Get a Free WorkTrek Demo
Let's show you how WorkTrek can help you optimize your maintenance operation.
Try for freeIf you’re responsible for maintenance in plants or facilities, you’ve likely come across predictive maintenance (PdM).
You might wonder if this advanced strategy could enhance your maintenance operations, or perhaps you simply want to know more about how it works and why it’s gaining popularity.
You will learn nine key statistics about predictive maintenance today.
By the end, you’ll understand PdM’s value, why companies are adopting it, and the requirements for implementing it effectively.
Let’s begin.
Predictive Maintenance Market Was Valued at $7.85B in 2022
Predictive maintenance is a rapidly growing market.
In 2022, its global value was estimated at $7.85 billion. By 2030, this figure is expected to skyrocket to $60.13 billion, according to Grand View Research.
That’s an astonishing compound annual growth rate of 29.5%
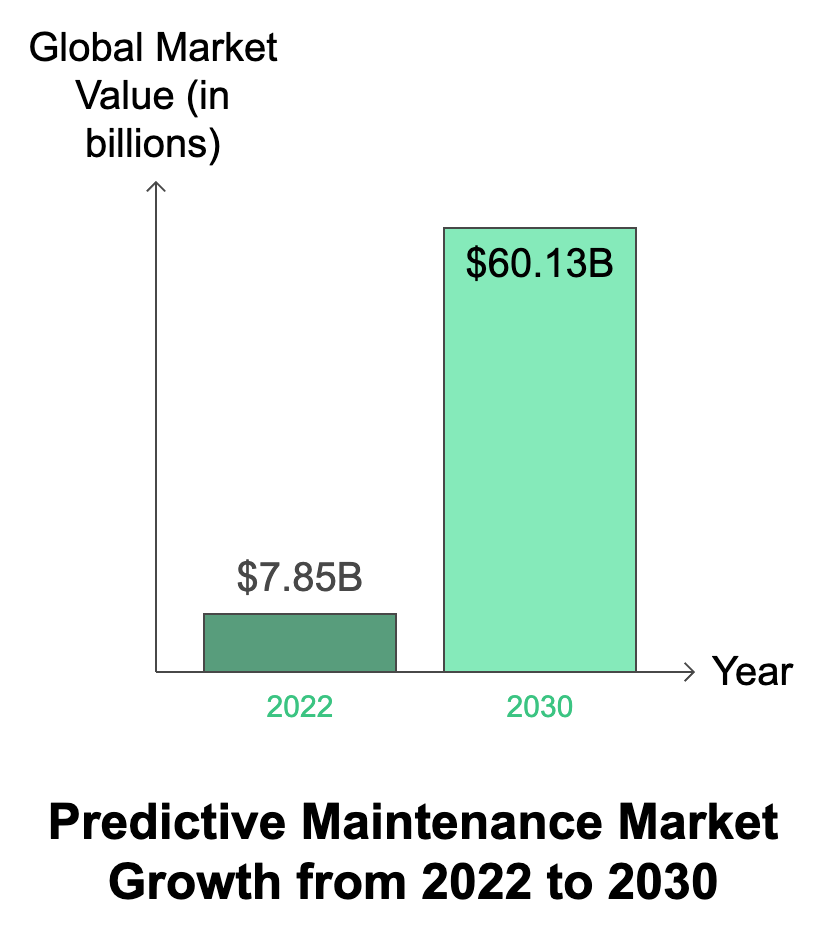
The report reveals that this growth is driven by two major factors:
- Stricter workplace safety standards
- The increasing availability of AI and machine learning (ML) tools
These advanced tools enable companies to predict when machinery will fail and schedule repairs before that happens, reducing costly unplanned downtime.
Not only does this keep the operations running, but it also reduces the risk of accidents.
This combination of enhanced safety and cost savings explains why more companies are adopting predictive maintenance and why the market continues to expand.
Now, who is leading the charge?
Industry giants like IBM, Schneider Electric SE, Siemens, and Microsoft are heavily investing in these technologies, making predictive maintenance more accessible and accurate than ever before.
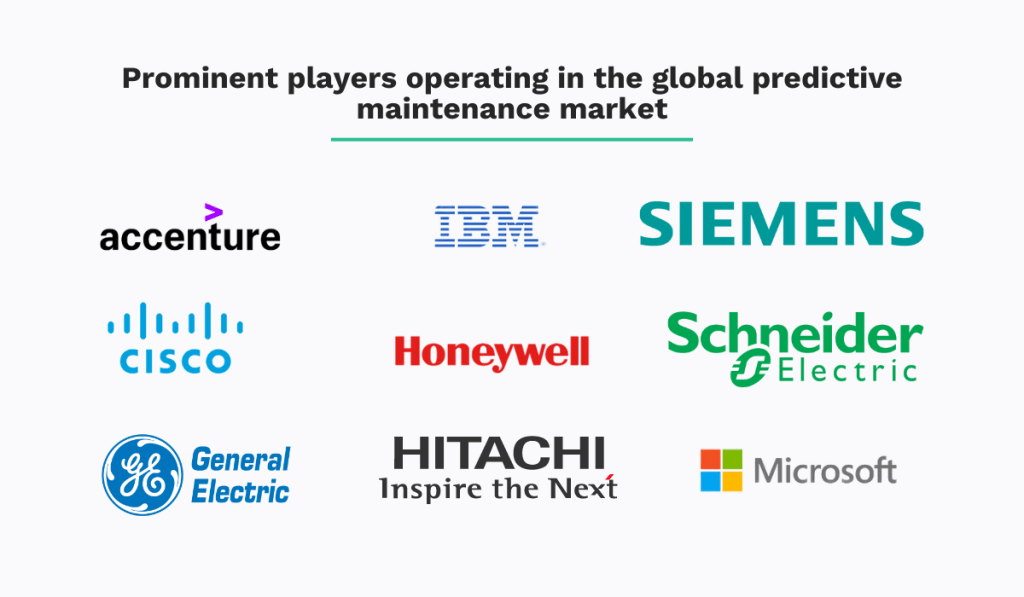
For example, Toyota is already leveraging IBM’s predictive maintenance solution, Maximo, to improve its operations and see impressive results.
Brandon Haight, General Manager at Toyota North America Indiana, explains what it looks like:
So, if you’re considering whether predictive maintenance is worth it, this explosive growth tells you that it’s becoming the preferred solution for businesses looking to improve efficiency and save on costs.
30% of Facilities Use Predictive Maintenance
Another global survey on the state of industrial maintenance in 2024, involving 1,165 MRO professionals across industries like manufacturing, retail, and hospitality, shines a light on the popularity of predictive maintenance.
Of the 1,165 companies surveyed, nearly one-third actively use PdM.
Predictive maintenance is the third most popular strategy behind preventive maintenance and the run-to-failure approach.
Preventive maintenance remains the most widely used maintenance strategy because it’s simple—based on regularly scheduled checkups tied to time or usage.
However, it has one fundamental drawback: it doesn’t consider the equipment’s actual condition.
This can result in unnecessary maintenance for machines functioning perfectly or failing to detect potential issues that may arise between scheduled checkups.
Predictive maintenance takes a more data-driven approach.
It analyzes real-time equipment data to detect wear and tear before an issue arises.
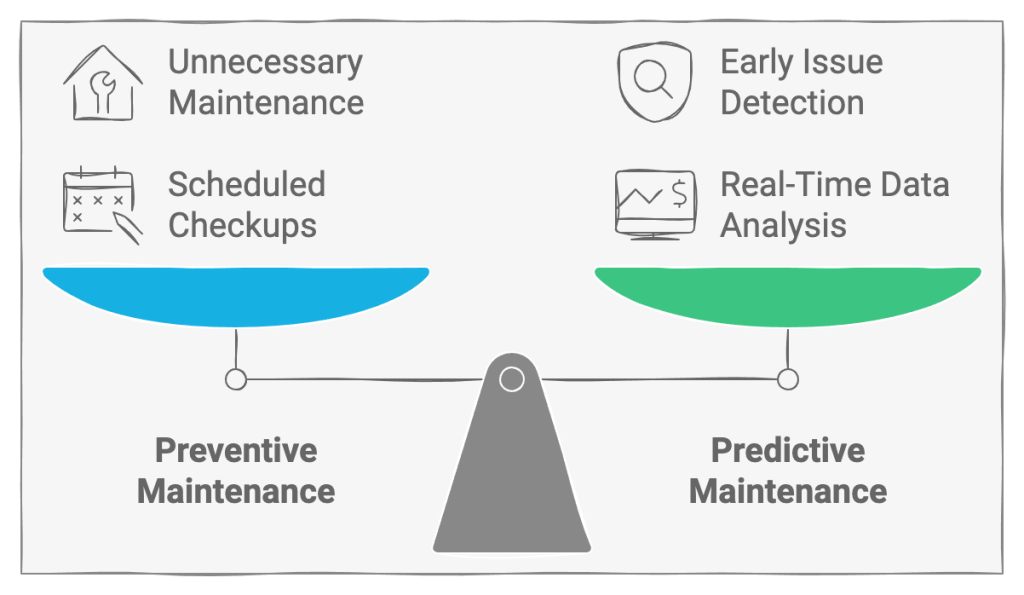
This reduces unnecessary maintenance and minimizes unexpected breakdowns, saving time and money.
Of course, PdM requires a higher initial investment in technology and training.
This upfront cost is one reason why preventive maintenance still leads the way for many companies.
However, as more businesses recognize the potential for long-term savings, predictive maintenance (PdM) is gaining traction.
And this statistic shows that the tide is turning.
79% of Facilities Involve Technicians in Predictive Maintenance
When it comes to predictive maintenance; you might wonder who’s taking the lead—maintenance inspectors, reliability engineers, IT specialists, or technicians.
According to a PwC and Mainnovation 2017 survey, the answer is clear: technicians play a key role in predictive maintenance.
They are directly involved in PdM efforts in 79% of surveyed facilities.
This makes sense, as maintenance technicians are the closest to the machinery and understand the nuances of how the equipment operates.
However, it’s important to note that most technicians are involved in lower maturity levels of PdM, primarily levels 1 and 2, where visual or instrument inspections are common.
Other professionals involved in the process, like maintenance inspectors and reliability engineers, are needed for higher predictive maintenance maturity levels.
But how do facilities stand when it comes to PdM maturity?
The following statistics will tell us.
Only 11% of Facilities Reach Level 4 Predictive Maintenance
The same survey revealed that most facilities were still in the early stages of predictive maintenance maturity in 2017.
Only 11% reached the highest Level (4), where big data analytics and machine learning drive decision-making.
To understand the journey to Level 4, let’s break down the four levels of PdM maturity (as per PwC and Mainnovation):
Level 1: Visual inspections | This is the most basic form, where equipment is checked based on technician observations. |
Level 2: Instrument inspections | Tools and instruments are used to measure conditions. |
Level 3: Real-time condition monitoring | Facilities gather real-time data from their machines to predict failures. |
Level 4: Big data and machine learning (PdM 4.0) | Here, advanced algorithms analyze large amounts of data to provide predictive insights that improve asset availability and reduce downtime. |
Essentially, maturity levels depend on how much data is being used to forecast equipment failures.
To reach level 4, companies must invest in sophisticated technologies like machine learning.
While only 11% of companies were at this level in 2017, it’s likely more companies have advanced since then, given the growing trend in the use of data-driven technologies.
Interestingly, the survey highlighted that certain sectors, like rail, were leading the way.
In 2017, 42% of rail facilities had already reached level 4, compared to the 11% of companies in all sectors.
The rail industry’s high use of PdM can be attributed to its reliance on similar assets across locations, which makes data collection and analysis more effective.
Additionally, political and public pressure to keep transportation running smoothly drives innovation and investments in this sector.
Predictive Maintenance Can Lower Costs by 25%
We’ve already touched on how predictive maintenance can save money.
However, Deloitte Analytics Institute gives us more specific information: PdM can lower maintenance costs by up to 25%.
How does this happen?
For starters, with predictive maintenance, you avoid emergency repairs, which means you also avoid related costs.
When a critical machine in a facility breaks down unexpectedly, you have to pay for emergency repair and associated costs like expedited parts shipping and overtime pay.
Another way PdM reduces costs is by extending the lifespan of the equipment.
By addressing minor issues before they escalate, your machines run smoothly for longer, reducing the need for replacements.
Additionally, compared to preventive maintenance, PdM skips unnecessary checkups that often happen with fixed schedules, focusing only on repairs when they’re truly needed.
All of this adds up to significant long-term savings for your facility.
47% Say Improving Uptime Is Their Main Goal With PdM
However, lower maintenance costs are not the main driver for adopting PdM.
According to the previously mentioned PwC survey, almost half of facilities say improving uptime is their main goal.
Why is uptime the main goal? Because downtime costs manufacturers billions each year.
When a machine stops unexpectedly, production ceases, resulting in revenue loss.
Take Sitech Services, for example, a company providing site services to 22 factories in the chemical industry.
Their former director, Richard Schouten, noted that downtime could cost them up to half a million euros daily!
For companies like this, uptime outweighs the importance of shaving a few percentage points off maintenance costs.
And it’s not just about money.
Downtime affects production schedules, delays deliveries, and can damage customer relationships—hurting your reputation.
That’s why more companies are turning to PdM to eliminate unwanted downtime and all of its negative consequences.
Predictive Maintenance Boosts Uptime by 10-20%
But how much can PdM improve your uptime?
According to Deloitte’s internal studies, it can be anywhere between 10 and 20%.
This is because PdM allows you to plan maintenance activities at the most convenient times.
Instead of reacting to breakdowns during production hours, you can schedule repairs during off-peak times or when the right personnel are available.
PdM also helps your logistics team by forecasting which parts you’ll need, ensuring you have the right components when maintenance is due.
In short, PdM can optimize your entire maintenance process to ensure equipment stays up and running when you need it most.
But there’s one critical factor you need for PdM to work.
And you probably already know what it is.
60% of Maintenance Professionals Say Data Availability Is Key to PdM Success
According to PwC and Mainnovation, 60% of maintenance professionals believe that access to reliable, accurate data is critical for successfully implementing predictive maintenance.
And it’s no surprise—PdM depends on continuous data streams to predict equipment failures before they happen.
Without this data from sensors, it’s impossible to predict maintenance needs effectively.
However, many facilities face challenges with data collection.
Older equipment may lack the sensors required for real-time monitoring, or the infrastructure to collect data from these machines might not yet exist.
This is especially challenging in environments like hazardous industries or in areas where assets, like trains or trucks, move over large distances, which demands robust IoT networks.
The quality of data is just as important.
To accurately predict failures, you need detailed information such as temperature, pressure, and even more advanced metrics.
Without these insights, predictive maintenance is essentially running blind.
51% of Facilities Aren’t Planning to Adopt Predictive Maintenance
Despite all the benefits of predictive maintenance, over half of the facilities surveyed in PwC’s 2017 study said they weren’t planning to adopt it.
Why would so many shy away from such a promising technology?
For one, implementing PdM is costly.
It requires substantial investments in hardware and software and hiring specialized workers like data scientists and engineers to interpret and act on the data.
However, this statistic is from 2017, and since then, the adoption of PdM has grown.
Still, many companies aren’t ready to adopt PdM.
For those companies, there’s still an option to improve reliability through other maintenance strategies, like advanced preventive maintenance.
For example, a modern CMMS like WorkTrek allows you to track meter readings and set advanced preventive schedules, as shown in the image below.
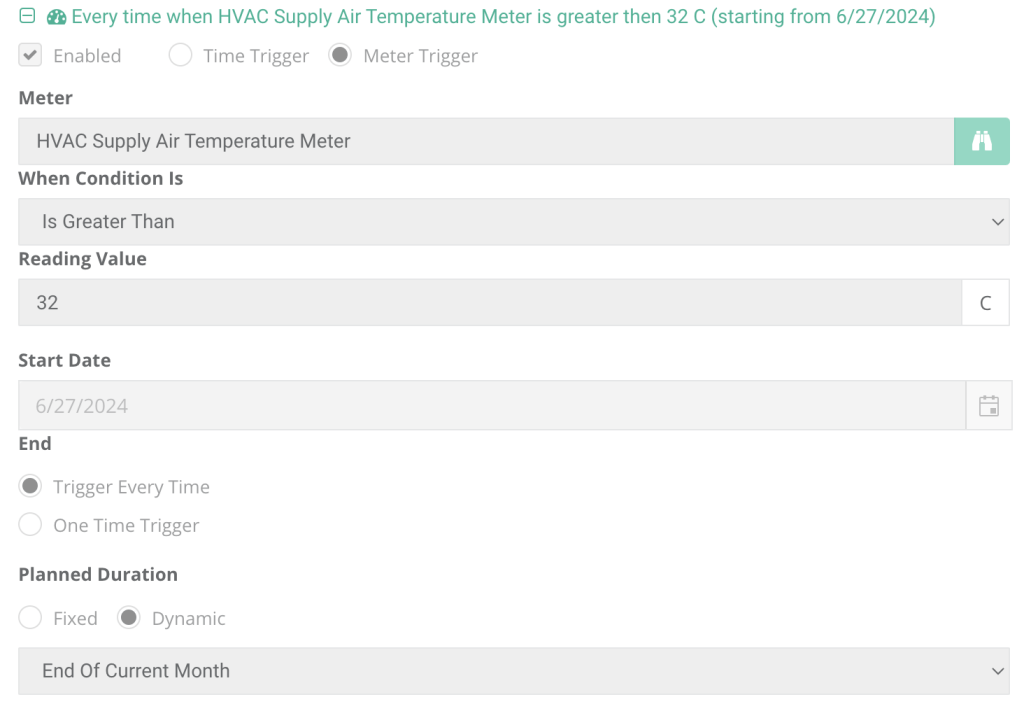
This can provide companies with a more reliable maintenance approach even if they are not yet ready for predictive maintenance.
Conclusion
Predictive maintenance is gaining momentum, bringing the benefits of reduced downtime, cost savings, and improved safety to more and more facilities.
However, only some companies are ready to adopt it, and many are still progressing through different maturity levels.
Nonetheless, the growing trend toward digitalization, artificial intelligence (AI), and machine learning positions PdM as the future of maintenance.
As more companies invest in these technologies, those that embrace predictive maintenance early on will be in a stronger position to reap its long-term benefits.