Get a Free WorkTrek Demo
Let's show you how WorkTrek can help you optimize your maintenance operation.
Try for freeKey Takeaways
- Neglecting building maintenance has led to fatal collapses in the U.S.
- India’s high-altitude maintenance centers for armored vehicles keep equipment battle-ready in extreme conditions.
- Honda Racing Corporation is opening a UK facility for F1 engine maintenance.
- Hitachi’s AI-powered railway maintenance reduces delays by 20% in Europe.
Maintenance practices vary widely across different industries worldwide.
In some places, neglect has led to tragic building collapses, while in others, cutting-edge AI and real-time monitoring are keeping trains and planes safer than ever.
By exploring these six stories, you will discover practical ideas to apply to your maintenance operations, making them more proactive, efficient, and safe.
Poor Building Maintenance Keeps Causing Deaths in the U.S.
The U.S. has faced some devastating building collapses in recent years, a tragic reminder of what happens when building maintenance is neglected.
Take the Champlain Towers South collapse in Florida in 2021, for example, where 98 lives were lost in a disaster.
Experts believe this disaster could have been prevented.
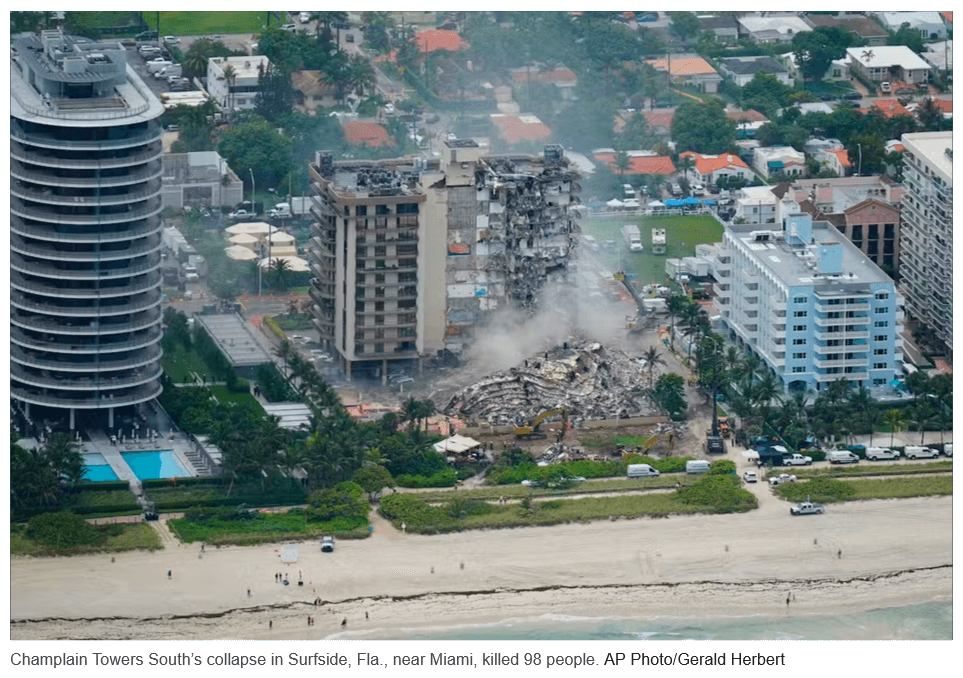
Back in 2018, an inspection report had already flagged severe structural issues in Champlain Towers.
Shockingly, this report went unread and unaddressed.
This is not an isolated case.
Older buildings often need proper inspections or repairs nationwide, particularly in cities with aging infrastructure like New York.
For many buildings, deferred maintenance worsens small, manageable issues until they become serious, even life-threatening risks.
Real estate attorney Janet Bozeman with Williams Teusink, LLC, explains why it comes to this:
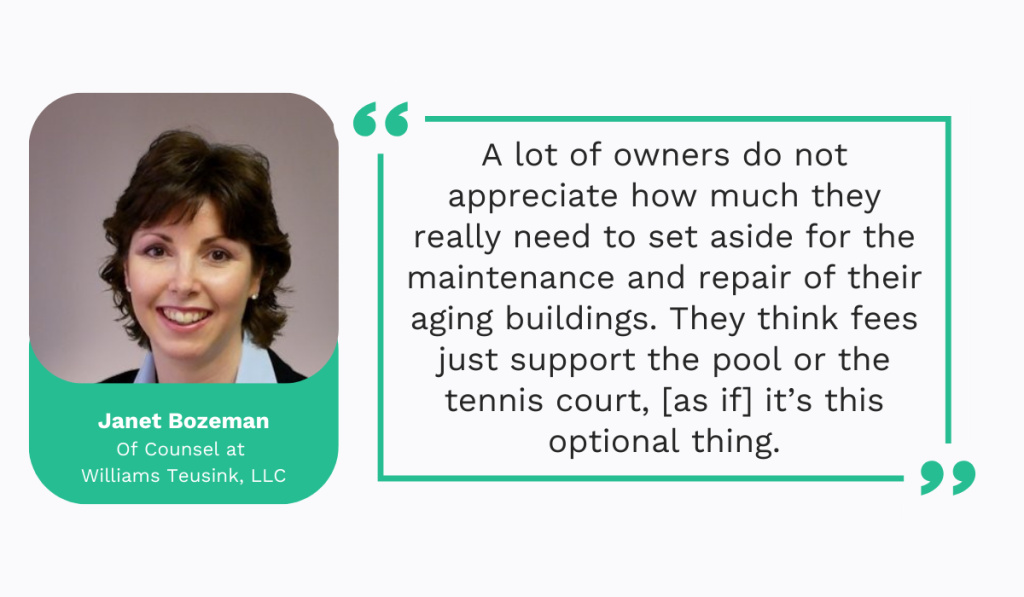
In other words, some property owners still don’t see the critical need to invest in upkeep for aging buildings, even as their structures face mounting stress over time.
However, preventive maintenance is essential, especially for buildings nearing or exceeding 100 years.
While a few areas, such as Florida and Jersey City, have introduced stricter inspection rules to address this gap, many regions still lack these protections, leaving maintenance managers as the primary (and sometimes only) line of defense.
Regardless of local policies, maintenance teams can advocate for regular assessments and repairs to make a tangible difference.
With today’s tools, like Computerized Maintenance Management Systems (CMMS), spotting and addressing issues early is more achievable than ever.
Some solutions, like our WorkTrek, even allow tenants to submit requests when they see signs of trouble, such as water intrusion, leaks, or structural cracks.
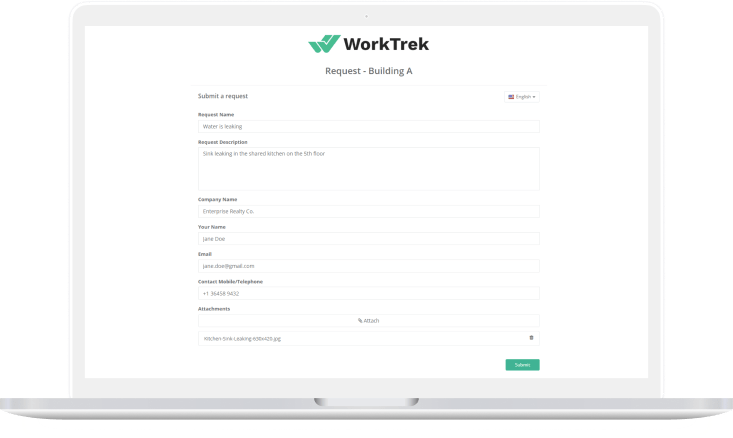
In this new era of maintenance technology, we have powerful resources to prevent minor issues from escalating into deadly hazards.
By staying vigilant and embracing them, maintenance managers can champion the safety and integrity of their buildings and help avoid another preventable tragedy.
Honda Racing Corporation UK Set to Perform Post-Race Maintenance on Honda-Built F1 Power Units
The high-stakes world of Formula 1 (F1) racing is as much about precision maintenance as it is about speed.
Engines or power units (PUs) in F1 cars must perform flawlessly under extreme conditions, which requires careful, detailed upkeep after every race.
Honda Racing Corporation (HRC) is taking a bold new step in this area by launching a UK-based company dedicated solely to the post-race maintenance of its F1 power units.
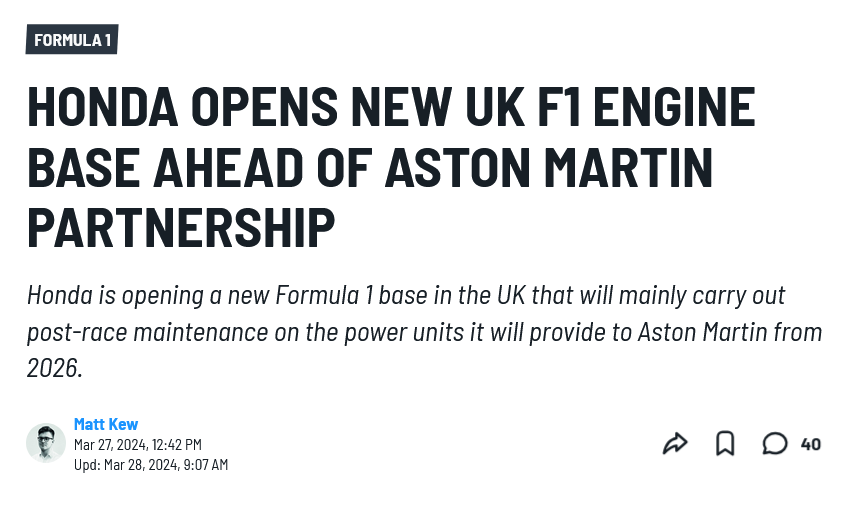
This shift represents a new, permanent approach for Honda.
Previously, HRC’s racing efforts were project-based, with teams assembled for specific events and disbanded.
Now, as HRC President Koji Watanabe explains, Honda’s operations are becoming a sustained, long-term commitment:
Until now, our activities have been projects, gathering people and money, disbanding when the project was over, and repeating. However, going forward, we will be responsible for all the racing company’s activities.
This decision to invest in a permanent facility is also strategic.
After Honda’s 2021 exit from F1, their supply role for Red Bull continued—thanks, partly , to Max Verstappen’s remarkable World Drivers’ title win that year.
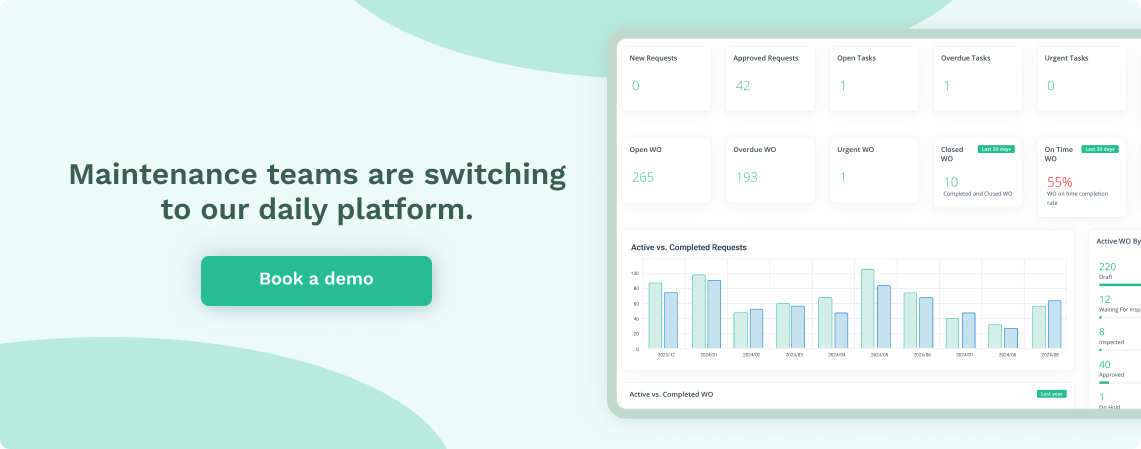
Honda’s official return in 2026 will come with the shift to new F1 power unit regulations, which include a 50:50 split between hybrid energy and the traditional 1.6-liter turbo engine, along with the complete removal of the Motor Generator Unit–Heat (MGU-H).
This evolution offers Honda a unique opportunity to develop advanced hybrid technology directly applicable to its road cars.
Moreover, the new regulations focused on a more sustainable F1 align well with Honda’s goals of advancing carbon-neutral fuels and high-efficiency motors and batteries.
Watanabe emphasized they have the budget for that::
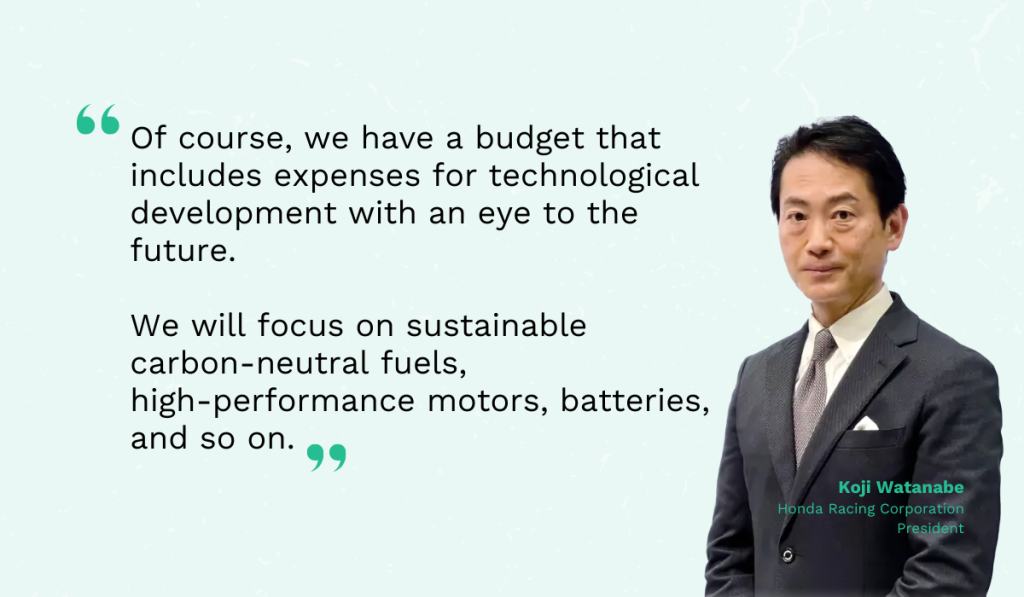
Finally, why the UK?
Establishing a base here supports Honda’s partnership with Aston Martin, set to begin in 2026.
Additionally, locating operations in the UK will optimize logistics for European races.
India Sets Up Armored Vehicle Maintenance and Repair Facilities
In high-stakes defense operations, reliable maintenance is critical—especially when vehicles are deployed in some of the harshest conditions on earth.
The Indian Army has set a new standard by establishing two high-altitude maintenance facilities for armored vehicles in Eastern Ladakh, near the China border, at elevations over 14,500 feet.
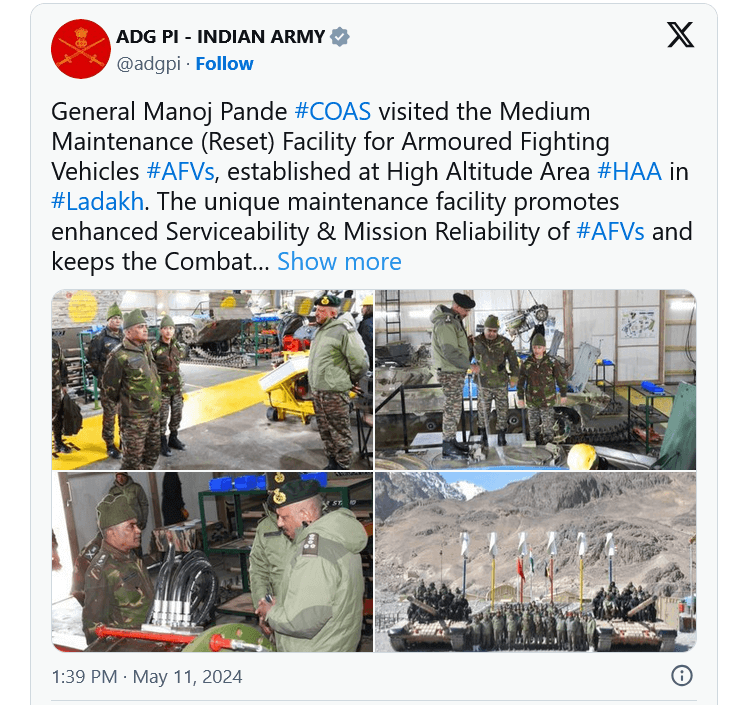
This region, along the Line of Actual Control (LAC), is recognized as the world’s highest battlefield for tanks and infantry combat vehicles.
These new maintenance facilities, located at Nyoma and near KM-148 on the DS-DBO Road, ensure that India’s armored fleet remains operational in this extreme environment, where temperatures can plummet to -40°C and oxygen levels are low.
Operating in such conditions presents unique maintenance challenges.
At these altitudes, critical systems like firing mechanisms, hydraulics, and engines are under tremendous strain from the cold and thin air, leading to frequent wear and performance issues.
As Indian Army officials explain:
However, by setting up maintenance facilities so close to the front line, the Indian Army can avoid the lengthy and challenging task of transporting vehicles back to lower altitudes for repairs.
With that, India has cut downtime, improved battle readiness, and ensured its fleet can respond swiftly to any situation.
This case proves that sometimes, a tailored approach to maintenance infrastructure is the best way to support demanding operations.
Romania Launches First HIMARS Maintenance Center in Europe
Romania recently made a significant move in European defense by launching Europe’s first High Mobility Artillery Rocket System (HIMARS) maintenance center in Bacău.
This center, developed through a strategic partnership between Romania’s Aerostar S.A. and U.S. defense leader Lockheed Martin, will be a critical hub for maintaining Romania’s HIMARS artillery systems.
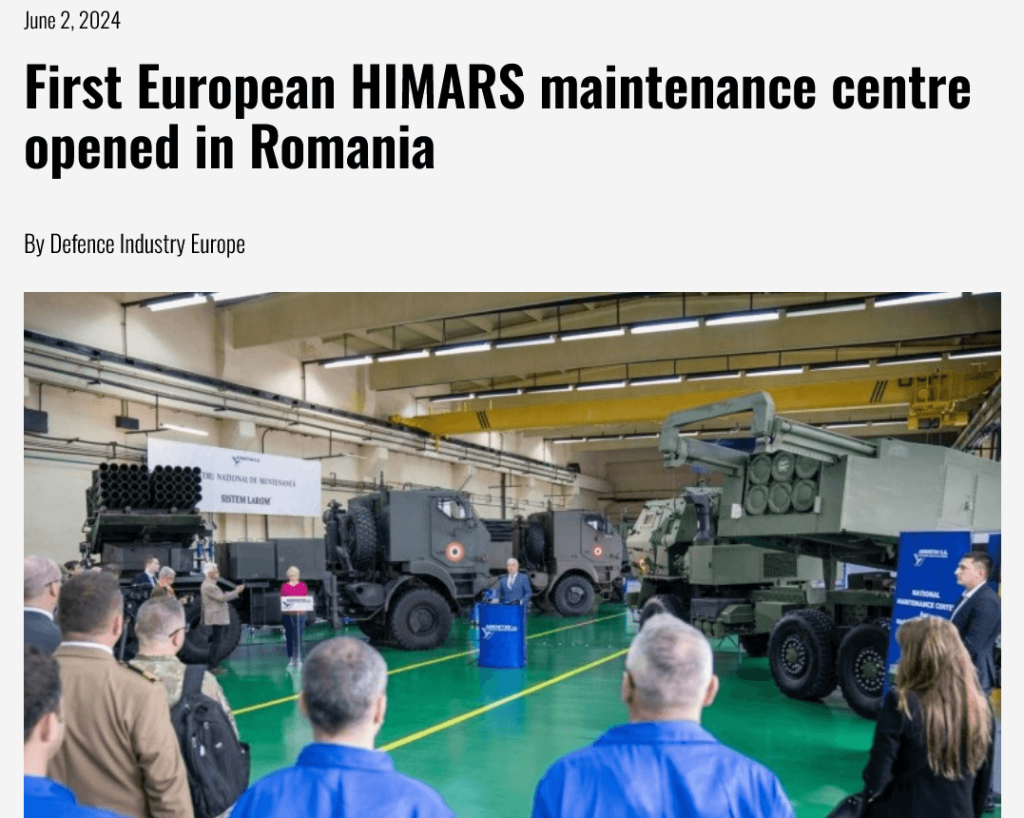
Why is this development noteworthy?
HIMARS is a highly mobile, long-range rocket system designed to deliver precise strikes quickly, making it essential for modern defense strategies.
For Romania, which sits on NATO’s eastern flank near potential hotspots, keeping HIMARS operational is vital for a responsive, ready defense force.
HIMARS systems were previously sent overseas for repairs, which meant costly transport, long downtimes, and delayed readiness.
By maintaining them locally, Romania can drastically reduce these costs and swiftly get artillery systems back into action.
Additionally, the maintenance center enhances Romania’s role in NATO’s defense capabilities.
This facility can also support HIMARS maintenance for neighboring NATO allies, helping ensure that critical artillery systems are always combat-ready across the region, as Angel Tîlvăr, Romanian Minister of National Defense, pointed out:
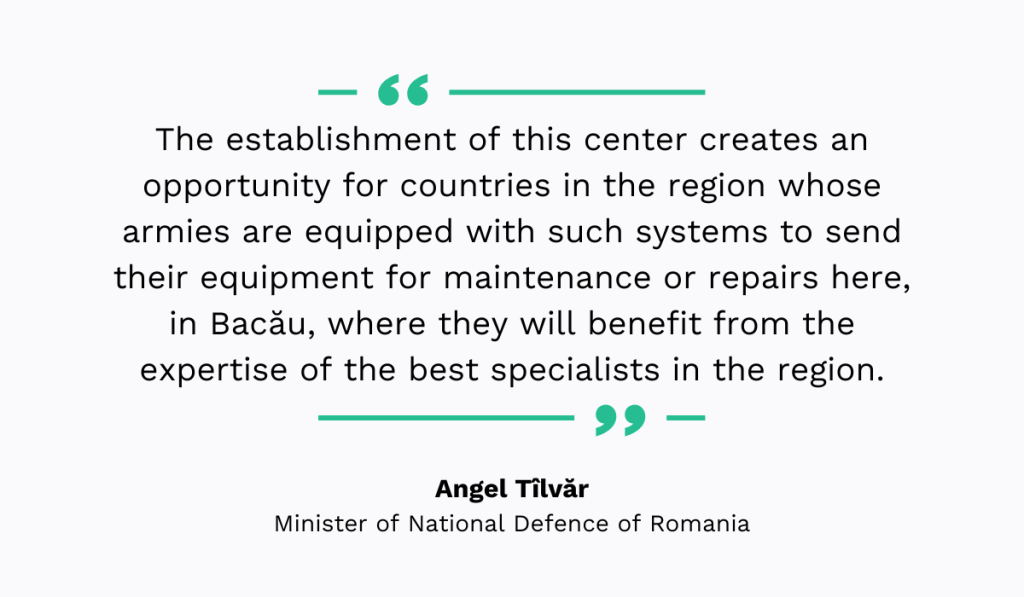
Beyond its defense benefits, the center brings significant economic impact to Bacău.
This facility is expected to create approximately 2,000 jobs, including roles for skilled technicians and engineers.
This boosts the local economy and fosters a skilled workforce in the high-tech defense sector.
Rolls-Royce Holdings Uses Digital Twin Technology for Engine Maintenance
Rolls-Royce Holdings plc, a British multinational aerospace and defense company, is transforming aerospace maintenance with digital twin technology.
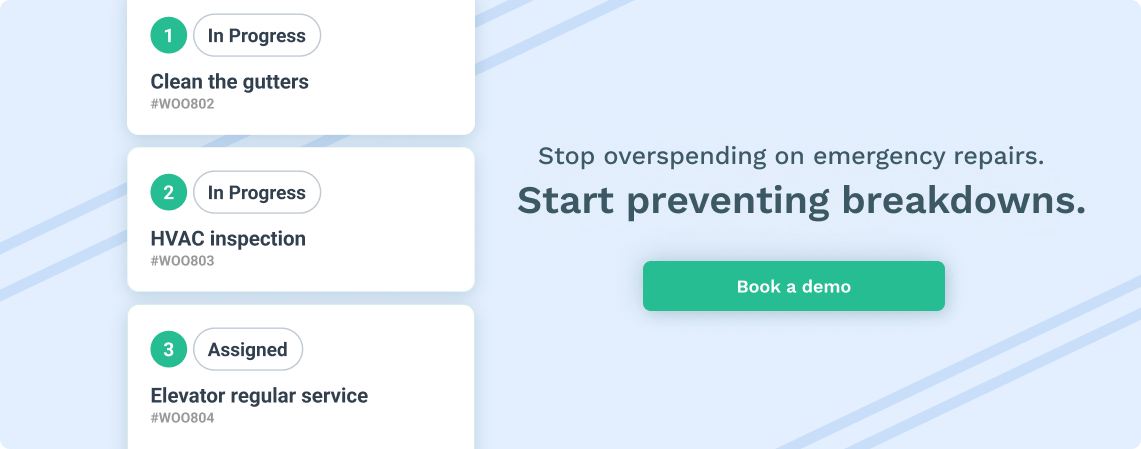
This groundbreaking approach creates virtual replicas—or “twins”—of the engines.
These digital twins allow Rolls-Royce to monitor engine performance in real-time, spotting potential issues and predicting maintenance needs before they become critical.
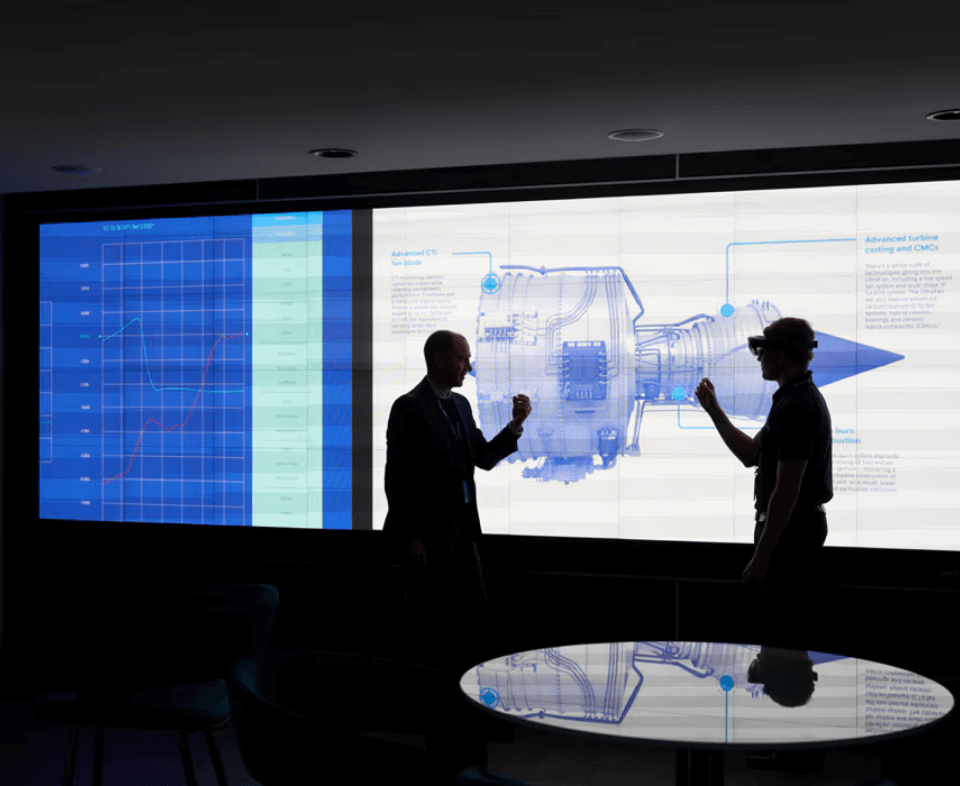
This reduces unexpected breakdowns, optimizes maintenance schedules, and extends engine lifespan.
Rolls-Royce explains the process:
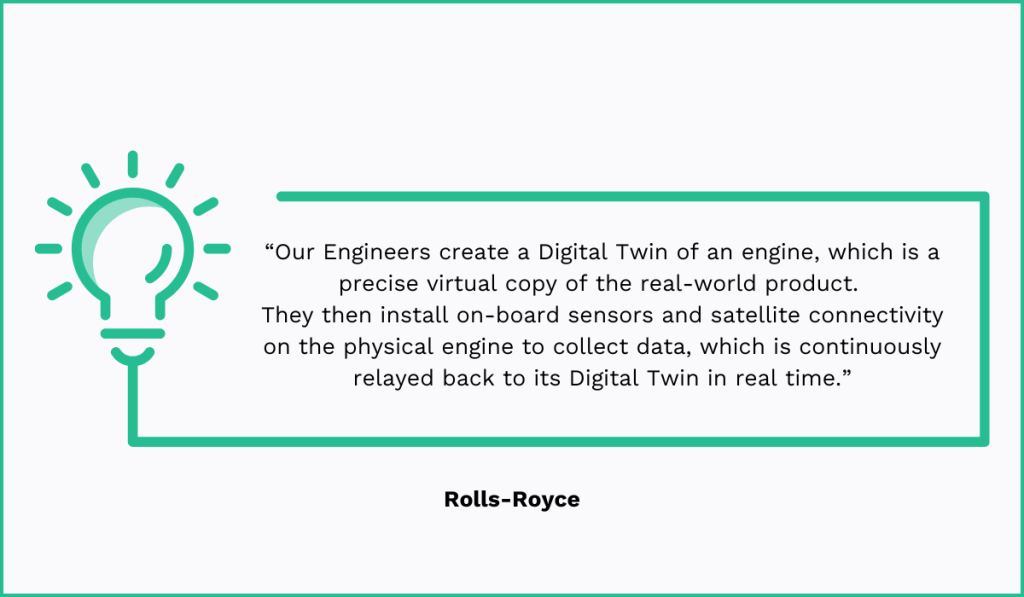
The virtual twin mirrors the real engine’s operation, providing data to predict when maintenance is needed.
This enables proactive, preventive maintenance, reducing aircraft downtime and enhancing reliability.
In addition to aviation, Rolls-Royce is expanding this technology to rail systems and marine power.
Partnering with Singapore’s Defence Science and Technology Agency, they’re also using machine vision tools to inspect hard-to-reach parts, showcasing the versatility and potential of digital twins.
As Industry 4.0 and data-driven maintenance evolve, digital twins offer a forward-looking solution for predictive maintenance—an essential tool to stay ahead in asset management.
Hitachi and Nvidia Launch AI-Powered Railway Maintenance Services
Hitachi Rail, a global leader in transportation technology, has teamed up with Nvidia, an American tech company known for its advanced semiconductor and AI technologies, to bring AI-powered maintenance to railways.
Together, they’ve turned Hitachi’s HMAX into an innovative digital maintenance system that uses AI to keep trains running smoothly, reliably, and safely.
How does it work?
HMAX uses sensors and cameras installed on trains and infrastructure to continuously monitor vibration, temperature, and other signals of wear and tear.
With Nvidia’s powerful AI processing, this data is analyzed in real time directly on the trains, enabling early detection of potential issues—well before they escalate into costly breakdowns or delays.
For maintenance managers, this is a game-changer.
Traditional maintenance relies on periodic inspections, typically conducted monthly or during off-hours.
In contrast, HMAX’s continuous monitoring provides an up-to-date view of each train’s condition, delivering highly accurate, timely insights.
This AI-driven system also addresses the current labor shortages in railway maintenance.
Namely, manual inspections require specialized equipment and skilled workers, who are increasingly scarce.
However, by automating frequent inspections, HMAX fills these gaps, ensuring trains remain in top condition with minimal manual intervention, as a Hitachi Rail’s representative explains:
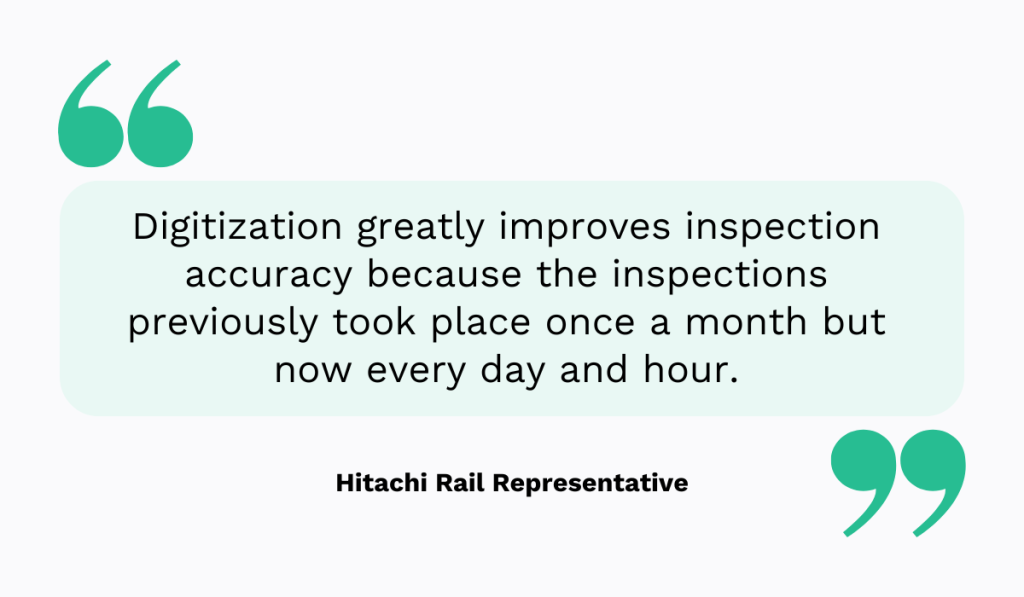
The impact is evident: since HMAX was deployed across approximately 8,000 train cars in Europe, delays—including maintenance-related—have dropped by up to 20%.
This efficiency boost shows how AI can solve real-world challenges in railway operations, making services smoother and safer for passengers and operators.
Conclusion
These six global developments reveal more than just new maintenance trends—they underscore the importance of staying proactive, adaptive, and vigilant.
Each example highlights a different aspect of the industry: the life-saving potential of structural monitoring, the logistical advantages of nearby maintenance facilities, and the efficiency boosts of AI and predictive analytics.
Hopefully, you will use what you learned today to strengthen safety, reduce downtime, and enhance your operations, regardless of your industry.