Get a Free WorkTrek Demo
Let's show you how WorkTrek can help you optimize your maintenance operation.
Try for free
Introduction
Conventional concepts such as the one that suggested intervention for repair only when a failure occurs have proven their validity in the past, but have been supplanted for several years by new techniques and systems, primarily that known as preventive maintenance. The possibility of applying maintenance management to any type of activity, also thanks to the use of maintenance management software (CMMS), has allowed its diffusion among an increasing number of companies aware that if they want to maintain their competitiveness, it is necessary to avoid excessively high costs caused by productivity losses, low levels quality, downtime and therefore, in other words, loss of profit.
What Does CMMS Software Do and How Does it Work?
The CMMS is a software capable of containing all the maintenance information: from the technical database to the asset sheets, through maintenance plans, requests for technical intervention and work orders. It also allows you to manage all the documentation, the history of interventions and work reports, the spare parts in the warehouse, as well as of course the technicians and suppliers.
Thanks to all this information, it is able not only to help you optimize maintenance processes, but also to provide all the data necessary for a detailed analysis of them, monitoring times, costs and performance thanks to business intelligence systems that analyze the data for you, creating personalized and incredibly detailed reports.
The best CMMS software is also able to automate a large part of these processes, for example by automatically creating work orders or assigning them, always automatically, to the right personnel, based on the indications you have given to the system.
Let’s say for example that you need to plan preventive maintenance interventions based on the working time of a machine. The CMMS is able to generate a new work order every time this time is reached, inform you if spare parts are available in stock, attach the necessary documents and maintenance checklists to ensure that the interventions are carried out in the correct way and finally assign them to the personnel indicated on the basis of the machinery or its location.
This allows you to drastically reduce the costs and management times of your resources, as well as naturally machine downtime, also reducing manual actions and margins of error.
One of the most important features of modern CMMS systems is the ability to use the mobile app.
Thanks to the mobile app, technicians can take the CMMS for company maintenance with them wherever they go in the field. They will be notified via a simple notification (or an email) when they are assigned a work order, they will be able to consult the documentation, record the intervention times, take advantage of the checklists attached to the work order and add the pieces in just a few taps spare parts used on the final report.
This will allow them not only to cut intervention times, but also to automatically record all data and information relating to the work order within the CMMS system. Once the intervention is completed, they will be able to automatically generate the end of work report, create it directly on their phone and send it to the system (as well as by email to the figures involved).
At this point the CMMS system records the data and sorts them within the platform, where they will be available in real time.
Likewise, the maintenance manager will have a complete view of the progress of maintenance operations, will be able to easily monitor, without any additional action, the work orders carried out and those still to be carried out, as well as analyze the recorded data in real time.
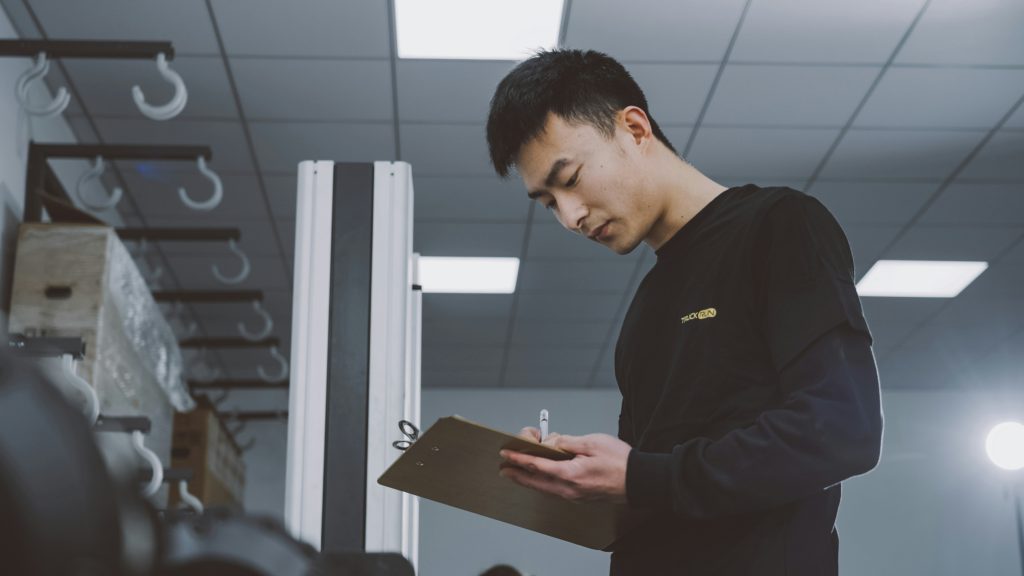
What is Preventive Maintenance?
Preventive maintenance is a special type of extraordinary maintenance that is carried out at predetermined intervals or according to the criteria prescribed in maintenance plans, and aims to reduce the probability of failure or deterioration of the functioning of assets or systems.
Definition of Preventive Maintenance
To give the most complete possible definition, preventive maintenance refers to all those activities that allow us to recognize the current functioning of the system, in order to take the necessary measures to slow down its normal degradation.
Objectives of Preventive Maintenance
Preventive maintenance therefore has the main objective of extending the life cycle of assets and limiting machine downtime or, more generally, other corrective maintenance actions, in order to prevent excessive qualitative and quantitative deterioration of production. This goal is achieved through periodic inspections or based on certain metrics chosen by the maintainer, so that necessary but not yet obvious preventive interventions can be implemented before excessive wear or failure becomes apparent.
This type of maintenance includes actions such as cleaning, lubrication, and replacement of plant or asset components.
Types of Preventive Maintenance
Even if it is not entirely precise, in general we could say that any type of intervention that does not belong to the field of corrective maintenance, therefore does not respond to a malfunction, belongs to the category of preventive maintenance. For this reason, there are many types of preventive maintenance and they require different technologies and experiences.
The most common types of preventive maintenance are:
- Maintenance in Condition
- Periodic Maintenance (Cyclic Preventive Maintenance)
- Predictive Maintenance
Preventive Maintenance in Condition
It is a maintenance policy based on meter readings or monitoring of specific pre-determined metrics, recorded and fed into the CMMS system. When the values set in the maintenance software are reached, a work order is automatically generated. A very simple example of this type of maintenance concerns cars: changing tires is a type of condition-based maintenance, as the check is performed based on the kilometers traveled and the condition of the component itself.
Periodic Preventive Maintenance (Cyclic)
Periodic preventive maintenance (or also cyclical maintenance) is a special type of maintenance based on predetermined cycles of use. Cyclic maintenance is a type of planned maintenance, i.e. which is carried out in accordance with the maintenance plan determined on a time basis. Unlike maintenance according to condition, in this case the decisive factor is the time of use of a particular machine or system, the number of trips or mileage. A simple but effective example is the fire extinguishers inside the building, which, due to compliance with regulations, must be inspected at the time intervals prescribed by law. But changing the car’s engine belt also belongs to that category, because a certain condition is created, the mileage traveled, with the aim of predicting the occurrence of a failure.
Other Types of Preventive Maintenance
However, among the various types of preventive maintenance there are others that we have not yet mentioned. Some of them are:
Statistical Preventive Maintenance: A type of maintenance planned based on statistical considerations relating to the duration and average life cycle of a component or machine. This type of maintenance, which partly belongs to those mentioned above, is often considered an integral part of periodic (or cyclical) maintenance since it is based on predetermined cycles of use.
Opportunistic Maintenance: Although this particular type of maintenance strategy is not necessarily part of preventive maintenance, the latter greatly favors its occurrence, because often, in cases of corrective maintenance, there is no time or real coordination to take advantage of the incident and the course of action of this type is ongoing. Therefore, it takes advantage of the period of planned shutdown or unavailability of the system to carry out inspections or overall maintenance interventions, in order to optimize times and ensure efficiency.
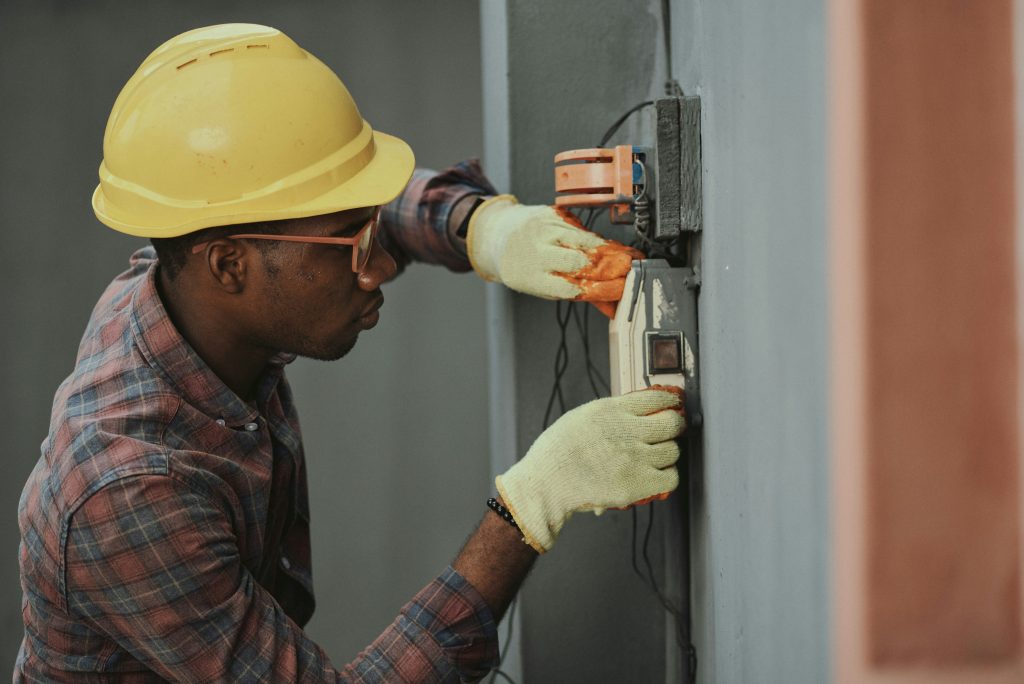
Preventive Maintenance Management Through Computerized Maintenance Management Software (CMMS)
The rapid evolution of today’s market forces all companies to actively engage in order to gain a competitive advantage over the competition. In this context, we have seen how preventive maintenance represents one of the fundamental aspects for achieving this goal.
One of the ways a company can improve the management of maintenance activities involves the use of software solutions that can involve and seamlessly connect the entire organization. For these reasons, more and more companies decide to introduce software solutions with advanced features.
Maintenance management software, commonly referred to as CMMS, an acronym for Computerized Maintenance Management Software, is a tool used by maintenance managers to manage their activities.
Unlike preventive maintenance management that is tracked through generic software, such as classic Excel, using maintenance management software provides maintenance teams with a large amount of notifications and information that is automatically generated when it is expected, thus facilitating the completion of assigned tasks. The above reports not only show updated information about the most problematic parts of the plant or machinery, but also allow you to measure the effectiveness of the operational teams and what to work on to improve the quality of interventions.
None of these goals can be achieved without the use of a maintenance software package.
Today, companies of all sizes, from the smallest ones composed of a few teams, to large multinationals with hundreds or thousands of maintenance workers, use some type of maintenance software. Generally, a CMMS is managed by a maintenance manager and technicians who have access to the system with progressively reduced authority depending on the level of responsibility.
Furthermore, CMMS or more simply maintenance management software is also used by senior management, who use reports generated by financial reporting systems to reduce maintenance costs, identify causes of accidents, measure productivity index and ensure compliance with applicable regulations.
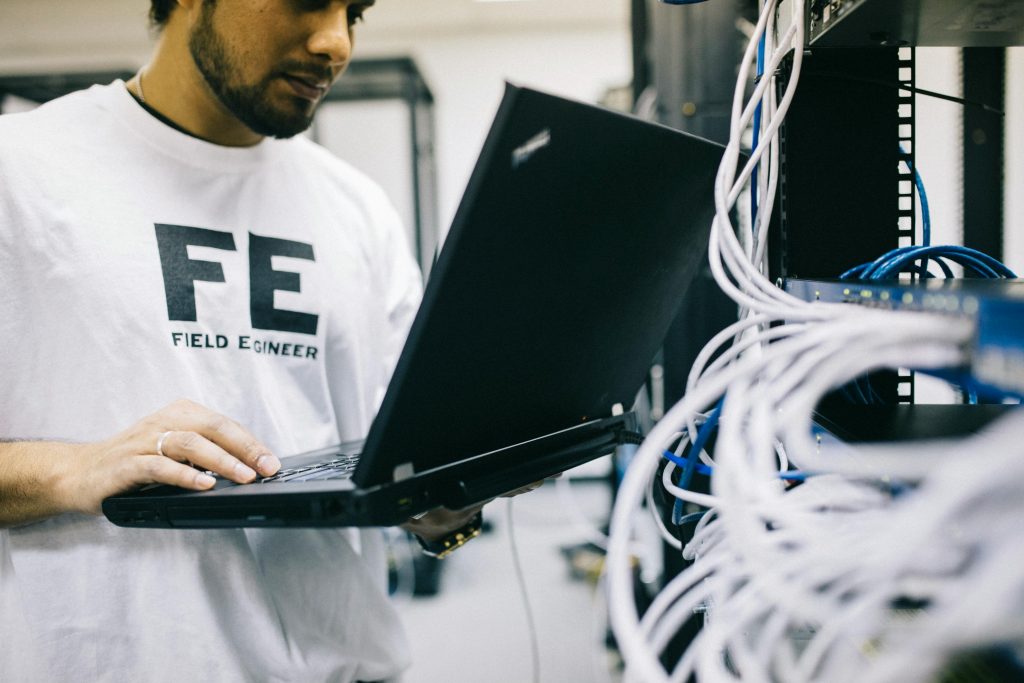
CMMS for Preventive Maintenance
A Computerized Maintenance Management System (CMMS) has the ability to carry out various functions that aid in the smooth execution of preventive maintenance tasks:
- With the help of CMMS software, users have the ability to schedule preventive maintenance tasks using predetermined intervals, whether it be time-based (such as monthly or quarterly) or usage-based (after a certain number of operating hours). It is possible to establish recurring maintenance schedules for either individual assets or groups of assets.
- The CMMS system allows users to allocate preventive maintenance assignments to designated maintenance technicians or teams. Assignments can be made considering factors such as skill levels, availability, workload, or geographic location, guaranteeing that tasks are carried out by the most suitable personnel.
- The generation of work orders is seamlessly facilitated by the CMMS system, which automatically creates them for scheduled preventive maintenance tasks. These work orders encompass comprehensive instructions, checklists, and specifications that guarantee uniformity and adherence to standards during the execution of maintenance activities.
- CMMS has the capability to automatically send alerts and notifications to maintenance staff when preventive maintenance tasks are approaching or past their due dates. These reminders can be received through email, SMS, or directly within the CMMS dashboard, ensuring that technicians are reminded to complete their scheduled maintenance activities.
- With the help of CMMS, users have the ability to meticulously document their preventive maintenance endeavors, encompassing the completion of tasks, observations made, and any challenges encountered along the way. This comprehensive documentation allows users to record crucial maintenance data, including the date and time of service, labor hours invested, parts utilized, and the overall condition of the equipment. This invaluable information can then be easily referenced and analyzed in the future.
- CMMS enables the tracking of asset history, providing a comprehensive record of all preventive maintenance conducted on each individual asset. Users have the ability to retrieve asset maintenance records, review previous maintenance tasks, and monitor maintenance patterns over time in order to evaluate the performance and dependability of the assets.
- As part of preventive maintenance, CMMS offers inspection checklists that can be customized to suit specific needs. These checklists allow users to establish inspection criteria, checklist items, and pass/fail criteria, ensuring that assets are thoroughly and consistently inspected.
- The integration of predictive maintenance is a feature available in certain advanced CMMS platforms. These platforms have the capability to connect with predictive maintenance technologies like IoT sensors and condition monitoring systems. By gathering and analyzing data in real-time from these sensors, the CMMS can anticipate equipment failures and initiate proactive preventive maintenance measures.
- CMMS provides reporting and analysis capabilities to evaluate the effectiveness of preventive maintenance. This includes generating reports and analytics on various performance metrics such as completion rates, adherence to schedules, reduction in downtime, and cost savings. By analyzing this data, users can pinpoint areas that require improvement, optimize maintenance strategies, and showcase the return on investment.
- CMMS has the capability to seamlessly integrate with maintenance parts inventory systems, guaranteeing the availability of essential parts and materials for preventive maintenance tasks. This integration allows users to effortlessly generate purchase orders or replenishment requests for the parts needed for scheduled maintenance activities.

The Advantages of CMMS for Preventive Maintenance
Organizations can benefit from various advantages when they choose to implement a Computerized Maintenance Management System (CMMS) for preventive maintenance.
- Through the practice of preventive maintenance, organizations can effectively identify and resolve potential problems before they escalate into expensive breakdowns or failures. By taking proactive measures to service equipment and address maintenance requirements, businesses can significantly reduce unplanned downtime and ensure seamless operational continuity.
- The longevity of assets can be prolonged through the implementation of regular preventive maintenance practices. By regularly inspecting, servicing, and repairing equipment, machinery, and facilities, organizations can enhance asset performance, minimize deterioration, and fully utilize the lifespan of their assets.
- One of the benefits of preventive maintenance is its ability to decrease maintenance expenses by minimizing the necessity for urgent repairs and replacements. By proactively addressing issues and preventing major breakdowns, businesses can avoid expensive periods of inactivity, repairs, and replacement costs, ultimately resulting in substantial savings in the long run.
- Regular maintenance and servicing of equipment through preventive measures significantly improves reliability and performance. By minimizing the likelihood of unforeseen malfunctions, operational dependability, productivity, and efficiency are all heightened.
- Creating a safer work environment is achieved through regular maintenance inspections and servicing, which play a vital role in identifying and resolving safety hazards and equipment problems. By implementing preventive maintenance measures, the potential for accidents, injuries, and occupational hazards caused by faulty equipment is significantly reduced.
- Maintaining compliance with regulations is a crucial aspect of organizational operations. Preventive maintenance plays a vital role in meeting regulatory requirements and adhering to industry standards for equipment safety and maintenance. Through thorough documentation of maintenance activities, inspections, and repairs, organizations can effectively showcase their commitment to compliance and establish a sense of accountability.
- Effective inventory management is crucial for organizations to efficiently handle spare parts, materials, and supplies needed for maintenance tasks. Through the implementation of preventive maintenance, organizations can accurately predict maintenance requirements and adjust stock levels accordingly. This proactive approach allows for optimized inventory management, minimizing the occurrence of stockouts and avoiding unnecessary costs associated with excess inventory.
- The implementation of preventive maintenance measures results in heightened accessibility of equipment, as it guarantees that assets are adequately maintained and ready for utilization whenever required. By strategically scheduling maintenance activities during planned periods of downtime and non-peak hours, organizations can effectively reduce operational disruptions and optimize the availability of their equipment.
- The implementation of preventive maintenance enables organizations to enhance their planning and scheduling of maintenance activities. Through the utilization of CMMS software, which automates maintenance scheduling, monitors asset status, and prioritizes tasks, organizations can achieve optimal allocation of resources, reduce idle time, and enhance overall maintenance efficiency.
- The implementation of preventive maintenance generates a wealth of valuable information and insights pertaining to the performance of equipment, maintenance patterns, and metrics of reliability. Through the analysis of this maintenance data, organizations can pinpoint areas for improvement, make informed decisions based on data, and continually enhance their strategies for preventive maintenance.
Conclusion
By utilizing a CMMS to incorporate preventive maintenance, organizations can reap a multitude of benefits. These include minimizing downtime, prolonging the lifespan of assets, saving costs, enhancing reliability and safety, ensuring compliance with regulations, optimizing inventory management, maximizing equipment availability, improving planning and scheduling, and making informed decisions based on data. Through proactive maintenance management, businesses can achieve heightened efficiency, productivity, and a competitive edge in their operations.