In other words, they moved from a reactive approach to more proactive strategies like preventive or predictive maintenance.
Without a strategy, you risk frequent emergency repairs or even needing to replace your equipment entirely.
On the other hand, regular maintenance extends the lifespan of your machines, spreading out costs over time and avoiding those sudden, expensive fixes.
Lastly, let’s not forget safety.
Equipment failures or poor maintenance can lead to dangerous accidents, particularly in high-risk industries like aviation, manufacturing, and construction.
For example, poor maintenance was the cause of a tragic 2022 helicopter crash in New Mexico, which killed four people.
Investigators determined that engine failure—due to fatigue and a lack of maintenance—caused the accident.
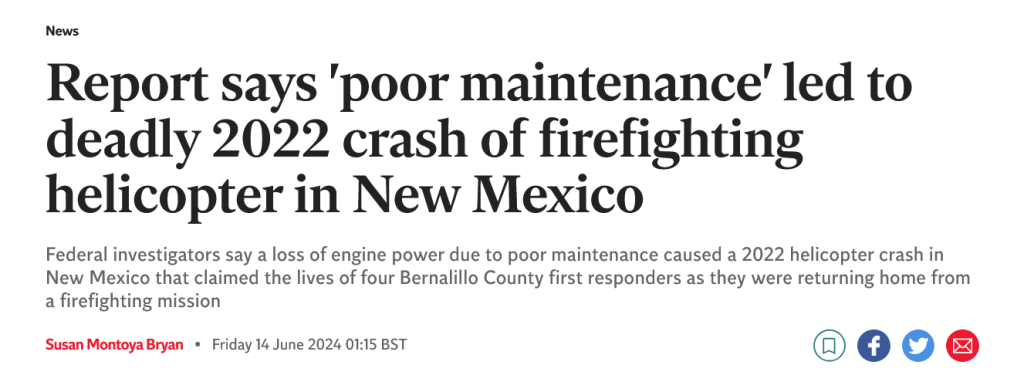
However, with the right maintenance strategy, maintenance is never skipped—especially not on critical equipment.
In fact, safety checks are built into the process, which reduces the risk of accidents caused by malfunctioning machinery.
In the end, if the equipment runs smoothly, your team can focus on getting the job done safely and efficiently.
All of this combined is why you need a good maintenance strategy.
Types of Maintenance Strategies
Maintenance strategies range from merely reacting to equipment failures to using advanced technology to predict issues before they happen.
Let’s break down the most common types of maintenance strategies and how they work.
Preventive Maintenance
Preventive maintenance focuses on stopping problems before they start.
Instead of waiting for something to break down, this strategy involves scheduling regular tasks—like inspections, part replacements, or cleaning—at fixed intervals.
These intervals can be time-based (e.g., every month) or usage-based (e.g., every 500 hours of operation).
The main goal is to catch potential issues early and prevent major breakdowns later.
This is also the most common maintenance strategy in industries, with almost 87% of facilities using it.
Preventive maintenance is popular because it reduces unexpected breakdowns and keeps repair costs low.
However, one downside is that you might end up replacing parts or doing maintenance even when it’s unnecessary—like changing a filter that’s still in good condition.
But the trade-off is worth it because it helps you avoid bigger problems down the line.
However, there is one challenge: planning preventive maintenance and keeping track of all those tasks.
It can get overwhelming, especially if you’re managing a large facility or hundreds of pieces of equipment.
Even more so if you’re still doing it manually.
That’s where a computerized maintenance management system (CMMS) steps in.
A good CMMS, like WorkTrek, makes organizing and planning preventive maintenance easier.
Instead of manually tracking every maintenance task or relying on guesswork, WorkTrek keeps everything organized in one place.
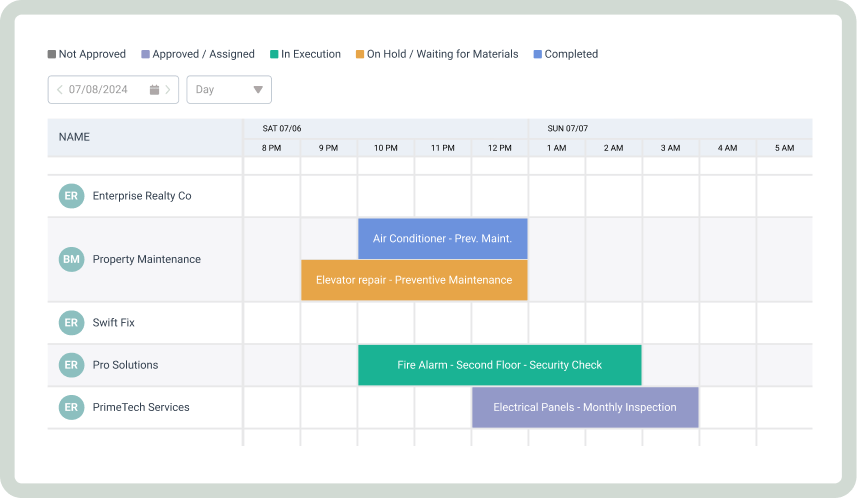
You can schedule maintenance, track work orders, and even set up automatic triggers based on real-time data, ensuring you’re always ahead of potential issues.
For example, if an HVAC meter shows that temperatures have reached a set point, you must update this in the system, and WorkTrek will automatically create a work order.
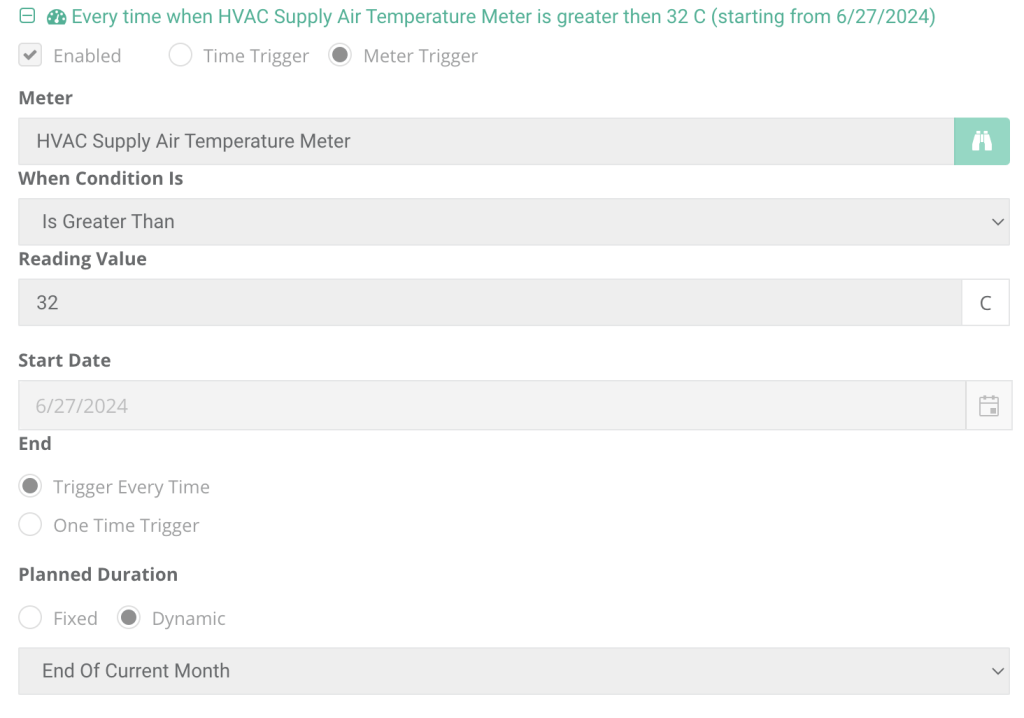
This will help ensure that the maintenance team responds to real conditions—not just following a set schedule.
In short, using a CMMS takes the burden off your team, making preventive maintenance smoother, more efficient, and more precise.
Reactive Maintenance
Reactive maintenance, or breakdown maintenance, is performed after equipment breaks down.
Essentially, you wait for the failure to happen and then repair the damage. It is unplanned and often urgent.
While this approach to maintenance sounds risky, it makes sense for non-critical or inexpensive assets where the cost of regular checks isn’t justified.
In industries where some equipment is cheap to fix, reactive maintenance can save unnecessary effort and costs.
And sometimes, there are things that you simply can’t plan for, as Justin Foat, Fleet Maintenance Manager at Herlache Truck Lines, explains with an example:
For example, during the hotter months, you can send out a truck fitted with brand new tires, have them hit the hot pavement, roll over a rock, and boom, it blows.
This is the kind of scenario that neither preventive nor predictive maintenance could have predicted.
As such, reactive maintenance still plays a major role in many industries.
In fact, 57% of facilities rely on it.
However, the problem is that 5% of companies still use it as their sole maintenance strategy, leaving them vulnerable to lost productivity, higher repair costs, and more unplanned downtime.
So, while reactive maintenance can be cost-effective for specific cases if it’s relied on too heavily, it can lead to higher overall repair costs and extended downtime.
That’s why it works best when combined with other maintenance strategies.
Predictive Maintenance
The predictive maintenance strategy removes the guesswork from equipment care by using real-time data to predict potential failures.
It monitors factors like vibration, temperature, or oil quality to spot early signs of wear and tear before they lead to bigger problems.
This strategy can deliver huge benefits; a Deloitte study provides the numbers to back this up.
Their research breaks down the benefits of predictive maintenance, like cost savings and increased equipment uptime:
Given these results, it is not surprising that industries worldwide are adopting predictive maintenance.
Even airports do it.
For instance, the UK’s biggest airport, Heathrow, uses predictive maintenance and machine learning to monitor its baggage handling system to prevent failures and minimize passenger disruptions.
Though predictive and preventive maintenance both aim to prevent future failures, there’s a key difference we must point out.
While preventive maintenance relies on a fixed schedule, predictive maintenance is data-driven.
Simply put, it triggers maintenance only when the data suggests it’s necessary.
This makes predictive maintenance more precise, but it also requires a bigger investment in monitoring technology and skilled personnel.
Reliability-Centered Maintenance
Reliability-centered maintenance (RCM) is a strategy that balances preventive, reactive, and predictive maintenance to ensure a system’s reliability.
The goal is to determine the most efficient way to maintain critical equipment while minimizing downtime and maintenance costs.
This strategy is used in industries where safety and uptime are crucial—like aerospace, defense, and energy.
In fact, RCM originated from the aviation industry in the 1960s, when the traditional approach of time-based maintenance wasn’t enough to prevent failures that were causing airplane crashes.
Below is an overview of the steps in the RCM strategy:
As you can see above, RCM has many steps and is a comprehensive approach.
Its complexity requires deep knowledge of the equipment and, like predictive maintenance, calls for advanced tools and training.
All in all, when you understand the strengths and limitations of these strategies, you can determine which approach—or combination of approaches—best suits your facility’s unique needs.
Whether you’re aiming for the regularity of preventive maintenance, the insight of predictive strategies, or the comprehensive nature of RCM, the right strategy can make all the difference in keeping your operations running smoothly and efficiently.
What to Consider When Choosing Your Maintenance Strategy
Don’t pick a maintenance strategy on a whim.
Critical factors must be considered before deciding which one works best for your facility.
Choose wrong, and you could face compliance issues, budget overruns, or constant equipment breakdowns.
So, what should you focus on?
Let’s break down the key factors to take into account.
Regulatory Requirements
First, ensure your maintenance strategy follows all industry standards and safety regulations.
In some industries, like healthcare or aviation, safety is non-negotiable.
Compliance mandates are strict, and cutting corners could lead to serious consequences.
For example, in aviation, the Federal Aviation Administration requires operators to conduct regular inspections to ensure aircraft are safe.
In these cases, relying only on reactive maintenance won’t cut it.
You’ll need a preventive or predictive approach to avoid non-compliance and hefty fines.
Your Budget
Not all maintenance strategies cost the same.
Predictive maintenance, for example, comes with a bigger price tag due to sensors, monitoring tools, and data analysis.
If your budget doesn’t allow for that level of investment, consider preventive maintenance instead. It’s less expensive and still effective at reducing unexpected downtime.
State of Your Equipment
Ask yourself—how old are your machines? Are they breaking down often?
If they are, pouring money into a high-tech predictive maintenance system might not make sense.
For instance, an older machine nearing the end of its useful life probably won’t benefit much from advanced monitoring systems.
In this case, sticking to preventive or even reactive maintenance might be the more practical choice.
But predictive maintenance can be a game-changer if you’ve got newer, critical equipment.
It helps you avoid surprise breakdowns and can save you a lot of money in the long run.
Moreover, if your equipment has failure modes that are simply unpredictable, you’ll also want a strategy that allows you to see problems before they happen.
Erik Hupjé, founder of The Reliability Academy and expert in the maintenance field, explains this approach.
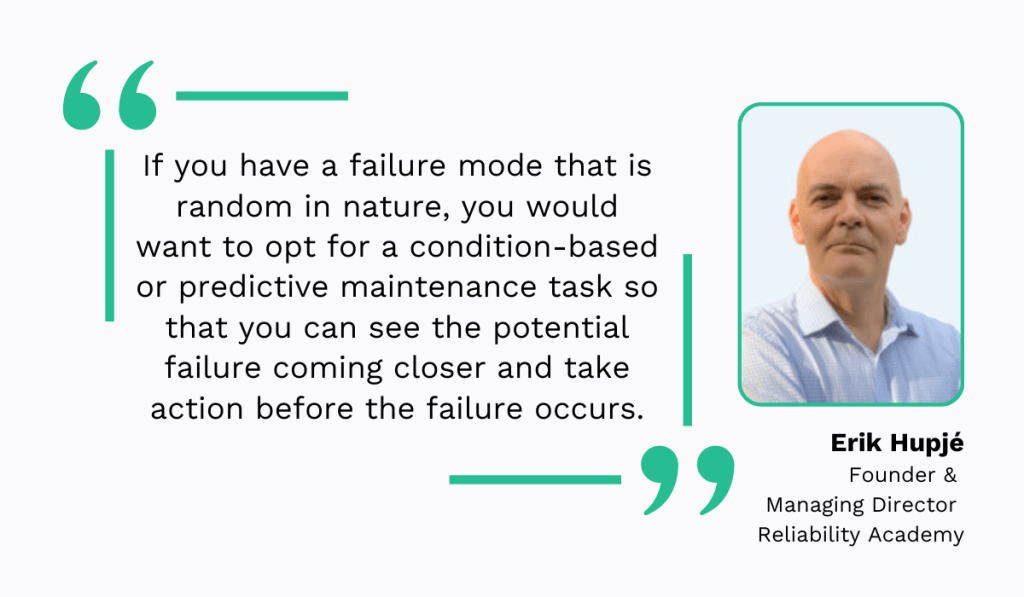
The bottom line is to assess your equipment’s condition carefully.
If it’s aging and near the end of its useful life, preventive or reactive maintenance may be more practical.
Staff Availability
Even the best strategy can fall flat if you don’t have the right people to do it.
Some strategies, like predictive maintenance, require specialized skills because your team needs to know how to analyze data and manage real-time monitoring systems.
Predictive maintenance might be unrealistic if your staff isn’t trained for that. Or you will have to invest in training them.
By thinking through these factors, you’ll be in a much better position to choose a maintenance strategy that makes sense for your facility.
Conclusion
The maintenance strategy you choose directly affects your facility’s performance, costs, and safety.
It’s about finding a system that fits your team, equipment, and budget.
Whether you go with preventive, predictive, or a mix of approaches, the goal remains the same: to keep things running smoothly with as little disruption as possible.
And remember, your strategy isn’t set in stone.
It should evolve with your needs, technology, and the condition of your equipment.
This way, you’ll extend the life of your assets and keep your facility efficient for the long term.