Get a Free WorkTrek Demo
Let's show you how WorkTrek can help you optimize your maintenance operation.
Try for freeTo effectively plan maintenance, you need more than just a simple calendar.
Successful maintenance planning requires a clear overview of your assets, inventory, technician availability, maintenance history, and the costs and time spent on past tasks.
That’s where the right software makes all the difference—consolidating these details into one place, giving you the insights you need to plan smarter and faster.
Today, we’ll explore seven top maintenance planning tools, starting with WorkTrek, our CMMS.
WorkTrek
WorkTrek brings all your maintenance data into one easy-to-access platform, making it simple to plan and manage tasks.
It gives you a complete asset list with key details like location, warranty information, maintenance history, and expenses.
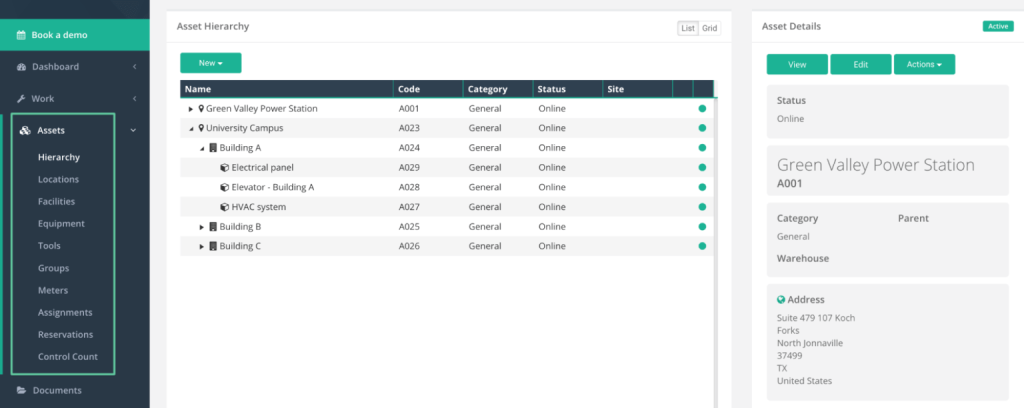
It also provides custom fields for users to add information they deem important.
With all this data in one place, it’s easier to identify which assets need maintenance, when they need it, and how much you’ll need to budget for it.
But that’s not all.
WorkTrek also lets you track assets over time using meter readings, such as working hours or mileage.
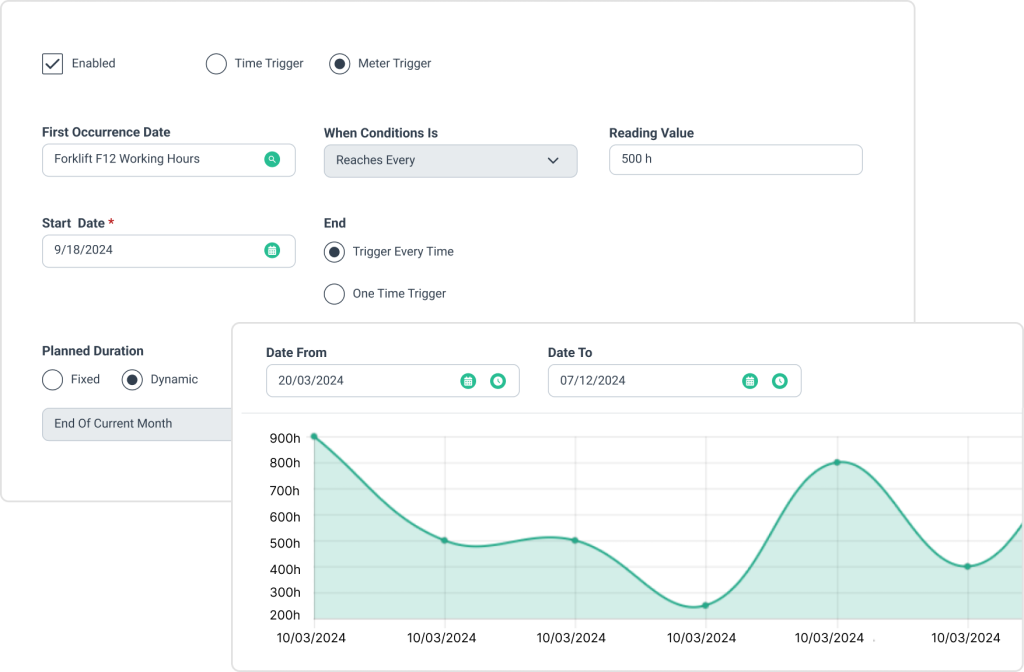
This feature helps you stay ahead by planning maintenance tasks before problems occur.
When planning different types of maintenance, WorkTrek gives you plenty of flexibility.
You can plan and schedule:
- Corrective maintenance
- Preventive maintenance
- Predictive maintenance
You can even plan additional tasks, like cleaning or safety inspections, and customize them to fit your needs.
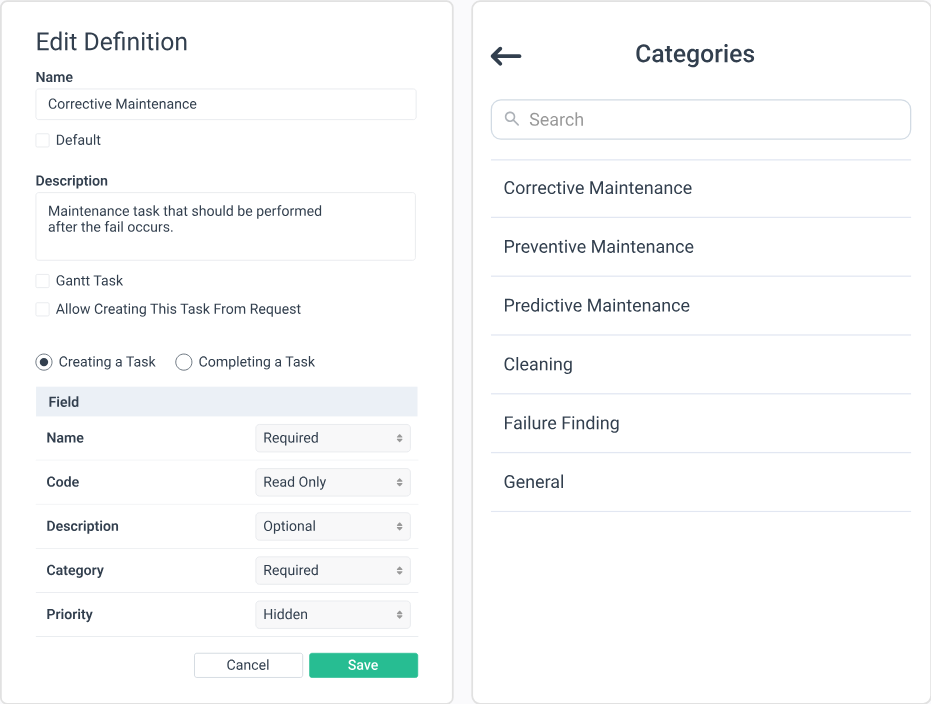
What sets WorkTrek apart is how detailed you can get with each work order.
You can break tasks into smaller steps and include checklists to ensure technicians complete everything by the book.
Plus, you can add labor hours and parts to each work order.
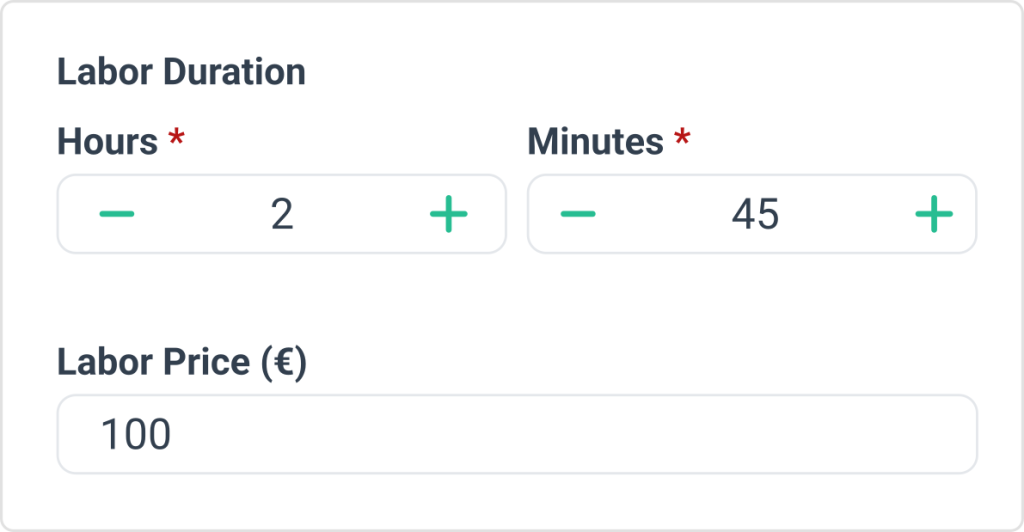
This way, you’ll always know the time and cost involved in a task, which is crucial for setting priorities and managing resources effectively, especially for future maintenance planning.
Planning all these tasks is incredibly easy, thanks to WorkTrek’s intuitive, calendar-based task view.
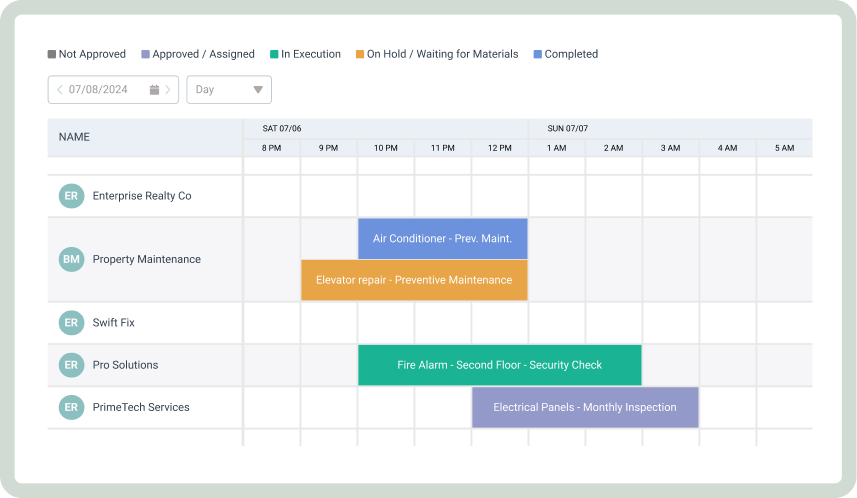
This tool helps you assign tasks, allocate resources, and see what’s coming up.
Another feature you’ll appreciate for better maintenance planning is parts and inventory management.
Spare parts tracking is a breeze in WorkTrek, with real-time updates that notify you when inventory levels run low.

This means you’ll always know when to reorder parts, helping you avoid delays and keep maintenance on schedule.
For on-the-go planning, the WorkTrek mobile app allows you to update schedules, assign tasks, and access asset information from anywhere.
Users consistently highlight the convenience of having all their data in one place, making WorkTrek a go-to solution for streamlined maintenance planning.
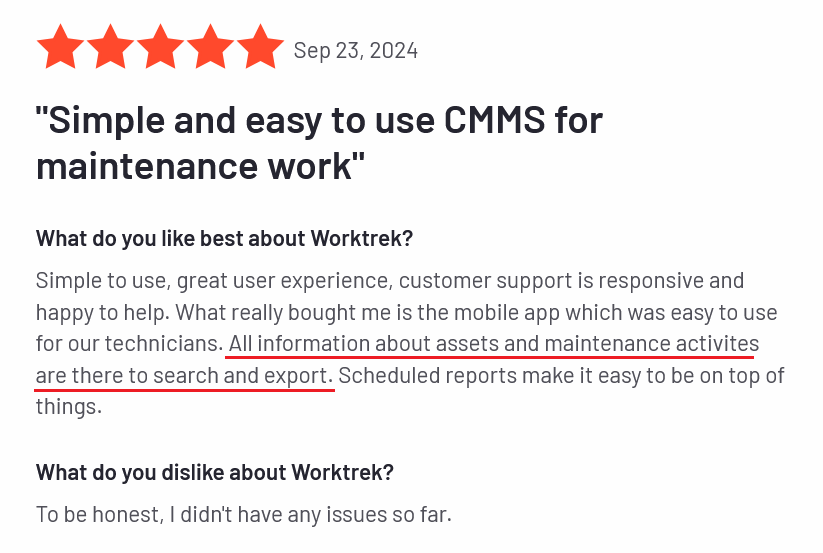
Pricing starts at $29 per user per month for the Starter Plan and $49 per user per month for the Professional Plan.
Custom pricing is also available if you need tailored solutions.
If your goal is to simplify maintenance workflows and make planning easier, WorkTrek might be the perfect fit.
So, book a demo or contact us to learn more.
IBM Maximo
IBM Maximo is an enterprise asset management (EAM) system built for large-scale enterprises with extensive and complex maintenance needs.
Leveraging generative AI, advanced analytics, and the Internet of Things (IoT), it offers a range of powerful features for maintenance planning.
Some of its standout capabilities include:
- AI-powered predictive maintenance planning
- Multi-site planning and resource optimization
- Integrated IoT connectivity
A particularly useful feature for maintenance planning is the ability to view asset health scores, as in the image below:
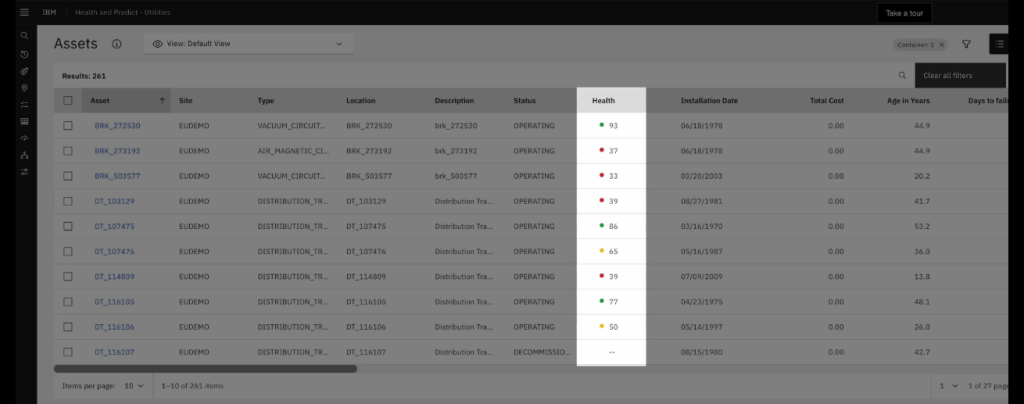
It shows you which assets are in the worst condition so you can prioritize their maintenance.
You can issue a work order directly from the list with just one click, streamlining the entire process.
Another useful tool is visual inspection.
With AI and mobile devices, you can check conditions on-site or in the field and spot problems that might not be visible otherwise.
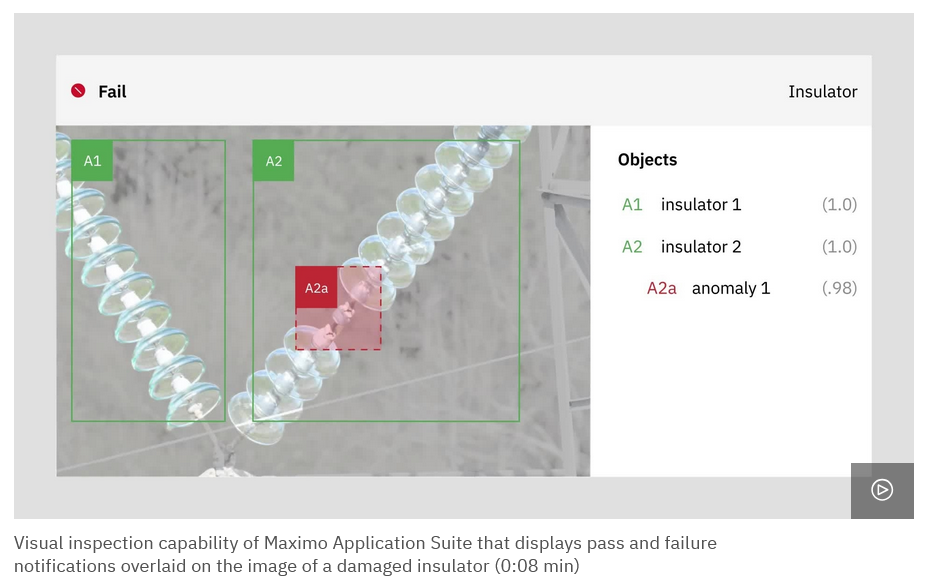
This helps you plan maintenance based on actual conditions, not guesswork.
Maximo also offers features like:
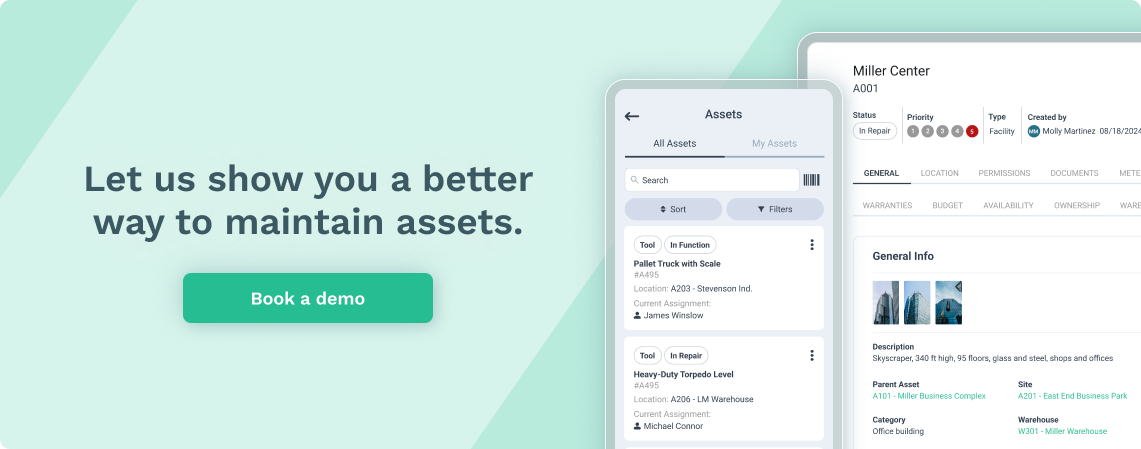
- Asset lifecycle management
- Energy optimization tools
- Risk analysis
It’s built to handle complex operations, making it a good fit for companies with multiple locations.
That said, it’s not the easiest software to use. Many users say it takes time to learn because it’s so feature-packed.
In a Reddit thread, many confirmed that while the software is powerful, its usability can be daunting.
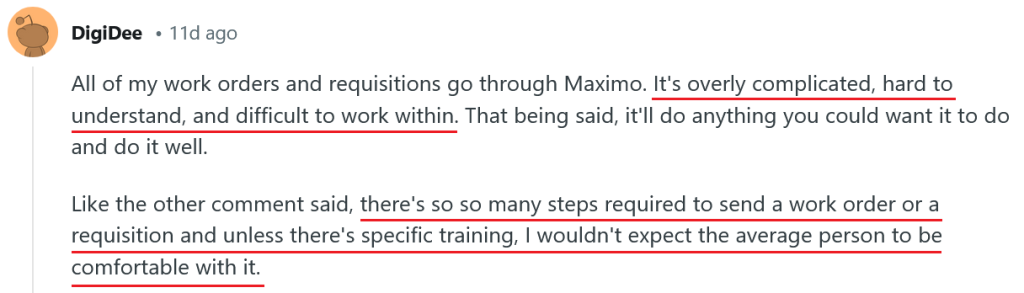
Maximo is not for a small business. It simply costs too much to implement it and can take years to set up.
From more specific drawbacks, one user mentions the difficulty in tracking time and part costs—a much simpler feature in tools like WorkTrek, as we explained above.
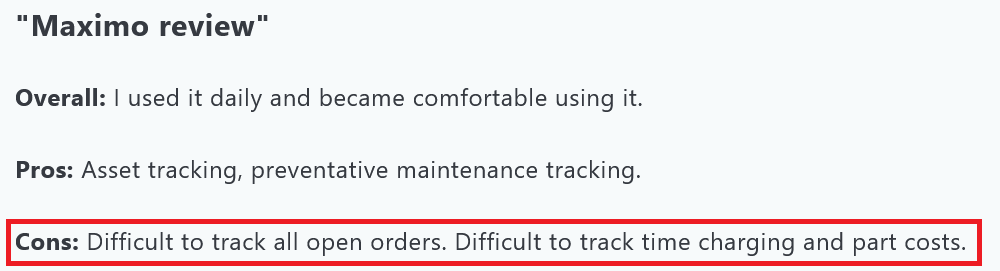
Another consideration is pricing—while no pricing details are available on the website (except for the price estimator), Maximo is clearly geared toward large enterprises rather than smaller businesses.
However, a 14-day free trial is offered for those who want to explore its capabilities.
Fiix
Fiix is a CMMS built for small to mid-sized businesses wanting to control their maintenance planning.
Similar to WorkTrek, Fiix lets you have all your asset data in one place from where you can easily plan and schedule maintenance.
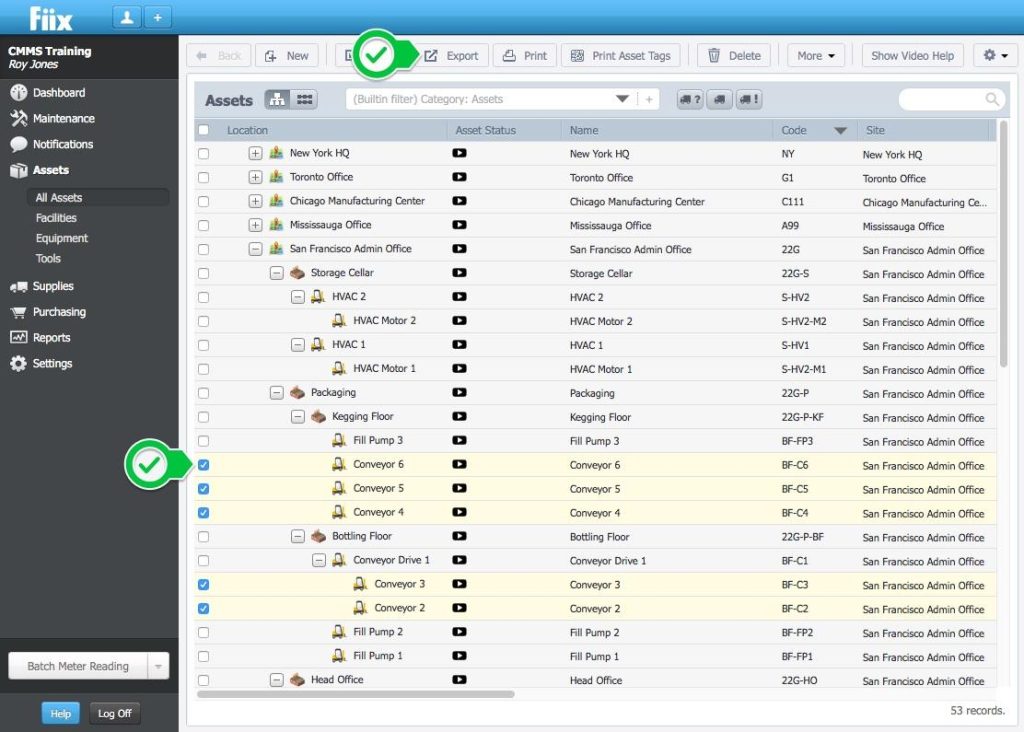
Planning preventive maintenance is easy with automated scheduling based on date and time, meter readings, or event and alarm-based triggers.
Moreover, Fiix provides insights to help you continuously improve your planning.
Its asset insights dashboard monitors where you’re spending extra time or money and alerts you if something needs attention, allowing you to act before downtime occurs.
The work order insights report, for example, lets you analyze past tasks to identify patterns and avoid recurring problems.
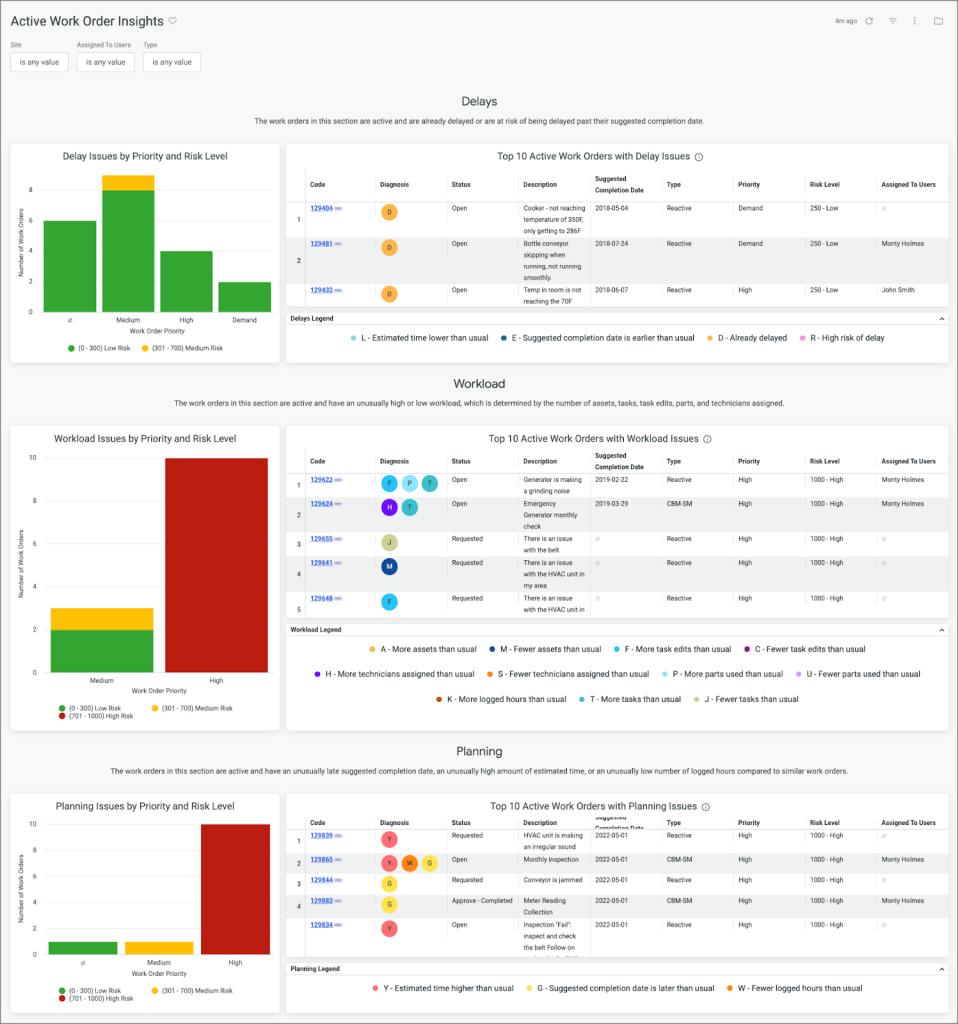
Spare parts management is another strong point.
Fiix, like WorkTrek, lets you set minimum quantities for parts and sends alerts when supplies run low.
Additionally, Fiix has a parts forecaster tool recommending which parts to reorder and when, helping you avoid shortages and overstocking.
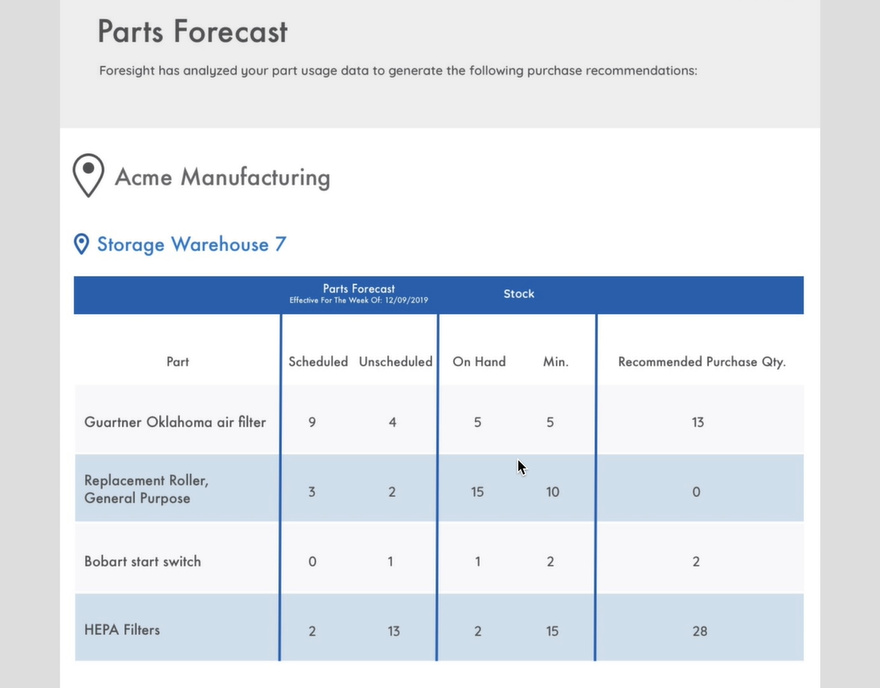
You can track up to 25 parts for precise planning without digging through endless data.
While Fiix offers dashboards and automation to monitor key maintenance metrics, many users note that its reporting capabilities are not as robust as they would like.
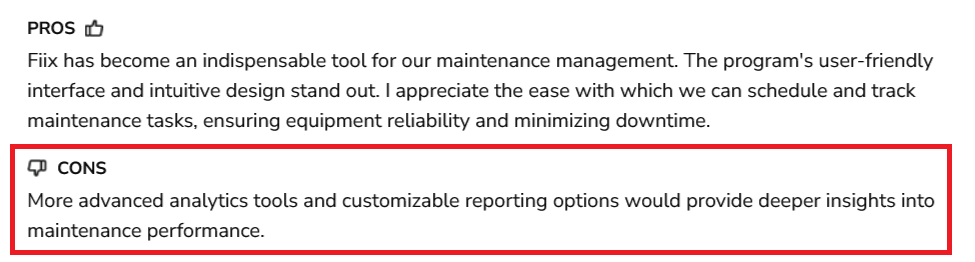
This could pose challenges for teams that depend on detailed data to make informed decisions and is something to keep in mind if reporting is a priority for your team.
Fiix’s free plan works well for teams new to CMMS tools, but its 25-task limit on preventive maintenance may be too limited for businesses with greater needs.
Teams looking for more flexibility might need to consider paid plans, which start at $45 per user per month.
The Professional plan, which includes advanced AI insights, costs $75 per user per month.
If you’re curious, you can take a free tour to see how Fiix works.
eMaint
eMaint offers both CMMS and EAM solutions as two different products.
Its CMMS comes with a range of features, making it a solid choice for businesses looking to streamline maintenance planning across multiple worksites.
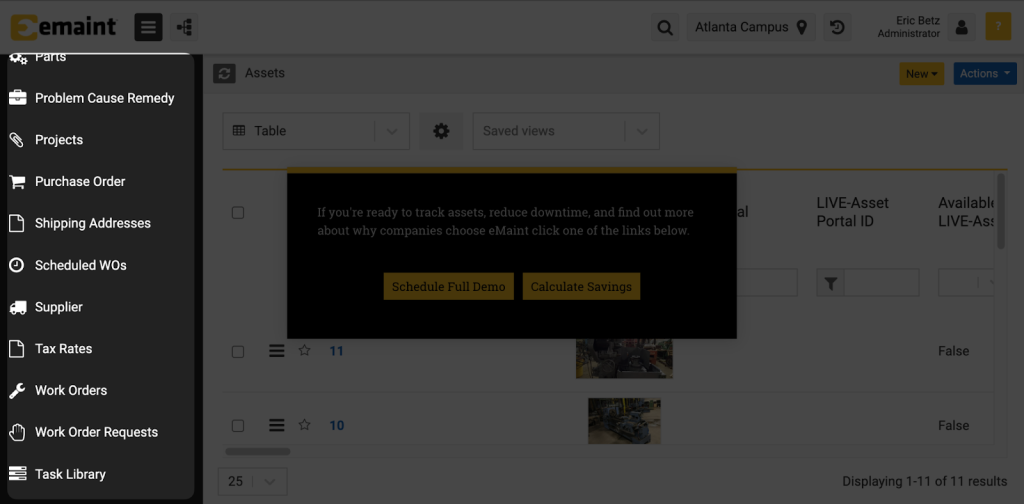
One of eMaint’s key strengths is its drag-and-drop scheduling interface, simplifying planning maintenance tasks.
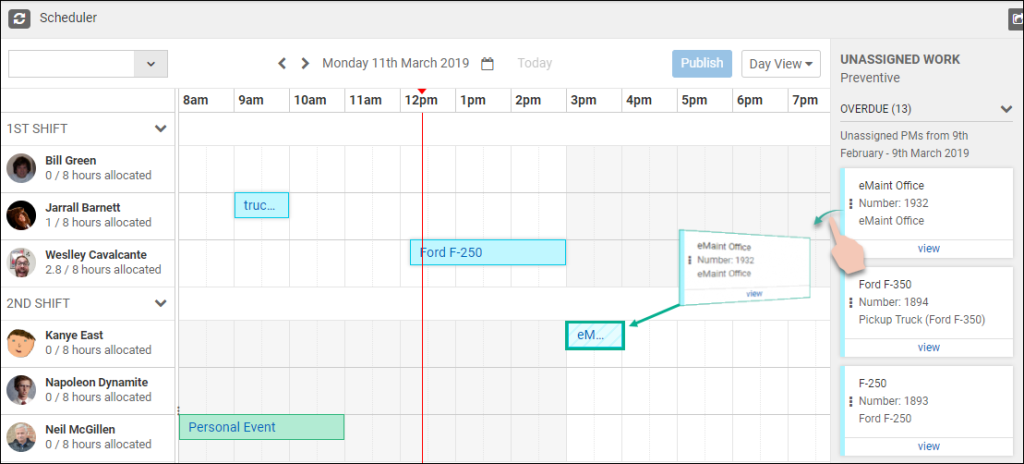
While all work order types are visible for tracking, this feature currently allows only preventive maintenance tasks to be directly scheduled, although updates are in progress to enhance this functionality.
The system also supports detailed maintenance logs and work order tracking.
It captures critical information, such as equipment history, work type, priority levels, and even different cost categories:
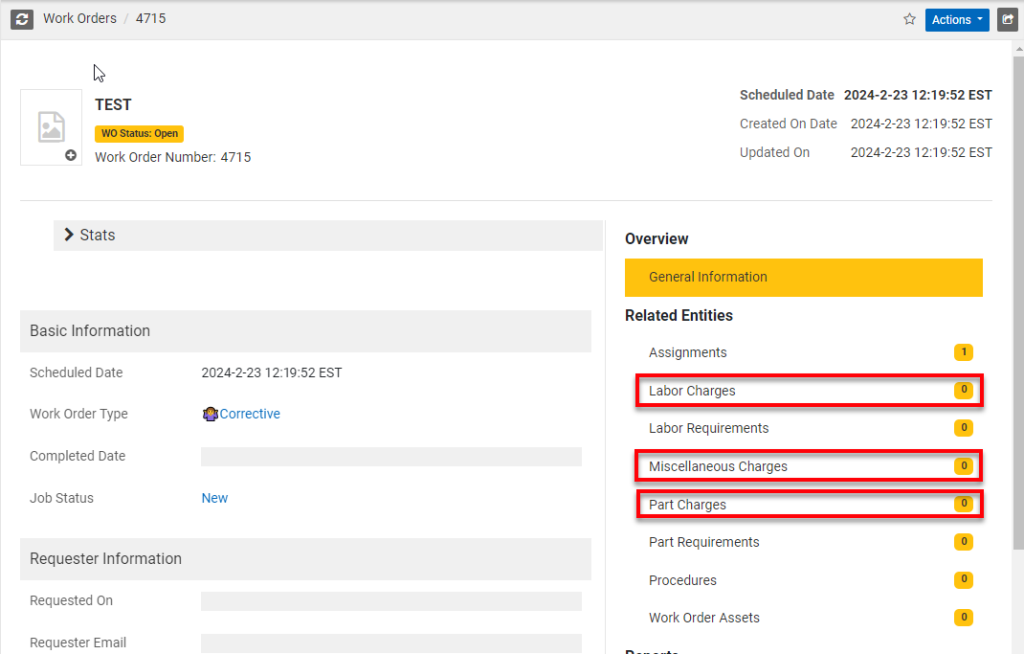
This data can help you analyze past tasks and improve future maintenance planning by identifying patterns, avoiding repeated issues, and refining resource allocation.
It’s also important to mention that eMaint integrates with asset monitoring tools like Fluke 3563 Analysis Vibration Sensors, enabling data-driven planning.
These sensors provide real-time health insights and allow you to monitor assets and predict faults or failures.
You can set alarms to trigger based on vibration levels or specific signatures. This gives you an early warning about potential problems and enough time to plan maintenance.
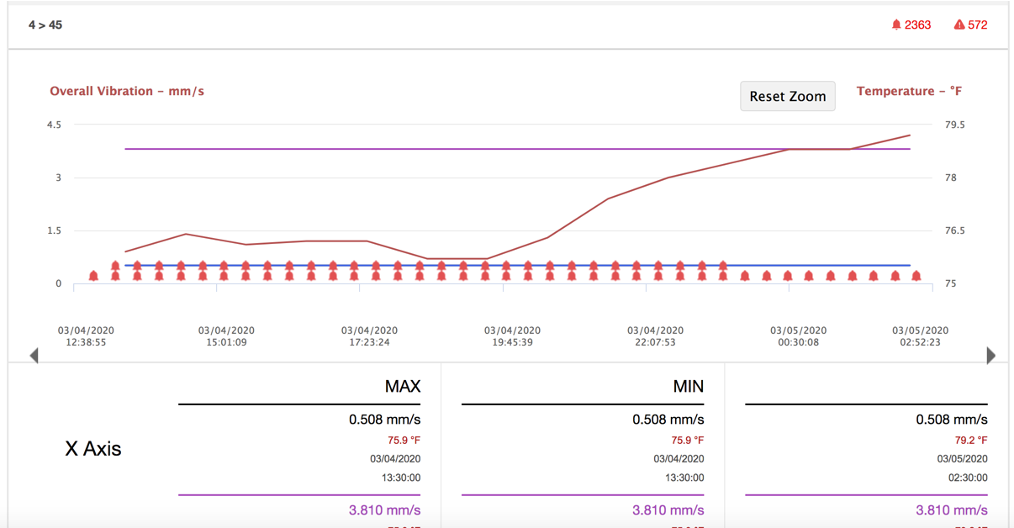
In addition to its planning tools, eMaint offers features such as:
- Asset history tracking
- Inventory management
- Reporting and analytics
For example, one user shared their experience with the system on Reddit, highlighting how it improved their ability to track MRO inventory.

Despite its strengths, eMaint does have some downsides.
Users have noted that it lacks a dedicated mobile app, though it offers mobile functionality.
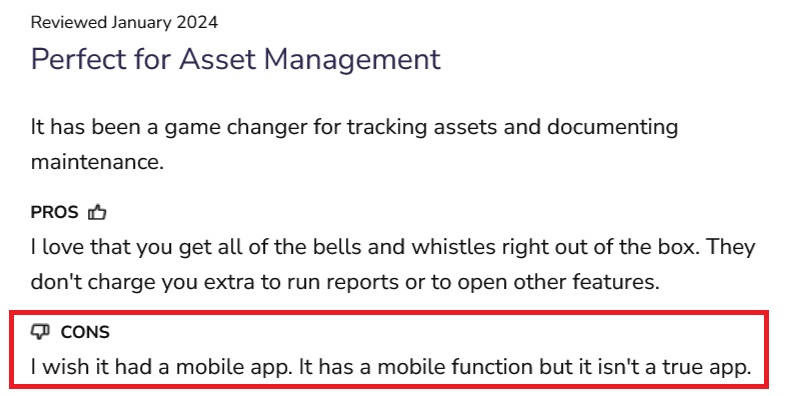
The lack of a dedicated mobile app in eMaint can disadvantage field teams as those accustomed to app-based solutions like UpKeep may find it less intuitive.
This could affect efficiency, particularly for technicians needing quick, on-the-go updates.
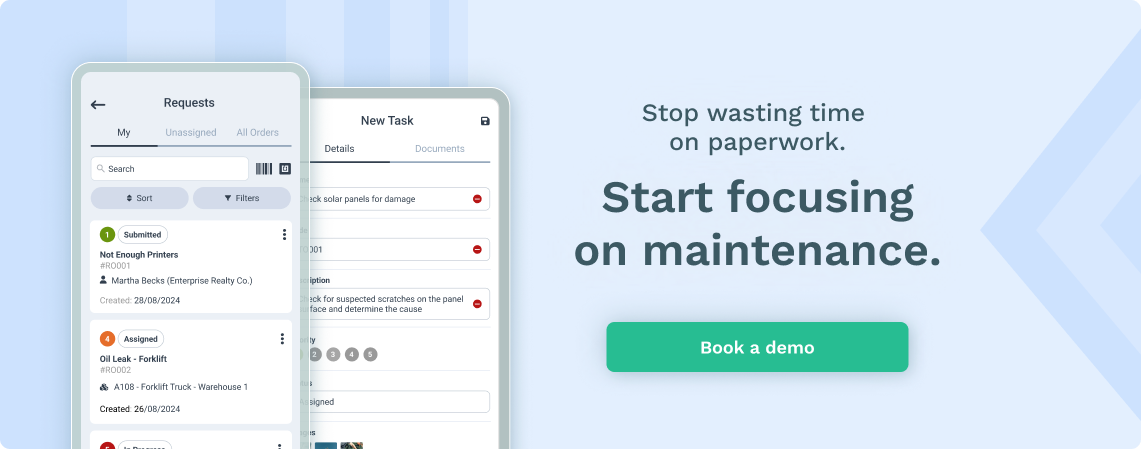
The system can also feel clunky, with a high learning curve for setup and modifications, making it less user-friendly for those new to CMMS tools.
To address this, eMaint provides training resources and customer support to help teams adapt quickly to the system’s capabilities.
Pricing starts at $69 per user per month, with a minimum of three users required.
Advanced features are available in higher-tier Pro and Enterprise plans.
If you want to explore eMaint further, a free demo is available.
UpKeep
UpKeep is a mobile-first CMMS built for maintenance teams in the field and small—to medium-sized businesses that need flexible and efficient solutions.
Its real-time mobile scheduling allows users to create, assign, and adjust maintenance tasks directly from their smartphones, ensuring tasks are completed on time.
The desktop version provides an easy-to-use overview of scheduled tasks, with a drag-and-drop interface for simple adjustments.
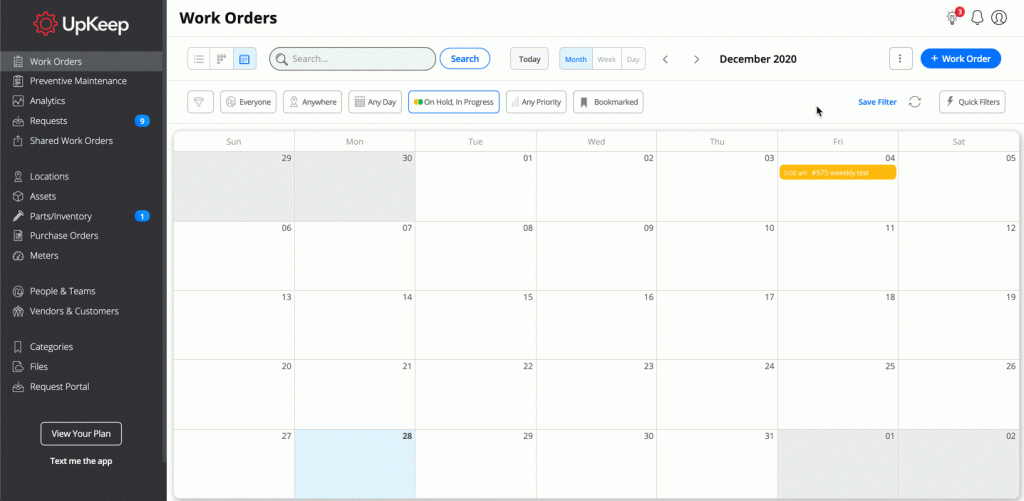
However, UpKeep’s Starter plan offers a monthly calendar view, which may not provide the granularity needed for daily or weekly maintenance planning.
Teams requiring more detailed scheduling need to upgrade to the Pro plan, which includes expanded calendar functionalities.
Another key feature for maintenance planning is UpKeep’s Meters Analytics.
This feature lets users plan and schedule maintenance more accurately, optimize resource allocation, and automate work orders based on real-time asset performance data.
Additionally, work orders can track wrench time and costs, allowing teams to monitor time and budget more effectively.
All you have to do is set it up in a work order, like below:
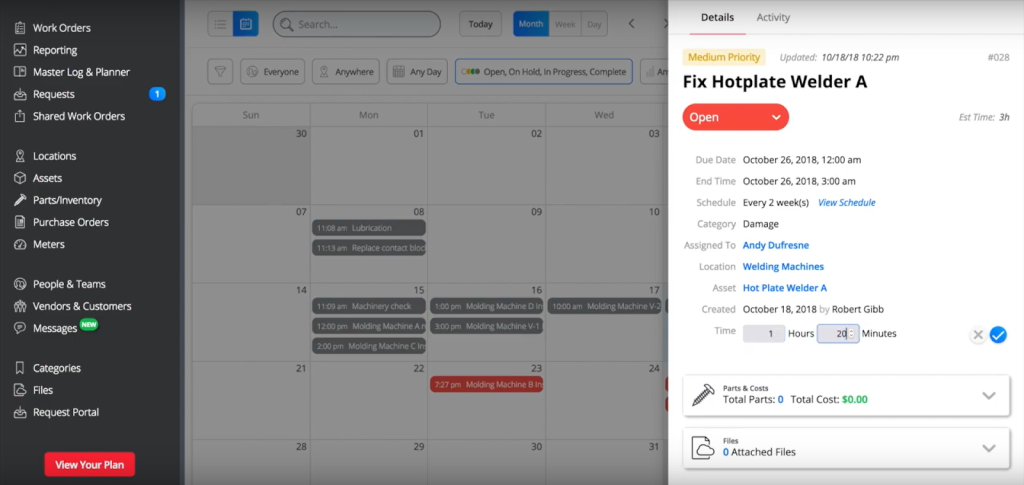
At the same time, UpKeep simplifies inventory management.
As parts are added to work orders and used for maintenance, they’re automatically deducted from inventory.
Moreover, just as in WorkTrek and Fiix, you can set minimum quantity thresholds for parts and receive alerts when stock runs low, helping to prevent shortages and reduce unplanned downtime.
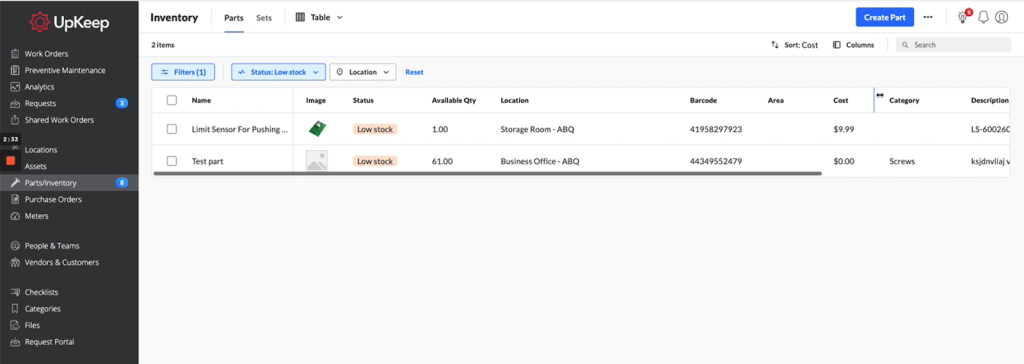
All in all, with its mobile-first approach and user-friendly interface, UpKeep makes it easy for maintenance teams to stay on top of tasks, even when on the go.
While UpKeep’s mobile-first approach is praised for its ease of use, occasional glitches, and limited customization options can frustrate users during high-demand periods.
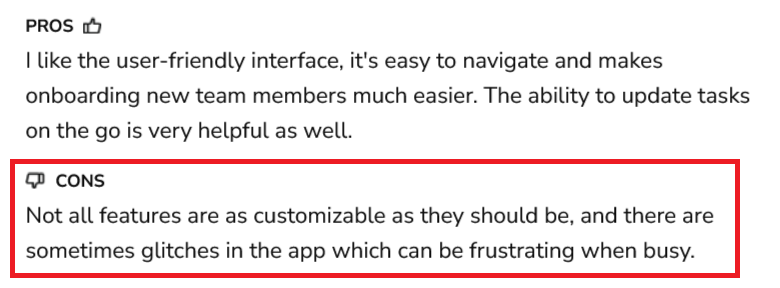
As for the pricing, UpKeep comes in three pricing plans:
- The Lite plan at $20 per user per month
- The Starter plan at $45 per user per month
- The Professional plan at $75 per user per month
Keep in mind that the Lite plan does not offer cost and time-tracking features, and preventive maintenance scheduling is also somewhat limited.
A 7-day free trial is available for those exploring UpKeep’s features.
Limble CMMS
Limble CMMS is a cloud-based solution for small—and medium-sized businesses and enterprises that need efficient maintenance planning tools.
It shares many features with other CMMS platforms we reviewed today, like storing all asset data in one centralized location.
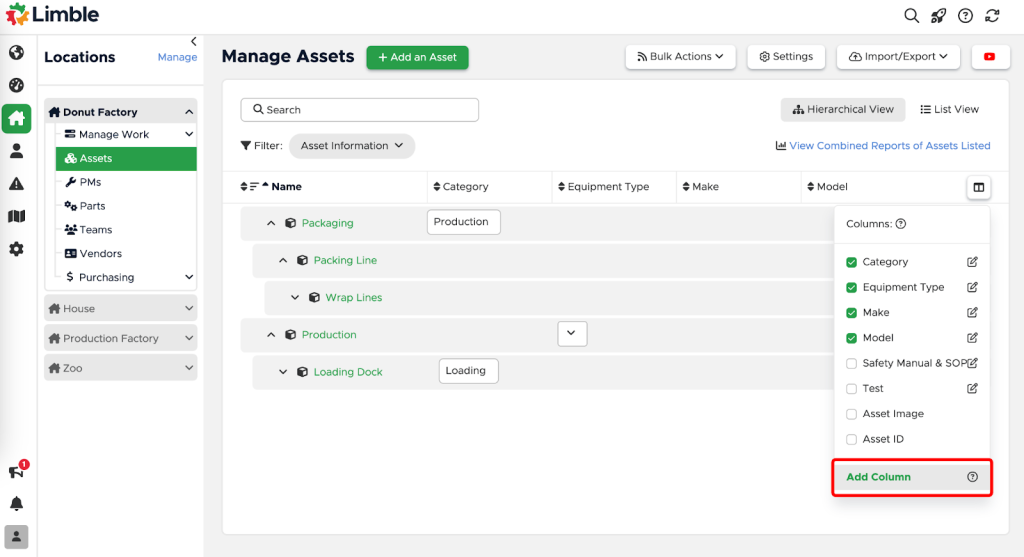
The data includes work history, manuals, related parts, and vendor information, helping maintenance teams easily access critical details when planning repairs or preventive tasks.
One of Limble’s key strengths is automation.
This CMMS can generate work orders automatically based on asset performance data.
Moreover, in Limble, you can sort and prioritize tasks by urgency, team, location, asset, or other criteria.
If plans change, re-prioritizing tasks takes only a few clicks, and dragging and dropping work orders to assign them to the right person is intuitive and efficient, as you can see below:
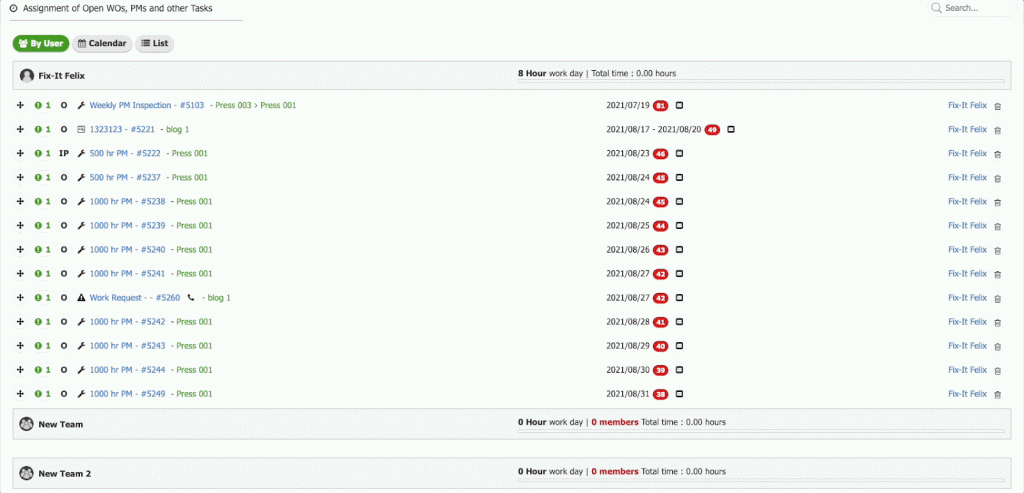
Maintenance KPIs are automatically tracked with every completed work order, providing valuable insights for improving processes.
Limble offers features like minimum part quantity thresholds for inventory control, which trigger work orders when stock levels fall too low.
Yes, the system will automatically generate a threshold task for a user to check the inventory and order more.
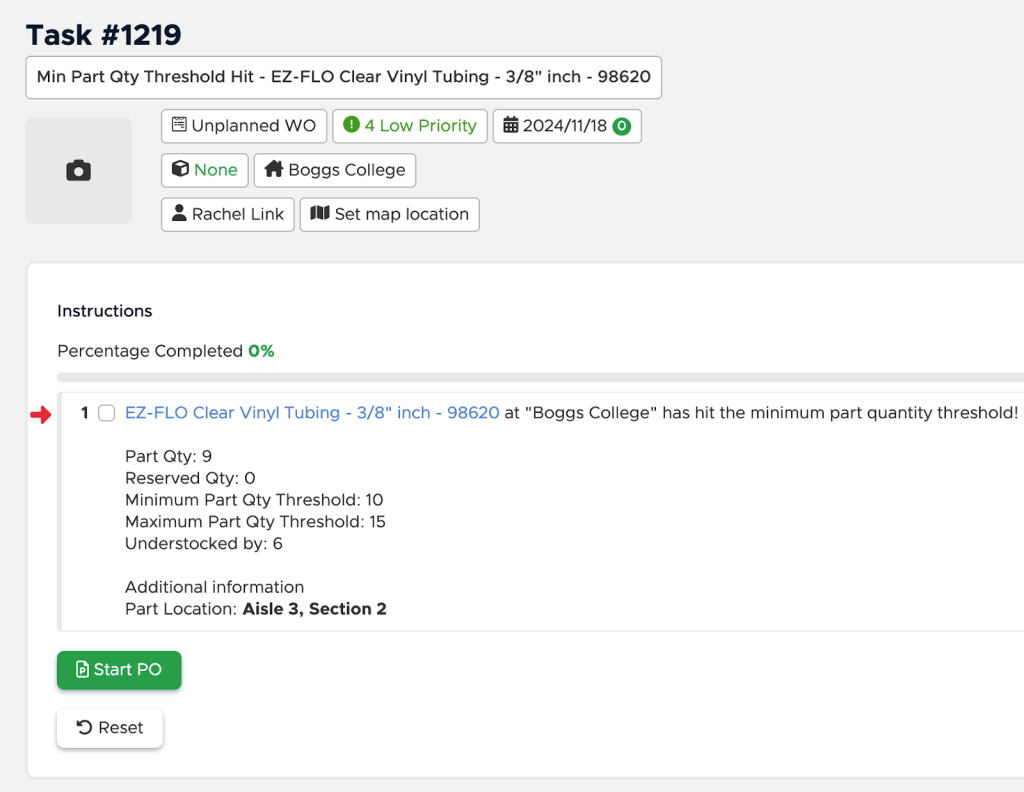
This prevents inventory issues from deterring maintenance plans.
While Limble excels in combining user-friendly tools with automation, it has some drawbacks.
According to a user who tested the software, Limble CMMS lacks native mobile app functionality, relying on an app window that can be buggy and slow.

Moreover, another user on Reddit has reported issues with excessive battery drain, particularly on iOS devices, which can disrupt fieldwork.

Another review mentions the lack of downtime cost tracking and planned downtime tracking.

These key maintenance planning features are available, but only in the Premium+ plan, making them inaccessible for teams on lower-tier subscriptions.
Speaking of pricing, the software has a free version with limited features—only four active recurring work orders and two work orders with attached procedures.
Pricing plans start at $28 per user per month.
Still, essential features like meter and threshold-based scheduling, parts inventory management, and time and cost tracking are available only in the Premium+ plan at $69 per user per month.
They offer a free trial and demo if you want to explore the platform’s capabilities.
Conclusion
Which of these tools felt like the perfect fit to improve your maintenance planning?
Is it WorkTrek’s seamless work order management and spare parts tracking or IBM Maximo’s AI-powered predictive maintenance for complex operations?
Perhaps mobile-first UpKeep caught your eye.
To choose the best maintenance planning tool for your company, start by identifying your priorities—whether you want robust asset tracking, advanced predictive insights, or streamlined mobile functionality.
Each software offers unique strengths, so weigh them against your team’s needs and budget.
Whatever you choose, you’re on the path to smarter maintenance planning, which will lead to fewer delays, better decisions, and a more productive operation.